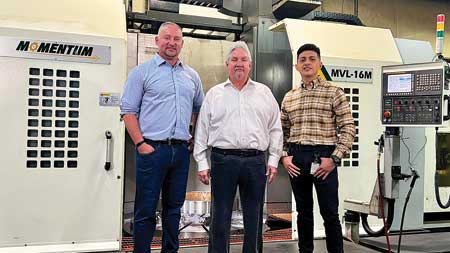
Tyler Hohman, Vice President; Allan Hohman, President; and Oscar Hernadez, Machine Shop Manager inside the machine shop at Fabcorp, with their Momentum MVL-16M vertical turning lathe in the background.
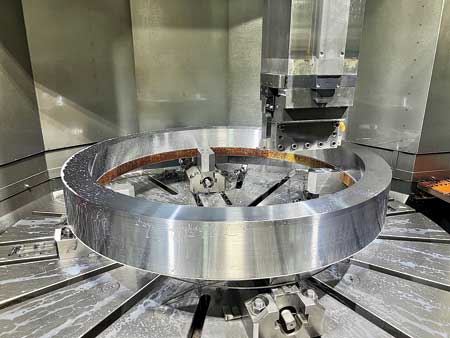
Precision turning the ID of a lock ring for a subsea gas mat on a Momentum MVL-16M vertical turning lathe at Fabcorp.
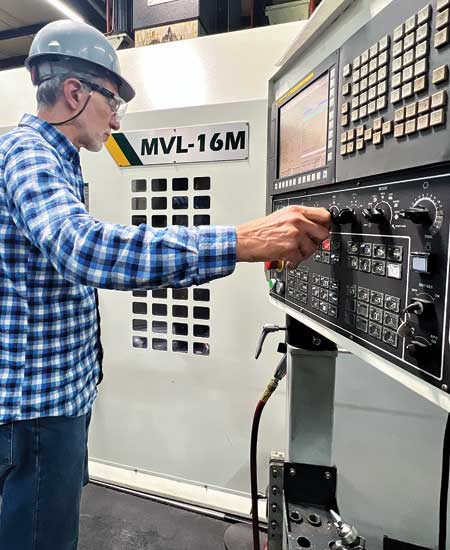
The machinist at Fabcorp programming and operating the Momentum MVL-16M vertical turning lathe.
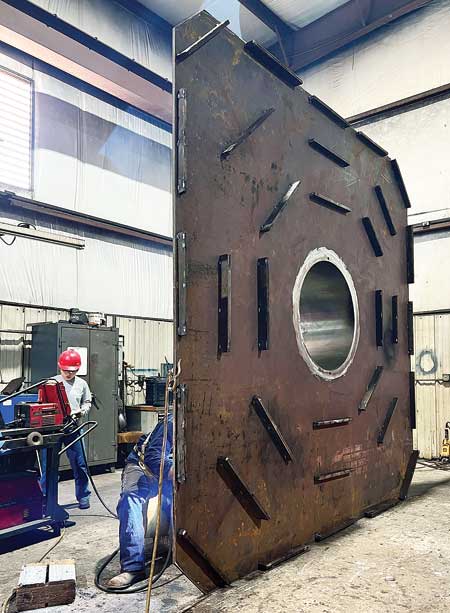
Welding the large subsea gas mat with the lock ring that was machined on a Momentum MVL-16M at Fabcorp.
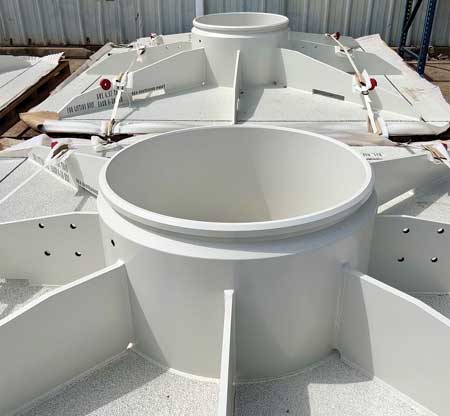
Subsea gas mats that have been fabricated and painted at Fabcorp, now ready to ship to the customer's offshore rig.
Fabcorp, Inc., established in 1992, is a womb to tomb fabricator, based in Houston, TX, where raw material comes in, is fabricated, machined and painted then shipped complete. A few years ago, Fabcorp came across several jobs requiring large, cylindrical components. This sent them on a search for a large capacity, heavy-duty CNC lathe with milling capabilities to take on the new challenge. According to Tyler Hohman, Vice President of Fabcorp, "The Momentum MVL-16M vertical turning lathe checked all the boxes."
Since acquiring the Momentum lathe, Fabcorp has machined critical components for a wide range of applications, from subsea work for oil exploration to parts for SpaceX used for space exploration. Currently, Fabcorp is machining lock rings for a subsea gas mat, which slips over a rough machined forging (also turned on the Momentum) to hold a wellhead together. Once they leave the machine shop, they are placed on weldments and Fabcorp personnel fabricate, weld, paint and ship complete to their customers.
"The MVL-16M's 63-inch chuck, 78-inch max turning diameter and 63-inch max turning height give Fabcorp the ability to perform full mill/turn work," said Oscar Hernandez, Plant Manager at Fabcorp. "I have turned up to 3/8 radial cuts on tough materials and have no complaints. The machine pushes it with the 75 HP main spindle."
Hernadez went on to explain the advantages of the MVL's full cross rail and full wrapped cast iron bed design, which allows them the ability to reach both sides of the chuck for turning, boring and probing: "I can place two tools in a single toolholder and turn ID and OD. I can bore an ID, turn the OD and face the lock ring with this one set-up, which relieves another pocket in the 15-station automatic tool changer for a milling tool or a right-angle head."
Henandez also pointed out that compared to the time it would take for two set-ups, they saved 12 to 13 hours by keeping large components, like the lock ring, in the Momentum for both turning and milling.
"We looked at all the competitors and we settled on Momentum because it is big, it is strong, it is tough, it is rigid and it is very accurate," stated Allan Hohman, President of Fabcorp. "We also chose the Momentum because it has strong support from the companies behind it. Besides the Momentum brand itself, it is represented locally (in Texas) by Hartwig, which I have known for over 30 years and I trust them. In addition, they are backed by Select Machining Technologies, the importer of Momentum lathes. So, we are lucky enough to have three tiers of protection, and they respond quickly. I mean, boom, just like that, they are out here and they're helping us solve problems."
Fabcorp started in 1992 with six employees in a 30,000 sq. ft. rented facility and today employs 192 across four facilities totaling 192,000 sq. ft., all owned by the company. Fabcorp capabilities include plate processing on Oxy fuel, high-definition plasma, waterjet and laser. The company has 38 TIG stations, 16 MIG stations and bending capabilities that go up to and include a 500-ton, 6-axis press brake. The machine shop has 38 CNC milling and turning machines with up to 6-axis capabilities.
Fundamentally, Fabcorp is a job shop, so according to Hohman, they do not know what the next customer is going to bring to the table, which is why they need equipment that does light and heavy manufacturing.
Homan said, "We are constantly growing, constantly moving and constantly improving, and the Momentum gives us that flexibility to do just that."
For more information contact:
Fabcorp, Inc.
6951 W Little York
Houston, TX 77040
888-830-3962
www.fabcorp.com
Momentum Machine Tool
10010 Houston Oaks Drive
Houston, TX 77064
844-200-8993
sales@momentumna.com
www.momentumna.com
Select Machining Technologies
910 Day Hill Road
Windsor, CT 06095
256-508-0805
www.selectmachiningtech.com
SOUTHWEST
Hartwig Southern
10321 Regal Row
Houston, TX 77040
713-749-9600
www.hartwiginc.com