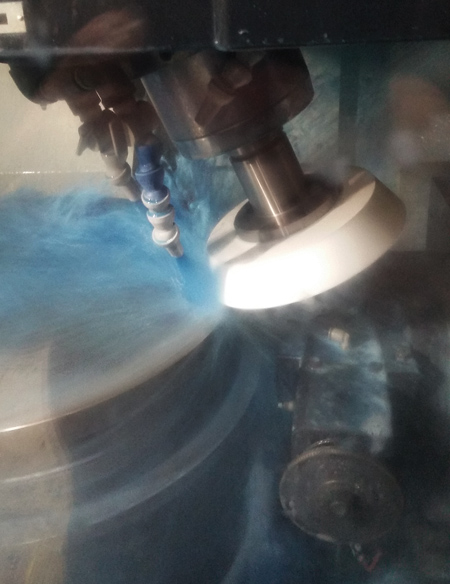
Face grinding a ring gear with an angle head wheel
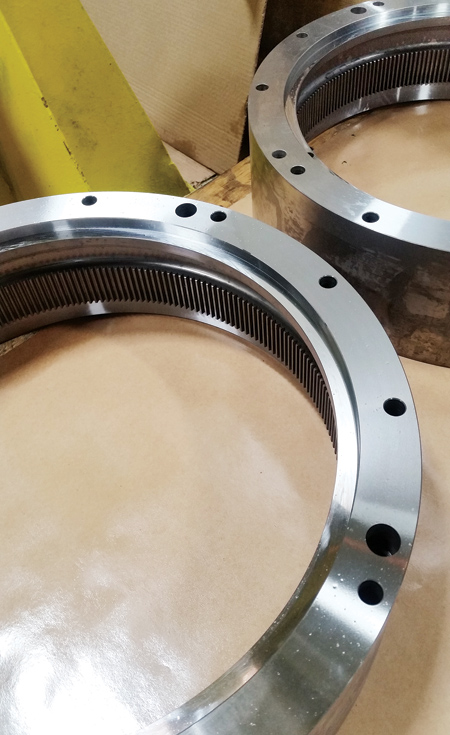
Finished ring gear (ground faces and I.D.)
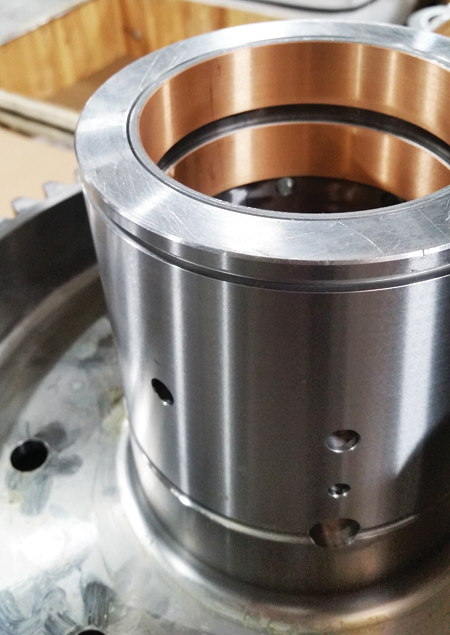
Finished idler gear assembly (O.D. grind, I.D. grind and face grind)
Schafer Gear Works, producer of high-precision, custom-engineered gears and machined parts for a wide range of applications, recently needed to procure equipment to reduce outside processing (OSP) costs. Equipment requirements included flexibility and the capability of meeting the size range of Schafer's products. Quick set-ups were a necessity. Schafer personnel determined that the solution was a new, more efficient multi-tasking machine that would meet job shop requirements.
Schafer selected a Taiyo Koki Vertical Mate 55, a vertical multi-tasking cylindrical O.D./I.D. grinder that, according to Engineer Jim Reilly, was a cost-effective solution that would meet their needs.
Vertical cylindrical grinding machines offer several distinct advantages for grinding applications. These include: simple clamping and clocking of workpieces; improved accuracy, particularly with long workpieces; and minimal workpiece deformation due to low clamping force.
In addition, reduced cycle times and improved accuracies are possible on the Vertical Mate 55 due to process consolidation, such as:
- Grinding of multiple inside and outside diameters and multiple internal/external faces in a single set-up
- Improved roundness and cylindrical accuracy because of reduced clamping force requirements
- The 6-place wheel (ATC) changer enables the right grinding wheels to be used for any operation
"The Taiyo Koki Vertical Mate 55 has the capacity to store six different wheels," said Reilly. "We have many part configurations that require face grinding, bore grinding and O.D. grinding. In the past, we would have to run each process at a different machine due to the type of grinding needed done. With the Taiyo Koki, we are able to run all processes in one machine with one set-up. This eliminates multiple part handling as well as multiple set-ups to a degree."
Schafer Gear Works grinds a wide variety of gears on the Vertical Mate 55, including those with O.D.'s up to 20" and bores up to 21.5", and I.D. grinding of bores between 2.0" diameter up to 21.5" from hardened steels, cast iron and bronze. According to Reilly, benefits realized include:
- Outstanding accuracy
- Cycle time reductions of 20 to 40%
- Reduced part handling due to the consolidation of more operations in a single part clamping.
Features of the Taiyo Koki Vertical Mate 55 include:
- Swing diameter: 21.7"
- Workpiece weight (including clamping device): 1,100 lbs.
- Max. grinding diameter: 19.7"
- Max. workpiece height: 17.7"
- Max. rotational speed of the working spindle: 350 RPM
- Max rotational speed of the grinding spindle: 15,000 RPM
- ATC unit with six-tool storage capacity
- Wheel spindle type: HSK-A63
- Wheel spindle features two-position turret with indexing angle of 0° and 22.5°
- Touch sensor for measuring I.D., O.D. and face (option)
- Scale feedback control for X-axis (one for Z-axis available as an option)
- Work spindle fixed-position stop.
A big benefit for Schafer Gear Works is high accuracy taper grinding. "High accuracy tapers (+/-.025°) are used in many different applications," said Reilly. "Tapers allow for a locking effect with a mating part. The more precise mating tapers are, the more effectively they lock when assembled. We make crankshaft gears for multiple customers who require precision taper diameters. The customer is then able to achieve a very strong taper lock to their shaft, which prevents slippage of the gear when higher amounts of torque are applied to the system."
Schafer has run wheel diameters down to 1.5" and spindle speeds up to 14,000 RPM. One stand-out feature is angle head face grinding, which allows the machine to be used like a rotary grinder. "The angle head feature allows circular face grinding," said Reilly. "This enables face grinding, which is much more effective than conventional cup wheel grinding. It also allows multiple operation capability in one set-up vs. conventional surface grinding on a separate piece of equipment."
Schafer makes custom as well as high volume precision gears. Gears are from 1.0" PD to 30.0" PD. Additional company capabilities include turning, milling, hobbing, shaping, broaching, O.D., I.D., surface and gear grinding. Additionally, the company has solid relationships with heat treat providers as well as plating and other contracted services.
Schafer Industries began in 1934 manufacturing high-quality gears as Schafer Gear Works. In 2012 it acquired two Dana Corporation plants and created Schafer Driveline. Today, Schafer Industries is a leading producer of high-precision, custom-engineered gears and machined parts as well as axles, transaxles, transmissions, brake assemblies and other components for recreational and off-road applications. "This makes us one of the few providers of integrated solutions in the industry," said Reilly. "Some of the most popular vehicles are powered by our innovations across a diverse set of industries including: aerospace, construction, light and heavy industries, mining, agriculture, defense, material handling, power train, automotive, gas and oil, medical instruments and recreational vehicles."
Headquartered at one of America's great natural crossroads in South Bend, IN, Schafer also has plants in Roscoe, IL, Fredericktown, OH, and Blacklick, OH. "We are ISO 9001:2015 certified and our cell-based manufacturing processes assure strict compliance to quality and delivery requirements for performance customer can depend on," said Reilly. "Our in-house engineering support teams provide expert and responsive customer service."
For more information contact:
Schafer Gear Works Roscoe, LLC
5466 E. Rockton Rd.
Roscoe, IL 61073
815-389-6055
www.schaferindustries.com
DMG MORI - Americas Headquarters
2400 Huntington Blvd.
Hoffman Estates, IL 60192
847-593-5400
Service Hotline:
855-DMG-MORI (364-6674)
us.dmgmori.com