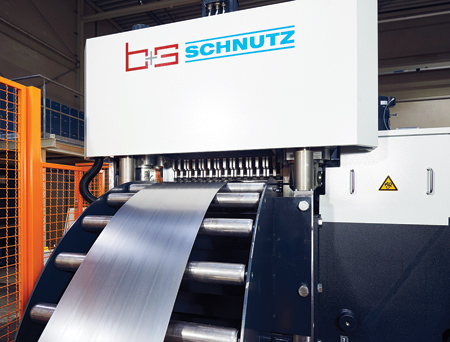
The new Schnutz machines at Adient each consist of a leveler with integrated feed unit, coil lift truck, decoiler, loop equipment and appropriate automation including safety devices.
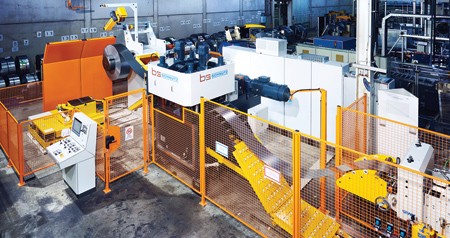
During the course of 2018, the machinery at Adient (Solingen, Germany) was gradually extended by the addition of strip feeding lines with high-performance levelers.
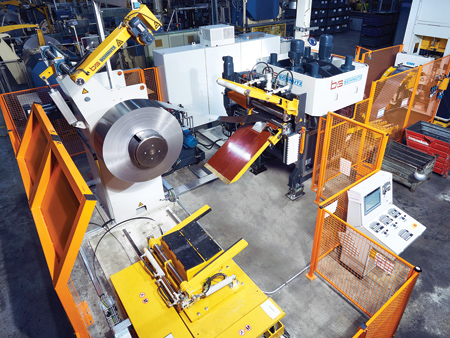
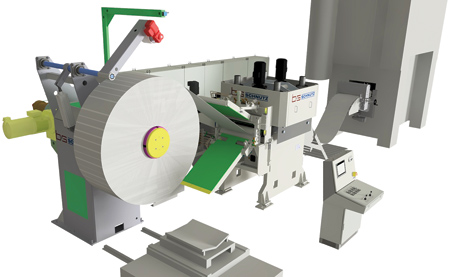
Simulation programs are used to analyze the working processes and plastic forming behavior of the material. Schnutz used the results of the leveling tests to modify decisive design parameters to suit customer-specific requirements.

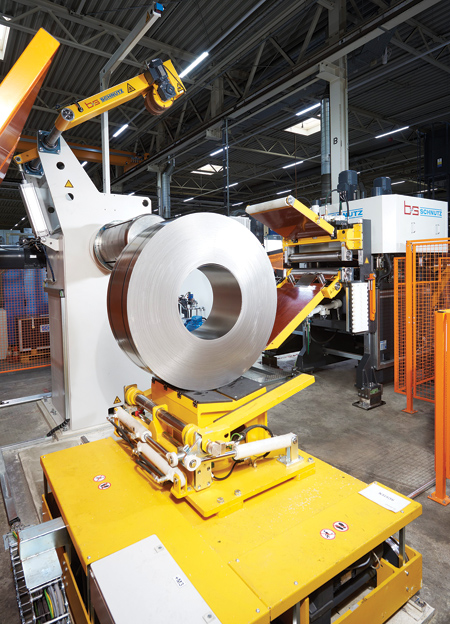
Coils are pushed on to the decoiler by the coil lift truck. For this purpose, they are automatically placed level with the decoiler mandrel. Once the coil has been clamped in place, it is rotated so that after loosening the binding strap, the beginning of the strip rests on the table.
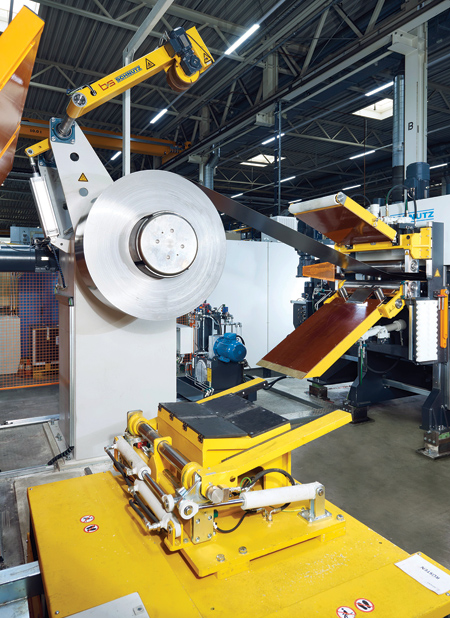
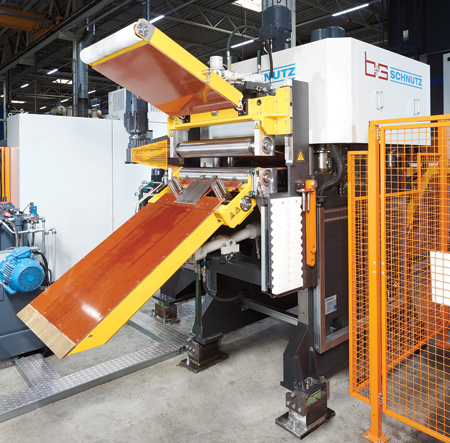
In the automotive industry, lightweight construction is more in demand than ever before. However, car seats and their fastening elements must withstand the enormous forces exerted on vehicles involved in accidents. High-strength materials are used to ensure high resilience, along with a lower weight. According to recent studies, the proportion of high-strength steels used in vehicles will increase from 15% in 2017 to nearly 40% in 2030.
"The machines of numerous automotive suppliers used up to now are often not designed for processing these materials," said a Schnutz GmbH spokesperson. "The globally active automotive supplier Adient therefore took appropriate upgrade measures: its press lines at Solingen, Germany, were extended by the addition of three highly efficient strip feeding lines with high-performance machines from Schnutz GmbH. The new machines enable flawless feeding and easy processing of the special materials, with perfect flatness being achieved."
"Prior to awarding the contracts to Schnutz, Adient carried out extensive tests at various suppliers," said Dr.-Ing. Lutz-Stefan Henrich, Managing Director of Schnutz. "The aim was to ascertain whether the machines were suitable for the complex and multistage forming processes of high-strength steel. Because we have many years of expertise in the leveling of demanding materials, such as high-strength steels and aluminum, we received a related enquiry. In the technical center in Siegen, Germany, Schnutz demonstrated to Adient the quality of its machines in joint leveling tests. For this reason, Adient decided to extend its machinery for processing high-strength materials by the addition of three strip feeding lines, including a high-performance leveling solution from Schnutz."
Advanced Analysis Allows Individual Adaptation
In Adient's Solingen pressing plant, seat rails are manufactured on several lines. "The high-strength material used requires special treatment in order to obtain the required flatness with optimal residual stress in the strip material," said Henrich. "Only when the geometry of the leveler matches the particular product can the best results be achieved."
Schnutz uses simulation programs to analyze the working processes and plastic forming behavior of the materials to modify the machines to suit customer-specific requirements. Schnutz used the results of these leveling tests to adapt design parameters, such as the number and diameter of the leveling rolls, to Adient's material.
"For fastening elements used in the automotive industry, high resilience is an important factor despite the low weight," said Henrich. "For this reason, the seat rails are made from high-strength steel materials. High plastic deformability of the steel materials used must be ensured at the same time." The steel forming resistance associated with increasing yield strengths places particularly high demands on the machinery.
Optimal Flatness and Elimination of the Dish-Shape
Each of the new machines at Adient is a leveler with integrated feed unit, coil lift truck, decoiler, loop equipment and appropriate automation including safety devices. "The coils are pushed onto the decoiler by the coil lift truck," explained Henrich. "For this application, they are automatically placed on one level with the decoiler mandrel. When the coil has been clamped in place, it is rotated, so that after loosening the binding strap, the beginning of the strip rests on the table." After opening the binding strap, the strip is fed by a feed unit through the leveler and via the transfer table to the servo feed of the press.
A particular challenge when leveling high-strength steels is something referred to as a dish-shape-a curvature transverse to the direction of strip travel. If this is not eliminated, further processing in a press can be hindered to a large extent, or even prevented. "It is therefore important that not only the coil curvature as such is corrected, but also that an optimal flatness exists in the traverse direction of strip travel," explained Henrich. "This is achieved by the special design of Schnutz levelers. In this way, the new machines ensure that the materials, also after further forming, maintain the specified shape and position tolerances. Adient was particularly happy that the dish-shape could be effectively eliminated while retaining the high material strengths."
Adient was also satisfied with the high level of automation of the machines. "We naturally also ensured that the necessary safety measures were in place," said Henrich. "Particular attention was paid to the loading of the decoiler and the interface to the coil lift truck."
Since the beginning of 2018, the machinery at the Adient facility in Solingen has been gradually extended by the addition of strip feeding lines, including high-performance levelers. The first machine was implemented in January and the second in April, while the third machine followed in the second half of the year as planned. "As a result, the output of the extended machinery could almost be doubled, while at the same time maintaining the highest quality," said Henrich. "This has ensured that Adient at its site in Solingen is well equipped to meet future challenges."
The company group Adient is an international supplier to the automotive industry, specializing in the production of car seats and associated automotive components.
The roots of Schnutz GmbH go back to a forge founded by Martin Schnutz in 1846 which, with the growth of the sheet metal industry in Siegerland, Germany, at the turn of the 20th century, increasingly focused on the design and construction of sheet metal working machines. In 1882, Schnutz produced the first levelers, which were continuously technically improved and extended. Recent innovations include the multi-motor drive-Schnutz Multidrive-as well as a further development of the electric motor driven support systems. Since 2014, the company has been part of the Burghardt + Schmidt Group.
For more information contact:
Mike McGuire
U.S. Sales Manager
Burghardt + Schmidt
1728 Maple Lane
Wheaton, IL 60187
630-868-3016
m.mcguire@b-s-germany.com
www.b-s-germany.de