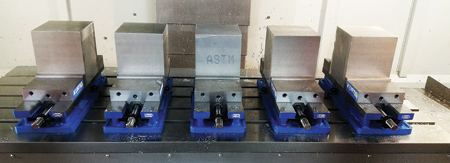
The Smart Machine SM 1565 features a large workspace, allowing multi-part set-up. Workpieces are 7075 aluminum and measure 5" x 6" x 7".
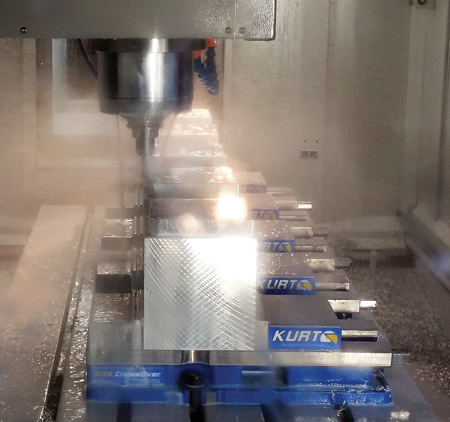
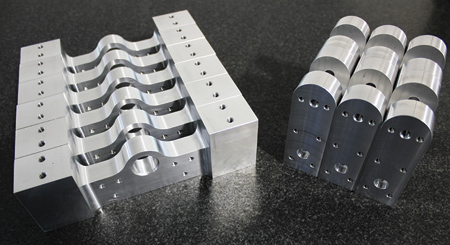
The SM 1565 is rigid, allowing tight tolerances with high repeatability in multi-part production. Workpieces are 6061 aluminum bearing blocks.
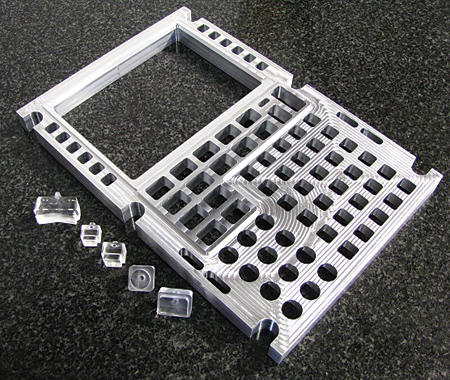
Control panel and buttons (6061 aluminum and clear acrylic plastics)
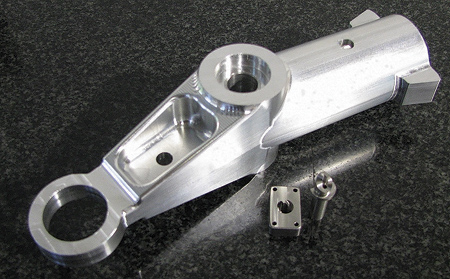
The SM 1565 can perform smooth, high-speed 3-D milling. Workpiece is 6061 aluminum connecting rod.
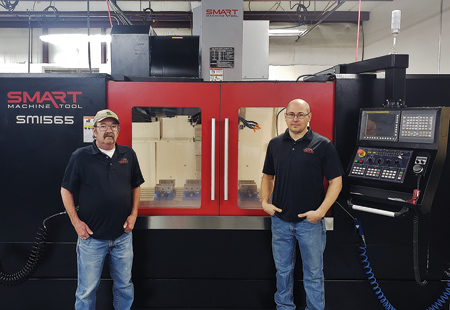
(l-r) Clyde Isgrig, Owner, and Chris Smith, Production Manager, C & S Tool & Die
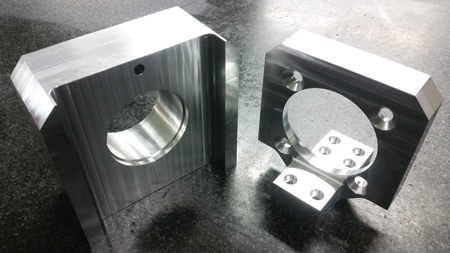
Motor bearing blocks (7075 aluminum, +/-.0005 tolerances)
C & S Tool & Die recently faced a common enough dilemma: how to increase productivity and shop capacity using fewer man hours.
C & S considers itself a specialty shop. "We do not do a whole lot of production work, although we are starting to bring in more of it. We mainly do a lot of mold and tool & die across a range of industries, including aerospace and automotive," said Chris Smith, Production Manager.
Because it is a job shop, C & S performs a lot of one-off machining. Typically, one operator runs one machine. The operator sets up a machine to make a special part, and then has to set it up again to make a different part. Operators usually do not have time to get away from one machine to go run another one.
Because of the machines' limited work area, there were also efficiency constraints for higher part runs, meaning C & S had reached its cap on productivity.
C & S focused on increasing productivity with a machine that had a larger work area. This way, one operator could set up, program and machine multiple smaller parts at a time, and then move on to another machine.
Gains in Productivity and Efficiency
C & S's machine solution is from Dynamic International's new line of machine tools-Smart Machine Tool USA-and the first one to be installed in the U.S. The Smart Machine model SM 1565 is a 60" vertical machining center (VMC).
SM 1565 specifications:
- X travel: 59.06"
- Y travel: 25.59"
- Z travel: 24.02"
- Table size: 62.99" x 25.59"
- Spindle taper: CAT40 (BIG PLUS)
- Spindle speed: 12,000 RPM
- Spindle HP: 25 HP
- Magazine capacity: 36.
The SM 1565 is now C & S's largest machine. When they get a job that requires a larger quantity of parts, they are able to put multiple parts into the machine at once. Smith has designed special fixturing that fastens a sub plate to the table. The operator puts the fixture on the machine, loads it with parts and runs the machining program. Meanwhile, another fixture is being loaded for the next run. The longer run time frees up the operator, who can now tend two and even three machines at a time.
One of C & S's higher quantity jobs involves aerospace components used in simulators for commercial and military flight training. Others jobs include components for die cast molding and fixturing for robotic welders. Types of component material machined at C & S include aluminum, alloy steels, stainless steels and tool steels.
The new VMC has had a positive effect on part quality. "The SM 1565 is a lot more rigid than some of the other machines we have," said Smith. "It can take a lot heavier and a lot faster cuts in steel, and it is more stable. It has a box way system rather than linear ways, which makes it more rigid. It is also surprisingly quiet for the size machine it is."
Smith said that the standard 12,000 RPM spindle is a bonus, since the majority of machines come standard at 8-10,000 RPM. Another feature he appreciates is the Renishaw probe for tool setting. "It is also 4th axis ready," he added. "I can put a 4th axis rotary in there and just plug & play. It is all interfaced for it already. Most machines would not come standard with that."
New Capabilities Bring in New Opportunities
"Although we bought the machine to run more of our smaller components, some of our customers know the size of the machine, so they are now bringing me bigger parts to run," said Smith. The SM 1565 has a 60" long workspace table, and Smith has had it machining workpieces up to 57" in length. Smith said there are plans to purchase a second Smart machining center in the near future and further increase their productivity.
C & S has a variety of capabilities, including:
- CNC milling, including 4th axis CNC milling
- CNC turning, including a 6-axis CNC lathe with live tooling and sub-spindle
- CAD/CAM design and programming
- Surface grinding
- Wire EDM
- Welding/fabricating
- Heat treating
- Metal surface finishing.
C & S was founded by owners Clyde and Diane Isgrig and has 12 employees. "We are dedicated to get the job done with efficiency using up-to-date programming technology and CNC machining equipment," said a company spokesperson. "Our #1 goal is to deliver on time with exceptional quality and to guarantee total customer satisfaction."
For more information contact:
C & S Tool & Die
107 E Industrial Drive
New Haven, MO 63068
573-237-7004
www.cstooldie.com
Smart Machine Tool
N25 W23287 Paul Rd.
Pewaukee, WI 53072
855-637-3220
www.smartmachinetool.com