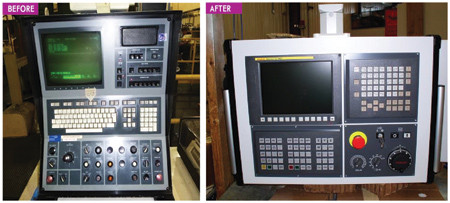
8000 control solution
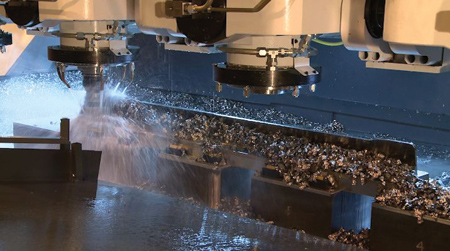
XT titanium metal removal
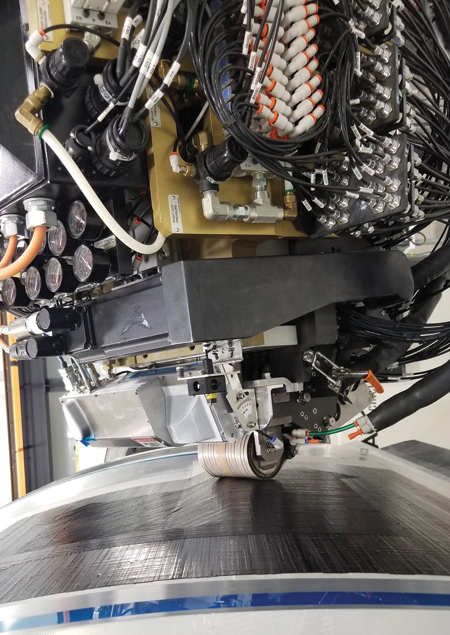
IPI
"If we are going to make ourselves, and foremost our customers, exceptional, we must think of their profits first and always," said Steve Thiry, President and CEO of the groups Fives Machining Systems, Inc., the home of Giddings & Lewis and Cincinnati models. "If this is not a part of our continuous improvement process, we are failing them and ourselves."
Thiry continued, "Not everyone was on board in the beginning. The long history of success, and natural competitive nature within our company, made the outward think we have today even more challenging to adopt at first. Information, best practices, applications knowledge from one person or department to another, had long been coveted within pockets of people throughout the company and are now being be shared among the legacy locations, under Fives. The early results were really eye opening. We had so much low hanging fruit that we could pass on as value to our customers."
"Delivering profits for our customers comes in many forms," said a company spokesperson. "For decades, the word 'profiler' and 'Cincinnati' were synonymous with multi-spindle high volume production. However, in recent years, both words have had more of an association with old, messy, outdated and even slow in some circles. This could not be further from the truth today. Enter the current Cincinnati XT profiler with a 57% increase in structure mass and independent A- and B-axis for titanium machining. On a recent order, the contracted obligation was to produce, in titanium, 75 cubic inches of metal removal per minute. The team at Fives exceeded this with a result of 155 cubic inches. When the team was pushed even further by leadership, collaboration with third parties ensued and the industry's best carbide and cutting tool experts were brought in for months of collaboration with the engineers from Fives. The result was an astounding 230 cubic inches per minute in titanium removed. This was only possible with the clear team focus on profits for the customer, and an openness to collaborate by all means necessary to be exceptional and lead vs. merely participate. The same team has applied this success to the new XP solution for the industry's best performance and production in aluminum."
The spokesperson continued, "A brand new innovation and offering that is the result of customer profits first philosophy at Fives is its new IPI, or in-process inspection, for use on new and or existing automated composite layup machines. This solution literally attacks some of the process variables that impede customers' actual profits while indirectly improving the overall HSE status that exists in today's current market. Manual inspection has been automated composite layup's Achilles heel for decades. Fives IPI and compact sensor solution literally inspects the fibers while the machine tool is laying up the part. Operators can then focus their time on running the equipment vs. starting, stopping and inspecting. Simply put, they can make more parts. Achieving the demanding performance requirements of modern composite structures is predicated on tightly controlling the tolerances of the as-built part to ensure that it matches the as-designed part to within the acceptable limits. Fives IPI not only complements this; it also achieves this and adds the element of high-fidelity data on laminate quality, which also allows for the added benefit of traceability. Fives' new IPI solution is also a more robust solution that, when coupled with its ability to detect defects at angles up to 45° and not interfere with the in-process aspect of highly contoured part layups, far exceeds the previously known solutions using laser line triangulation (LLT) that are more disruptive, limited and far less effective on variables such as sheen in carbon fiber pre-preg, which are common in military grade materials."
Robert Harper of Fives Cincinnati commented, "With customers in both the commercial and military world, we needed to consider the materials as much as we considered the technology. To create the solution we have today, we needed to consider the whole environment of both processes."
Early in the development at Fives, when working on the newly offered IPI technology, comments from the team were made about the need for more machines in the market vs. improving the performance and process of all the existing machines. If the technology improved performance significantly, would not customers need fewer machines? "'Yes' was the clear answer, but the focus on the customer's profits as the priority prevailed, and the new solution is an option on every new machine, as well as on legacy machines as a productivity upgrade," said the spokesperson.
"It is simply the right technology at the right time," said Thiry. "In a market that is seeing increasing price pressures throughout the supply chain, we have to deliver that value. The stability of our platforms in AFP and ATL applications-combined with our engineers' understanding of the materials and this new IPI technology-add up to a very financially attractive and risk adverse solution."
"So how does a group like Fives, with one of the largest historical install bases and trained aftermarket teams, globally adapt this customer profits first approach? Culturally it may have been our biggest challenge," said Nolan Strall, the Director for Fives Metal Cutting | Composites business unit, Machine Tool Services and Solutions, managing their aftermarket business. A complete evaluation of the group's pricing for commodity based items within the spare parts is underway, service hours and contracts have been reevaluated, and the biggest change came from the group's offerings and solutions associated with their retrofit rebuild programs. One such offering is the latest Giddings & Lewis 8000 control upgrade. Strall continued, "In looking at the group, we had to get out of the mindset of competing. Competing internally, competing with each other. That shift allowed us to look internally and see what other great things were taking place. The new machine business was putting out some fantastic value add features with its standard control packages. Fives overall efforts and focus on standard and optional Internet of Things (IoT) offerings surely complemented this. We already were authorized systems integrators with the primary commercially available CNC controls suppliers. By overcoming the internal fear-together as a team-of replacing a possible machine sale with a high value based retrofit option, that was again customer profits focused, we came up with the solution."
The new 8000 control retrofit option is designed to minimize the disruption at the customer. "It is prepared in advance, and installed with speed," said the spokesperson. "In addition to attacking an impending obsolescence issue, it utilizes the solid structure and design of the original horizontal boring mills (HBMs) and vertical turning centers (VTCs) and modernizes them with increased memory, accuracy capabilities, reliability, ease of maintenance, remote operator pendants and the potential for future expansion. Customers who have adapted this solution report increased productivity and more accurate parts." The solution offered includes customer based training at their location or within the Fives locations. Additional options are also available from the group.
Thiry concluded, "The question we asked ourselves was simple: 'What would we want a supplier to consider first, if we were the customer?' From there, it was getting everyone reprogramed from what we were, to where we are going as Fives. If we improve the bottom line of our customers, everything else falls into place."
Fives Metal Cutting | Composites Business Unit consists of Fives Cincinnati and Fives Giddings and Lewis, Fives Line Machines, Fives Forest Line, Fives Lund, and both global aftermarket teams, Global Services and Machine Tool Services and Solutions.
For information on
Giddings & Lewis products contact:
Fives Machining Systems, Inc.
142 Doty Street
Fond du Lac, WI 54935
920-921-9400
www.fivesgroup.com
AeroDef 2019 Booth 1826
For more information on
Cincinnati products contact:
Fives Machining Systems, Inc.
2200 Litton Lane
Hebron, KY 41048
920-921-4600
www.fivesgroup.com