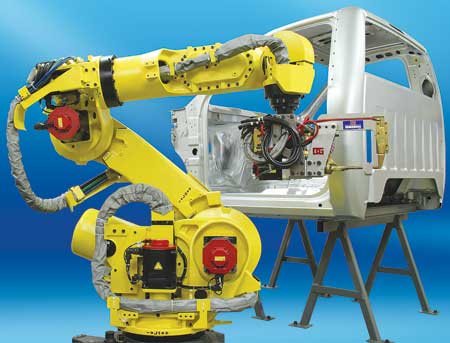
The R-2000iB/210FS is shown using a servo weld gun control to simulate spot welding inside a truck cab. The slim wrist of the R-2000iB/210FS is ideal for spot welding in tight spaces such as a vehicle body.
A member of FANUC Robotics' family of R-2000iB material handling and spot welding robots, the R-2000iB/210FS robot has a hollow wrist with internally routed utilities and signal cables, making it useful for applications such as servo spot welding, clinching, riveting and material handling.
"Compared to conventionally dressed robots, the R-2000iB/210FS eliminates the need for dress-related adjustments when a part program changes or new parts are added, which significantly reduces tryout time and life cycle costs," said a company spokesperson. The R-2000iB/210FS operates with the company's latest R-30iB controller with integrated intelligent functions such as iRVision and ROBOGUIDE Simulation Software.
"iRVision Tip Inspection software verifies the welding tip condition, and checks proper alignment to help arc and spot welding customers reduce part manufacturing issues and scrap/rework costs caused by poor tip conditions," said Tim Holcomb, Product Manager, FANUC Robotics America.
The R-2000iB represents a family of industrial robots, including pedestal, invert, compact and rack mount versions with a variety of payloads and reaches. The R-2000iB offers a slim arm and wrist assembly which minimizes interference with system equipment and allows the robot to operate in small workspaces.
According to the company, additional R-2000iB/210FS features and benefits include:
- Fast system integration
- Lower life cycle cost than conventionally dressed robots
- Reliable dressout with accurate simulation
- Compact, high torque capability wrist
- Spare parts are interchangeable with standard R-2000iB robot models
- New routing of primary axis solution arm minimizes robot width
- Utility protection eliminates interferences with tooling or items in the work cell.
iRVision Tip Inspection error proofs weld tips to reduce part manufacturing issues and scrap/rework costs caused by poor tip conditions. According to the company, it offers a variety of advantages for arc and spot welding, including:
- Arc welding:
- Measures contact tip wear
- Maintains an accurate tool center point (TCP)
- Calculates maintenance cycle
- Improves weld quality
- Spot welding:
- Measures tip wear
- Measures and verifies alignment
- Verifies tip dress
- Verifies new cap and cap type
FANUC's iRVision is an integrated, plug-and-go vision system that runs on the standard CPU of every FANUC R-30iB controller without any additional hardware. iRVision is intended to provide easy setup and operation for factory environments requiring 2D and 3D guidance, error proofing, visual tracking and quality control.
The FANUC R-30iB controller uses high-performance hardware and the latest advances in network communications, integrated iRVision and motion control functions, according to the company. The R-30iB controller features FANUC's exclusive iPendant with 4D graphics. The iPendant displays process information and the actual process path directly on the iPendant screen, enabling easier setup and troubleshooting. The R-30iB is compact and also energy efficient, requiring less power consumption than previous models.
FANUC Robotics' ROBOGUIDE family of offline robot simulation software products are built on the Virtual Robot Controller. ROBOGUIDE allows users to simulate a robotic process in 3D space or conduct feasibility studies for robotic applications without the physical need and expense of a prototype work cell setup.
For more information contact:
FANUC Robotics America, Inc.
3900 West Hamlin Rd.
Rochester Hills, MI 48309-3253
248-377-7000
800-iQ-ROBOT
www.fanucrobotics.com