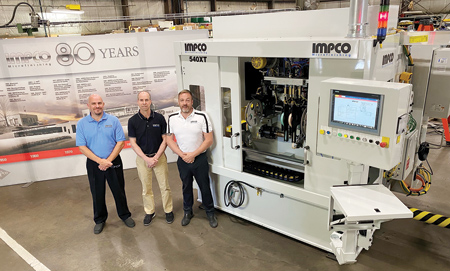
IMPCO announces recent order from an EV OEM for shaft microfinishing systems. (l-r): Gregg Judge, IMPCO Parts Manager; Bill Kurzynowski, IMPCO Sales; and Mark Hendel, IMPCO Global Sales Director
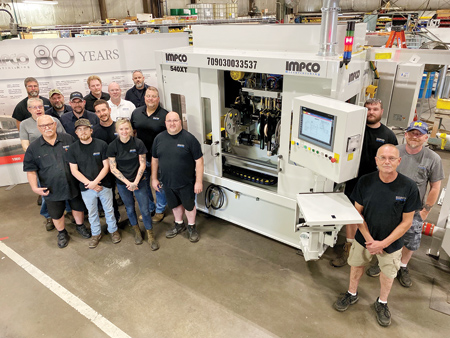
IMPCO skilled trades celebrate recent order from an EV OEM for shaft microfinishing systems. Shown in the image is one of the systems.
IMPCO Machine Tools has received orders for five microfinishing systems to be delivered to electric vehicle (EV) OEM plants in Mexico and USA. The order total is $3.5 million. Each robot-loaded system is designed to microfinish the bearing diameter to millionths of an inch (1 µm) on a family of 300 mm rotor shafts used in the drivetrain of electric vehicles.
"Our process is a highly refined process that permits essential rotating components to operate efficiently with minimum frictional loss through noise and vibration for extended duty cycles," said Mark Hendel, IMPCO Global Sales Director. The IMPCO Standard 540 Series Microfinishing Systems will perfect surface finish, roundness and straightness of the bearing journals on the shafts at production rates greater than 100 parts an hour. Machine flexibility is key in today's market, so having the ability to change over between part types in less than 10 min. allows for future product design flexibility.
"We began our work on this project more than two years ago in our R&D lab, working with the customer on the critical points on bearing journal design including geometry and surface finish. We then proved our process on the customer parts, further refining the process to meet noise and vehicle harshness (NVH) goals to assure minimum noise when the motor is running. NVH standards are critical in electric vehicles," Hendel said.
In operation, IMPCO Microfinishing removes the microscopic amorphous surface material left from the grinding of a dimensionally finished shaft-type part, such as a crankshaft, camshaft or pump shaft, to permit a highly precise fit to a mating part. "The process controls surface finish, roundness and straightness to microns-mere millionths of an inch-tolerances unattainable with grinding," said an IMPCO spokesperson.
"Generating the final functional part surface texture and geometry, IMPCO microfinishing is the key to friction reduction, higher performance, longer durability and greater reliability of precision shafts," an IMPCO spokesperson said. The patented IMPCO Generating Bearing Quality (GBQ) process typically removes less than 10 microns of material using as a cutting media a non-compressible abrasive tape.
The tape is pressed against the surface by a non-compressible tool that is designed to conform dimensionally to the component. The tool consists of two hard shoes which are held in toolholders attached to two hydraulic arms. The arms are closed at a set pressure before the cycle begins. The bearing component is rotated and oscillated between centers for a defined period-typically less than 10 sec. Fresh tape is incrementally indexed after each process cycle to ensure a consistent cutting edge from one part to the next and reduce material build up at the edge of the tape.
IMPCO employs more than 50 in Michigan designing and building special automated machines that polish camshaft, crankshaft and other precision load bearing journals for drivetrain manufacturers worldwide.
"Today we are positioned at the forefront of microfinishing technology," said Hendel. "This all started 55 years ago when IMPCO designed, built and delivered the world's first automated microfinishing machine in response to a request from Chrysler Corporation for polishing its new V-8 engine crankshaft."
For more information contact:
IMPCO Machine Tools
3417 West St. Joseph Street
Lansing, MI 48917
517-484-9411
sales@impco.com
www.impco.com