
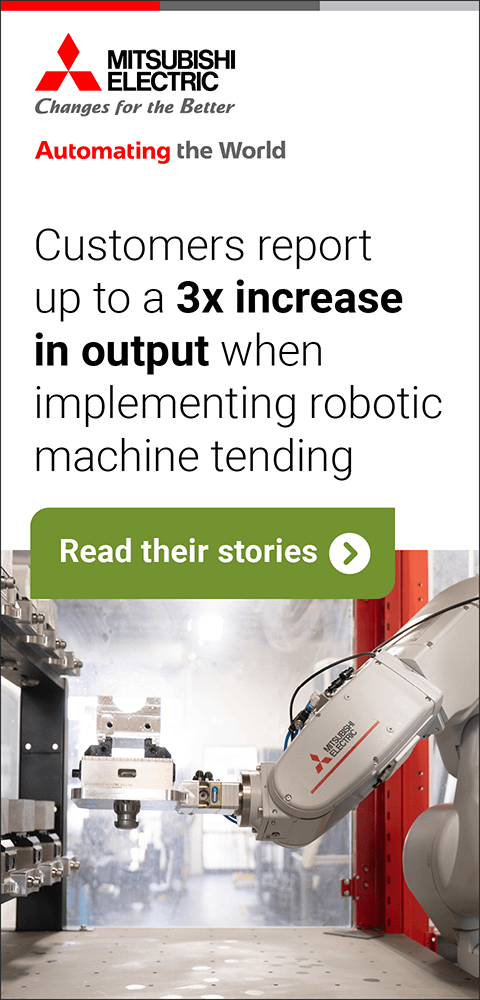
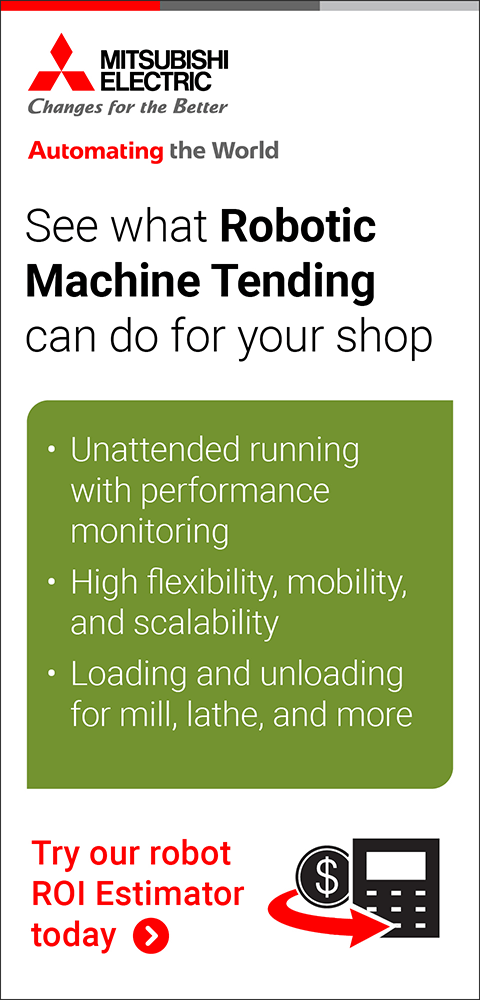
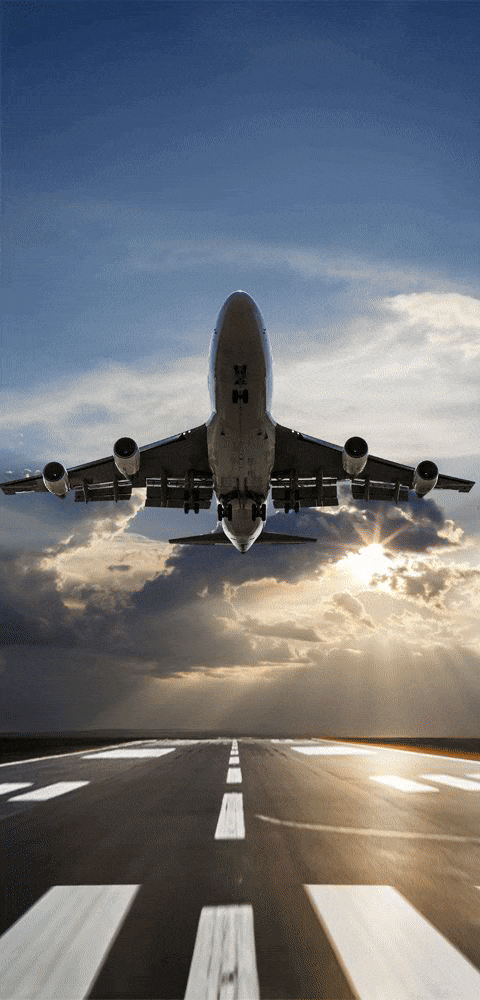
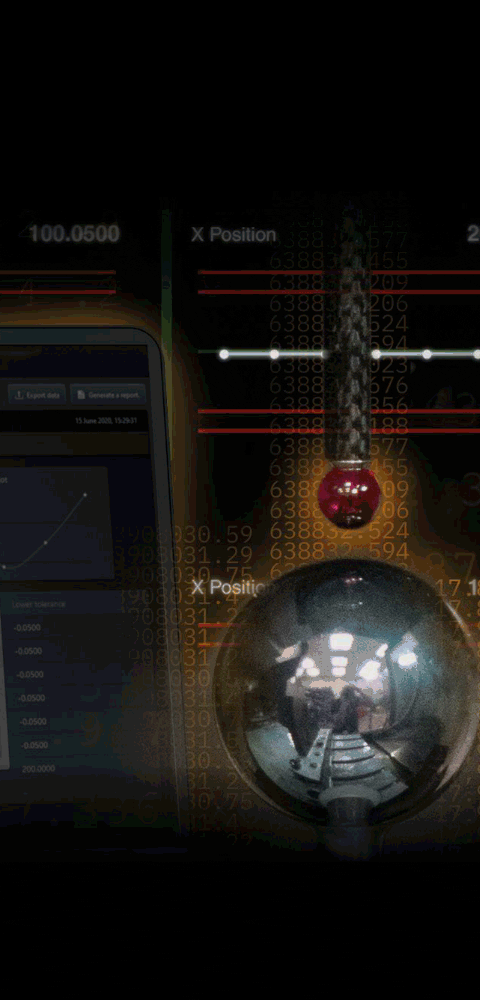
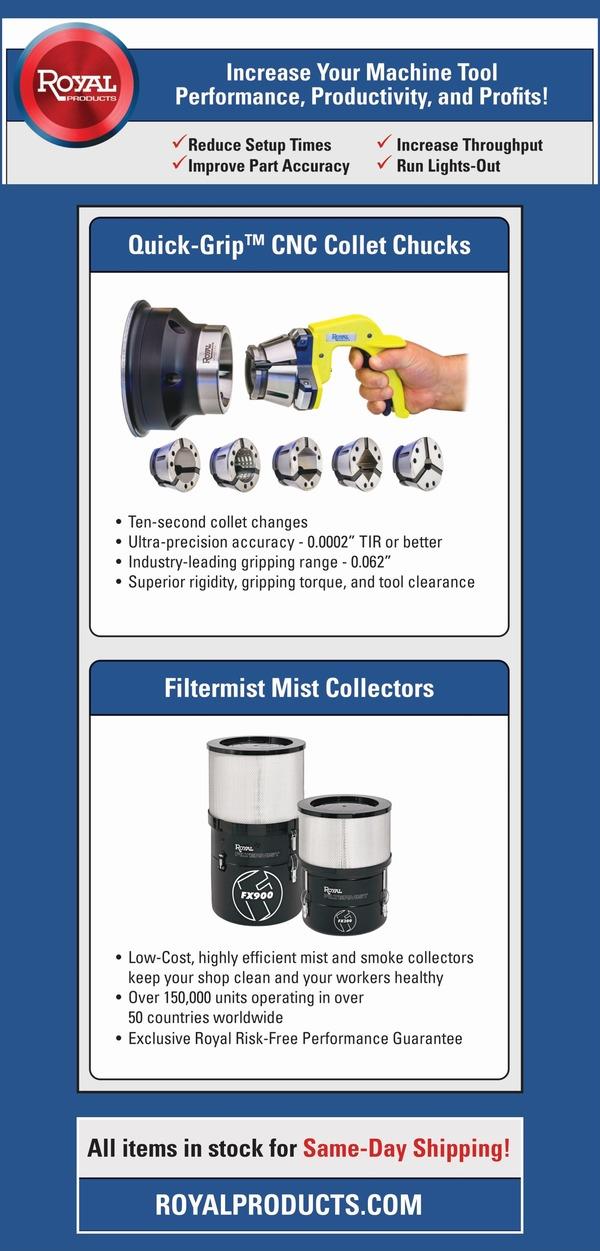
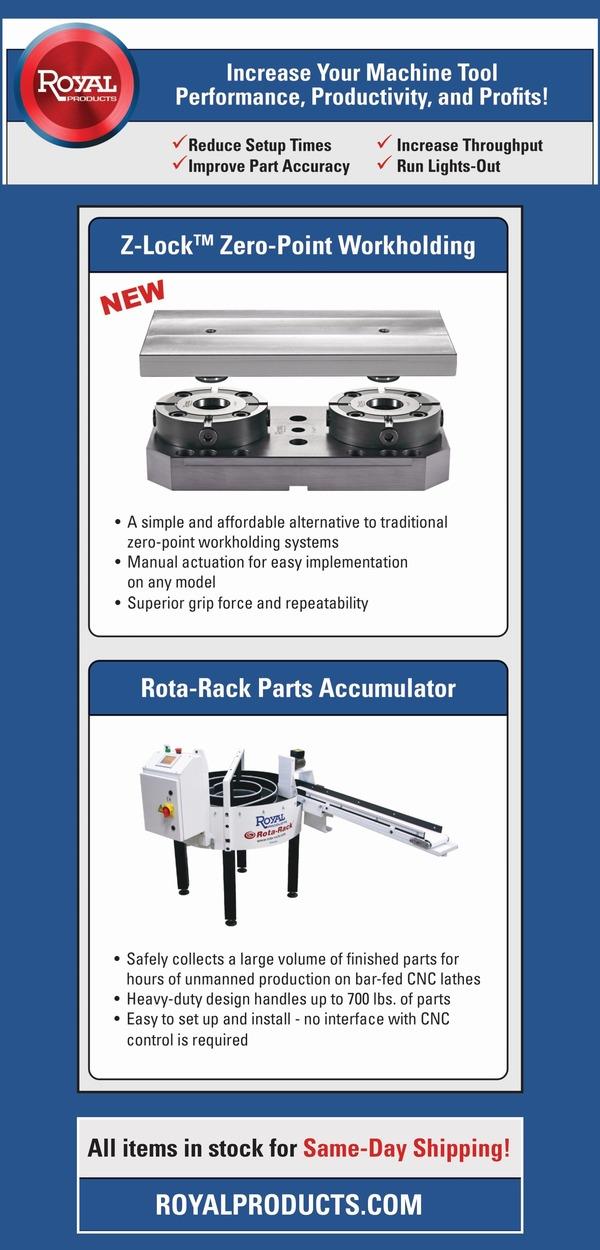

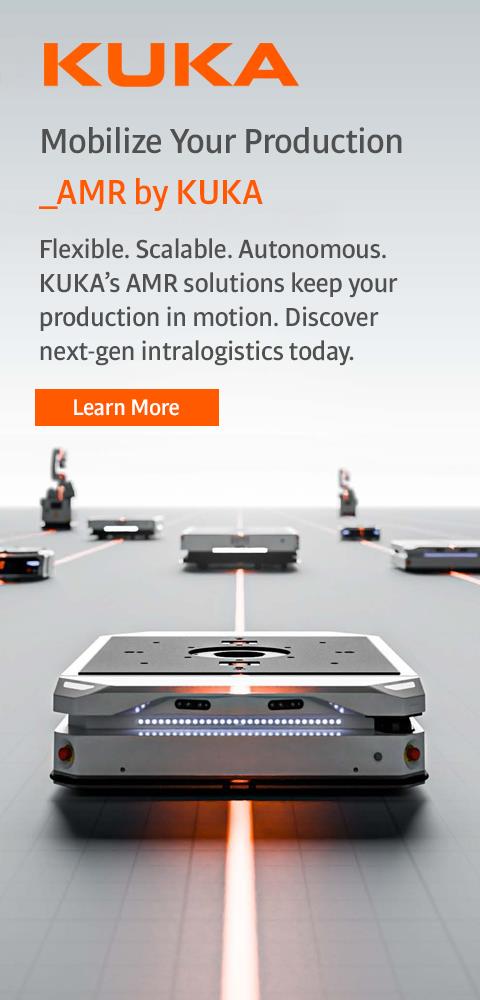
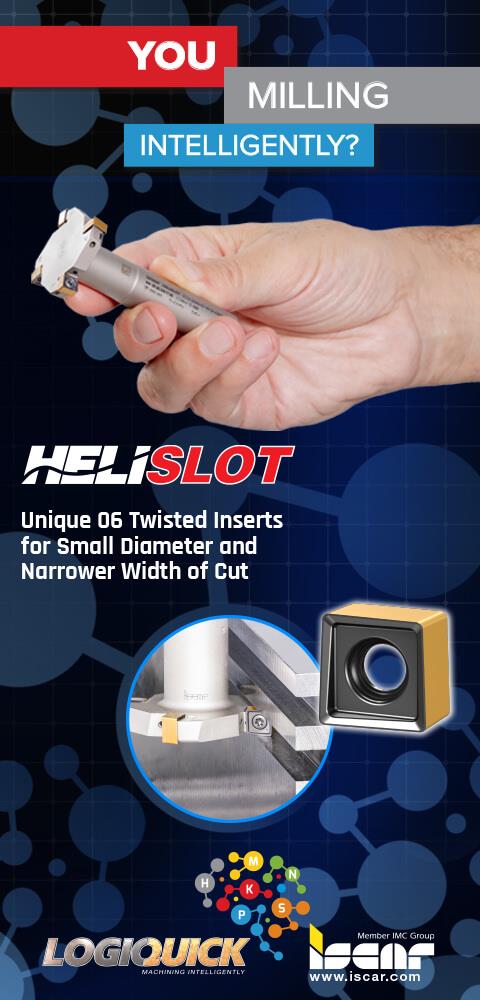
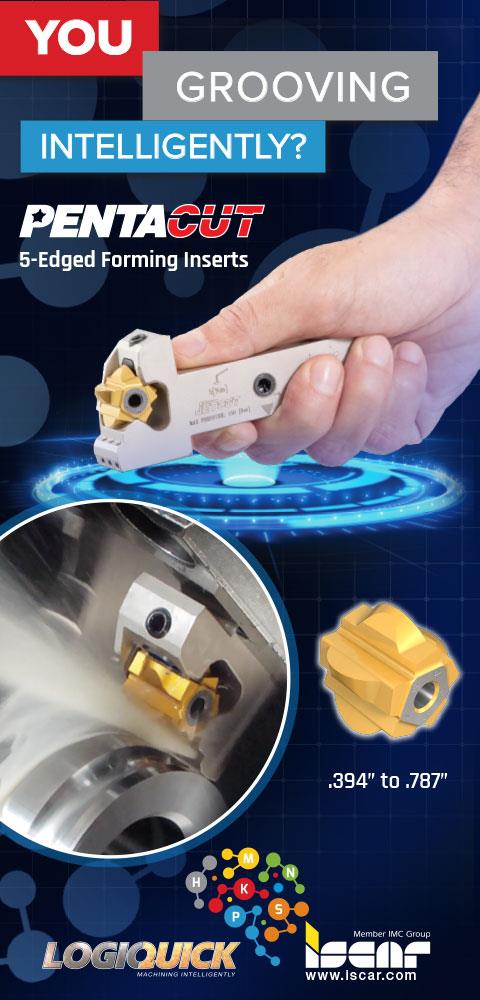
Optical Inspection Systems for Stator Hairpins
September 1, 2022
Marposs offers a noncontact measuring system for performing dimensional verification of hairpins used in stator windings. Through optical inspection using three proprietary high-resolution cameras featuring telecentric optics, this system measures the head, tail and roof of the hairpin with the goal of keeping lengths, widths and twisting under control. This helps to avoid problems during rotor assembly, such as avoiding damage to the insulation paper inside the rotor slots.
"The challenge is to produce single hairpins so that they properly fit the stator grooves," said a company spokesperson. "This is complicated by the fact that hairpins are made of thin copper bar, and therefore, inherently weak. Traditional contact systems, or use of reference profile masks/jigs, can easily deform the intended shape."
The Marposs noncontact system works by positioning the hairpin on tempered glass with reference points for pin placement. The measurement cycle is then initiated by acquiring three images in sequence, one image for each camera. The processing software identifies the pivotal points of the part, enabling reconstruction of the required dimensions and ensuring accuracy. The entire measurement cycle is accomplished in only five seconds.
The system is designed for operation in the workshop or lab environment, and provides the flexibility to measure a variety of parts. It can be provided as a manual-loaded test bench or designed for integration into an automated production line for 100% product inspection.
Optional offerings to complement the optical hairpin inspection system include Marposs SPC software for statistic elaboration and data transfer, and a station for gauging the stripped area of the hairpin.
For more information contact:
Marposs Corporation
3300 Cross Creek Parkway
Auburn Hills, MI 48326
248-370-0404
marposs@us.marposs.com
www.marposs.com
< back