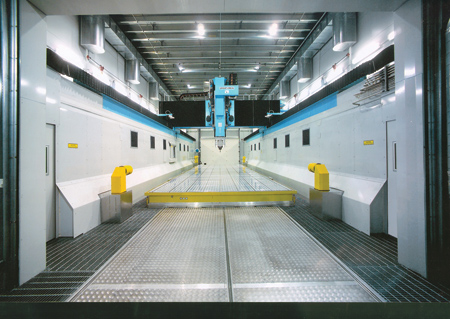
The Droop+Rein high-speed machines are doing all of the finish machining work.
A highly skilled and versatile workforce of engineers, operators and support personnel is working for the Naval Foundry and Propeller Center (NFPC) in the Philadelphia Naval Business Center (formerly Philadelphia Naval Base). The NFPC manufactures submarine propellers for the United States Navy.
NFPC has very large machining capability to manufacture propellers. Because of the time required to build these parts, the challenge the engineers were faced with was finding a way to cut manufacturing times. About eight years ago, NFPC started a research program to test high speed machining on the propeller's copper-based alloy. Successful testing led to a search for high-speed machines large enough to accommodate the largest submarine propellers of up to 24' in diameter.
"When we started to survey the machine tool market, we looked at the traditional companies in the U.S., France and Japan. We did not know Starrag existed, much less its capabilities. After the technical specifications were published, Starrag and another company were selected for the final evaluation based on the technical merits of the offers. Starrag won the contract with the best price and the excellent Droop+Rein FOGS machine they offer," said Faris Ibrahim, Mechanical Engineer at NFPC. "From that day in 2005, we started a relationship with Starrag, which led to another Droop+Rein FOGS purchase in 2012 and three more in 2019-and we will need many more in the future."
Starrag successfully delivered in 2007 and 2012 two high-speed Droop+Rein machining centers. The machines are Droop+Rein FOGS 70 68 TT M30 C, which per the Navy specifications had the following dimensions: X-axis 267"; Y-axis 275"; Z-axis 90"; rotary table 275" with main power drive 2x134 HP. The twins, the biggest machine tools in the history of FOGS machines, are turning, drilling and contour milling the US Navy's submarine propellers.
The next three Droop+Rein machines were successfully delivered in 2019. These machines are FOGS 70 68 M 30 K, FOGS 75 75 TT M30 C and FOGS 85 85 TT M30 C.
"The Naval Foundry and Propeller Center is the U.S. Navy's only submarine propeller producing facility," said Ibrahim. "The Droop+Rein high-speed machines are doing all of the finish machining work. The machines are performing extremely well. They have become the workhorses of our shop. Our investment is paying off with improved surface finish and accuracy."
The machining requirements are very high-the propellers are made of a copper alloy that is difficult to machine. Additionally, the blades have a complex geometry with local accuracies on the order of 0.010" or 254 µm. The propeller has very complex curvatures modeled in a CAM system to produce very complex cutting motion, which the Droop+Rein FOGS machine must reproduce extremely accurately with their six axes. "The capability of the machine control, combined with high-speed cutting, allows us to produce almost mirror finish sculpted surfaces," said Ibrahim.
"These results are also based on special machine tool characteristics," continued Ibrahim. "When we had our first meeting after contract award, we presented the Starrag team with a difficult task. We needed a special head in order to machine between the tightly stacked blades. After many discussions and simulation studies, the Starrag team presented us with a unique head design that eventually became known as `Hammer Head.' This head gave us the ability to easily reach and contour every part of the propeller. It was a brilliant design that really showcased their technical ability."
For Ibrahim, the Droop+Rein FOGS machines were a good example of how turn-key machine tool projects should be handled. Starrag handled everything from the design and construction of a very large foundation, shipping, unpacking, installing and testing the machine tool at the Navy site in Philadelphia with the help of local subcontractors.
"We are very satisfied with these machines," said Ibrahim. "They are performing per the specifications. Starrag's support has been phenomenal and we hope to continue our cooperation for our future machine tool needs."
For more information contact:
Starrag USA Inc.
North American Headquarters
Skyport Business Park
2379 Progress Drive
Hebron, KY 41048
859-534-5201
ussales@starrag.com
www.starrag.com