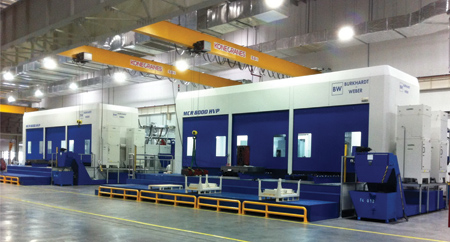
BURKHARDT+WEBER MCR 8000 machine installation
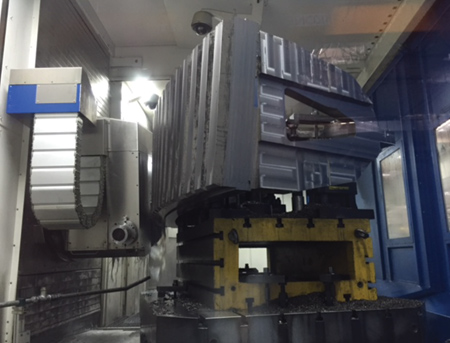
Gashing head cutting teeth
"The economics for manufacturing large segmented special gears is an investment of great magnitude overall, which includes also several expensive XXL machine tools for machining. The BURKHARDT+WEBER MCR 8000 twin spindle machining center creates a highly economical exception, while applying a new machining philosophy," said a company spokesperson.
About six years ago, the BURKHARDT+WEBER team was challenged to supply an economical multitasking CNC machining center for generating segmented gears up to Module 50. These large gear segments with a tooth heights specification for up to 1,500 mm (59") are assembled to create spur gears, helical gears or herringbone gears. For efficient tooth generation with acceptable delivery times, gashing the teeth was the preferred method in cutting the teeth. Some of these gears can be up to 18 meter (60') in diameter. Typically, the generation of these gears requires assembly for machining on a combination of three types of conventional large machines. From turning to milling to gear generation to finishing, the gears are then machined in sequence by relocating the part several times. A very time-consuming process.
The application team's result was the creation of the BURKHARDT+WEBER MCR 8000 special machining center with dual spindle design, making the complete machining process possible on one BURKHARDT+WEBER CNC machine. The Siemens 840 Dsl combines all features needed to perform these demanding tasks. The MCR 8000 is equipped with a dynamic, high torque 5-axis spindle concept to perform all machining operations before and after the gear generation process. For the gear gashing spindle with rotary C-axis for milling the teeth, a special gear box was developed. Furthermore, the gashing unit was equipped with a palletized milling head exchange feature to allow quick exchange of the milling head.
The second gashing head spindle produces up to 4,000 Nm continuous duty torque for powerful milling and quick gear generation. The turning operations are replaced by circular milling with dynamic axis movements. To make the process even more economical, automatic tool exchange is made available for both spindles with a tool capacity of up to 352 tools. A pallet change provides for quick part changeover, thus creating a very productive machining solution, which has proven its economic performance and its technical reliability over several years already. Thus BURKHARDT+WEBER can provide a field proven solution today. Due to the new gashing headstock design, the application can be expanded to the generation of gear racks and furthermore can also machine smaller non-segmented gear sizes of less than 3,200 mm in diameter, which includes the machining of the pinion gears typically meshing with the large gears.
"The result is a flexible and productive CNC machining center replacing three conventional large XXL machines with one productive multitasking process, thus creating an exceptional savings," said the spokesperson. "The overall investment for complete machining of extremely large gears is greatly reduced. The application range is expanded, making the machine more flexible than conventional machines."
For more information contact:
BURKHARDT+WEBER LLC
Machines and Methods
1845 Airport Exchange Blvd.
Erlanger, KY 41018
859-308-6625
info@burkhardt-weber.com
www.burkhardt-weber.com
NORTHEAST
CT, ME, MA, NH, W.PA, RI, VT
INIRAM Precision Machine Tool Inc.
333 North Main Street
Middleton, MA 01949
978-854-3037
www.iniram.com
WEST
WA, OR, ID, MT
Machines & Methods, Inc.
13400 NE 20th Street
Suite 15
Bellevue, WA 98005
425746-1656
www.machinesandmethods.com