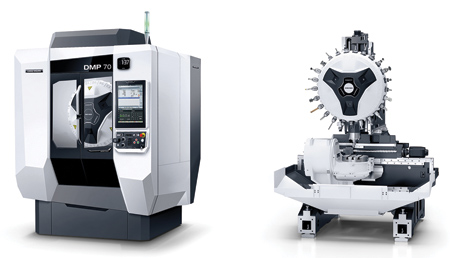
With a footprint of just 46.28 sq. ft., the DMP 70 nevertheless has travel paths of 27" x 16" x 15"
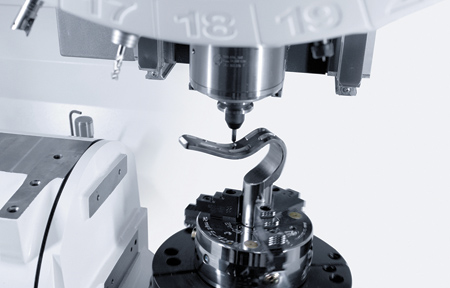
The DMP 70 is a compact production machine for applications in medical technology, job shops, as well as the aerospace sector and other demanding industries.
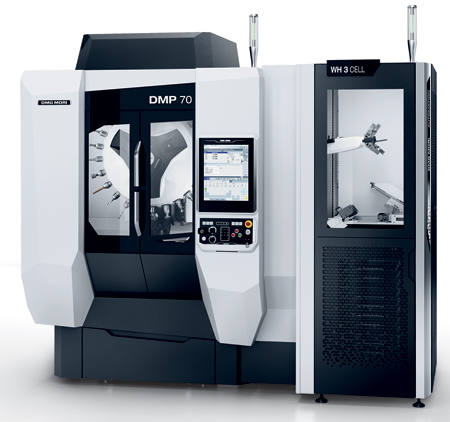
Automation solutions, such as the workpiece handling WH 3 Cell, can be connected from the right, left or front.
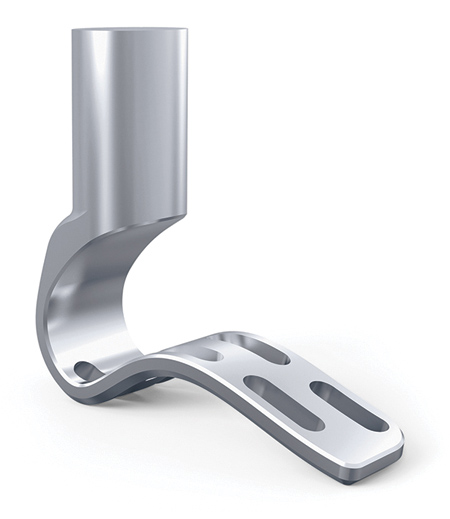
Aluminum prosthetic foot
As the successor of the MILLTAP 700 (with more than 3,000 machines installed), the DMP 70, by DMG MORI, is designed to offer maximum productivity in the smallest space. With a footprint of 46.28 sq. ft., it is 10% smaller than the MILLTAP 700. DMG MORI has designed the compact production machine for applications in medical technology, job shops, as well as the aerospace sector and other industries. Travel paths of 27" x 16" x 15" and the optional integrated rotary table enable 5-axis simultaneous machining. Automation solutions, such as the workpiece handling WH 3 Cell, increase flexibility.
The optimized machine design has made the DMP 70 an extremely rigid production machine, with a metal removal rate that is 10% higher than the MILLTAP 700. The grey cast iron machine bed and enlarged 1.3 in linear guideways are the basis for the 30% faster machining times on demanding workpieces. Additional machining stability has been achieved through the high-strength spindle due to higher accurate preload.
The DMP 70 is designed to be user friendly for machine tending and operation due to the ergonomic stealth design, clear, well-lighted work area and optional automatic doors. Scratch resistant surfaces protect the machine from damage and minimizes cleanup time.
DMG MORI has improved thermal stability with an optimized cooling concept and increased the long-term accuracy of the DMP 70. Direct absolute scale feedback systems provide high levels of positioning accuracy to meet the high precision demands of the target sectors. With reengineered high accuracy components, the DMP 70 has a 60% increased accuracy over its predecessor.
With rapid traverse rates of 60 m/min and an acceleration of up to 2 G in each axis, the DMP 70 offers high speed and acceleration. In its standard version, the DMP 70 is equipped with an inline spindle with a speed of 10,000 RPM and 78 Nm torque. Its fast tool change and chip-to-chip times of 1.5 seconds also contribute to a high level of productivity. The easily accessible tool magazine has a capacity of up to 15 tools with lengths up to 9.8", and a 25-tool magazine is available as an option.
The DMP 70 utilizes DMG MORI's SLIMline multi-touch control with Siemens Operate 4.8. The 19" high-resolution display allows 3D machine simulation to be incorporated into the production process to reduce machining errors.
A portfolio of options completes the DMP 70; with high-speed spindle options, various table configurations, as well as coolant systems and chip conveyors, flexibility is the focus even where the connection of automation solutions is concerned.
DMG MORI can connect the workpiece handling WH 3 Cell from either the left, right or front, and the horizontally automaton door enhances the teach process. The entire WH 3 automation solution has a space requirement of 94.72 sq. ft.
For more information contact:
DMG MORI - Americas Headquarters
2400 Huntington Blvd.
Hoffman Estates, IL 60192
847-593-5400
Service Hotline:
855-DMG-MORI (364-6674)
www.us.dmgmori.com