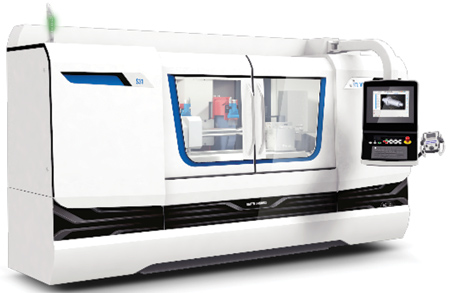
The new STUDER S31 with 1,000 mm distance between centers.
The S31 is designed to perform complex and varied grinding tasks precisely and reliably. It can be used to produce small to medium-sized workpieces with a distance between centers of 400 mm, 650 mm, 1,000 mm and 1,600 mm and a center height of 175 mm in individual, small batch and high-volume production. With a high-resolution B-axis of 0.00005° the swiveling wheelhead enables efficient external, internal and surface grinding in a single clamping.
The foundation of the universal cylindrical grinding machine is the machine bed made from solid Granitan S103. This provides high dimensional stability due to its favorable thermal behavior, while the mineral casting largely equalizes short-term variations in temperature. STUDER has redesigned the machine base geometry and added a base temperature control to help ensure quick and stable production. The fixing of the dressing device on the double T-slot of the longitudinal slide reduces the complexity of set-up and changeover. The S31 features StuderGuide guideways with their damping component in the direction of movement.
The S31 is based on the STUDER T-slide concept. It now has an extended X-axis stroke of 370 mm. This enables a large number of wheelhead variants, which can be precisely tailored to the customer's requirements. Customers can choose between the turret wheelhead with continuously variable B-axis or B-axis with 1° Hirth coupling. The turret wheelhead can be equipped with several grinding wheels. Due to the software for grinding wheel alignment, STUDER Quick-Set, changeover times are reduced by up to 90%. The S31 enables grinding of different diameters and cones with just one grinding wheel and without time-consuming intermediate dressing. This is made possible by the direct drive on the B-axis with a positioning scatter of <1".
"Over a hundred years of grinding experience are invested in StuderWIN, which enables reliable programming and efficient operation," said a company spokesperson. "StuderTechnology also automatically calculates the optimal grinding parameters in a matter of seconds, based on just a little information. This means high quality and a stable process at the first attempt." The optional integrated modules such as StuderForm, StuderThread or StuderContourBasic, extend the functionality of the machine.
The S31 is equipped with a FANUC 0i-TF and is optionally available with the FANUC 31i-B for high speed machining (HSM). The PCU manual control unit enables set-up of the machine close to the grinding process. Non-productive times can be reduced to a minimum with the electronic contact detection function. In addition, the standardized loader interface enables automation of the S31.
Additional benefits include:
- Maximum workpiece weight 150 kg
- Thermal stability due to innovative base temperature control (dbc 650 to 1600)
- Constant cutting speed as standard
- Can be flexibly extended with integrated software modules
For more information contact:
UNITED GRINDING North America Inc.
2100 UNITED GRINDING Blvd.
Miamisburg, OH 45342
937-859-1975
info@grinding.com
www.grinding.com