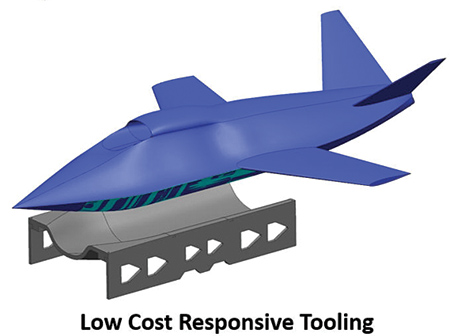
Air Force Research Laboratory conceptual aircraft and full-scale tool
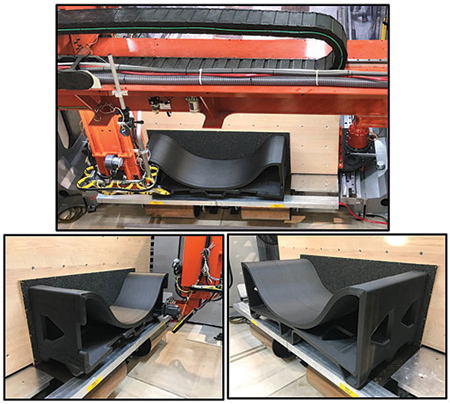
Mid-scale tool-3D printing on the Large Scale Additive Manufacturing (LSAM) machine
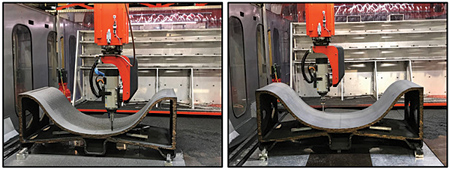
Machining (left) and probe (right) operation on Thermwood LSAM
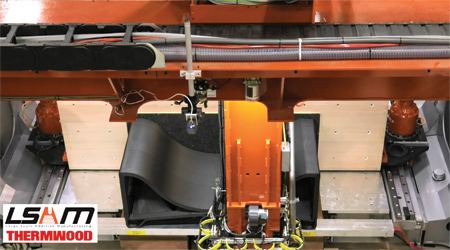
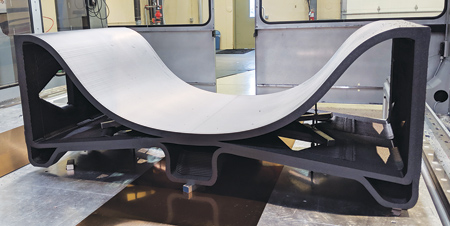
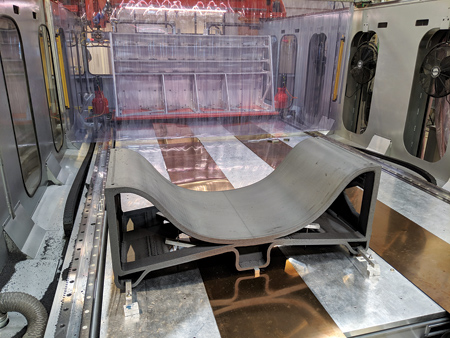
Mid-scale tool printed on the LSAM machine.
The United States Air Force Research Laboratory (AFRL) Manufacturing and Industrial Technology Division (ManTech) expressed interest in large scale polymer-based additively manufactured (AM) composite cure tooling. Boeing submitted an idea to ManTech's Open BAA to evaluate the current state of AM technology with respect to the fabrication of low cost autoclave capable tools for the production of composite aerospace components. The initial demo tool is for an AFRL concept aircraft fuselage skin. Boeing contracted Thermwood to demonstrate the capability of its Large Scale Additive Manufacturing (LSAM) machine.
The Thermwood LSAM offers an innovative AM machine capability with its vertical lay print (VLP). The VLP AM process provides a significant cost benefit by increasing the size components can be printed, thus reducing assembly cost for large tools. To validate the VLP process using high temperature autoclave-capable materials, Boeing and AFRL chose to 3D print a section of the large tool to evaluate the LSAM functionality. The mid-scale tool was printed on Thermwood's LSAM Additive Manufacturing Demonstration machine in Southern Indiana using a 40 mm print core running 25% carbon fiber reinforced polyethersulfone (PESU).
The initial test tool has the same width, height and bead path as the final mold, incorporates all major features of the final mold, but compressed in length being only 4' long. The final tool will be over 10' long. The mid-scale tool set a milestone achievement as the first high temperature tool printed using the VLP system. The mid-scale tool required 5 hours, 15 minutes hours to print with a print weight of 367 lbs. After final machining, the tool was probed for surface profile and tested for vacuum integrity. The tool passed room temperature vacuum test and achieved dimensional surface profile tolerances. The full-scale tool will weigh approximately 1,400 lbs. and require 18 hours to print.
The program is progressing to the next step, producing a full-size tool. Boeing and the Air Force are carefully documenting all operational parameters of the project to transition the technology to production programs. Additive manufactured autoclave tooling offers significant advantages over traditional methods of producing these tools. 3D printed tooling is less expensive and can be fabricated in days or weeks rather than months.
AFRL is very interested in tooling approaches for the Low-Cost Attritable Technology (LCAAT) program, which has a goal to break the cost growth curve and field new systems faster. AFRL Program Manager Andrea Helbach said, "We are interested in additively manufactured tooling's ability to reduce the cost and time to procure autoclave capable tooling. Additionally, AM tooling supports changes in vehicle design with minimal non-recurring expenses."
"Future fielded low cost but capable UAVs will need a responsive materials and manufacturing processes strategy," said Craig Neslen, LCAAT Initiative Manufacturing Lead. "Additive manufactured composite tooling is one of many technologies being evaluated to ensure the industrial base can handle future manufacturing surge requirements as well as accommodate periodic system tech refresh activities, which could necessitate minor vehicle design changes at an acceptable cost."
"LSAM is intended for industrial production. It is not a lab, evaluation or demonstration machine, but is instead a full-fledged industrial AM system intended for the production of large scale components," said a spokesperson. Thermwood has applied for 19 separate patents on various aspects of this new technology, several of which have already been granted and more will be coming as development continues.
For more information contact:
Thermwood Corporation
904 Buffaloville Rd
Dale, IN 47523
800-533-6901
www.thermwood.com