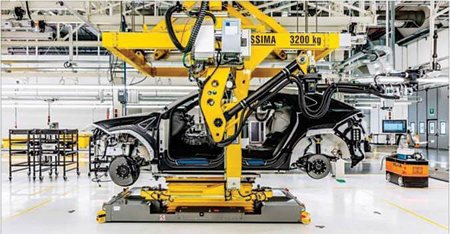
Dürr designed a flexible line configuration for Urus assembly.
The Urus super SUV from Lamborghini is manufactured under the most modern conditions. The Lamborghini plant in Sant'Agata Bolognese, Italy, features highly flexible assembly lines with newly developed automated guided vehicles (AGVs) and ergonomic workstations. As the general contractor, Dürr was responsible for the installation of the assembly lines as well as for the integration and optimization of innovative technologies and processes.
With a view to the market launch of the Urus super SUV, Lamborghini modernized its long-established plant within 18 months during ongoing production. The production space doubled from 80,000 sq. m to 160,000 sq. m, and the overall capacity expanded to 7,000 vehicles annually. Lamborghini entrusted Dürr with developing new production lines for complete vehicle assembly. It is based on a forward-looking layout in which each area can be used flexibly. That allows the line configuration to be modified at any time and adapt to changing requirements.
The conveying system with AGVs, specifically developed by Dürr for the Urus, provides a high degree of flexibility. The AGVs move individual components and bodies separately, instead of one after another in a linear conveyor system as had been the case. They run without rails and are freely programmable like robots. This means that future model series can be manufactured on existing lines, since they can be changed over quickly to accommodate new market scenarios and varied production requirements. The AGVs at Lamborghini come in three different sizes and are suitable for line feeding tasks, the processes in the main line and for subassembly and powertrain operations.
In addition to the AGVs, Dürr installed other technologies that meet the demanding standards for ergonomics in the workplace. These include loading carriers (body on AGV), unloading devices (car from AGV), rotating and vertical adjustable carriers for body transport and lifting, as well as slat conveyors with a lifting table for moving the vehicle into an ergonomic position.
Overall control of the project on behalf of the Dürr Group rested with CPM, its Italian subsidiary specializing in final assembly. CPM and Lamborghini were already working together on layout design for conveyor technology, assembly lines, marriage stations, trim lines and the end-of-line area. CPM was supported by its German colleagues from Dürr Assembly Products, which supplied the x-road roll/brake test stand and adjusted it precisely to meet requirements for production of the Urus model.
For more information contact:
Dürr Systems, Inc.
26801 Northwestern Highway
Southfield, MI 48033
248-450-2000
www.durr.com