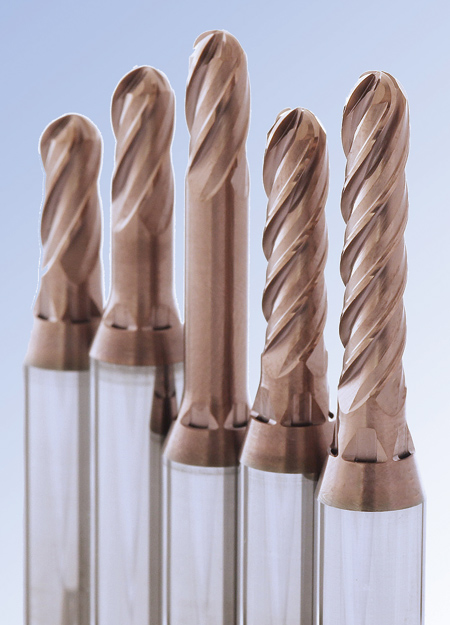
The range of finishing cutters entails several lengths up to milling depth of 5 x d and cutting edge length 4.5 x d. The available diameters go from 1 mm to 8 mm (.039" to .315").
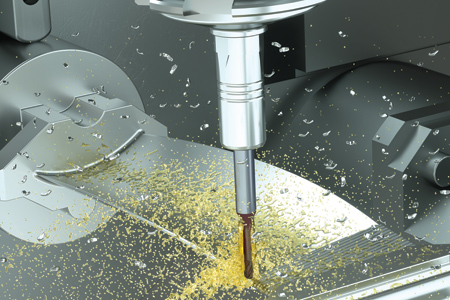
"Massive and continuous coolant flow, which controls the temperature at the edges and provides a chip-free milling area, helps the tool to reach highest performance levels through high chip removal rates, high tool life and enhanced surface quality," said a Mikron spokesperson.
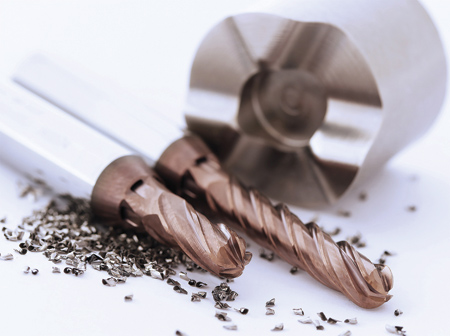
"Complex geometry allows the four teeth finishing cutter to achieve high surface quality-crucial for applications such as bone implants," said a Mikron spokesperson.
Mikron has added to is CrazyMill Cool product line. A four teeth finishing milling cutter with shank integrated cooling is available in diameters of 1 mm to 8 mm (.039" to .315") and for milling depths of up to 5 x d.
This milling cutter is suitable for machining all materials up to a hardness of 54 HRC, and was developed in particular for stainless steels, titanium, heat resistant alloys based on nickel and chrome-cobalt-alloys.
"Heat must be controlled when machining stainless and heat resistant steels, since it cannot be absorbed by the material and chips. The milling cutter of Mikron Tool handles this with three up to five coolant ducts integrated into the tool shank. This delivers constantly a massive coolant jet directly to the milling area, independent of the work position and possible interfering edges," said a company spokesperson. "Because the tool receives continuous coolant, it does not risk overheating. Hence it is possible to simultaneously work with high speeds, feeds and working depths. This results in a high chip volume and increased tool life." Another advantage is the continuous flushing of chips from the milling area. This avoids a repetitive cutting up of chips and the subsequent damaging of the milled surface, and in turn facilitates-in conjunction with the corresponding geometry-increased surface quality.
There is a flute angle of 30º on the shorter tools (with cutting length 2 x d), while the longer versions (with cutting lengths 3.5 x d and 4.5 x d) have a progressive flute angle increase from 30º into 40º. For both versions, the transition of 30º from the radius to the cylindrical section is engineered to create optimal cutting edge corner stability and smooth milling without vibrations.
With its four teeth, the milling cutter is suited for pre-finishing and fine-finishing. For maximal milling performance, the manufacturer clearly defined the corresponding milling cycles and provides detailed cutting parameters. Alberto Gotti, Manager of R&D at Mikron Tool, said, "Tool users often do not venture to use high cutting parameters in the beginning and thus miss to take full advantage of the performance capacity of these tools. There is no need to reduce the parameters because these are all based on practical tests with corresponding materials and specific tools. Therefore, one should adhere to the indicated speeds. Slower is not safer in this case."
With Version N (milling depth: 4.5 x d) it is, for instance, possible to mill at the radius and simultaneously at the cylindrical section and therefore use the entire length of the tool. Especially when finishing or also multipass milling with the head section, Mikron Tool recommends working with an inclination of 15º. In this way, all four cutting edges are engaged in the milling operation, which results in a better surface quality. "Initial positive experiences have been reported in medical applications when milling bone plates made of titanium," said the spokesperson.
In principal, according to Gotti, with all materials, increased efficiency is possible due to cooling and geometry. "This stands out especially when using CrazyMill Cool to machine titanium or stainless and heat resistant materials," he said. "There are several strategies for conventional tools: some manufacturers recommend milling with fast feeds and speeds but with a smaller milling path (ap); others try increasing milling depths but with reduced speeds and feeds. This is where the new 'crazy' cutter differentiates in its use. High machining data are recommended for all parameters." An example is pre-finishing a titanium workpiece with a milling cutter O 3 mm with 150 m/min (5,905 IPM) speed, feed of 0.025 mm/U (.001 IPR) and a milling path ap of 2 x d, reaching with this a chip removal rate of 2,864 cu. mm/min (.175 cu. in.) and simultaneously high tool life of more than 60 m.
Two versions of the CrazyMill Cool Ball Z4 are available with especially long cutting edges. These have progressive spiral flutes (from 30º to 40º) that provide vibrationless milling and additional surface quality improvement. The 30º angle at the tip prevents an accentuated interface between the cutting edges and the cylindrical section and therefore reduces the risk of cutting edge break-out. These versions are especially suitable for side milling because in one or a few mill paths the entire depth can be machined. "Independent of the milling width the Ra values of the X-axis (perpendicular to the milling direction) between 0.1 and 0.3, in the Y-axis (along the milling direction) are in the range of 0.06 and 0.1. These are values that are usually in the range of what is achieved with fine grinding or even ultra-fine grinding," said the spokesperson.
For more information contact:
Mikron Corp. Monroe
200 Main Street
Monroe, CT 06468
203-261-3100
mmo@mikron.com
www.mikron.com