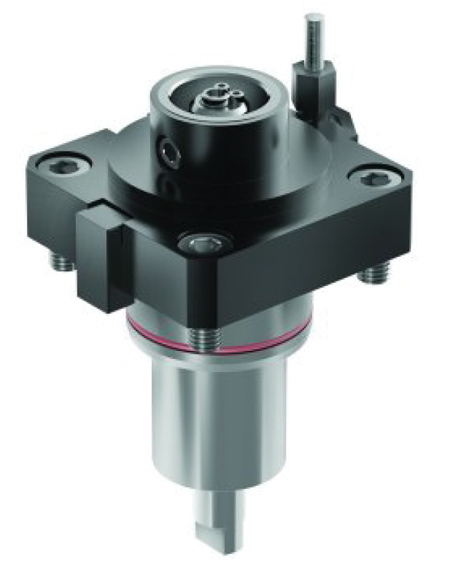
A variety of clamping unit styles and types are readily available.
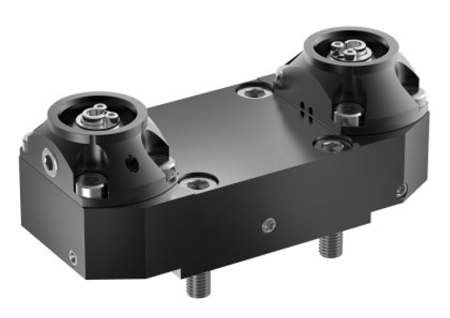
Dual station and offset clamping units provide enhanced flexibility when tooling up today's multi-axis, multi-spindle, Y-axis capable CNC lathes.
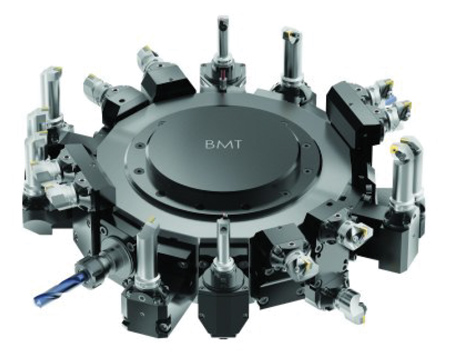
Turret adaptive clamping units are available for the BMT turret shown here as well as Mazak VDI turrets
Kennametal has added to its KMTM quick change tooling solutions with its turret adapted clamping units. Kennametal partnered with lathe tool specialist EWS Tool Technologies to manufacture and support this series of KM adapters.
"The majority of machine shops use the standard turret tooling that came with their CNC lathe, and not a quick-change tooling system," said Michael Schuffenhauer, Manager Tooling Systems at Kennametal. "This indicates a tremendous opportunity for these shops to become more competitive."
"Turret adapted clamping units replace standard block-style turret tooling with quick-change capable adapters made specifically for your brand of CNC lathe," said a company spokesperson. "This is true for both VDI and BMT-style turrets, whether they are rotating or static, and for toolholders with axial, radial and even angular orientation. Quick-change is easy to implement. Total tooling costs are reduced. Concerns over toolholder rigidity are eliminated. And because each clamping unit model was created by EWS to be a perfect match for specific machine tool builders, it is as if the machines were designed with a KM turret."
"Available machining time is one of the key contributors to any manufacturing company's productivity," said Schuffenhauer. "Obviously, reducing set-up is a big part of improving this metric, something at which quick-change tooling systems excel. But there is also the downtime that comes during tool changes, when the operator spends 10 minutes looking for the screw that fell into the chip pan, for example, or the time lost by having to touch off a drill in the middle of a job. KM eliminates this non-productive time, and turret adapted clamping units are the bridge between the system's quick-change capabilities and the machine tool."
Offset and inline clamping unit models are available, as well as models for right- or left-hand placement. Hydraulic chucks, ER collet holders, shell mill adapters, I.D. and O.D. turning cutting units are part of the KM adapter lineup. The clamping unit size range offers interfaces ranging from 32 mm to 63 mm (KM32 to KM63).
"KM uses a pair of hardened steel balls that sit within a tapered tool shank," said Schuffenhauer. "As clamping force is applied, the tail end of the taper expands while the toolholder is pulled back against the locating face. Together with a small amount of interference at the gauge line, this three-point contact provides extremely precise radial and axial positioning and repeatability, as well as high clamping forces. Simply put, it is the most rigid and accurate quick-change system available in this size range."
The ROI calculator on Kennametal.com may be used to quantify improvements in machine utilization. "A potential positive return on investment (ROI) in as little as three to six months is not unusual, and our Customer Application Support (CAS) team is ready to help customers ensure they are getting the value they seek," said Jay Verellen, Kennametal Director of Global Product Management, Tooling Systems. "To use the ROI calculator, enter a few inputs, such as hourly rate and number of set-ups per shift, and it will make sense pretty quickly. In addition, the less tangible effects of KM should also be considered. Set-ups and in-process tool changes are simpler, so having a less skilled operator is not a scary proposition. And flexibility is greatly increased, making it easier to meet customers' changing requirements."
For more information contact:
Kennametal Inc.
600 Grant Street
Suite 5100
Pittsburgh, PA 15219
800-446-7738
www.kennametal.com