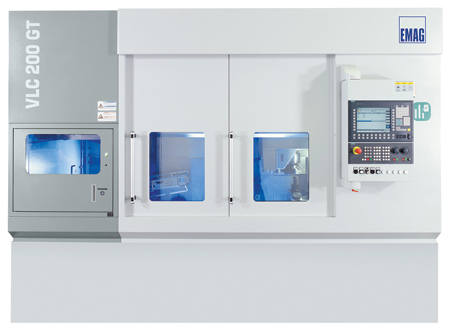
The compact design of the machine means that little floor space is required. It can also be integrated and interlinked easily into an existing production system.

The machining area of the VLC 200 GT: the turning/grinding combination provides reductions in process time for gearwheels.
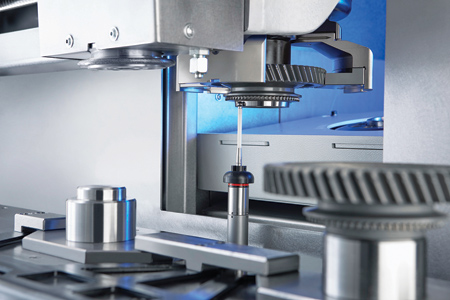
An integrated measuring pin is designed to provide consistently high machining quality.
The production of a large volume of parts with extremely high quality has been a key feature in the production of automotive transmissions for decades. Developments in both the marketplace and technology, however, are continuing to change production at a very fast pace. For example, the number of gears needed for the production of cars has been rising. This increase in quantity is pushing the production volume of gears even higher. At the same time, the competition from new market participants in Asia is intensifying.
What can the transmission builders of OEMs and suppliers do in their production areas to address these developments? "One of the most efficient answers to that question is a solution from EMAG L.L.C.," said an EMAG spokesperson. The EMAG Groups' VLC series offers customers multifunctional machines that perform an array of hard machining processes on the transmission components in quick succession. The company, which is headquartered in Salach, Germany, with its U.S. location in Farmington Hills, MI, specializes in turning and grinding, and has now added another element to this portfolio, the VLC 200 GT. This machine was developed by EMAG engineers especially for the chuck machining of automotive gears. Users benefit from efficient turning and grinding processes in a single clamping operation.
The automobile industry is continuing to spend more money on research-annual increases of between 7% and 8% in this area have long since become standard. OEMs and suppliers in Germany alone recorded more than 34 billion euros in development expenses in the past year, according to a study by the German Association of the Automotive Industry or VDA (Verband der Automobilindustrie). One of the main focal points of this dynamic innovation is the transmission design. Today's transmissions are generally becoming smaller (and therefore lighter), but can simultaneously offer more gear ratios and therefore have more gears and gearing components. This produces optimum speed ranges, and reduces fuel consumption. Each individual gear must be manufactured extremely quickly and very precisely. Given the high unit volumes, the production technology is virtually always a concern for production planners. They try to find solutions that reduce processing time and unit costs, while still continuing to increase the quality of the parts. "The transmission specialists at EMAG have been meeting this challenge with success for decades. A notable quantum leap was achieved nearly 20 years ago when they developed the first pick-up machine for the combined turning and grinding machining of chucked parts," said a company spokesperson. Its key feature was the intelligent combination of the two machining processes in rapid alternation, based on the shape of the workpiece and the quality required-a principle that the EMAG engineers have been continuously improving. With the VLC 200 GT, EMAG has introduced a new machine that ensures major advances in productivity, especially in the machining of automotive gears. Peter Loetzner, President and CEO of EMAG L.L.C., explained their approach: "The high unit volume and quality requirements of gears make them ideally suited to our approach. We now offer users a machine that is completely tailored to these components every detail."
Complete Process, Including Dressing
A simple description of the process gives some idea of the advances in productivity made possible by the VLC 200 GT. To start with, the machine is loaded at exceptionally high speed by the integrated pick-up spindle, a classic EMAG feature. To minimize non-productive times, EMAG has optimized features such as the mechanism of the machining area door. Once the spindle with the part reaches its machining position, the process starts with hard pre-turning of the shoulder and the bore hole in quick succession. Only a few micrometers of material are then left to be removed from the gear. That means the subsequent grinding process, using either aluminum oxide or CBN grinding wheels, takes significantly less time.
Meanwhile, the machining quality also benefits from the combination of turning and grinding: when there is only a small amount of material remaining to be ground away after turning, the specifications for the grinding wheel can be based more precisely on the end quality required-as a result, surfaces with an average peak-to-valley height Rz of less than 1.6 micrometers can be created reliably with the VLC 200 GT. In addition, this multifunctional technology offers users a multitude of possibilities generally: internal and external grinding spindles, scroll-free turning tools, block toolholders and EMAG's 12-station tool turret can all be installed as required.
Lower Tool Costs
There is an additional advantage in terms of tool costs, because during this process the grinding wheel wears down more slowly and therefore does not need to be dressed as often. When it does need dressing, the VLC 200 GT features a separate diamond-coated dressing roll designed specifically for this. "With its separate rotating dressing system and gap control monitoring, the machine is perfectly equipped to exploit the advantages of CBN grinding," Loetzner said. To ensure sustained process reliability and high machining quality, the integrated measuring pin is used to check the diameter and length of the clamped component at the end of the process. Operator comfort and ease of access were important priorities for EMAG's developers, so large doors allow easy access to the machining area. The tools and clamping devices are easily accessible and can be changed quickly and conveniently.
The machine can be incorporated into a plant's production system very well with the aid of a variety of automation systems. One option for this is the TrackMotion system. This automation system developed by EMAG handles transportation from machine to machine with functions such as part gripping, positioning and flipping of the workpiece. "There is also the option of using the VLC 200 GT as a stand-alone machine with simple O-belt automation. This is an appealing alternative for many customers in the Asian markets especially," Loetzner said. "This ultimately demonstrates the decisive advantage of this machine: we are offering producers of gears a custom-fit, flexible, highly productive solution with excellent value for money. That is inevitably going to win out in the marketplace."
For more information contact:
Kirk Stewart
Vice President of Sales
EMAG L.L.C.
38800 Grand River Ave.
Farmington Hills, MI 48335
248-996-4703
kstewart@emag.com
www.emag.com
SOUTHWEST
TX, LA
Eric Klenner
Regional Sales Manager
EMAG L.L.C.
248-595-1530
eklenner@emag.com
TX, OK, AR
Glenn Wise
Regional Sales Manager
EMAG L.L.C.
248-756-1641
gwise@emag.com
NM
Shane Cross
Regional Sales Manager
EMAG L.L.C.
248-207-5365
scross@emag.com
SOUTHEAST
MS
Eric Klenner
Regional Sales Manager
EMAG L.L.C.
248-595-1530
eklenner@emag.com
AL, GA, FL, NC, SC, E. TN, VA
Dave Fitzgerald
Regional Sales Manager
EMAG L.L.C.
248-595-1117
dfitzgerald@emag.com
W. TN
Mark Comeaux
Regional Sales Manager
EMAG L.L.C.
248-938-2097
mcomeaux@emag.com
NORTHEAST
W. PA, WV
Mark Comeaux
Regional Sales Manager
EMAG L.L.C.
248-938-2097
mcomeaux@emag.com
NY, PA, DE, MD, NJ, CT, RI, MA, VT, NH, ME
Kevin Gadde
EMAG L.L.C.
248-938-2430
kgadde@emag.com
Portions of NY and PA
Jeff Moore
Regional Sales Manager
EMAG L.L.C.
519-835-8425
jmoore@emag.com
MIDWEST
OH, KY, S. IN
Mark Comeaux
Regional Sales Manager
EMAG L.L.C.
248-938-2097
mcomeaux@emag.com
N. IN, W. MI
Peter Vandersluis
Regional Sales Manager
EMAG L.L.C.
616-307-7401
pvandersluis@emag.com
E. MI
Jeremy Elder
EMAG L.L.C.
248-962-8963
jelder@emag.com
ND, SD, NE, KS, MN, IA, MO
Bill Konetski
Regional Sales Manager
EMAG L.L.C.
612-804-0857
bkonetski@emag.com
IL, WI
Kirk Stewart
Vice President of Sales
EMAG L.L.C.
248-996-4703
kstewart@emag.com
WEST
WA, OR, CA, NV, ID, MT, WY, UT, CO, AZ
Shane Cross, CMTSE
EMAG L.L.C.
248-207-5365
scross@emag.com