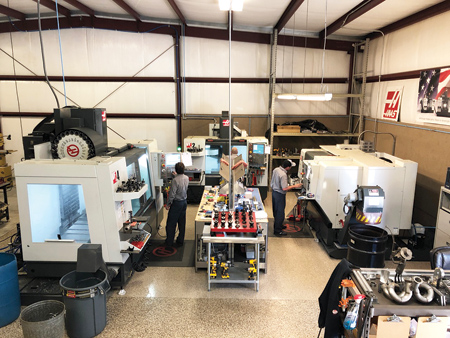
James Nunn programs one of the turning machines on Machine Nunn's 6,000 sq. ft. shop floor.
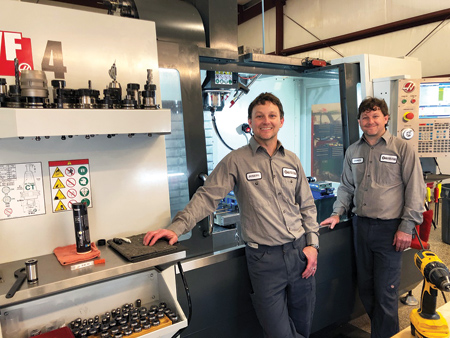
Brothers Joseph and James Nunn with the CNC vertical mill that machines the fixturing plate for Southern Grind.
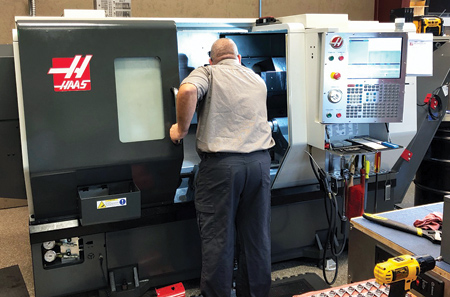
Joe Ward sets up the Haas ST20Y lathe.
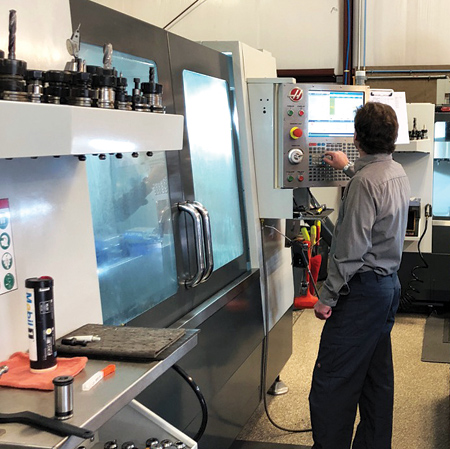
James Nunn programs the flange cap hat for an ocean buoy.
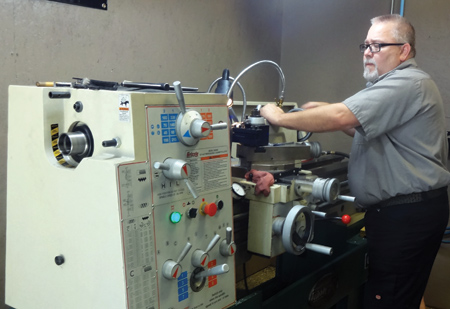
Joe Ward machines a part on the shop's manual lathe.
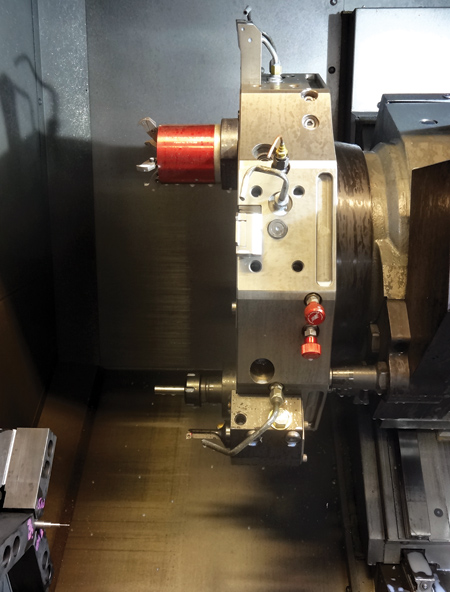
Interior of the Haas ST20Y lathe with live tooling.
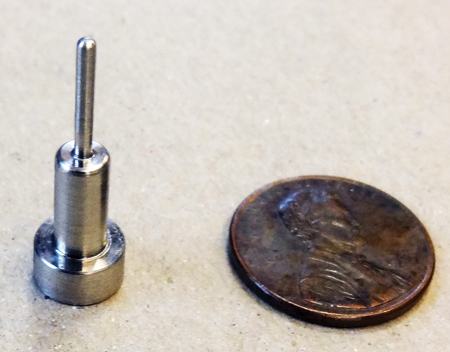
This rifle firing pin was "pushed and turned" in a process similar to that used in Swiss machining.
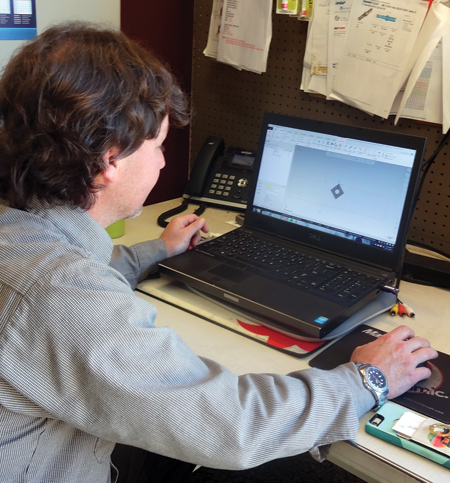
James Nunn programs a lead screw alignment block in Mastercam.
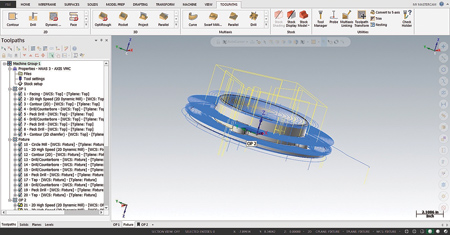
Toolpaths for an ocean buoy, which is machined on a 3-axis mill. The 2-D Dynamic toolpaths remove material quickly. The OptiRough toolpaths roughed out even more material at high speeds.
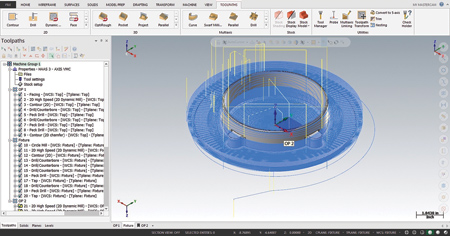
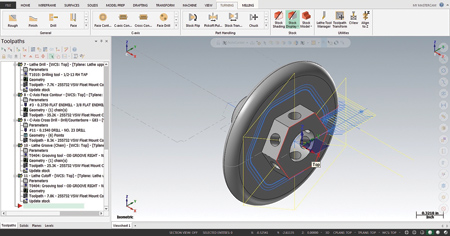
Ocean buoy part programmed in Mastercam 2018 Lathe.
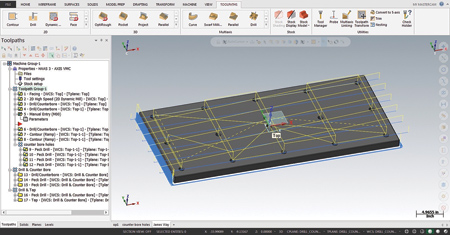
The software's 2D Dynamic milling toolpaths and drill features are programmed to create a 48" x 36" fixture plate for high-end knife company Southern Grind.
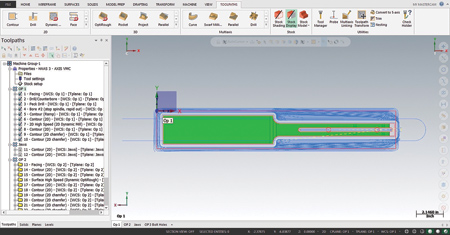
This part, used to check elevation trim tabs on airplanes, was programmed using Mastercam 2018 Mill. 2D Dynamic and OptiRough toolpaths helped remove material rapidly.
For nearly 20 years, brothers James and Joseph Nunn worked in the pits at NASCAR race tracks and race shops, building and maintaining high-speed race cars. For them, every workday was different and, often, exciting. But, as time went on, a bigger challenge kept coming around the bend-starting their own machine shop.
In July of 2015, the brothers opened their doors for business in a 6,000 sq. ft. building James and his wife Shelly built in Statesville, NC. They had limited equipment-one machine, to be exact-but plenty of drive, determination and each other, a worthy combination for a business start-up, they thought.
Initially, the Nunn brothers took in a fair amount of gunsmithing work-threading barrels, making parts, fixing and repairing firearms; hence the play-on-words company name, "Machine Nunn." As more and different work came their way-jobs that required a CNC machine-they purchased a mill and, according to brother, James Nunn, "it all kind of started from there."
"The first year or two was a struggle," James said. "We were getting some work from NASCAR race teams who were outsourcing parts. But doing business in a competitive environment like that-where car part secrets and non-disclosure agreements rule the day-things got complicated." Both James and Joseph continued to work full time jobs and dedicated their evening hours to their machining operation. In January 2017, James made the decision to work at Machine Nunn CNC Shop full time.
Gradually, they grew their customer base, making specialty parts for companies from a number of other industries. They added more equipment, including a second mill and two CNC lathes.
Today, the company produces high quality parts for motor sports, government/military projects and gun manufacturers. "We are really more of a job shop," James said, "making anywhere from one to 2,000 parts for any one of our customers." Machine Nunn operates all Haas equipment, including the VF2 3-axis CNC vertical mill, the ST20Y Y-axis CNC lathe and VF4 3-axis CNC vertical mill. At the end of 2018, they added another Haas lathe, the ST15.
"We do some very small parts and some very large ones," James said. "Parts that are smaller than a penny to something like I am working on right now in the mill that is 11-1/2 inches diameter." James said that they recently made a 48" x 36" fixture plate for Zac Brown's Southern Grind (Peachtree City, GA), the high-end knife company owned by singer Zac Brown.
Machine Nunn works with tolerances ranging from +/-0.0005" up to +/-0. 010". To program their CNC machines, Machine Nunn uses Mastercam CAD/CAM software (CNC Software, Inc., Tolland, CT).
"Mastercam was the clear choice for us," James said. "It is perfectly suited to our needs." The shop uses Mastercam for SOLIDWORKS, which allows them to program parts directly in the SOLIDWORKS environment, enabling them to not only communicate better and more directly with engineers, but also help them in the quoting process. "Generally speaking, everything is easier if you get a visual look at things," Joseph said.
These days, James spends most of his time programming the CNC machines at Machine Nunn. But getting to this point took over a year of his time and his complete dedication to learn how.
"Not being from the CNC side of things made it difficult to get started," James said. "We tried hiring guys who could work at night to help with programming-enough to get a part running. But that had clear limitations."
So, the Nunn Brothers reached out to their Mastercam Reseller, Barefoot CNC (Morganton, NC). For the better part of the next year, Barefoot Applications Engineer Jason Parks spent Saturdays, Sundays and late into many weeknights training James on the software.
"I did everything I could do to move through the learning curve," James said. "I took 10 online instruction classes, which were helpful. But, it was really sitting beside Jason day after day that helped me. I had my own personal Mastercam teacher and I became a sponge. Everything Jason could show me, he showed me. Everything I could take in, I took in. Sometimes I would get it the first time, sometimes it would take two or three; but I was persistent."
James said he also learned a lot by studying Parks' programming when Parks was not there. "I would look at how he did something and then try to relate it to another part. I would look at the toolpaths Jason had set, the numbers and the options he had picked. It was all very instructive."
Today, James said he is comfortable and confident using his CAM software. He cites what he describes as by far, the most valuable feature of the software for him: Dynamic milling. "It just does everything for you," he said. Then James went on to explain what he meant by that, using the job he was working on that week.
"The part is 11 inches around and the stock is 11-1/2 inches, with part of the circle going in to 6 or 7 inches. Instead of doing a contour with multiple paths and having to figure out the math, the number of passes, the step-overs, and feeds and speeds, I just programmed a Dynamic toolpath and said, `My part is this big and I am going to this size and I only want to step over this much, and I do not want to hit this part; but I do want to cut from here.'
"And you just enter the numbers, click on the lines that you want to cut from and to, define the avoidance region with a cut from, a step over, a feed and speed, and you tell it how deep to go.and-boom!-there is your toolpath," he said.
"Plus, the Dynamic motion takes all the material away in one simple, continuous, non-stop, uninterrupted cut," he added. "Not only does that make better parts faster-because it is not lifting, stopping and starting again-but it also extends the life of the tool." It is the proprietary algorithms programmed into the software that detect changes in the material, keeping the endmill constantly engaged with the material.
James noted that, on that job he described, he was doing 91.7 IPM at 7,643 RPM.
"I know people say that you can do/or push the machine and endmills," James added. "But I am an owner/operator. I can make endmills live a long time. I am at a 60% stepover and at full depth of cut (2 inches) and I think it was about a 0.0005-0.0007 inch per tooth (IPT)."
"I understand that is conservative," he continued, "but I also know that when you stay engaged in the cut, you are not doing that start/stop shock that is tough on endmills. We are a job shop, a Mom-and-Pop. Money is tighter here than in bigger shops. So, if I can slow down a little bit and get three times more out of my endmill, that is what we do. To me, my time is not worth as much as saving on the end mill."
In addition to Dynamic milling, James said he is now relying pretty heavily on the software's tool library, resulting in a better quality job and in a significant time saving.
"The library gives me a starting point, even with feeds and speeds," James said. "At this point, I do not 100% understand how to build tools. But, especially in the 2019 release, Mastercam's made it a lot easier. Instead of building a full tool, if I have got an end mill, I just pull it in and change a couple of numbers. Instead of spending the extra five or 10 minutes building a tool, it is already there. Plus, the tool is more accurately built in the software. And, of course, with a more accurately-built tool, you make a more accurate part."
James said that they are now saving all their usage data in their tool library, which the Nunn brothers anticipate will help them be competitive when quoting jobs going forward.
The Nunn Brothers rely on Barefoot a lot less now. "Every once in awhile, we lean on them. But we do a lot on our own," James said.
But their gratitude to Barefoot for all the training and support they have gotten makes them eager to pay it forward. The brothers are looking for ways to partner with Barefoot to make their shop a hands-on training center for younger people going to school for CNC machining and programming.
"The truth is, we do not get machinists out of the community college," Joseph said. "We get guys that have a degree, but they still have to be trained. In smaller shops like ours, you need people who can come in and help you, versus someone who needs to be trained."
"I also think there is a lack of machinist/programmers. We would love for Machine Nunn to be a learning atmosphere," Joseph said. "We intend to keep exploring how we can become a part of education and training beyond the classroom."
Meanwhile, in just three short years, Machine Nunn has built a reputation for expertise in welding, building car parts and machining specialty parts, firearms and gun barrels.
"These guys are at the point where they are ready and willing to take on jobs that the more experienced companies are turning down," said Jimmy Wakeford, President and CEO at Barefoot.
"It is all about perseverance," Joseph said. "There are a lot of people who just quit and say, `We cannot do that.' My brother and I have been working together for over 20 years and anywhere we have worked, it was never, `We cannot do that' but, rather, `We will figure it out.'"
For more information contact:
Machine Nunn CNC Shop
1235 Old Mountain Road
Statesville, NC 28677
704-873-4931
www.machinenunn.com
CNC Software, Inc.
671 Old Post Road
Tolland, CT 06084
800-228-2877
info@mastercam.com
www.mastercam.com