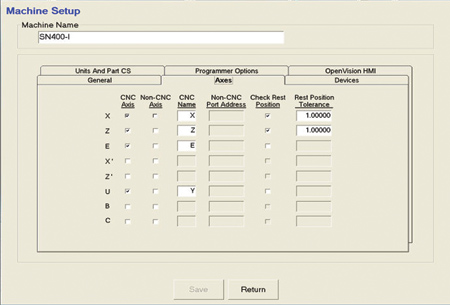
Open Vision Grind shows machine set-up.
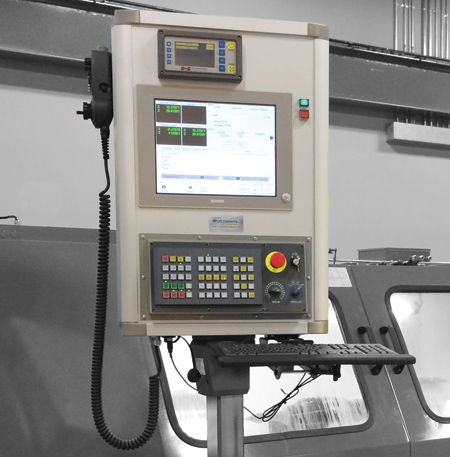
Software package called Open Vision Grind
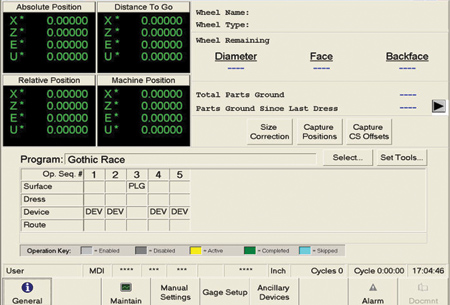
The FANUC open-architecture control displays the progress of the grind operations.
Most old grinders were built for a specific application and since controls, such as FANUC, did not have the exact options required for grinders at the time, OEM's developed their own proprietary controls. In the years since, many OEMs have gone out of business or simply stopped supporting these legacy controls. Fortunately, today's advanced CNCs can replace these obsolete controls and breathe new life into old grinders. In some cases however, special software that runs on an industrial PC may be needed to provide the unique functionality required by grinding machines.
Control and grind process engineers at CNC Engineering, Inc., a FANUC retrofitter, recognized this issue years ago and developed a grind specific software package called Open Vision Grind for I.D., O.D., Vertical, Roll, Blade Tip and specialty grinding machines. "Since its inception, Open Vision Grind has been installed on hundreds of new and retrofitted grinders around the world," said a company spokesperson.
Taking advantage of FANUC's FOCAS2 open-architecture technology, CNC Engineering, Inc. connects an industrial PC to a FANUC control via a high-speed serial bus (HSSB) card and fiber optic cable. Open Vision Grind software is a modern, conversational programming interface, which allows grinders to be programmed without ever having to deal directly with NC program commands. After defining a new operation, the engineer or operator simply enters the parameters required for the operation in an easy-to-use format. When the machine is in operation, the most relevant information is displayed on the main screen, along with necessary display of the progress of the grind operations.
The conversational programmer also allows for programming of multi-surfaces, multiple dressing devices and multi-wheel and / or wheel heads in the same program. Furthermore, the conversational programmer supports a variety of ancillary devices for controlling such things as auto-loading systems, swing down dressers, probing, various gauge interfaces and tool and quill auto-changers. An off-line programmer is provided with each system so programming can be done either at the machine or a remote PC.
Taking full advantage of the FANUC control, the software also includes the ability to program by part reference. This is accomplished by employing a separate coordinate system for the workpiece. The X-axis zero point can be placed either at the workpiece centerline or at a reference surface on the workpiece. The Capture Positions feature enables the operator to quickly resolve workpiece offsets and dresser alignment for easy set-up.
Additional Open Vision Grind features include:
- Vector, Plunge, Oscillation, Contour grind types
- Multiple wheel, Dress and Work spindle control capability
- X, Z, X, Z, E, U, W, P and C-axis control
- Multi-path capability (multiple grinding applications simultaneously)
- Database mapping of the grinding process (interface to engineered grind models)
- CBN wheel control with adaptive cycles available
- Gap Elimination, AE sensor interface, and integral gauge interface offerings
- Inch/Metric and Radius/Diameter switching automatic function
- Integral CAD like programming for dress and grind contouring
- Visual programming with graphical programming screens
- Database sharing amongst machines
- Offline programming software
- Cycle time monitoring
- Process tools, real time process data capture with graphing
- Visual as well as descriptive display of cycle while in process
- Machine configuration mapping allowing customization per machine
- Built-in debugger allowing offline analysis
- Custom screen development.
There are two ways to implement Open Vision Grind to increase grinder productivity:
- Grinders can be retrofitted with a new FANUC CNC and Open Vision Grind
- Grinders equipped with FANUC series 16i/18i/21i controls, or newer, can be upgraded with a PC front-end and Open Vision Grind.
For more information contact:
CNC Engineering Inc
19 Bacon Rd
Enfield, CT 06082
860-749-1780
www.cnc1.com