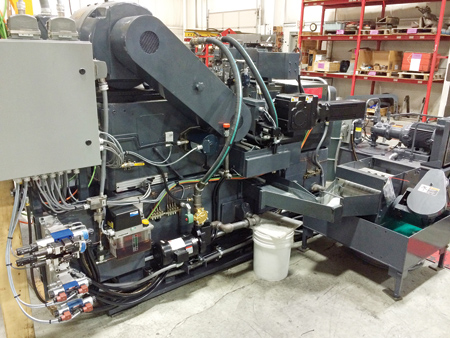
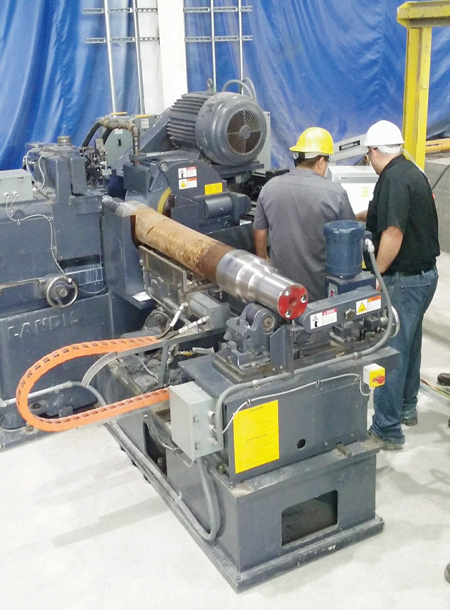
Extensive mechanical and electrical upgrades to this Landis centerless grinding machine include a new Flexium CNC system from NUM.
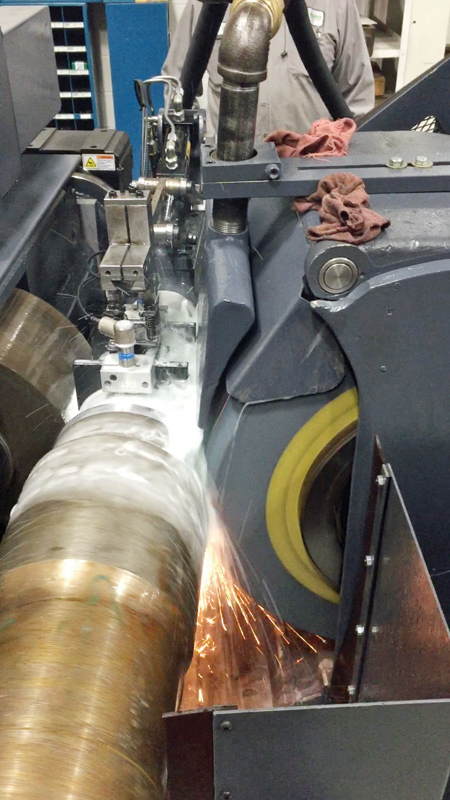
The machine's plunge grinding cycle is controlled by a servomotor-driven axis, utilizing feedback from a linear encoder.
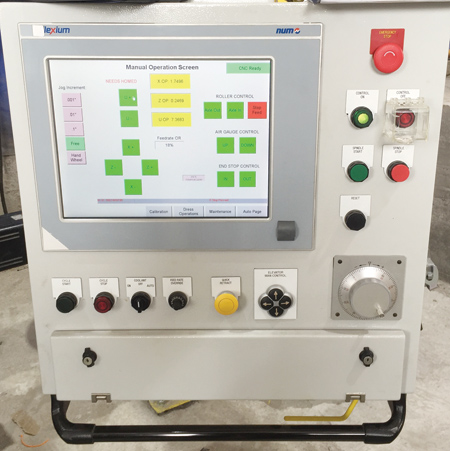
The machine's new control console incorporates a Flexium operator panel with a touch-sensitive display screen.
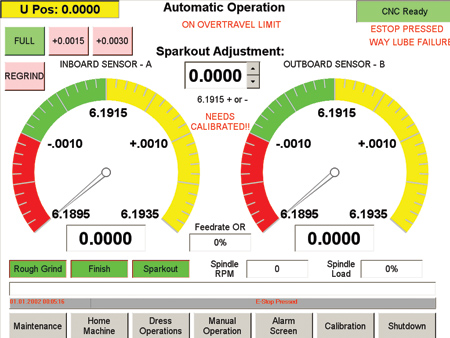
During grinding, the main control screen displays two large analog-style dials that allow the operator to monitor the tolerance of axle taper very easily and accurately.
A comprehensive upgrade of classic high power centerless grinding machine tools is helping a leading railcar axle manufacturer to greatly simplify precision grinding operations on axle forgings. A key element of the project - which has been managed by APeC Integration Services, Inc - is the retrofit of customized CNC control based on NUM's powerful Flexium platform.
Based in Wattsburg, PA, APeC is an electrical systems integrator specializing in upgrading machine tools with modern PLC and CNC control systems. Established in 1989, the company has specialized in enabling clients to maximize the longevity and performance of their machine investments. Key retrofit services include upgrading servo and spindle motors and drives, PLC integration and custom machine controls and complete CNC replacement.
The machine tools in this particular project are high capacity Landis centerless grinders, which utilize a dressable grinding wheel and a plunge grinding cycle to create precision profiles on railcar axle journals. During grinding, both the axle workpiece and the grinding wheel rotate in the same direction, which means that the two surfaces are moving in opposite directions at the point of contact, resulting in smoother operation. Once the machine is up to speed, the grinding wheel is fed - or plunged - into the workpiece and makes continuous contact with a single point along its length. The plunge action is controlled by a servo-driven axis grinding at several feed rates, with transition points monitored by in-process gauging. A built-in automated two-axis dresser system with a diamond tipped tool is used to dress the grinding wheel whenever necessary.
"This is the second time that APeC has improved the performance of these grinders with control systems based on NUM CNC kernels," said a company spokesperson. The original machines were hydraulically actuated and equipped with tracer type wheel dressing systems. In the mid 1990's, APeC performed a full mechanical and electrical upgrade on each machine that included retrofitting a modern CNC system and in-process gauging instruments. "On that occasion, the company based the upgrades on NUM's Power 1060, which at the time was regarded as one of most flexible and user-friendly CNC systems on the market," said the spokesperson.
After a further 20 years' full-time service in a busy production environment, the machines became due for another mechanical and electrical upgrade. APeC had supported the machines and worked closely with their operators throughout this period, during which time it had also developed a number of ideas for making the machines even easier to operate and more productive. The upgrade program offered the ideal opportunity to put many of these ideas into practice.
To expedite machine upgrade and minimize the impact on its customer's production schedules, APeC managed a three-way development partnership. All major mechanical re-design, hydraulic, lubrication and geometrical rebuilding aspects of the project were handled by EURO Machinery Specialists, Inc., a company with some 45 years' experience of refurbishing and modernizing high value metalcutting machine tools. On the control side, APeC collaborated with NUM USA to develop a unique and intuitive human machine interface (HMI). This enables operators to learn how to use the machines very easily and quickly - even if they are unfamiliar with these types of grinders.
"A key project goal was simplifying machine operation as much as possible. NUM's open Flexium CNC platform provides the control flexibility and HMI customization facilities that we needed to develop individual, task-oriented screens," said Dave DeCoursey of APeC. "The user interface is consequently now much more ergonomic. Most operations, such as offset calculations, calibration, dressing and automatic grinding cycle initiation, are now performed using single, virtual pushbuttons that are only displayed when appropriate."
Each machine upgrade uses several NUM products, including the CNC kernel, touch-sensitive operator panel, servo drives and motors. The Flexium CNC system uses EtherCat I/O communications, making it simple for APeC to implement an advanced plunge depth control architecture. The in-process gauging instrumentation previously used for this aspect of machine operation has been replaced by a linear encoder, which facilitates fast and accurate depth control, as well as providing real-time feedback to the operator throughout the grinding cycle. The main control screen features two large analog-style dials, supported by digital displays, which derive their input data from separate measurement probes located along the length of the axle journal, allowing the operator to monitor taper tolerance.
The client and application specific HMI software that APeC has developed for the grinding machine upgrade is task oriented. It uses individual screens that are tailored to the application, with clear context-sensitive functions that help to prevent human error. By using the Extended NCK Access (ENA) facilities of the Flexium CNC controller, each custom PLC-driven visualization can control and monitor the CNC functions directly. This form of control approach is especially useful for automated teach type functionality, such as guiding an operator through machine start-up and preparing for automatic cycles.
For example, the start-up screen initially displays only the status of the CNC system and a single `Shutdown' button. As soon as the CNC system indicates that it is ready, the start-up screen displays two additional buttons: Home Screen and Manual Operation. When the operator touches a displayed button and causes a change of screen, the software automatically alters the CNC mode accordingly and selects the corresponding part program if applicable. By confining the operator's available options to just those that are appropriate at the time, the software helps to ensure consistent and efficient machine use.
Another major advantage of this type of control approach, with extended access to the NCK, is that it can be used to help the operator with tool offsets and adjustments to part program dimensions. When the grinding wheel or dressing tool is replaced, the operator can manually position the tool on the desired surface of the wheel, access a password-protected screen and then simply press a button. The offsets are calculated and pushed into the dressing program automatically, using the ENA facility. This same facility allows the operator to alter dressing dimensions and sparkout setpoints simply by adjusting a value up or down - these are then pushed into the corresponding part program.
"The open architecture and advanced functionality of Flexium CNC systems enable engineering companies to implement innovative machine control solutions for retrofit or new machine tool projects," said Steven Schilling, General Manager of NUM Corporation in Naperville, IL. In this instance, APeC and Euro Machinery Specialists, with NUM's support, have created a CNC retrofit that adds significant value to the customer's existing manufacturing facilities."
For more information contact:
Steve Schilling, General Manager
NUM Corporation
603 East Diehl Road, Suite 115
Naperville, IL 60563
630-505-7722
sales.us@num.com
www.num.com
APeC Integration Services, Inc.
8139 Venshire Drive
Wattsburg, PA 16442
814-739-2590
apec2000@aol.com
Ron or Karl Engelke
EURO Machinery Specialists, Inc.
N59 W14272 Bobolink Ave
Menomonee Falls, WI 53051
262-252-4280
info@euromachinery.net
www.euromachinery.net