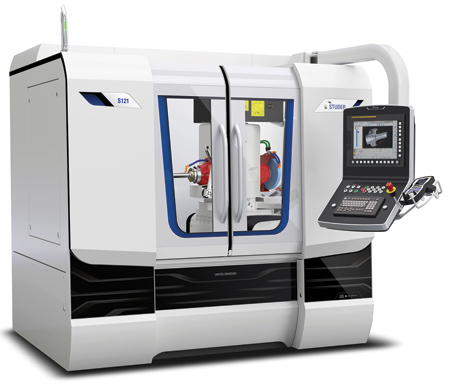
The S121 radius internal cylindrical grinding machine with an exceptional price/performance ratio has a swing diameter of 250 mm and grinds workpieces up to 300 mm.
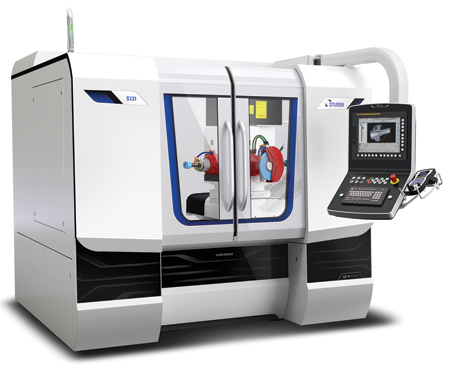
The S131 radius internal cylindrical grinding machine with 4-position spindle turret with direct drive has a swing diameter of 300 mm and grinds workpieces up to 300 mm.
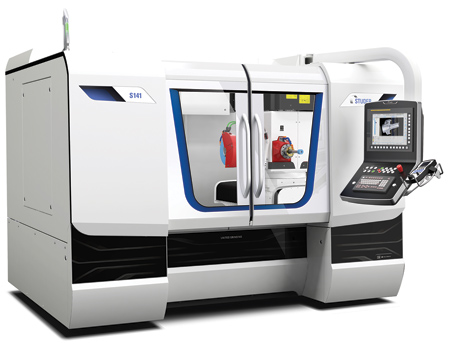
The S141 radius internal cylindrical grinding machine for larger workpieces has a swing diameter of 400 mm and grinds workpieces up to 300 mm.
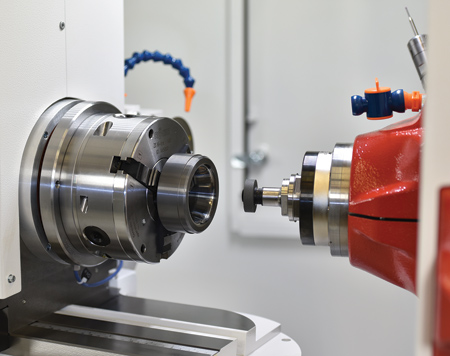
Grinding internal tapers and radii on a die
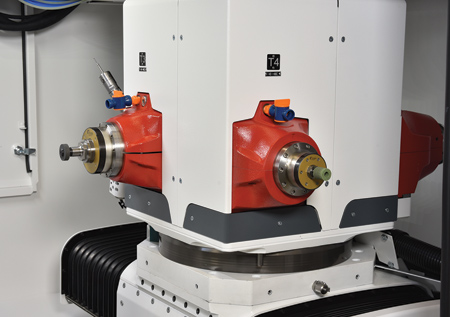
4-position spindle turret (high-precision) with direct drive
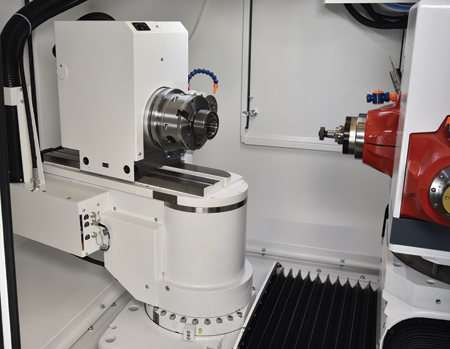
Stable B-axis with direct drive for simultaneous radius grinding
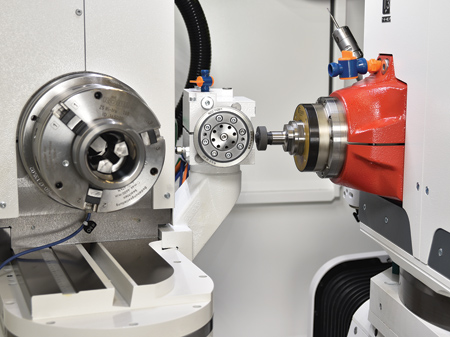
Thermally stable and rigid dressing unit
As part of its recent Motion Meeting 2016 in Thun, Switzerland, United Grinding presented its latest technologies for internal and radius grinding. What still appeared as a separate machine with the S141 universal machine (component length up to 1,300 mm) in May 2014 has evolved into a complete machine platform with the universal machines in the S141 and S151 series in autumn 2014, the S131 universal machine and the S122 production machine in spring 2015 as well as the S121 universal machine in autumn 2015. STUDER is now completing this platform. The Thun grinding machine specialist is bringing three new radius internal cylindrical grinding machines to market, to replace the CT700 and CT900 models.
The main fields of application of the new S121, S131 and S141 radius grinding machines are the manufacturer of dies - especially in the packaging industry - where tungsten carbide and ceramic are primarily processed, and the production of hydraulic components such as axial pump pistons, guide plates and housings made of hardened steel, cast iron and copper. Other fields are the production of complex workpieces with several tapers greater than 20° to 90° in a single clamping, where the main applications are in watch and medical technology with extra-hard materials such as industrial ceramic, sapphire and tungsten carbide, as well as the manufacture of human implants for shoulders, knees and hips from ceramic and titanium.
In the past, this range of parts was covered by STUDER universal internal cylindrical grinding machines CT750 and CT960. With its market entry, the S121 radius grinding machine will now take over the range of applications of the CT750, while the S131 has been designed for the previous component range of the CT960. New with the S141 radius grinding machine is that the machining of larger workpieces is also now possible. For the user, this means in figures: The swing diameter above table is 250 mm for the S121, 300 mm for the S131 and 400 mm for the S141. External diameters up to 160 mm can now be machined with an external grinding wheel 250 mm in diameter. The maximum length of parts including clamping device is 300 mm for all three radius grinding machines, and the maximum workpiece weight including clamping device is 100 kg.
"There are good reasons why STUDER is replacing the CT models, which translate into increased customer benefit. First and foremost, a higher level of technology has been achieved with the new radius grinding machines," said a company spokesperson. This is evident in the machine bed, which now comprises of Granitan and offers higher dampening levels, thermal stability and guidance accuracy. It is also reflected in the StuderGuide guideway and drive system with linear motors, which features high wear resistance, a long working life and high dynamics (interpolation possibility). The main benefit which customers can derive from the new machines is the extended range of parts possible due to the larger size of the machine, and the new dressing concept which, due to the new arrangement on the B-axis (simultaneously swiveling workpiece table) is not only simpler, but also offers thermal stability and mechanical rigidity. "The fact that the new S121, S131 and S141 are now also manufactured according to the Thun modular principle also means non-variable parts in maintenance and service and consequently a higher availability of service technicians. It also means harmonization of the components and, with the new design and improved ergonomics, an increase in the machine's value," said the spokesperson.
"With StuderSIM, STUDER answers the question of what an operator needs in order to be able to machine complex parts - often in a single clamping. The answer: An assistant, with which workpieces - derived from a drawing - can be completely defined, all necessary geometric data for the grinding cycles can be generated and with which the grinding process can be checked and visualized by means of simulation on a PC or on the machine. StuderSIM is this powerful assistant," said the spokesperson. It is complemented by hardware which features the previously mentioned Granitan machine bed and the StuderGuide guideway and drive system with linear motors. It also includes X- and Z-axes in a cross-slide arrangement as well as a cross slide, which in the case of the S121 can either take one spindle, two spindles in parallel or two spindles on a hydraulic turret, and in the case of the S131 and S141 comes with a 4-position turret with direct drive. The machines are also equipped with a workhead on a simultaneously swiveling B-axis, a dressing spindle or a fixed dresser on the B-axis and a measuring probe on the grinding head. Other features are the enclosure and the control console in the STUDER design.
The S121, S131 and S141 radius grinding machines differ from the universal cylindrical grinding machines of the same name in a number of technical details. The B-axes of the radius grinding machines are set up simultaneously and offer interpolation (from -60° to +90°), while the universal cylindrical grinding machines have a swiveling table, which can be positioned from -10° to +20°. In addition, the spindles on the radius grinding machines are arranged at the rear of the turret, while this is the other way round on the cylindrical grinding machines: they are at the front. There are also differences in the dressing concept. The radius grinding machines have the dresser on the B-axis, while the cylindrical grinding machines are equipped with two swivelling dressers. Last but not least, the S121 to S151 cylindrical grinding machines use the STUDER operating system StuderWIN, while the new radius grinding machines use the StuderSIM operating system.
"With the market entry of the S121, S131 and S141 radius grinding machines, the platform of STUDER internal cylindrical grinding machines is now complete and rounded," said the spokesperson. In addition to the new radius grinding machines, the platform includes the simple S110 and S120 machines, the S121 to S151 universal internal grinding machines and the S122 production internal grinding machine. Five machines have been replaced (S120, S145, S151, CT700, CT900), enabling four new market segments to be opened up. The S121 universal internal grinding machines are small machines for a large application range, the S122 production internal grinding machine is a machine for large component output and high availability, and the S141 and S151 universal internal grinding machines (700 and 1,300 mm) are machines for long workpieces. Finally, a fourth market segment is opened up with the new S141 radius grinding machine for parts up to 400 mm in diameter.
For more information contact:
UNITED GRINDING North America, Inc.
510 Earl Blvd.
Miamisburg, OH 45342
937-859-1975
info@grinding.com
www.grinding.com
Southwest
E. TX
Charles Harter
CJ Harter & Son Machinery Inc.
550 Westcott, Suite 375
Houston, TX 77007
713-227-7221
harterhou@sbcglobal.nex
AR, LA
Steve Wherry
Cardinal Machinery
7535 Appling Center Dr.
Memphis, TN 38133
901-377-3107
s.wherry@cardinalmachinery.com
www.cardinalmachinery.com
NM
Mike Geoffroy
The Geoffroy Company, Inc.
5910 S. University Blvd, C-18 #211
Greenwood Village, CO 80121
303-756-3684
TGCIdenver@comcast.net
Southeast
AL, MS, TN, FL (Panhandle)
Steve Wherry
Cardinal Machinery
7535 Appling Center Dr.
Memphis, TN 38133
901-377-3107
s.wherry@cardinalmachinery.com
www.cardinalmachinery.com
VA, NC, SC, GA
David Chesnutt
Methods Machine Tools, Inc.
13607 South Point Boulevard
Charlotte, NC 28273
704-587-0507
dchesnutt@methodsmachine.com
www.methodsmachine.com
Northeast
NY (All Except NYC & Long Island)
Gordon Britton
Britton Machinery Sales, Inc.
330 Castlebar Rd.
Rochester, NY 14610
585-721-4160
gbritton@brittonmachinery.com
W. PA
Mark Henne
Marcus Machinery
106 Bellefield Court
Gibsonia, PA 15044
412-862-0803
mark.henne@marcusmachinery.com
www.marcusmachinery.com
WV
Chip Storie
Ellison Technologies
5333 Muhlhauser Rd.
Hamilton, OH 45011
513-874-2736
cstorie@ellisontechnologies.com
www.ellisontechnologies.com
DE, MD, NJ, E. PA, NY (NYC & Long Island)
Chris Cowan
Tuckahoe Trading
94 N. Hamilton St.
Doylestown, PA 18901
215-345-9275
chris@tuckahoetrading.com
www.tuckahoetrading.com
Midwest
MN, ND, SD, N. IA, W. WI
Dan Hales
Hales Machine Tool Inc.
2730 Niagara Lane North
Plymouth, MN 55447
763-553-1711
dhales@halesmachinetool.com
www.halesmachinetool.com
E. WI
Bob Stoltz
Merwin Stoltz Machine LLC
N30 W28979 Lakeside Road
Pewaukee, WI 53072
800-923-6255
merwinstoltzmachinellc@gmail.com
MO
David Smith
CJ Smith Machinery Company
2275 Cassens Dr., Suite 123
Fenton, MO 63026
636-349-7757
dsmith@cjsmith-machinery.com
www.cjsmith-machinery.com
IN, N. IL
Chris Tauber
Integrated Machinery Systems
101 North Prospect Ave.
Itasca, IL 60143
630-250-8305
chris.tauber@imscnc.com
www.imscnc.com
KY
John Stephenson
Tri-S
3 North Shaw Lane
Fort Thomas, KY 41075
859-380-5909
trisjohn@fuse.com
KY, OH
Chip Storie
Ellison Technologies
5333 Muhlhauser Rd.
Hamilton, OH 45011
513-874-2736
cstorie@ellisontechnologies.com
www.ellisontechnologies.com
MI
Brad Contrucci
Tooling Systems Sales
1782 Apple Ridge Court
Rochester Hills, MI 48306
248-656-2035
bradc@tssgrinding.com
www.toolingsystemssales.com
West
AZ
Richard Adams
Adams Machinery
215 S. Rockford Dr., Suite 101
Tempe, AZ 85281
480-968-3711
dick@adamsmachineryaz.com
www.adamsmachineryaz.com
S. CA
Jay Davis
DMARK Corporation
10552 Humbolt St.
Los Alamitos, CA 90720
562-799-9010
jdavis@dmarkcorp.com
www.dmarkcorp.com
NV, N. CA
John Franchuk
Die Mold Machinery
300F Danville Boulevard #323
Alamo, CA 94507
925-831-0920
john@diemoldmachinery.com
www.diemoldmachinery.com
CO, E. WY
Mike Geoffroy
The Geoffroy Company, Inc.
5910 S. University Blvd, C-18 #211
Greenwood Village, CO 80121
303-756-3684
TGCIdenver@comcast.net
MT, UT, S. ID, W. WY
James Grisley
JM Grisley Machine Tools, Inc.
1485 South 300 West St.
Salt Lake City, UT 84115
801-486-7519
sales@jmgrisley.com
www.jmgrisley.com
OR, WA, N. ID
Gary Anderegg
Machine Toolworks, Inc.
14600 Interurban Avenue South
Tukwila, WA 98168
206-575-3390
ganderegg@machinetoolworks.com
www.machinetoolworks.com