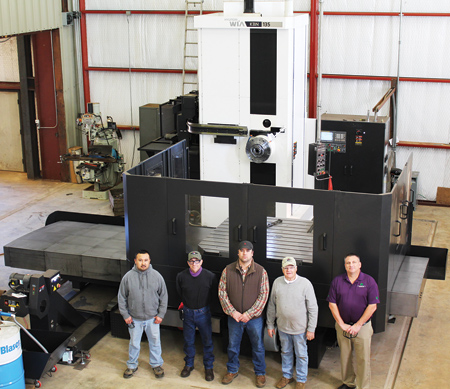
The Hyundai WIA KBN135 boring mill at West Craft Manufacturing. (l-r) Oscar Martinez, Programmer/Production Supervisor; Tony Bourbon, Machine Operator; Jake West, Vice President; Gerald West, President, CEO & Founder; and Chris Pannell, Account Manager, Hillary Machinery
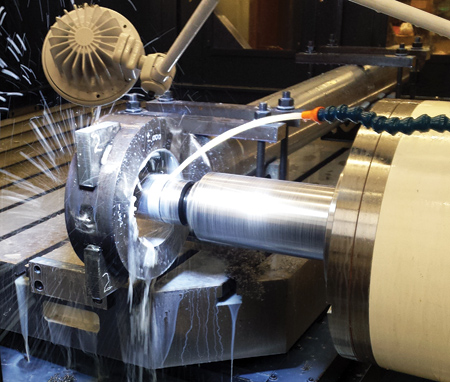
The Hyundai WIA KBN135 machining a long hydraulic cylinder rod
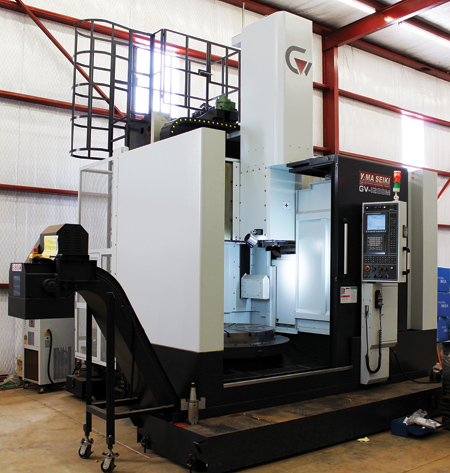
A Yama Seiki GV1200M vertical turning center allows West Craft Manufacturing to produce larger hydraulic cylinders.
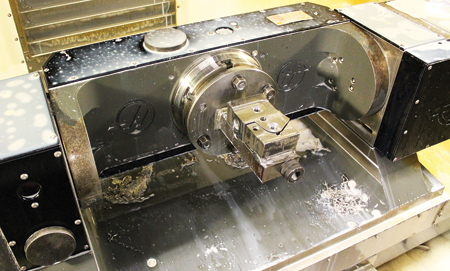
A 5-axis machining center at West Craft Manufacturing produces 9,000 multi-port manifold blocks annually.
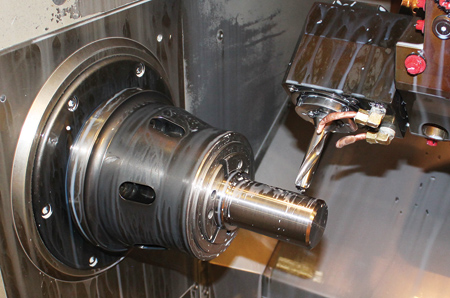
This multitasking machine at West Craft Manufacturing produces 21,500 cylinder rods annually.
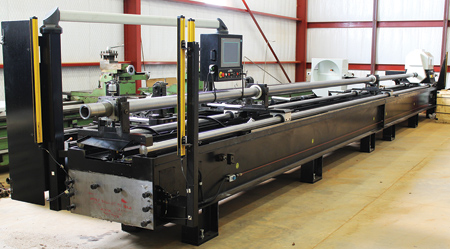
West Craft Manufacturing recently added a hone for 2"-26" diameter cylinders measuring up to 32' in length.
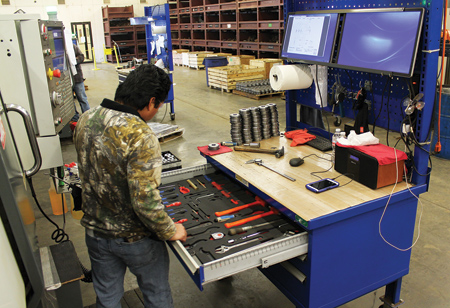
West Craft is currently in the process of standardizing its machining workstations.
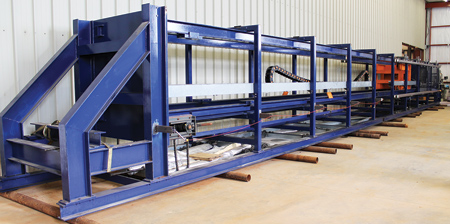
West Craft recently added a new test stand for testing cylinders up to 30" bore and 50' stroke.
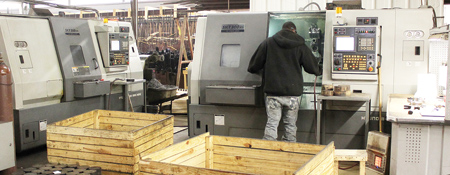
Two Hyundai WIA SKT300MS (now the L300MS) produce 42,000 pistons and glands annually.
In order to meet the growing demand for its hydraulic cylinders and support the needs of its existing large OEM customers, West Craft Manufacturing had to streamline its manufacturing process.
The process included location of raw materials, individual component machining, assembly and quality control testing. The goal was to increase throughput and shorten delivery time without increasing cost. Also, the plan was to add new production capacity to more efficiently supply larger hydraulic cylinders.
At West Craft raw material is stored inside the plant, in-line with the cut-off shop where material is loaded and fed into automatic saws, cut to length and then taken to their respective machining cells. The parts then move on to assembly and testing. The goal is to have each stage of the manufacturing process continuously feeding the next stage, creating the maximum amount of workflow, avoiding bottlenecks and using the least amount of labor.
West Craft considered a variety of solutions, including automatic cut-off saws, live tool sub-spindle machines, multitasking machines, 5-axis machines, a horizontal boring mill and a vertical turning center.
For the machining solution, West Craft selected two Hyundai WIA L300MS live tool sub-spindle turning centers, a Hyundai WIA KBN135 horizontal boring mill, a Yama Seiki GV1200M vertical turning center, a 5-axis machining center and a Y-axis turning center.
The Hyundai WIA L300MS live tool sub-spindle turning centers were selected to more efficiently produce the 21,000 5" threaded glands and 21,000 5" pistons needed annually to support West Craft's large OEM customers. According to Jake West, Vice President, what once took 20-25 minutes on four lathe operations, two mill operations and multiple machine operators, now only takes 8-10 minutes with just one machine operator. This eliminated the bottleneck and greatly increased throughput and efficiency.
To more efficiently supply the growing demand for its large hydraulic cylinders, West Craft also added a new Hyundai WIA KBN135 horizontal boring mill and a new Yama Seiki GV1200M vertical turning center. "Together, these two machines will enable us to produce larger hydraulic cylinders, up to 36 inch bores, in fewer set-ups, thus increasing throughput while decreasing cost and delivery time to our customers," said West.
A 5-axis machining center was also added to more efficiently machine roughly 9,000 multi-port valve blocks produced annually, another high volume part for its OEM customers. "What once took various milling machine set-ups and 15 minutes now only takes 8 minutes using one set-up on the 5-axis machine," said West.
Additionally, a Y-axis turning center was added to more efficiently process its annual production of 21,500 cylinder rods to support its large OEM customers. "What once took 5 minutes and two machine set-ups has been cut to 3 minutes on one machine set-up," said West.
West Craft Manufacturing provides complete end-to-end manufacturing of hydraulic cylinders including design, machining, fabrication and testing of standard and custom hydraulic cylinders from 1" to 36" in diameter and up to 100' of stroke.
The company recently added a new test stand for testing cylinders up to 30" bore and 50' stroke, and a new hone for 2" - 26" diameter cylinders up to 32' feet long.
The company is currently in the process of standardizing its machining workstations. This will allow the operators to see the image of the part they are producing on a PDF file that is directly connected to the production office. This allows more efficient scheduling of the next job for that machine and the operator can prepare the necessary tools for the upcoming job to reduce set-up times. The goal is to have a paperless facility to maintain efficiency and cleanliness.
West Craft Manufacturing was founded in 1969 by Gerald Harmon West and is family owned and operated. Gerald West started out operating and repairing heavy equipment in the logging industry in East Texas. The equipment had a lot of hydraulic cylinders on them. If they started leaking, they would lose power and eventually break down. Operators simply could not afford to wait for repairs, so Gerald would take the cylinders home and repair them himself. Soon, other machine operators would ask Gerald to fix their cylinders. Seeing the need for a more reliable cylinder, Gerald started manufacturing better hydraulic cylinders in his garage and later formed and incorporated West Craft Manufacturing.
According Gerald West's sons Jake and Josh, their father worked tirelessly seven days a week. They grew up in the company and today have taken on more significant roles. In 1997 the company purchased its first CNC machines, which allowed it to tap into higher volume production orders. They have since added several more CNCs, and every year have made improvements and investments in the company in order to better serve their customers.
West Craft Manufacturing is ISO 9001:2008 certified and serves a wide variety of industries, including oil and gas, construction, crane and hoist, dump truck/trailer, agriculture, forest/logging, steel production, refuse, lock and dam, aerial/utility, material handling, marine/ship building and hydraulic lift gates.
For more information contact:
West Craft Manufacturing
506 Palestine Street
Alto, TX 75925
936-858-4426
sales@westcraftmfg.com
www.westcraftmfg.net
Hyundai WIA Machine America Corp.
265 Spring Lake Dr.
Itasca, IL 60143
630-625-5538
hhansen@hyundai-wiamachine.com
www.hyundai-wiamachine.com
Yama Seiki USA, Inc.
5788 Schaefer Ave.
Chino, CA 91710
909-628-5568
info@yamaseiki.com
www.yamaseiki.com
SOUTHWEST ONLY
Troy Owen
Hillary Machinery Inc.
1825 Summit #207
Plano, TX 75074
800-683-1516
sales@hillaryinc.com
www.hillaryinc.com