
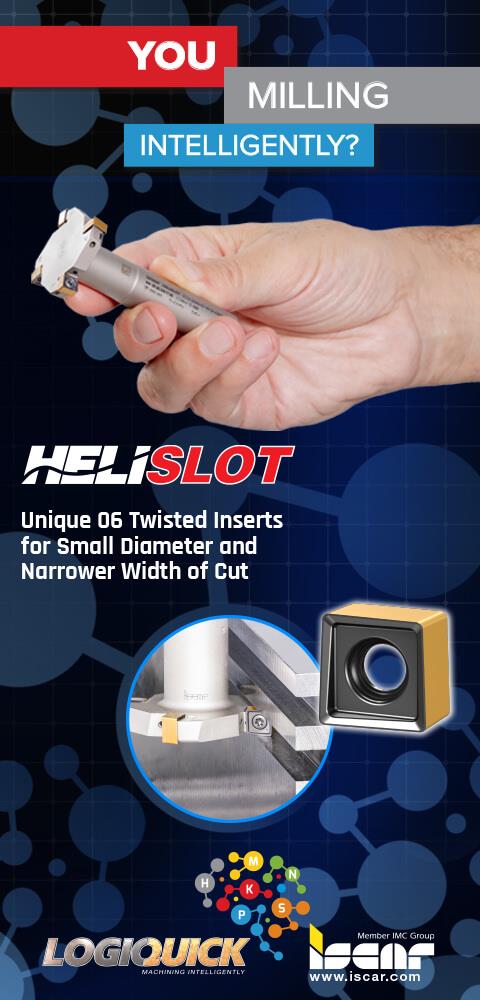
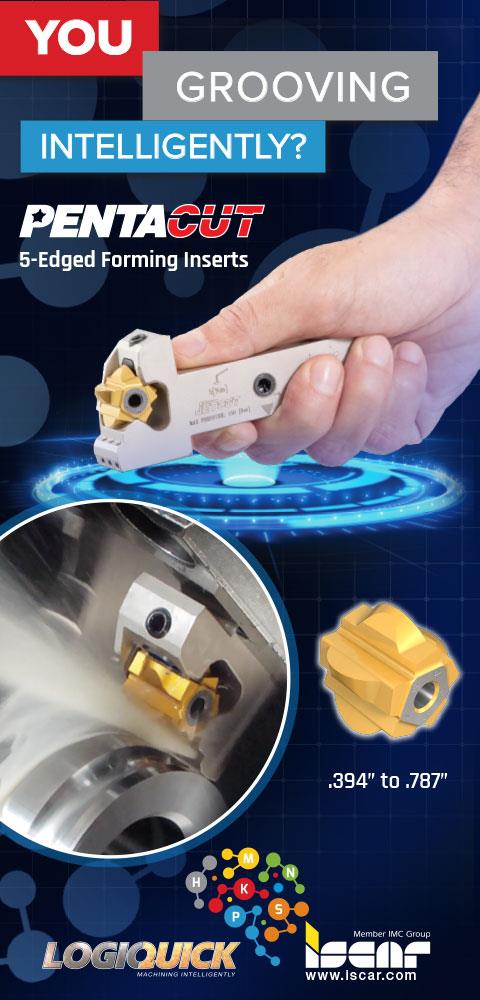
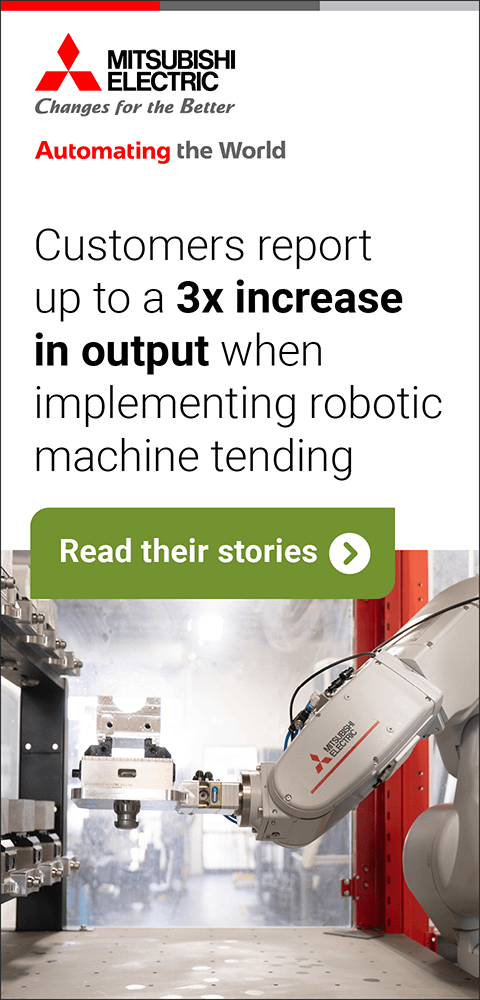
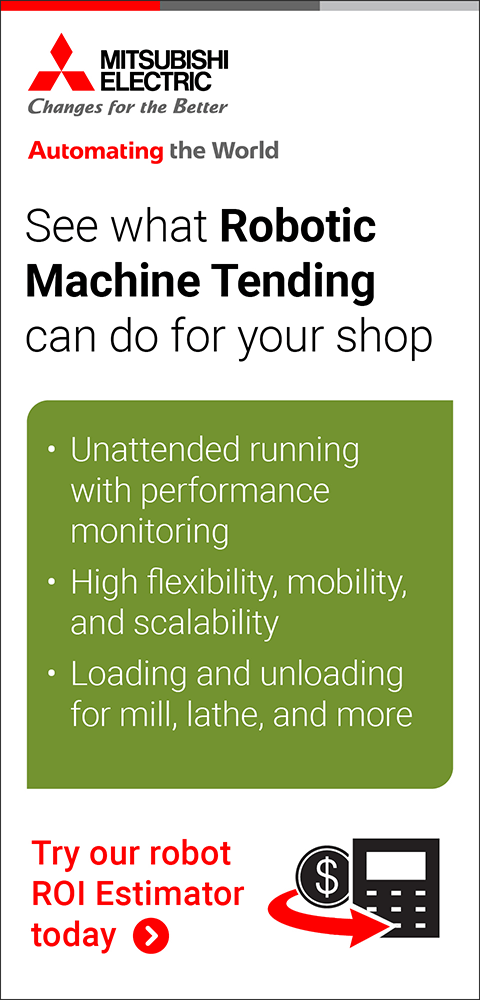
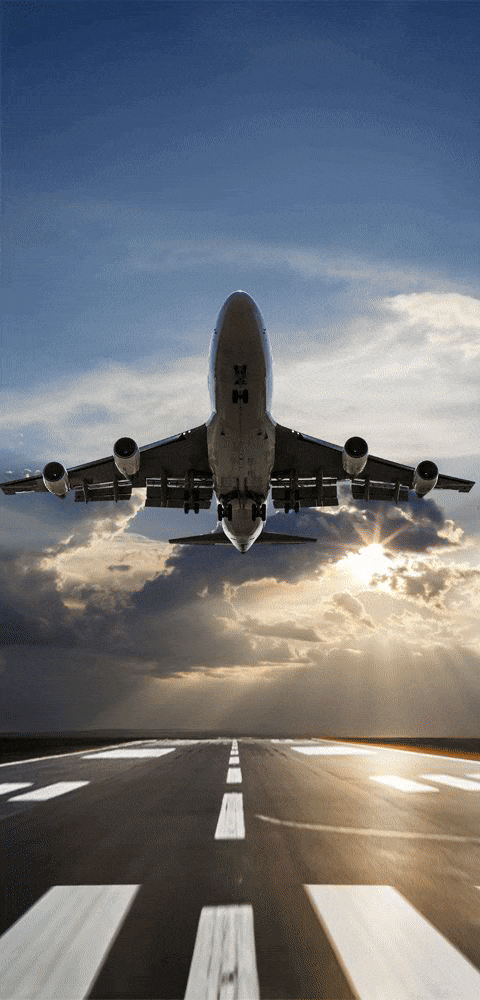
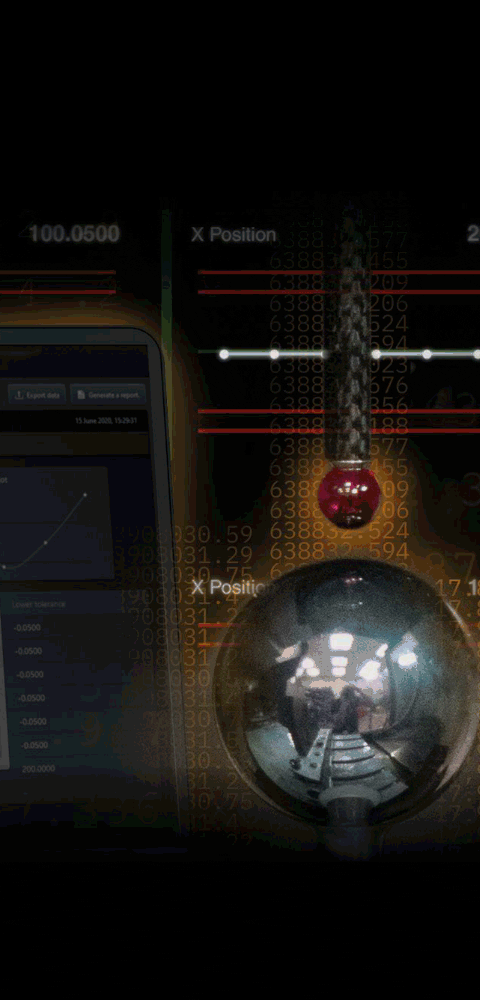
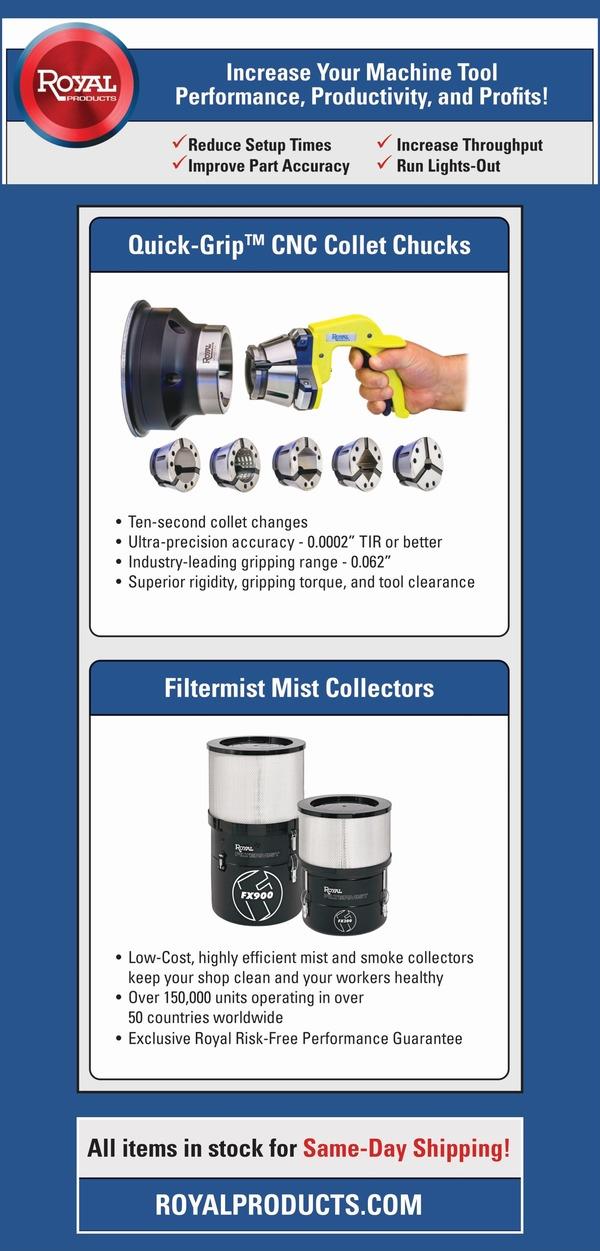
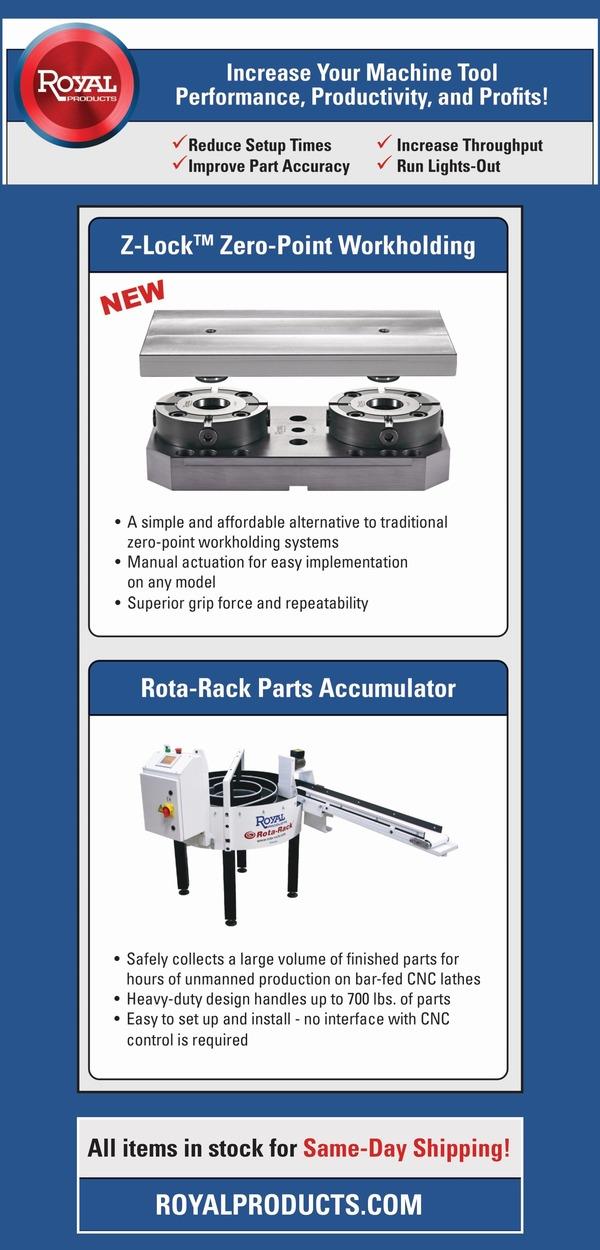

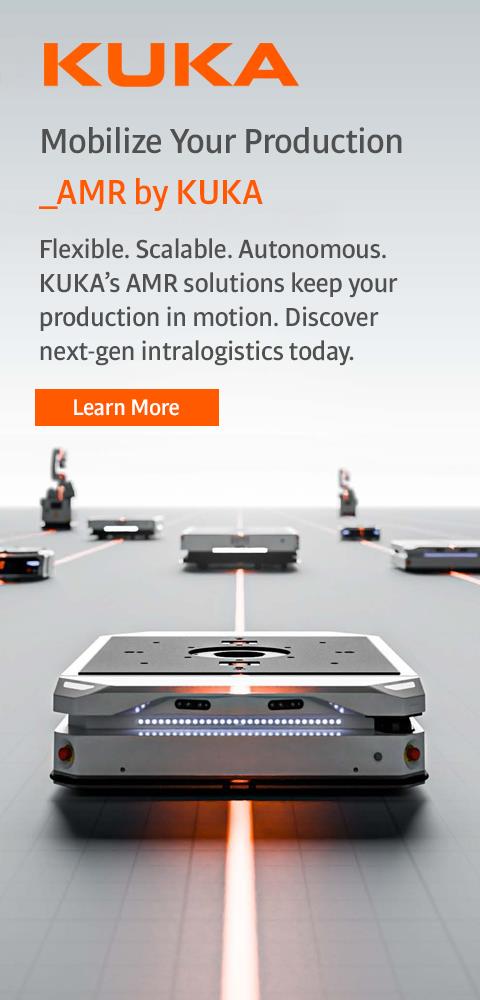
Latest Composite Applications Software
June 1, 2016
CGTech is now shipping the next major release of VERICUT Composite Applications: VERICUT Composite Programming (VCP), VERICUT Composite Simulation (VCS) and VERICUT Composite Paths for Engineering (VCPe). VERICUT Composite Applications are being used by manufacturers to program and simulate automated fiber placement machinery from machine tool builders such as Electroimpact, mTorres, Mag and others.
Simulation is critical when working with high-value aerospace components, especially those made with composites. "Because composite workpieces have a significant amount of process time and labor in them prior to machining, they can be more expensive than even some exotic metal alloy workpieces," said Product Marketing Manager Matt Radebach. "It's usually not possible to repair a composite workpiece damaged during machining. Thus, validation of the part program is extremely critical."
VCPe gives the user the ability to measure and evaluate the effects of AFP and ATL path trajectory, material steering, surface curvature, course convergence and other process constraints as they would be applied in manufacturing. The software also provides produceability analysis of the fiber angle based on the curvature of the part, and overlap and gaps needed for structural analysis. Tape course geometry can be written to various CAD formats for further evaluation by the user's existing analysis methods and tools.
VCP reads CATIA V5, STEP or ACIS surface models. It also reads Fibersim, CATIA V5 or other external ply geometry and information. VCP then adds material to fill the plies according to user-specified manufacturing standards and requirements. Layup paths are linked together to form specific layup sequences and are output as NC programs for the automated layup machine.
VCS reads CAD models and NC programs, either from VCP or other composite layup path-generation applications, and simulates the sequence of NC programs on a virtual machine. Material is applied to the layup form via NC program instructions in a virtual CNC simulation environment. The simulated material applied to the form can be measured and inspected to ensure the NC program follows manufacturing standards and requirements. A report showing simulation results and statistical information can be automatically created.
For more information contact:
CGTech
9000 Research Dr.
Irvine, CA 92618-4214
949-753-1050
info@cgtech.com
www.cgtech.com
< back