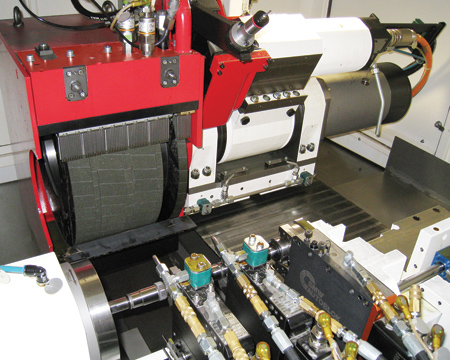
ShaftGrind with Multiwheel Transmission Shaft Technology
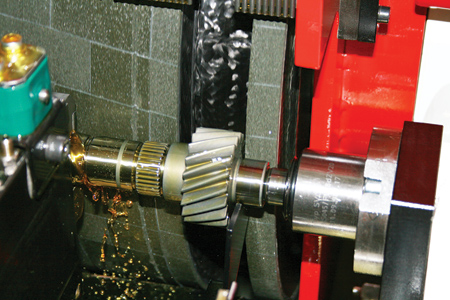
Highly productive grinding of gearshafts in one single plunge
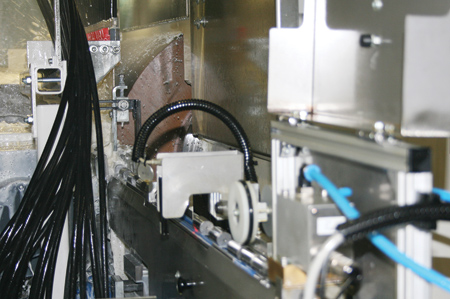
Throughfeed grinding of planetary gear pins on a KRONOS L
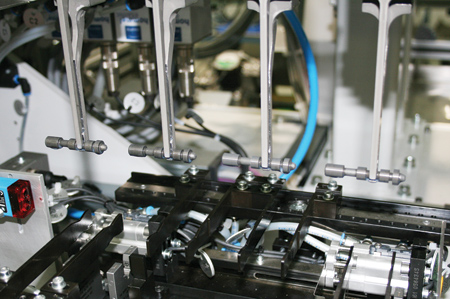
Multiple production for high productivity
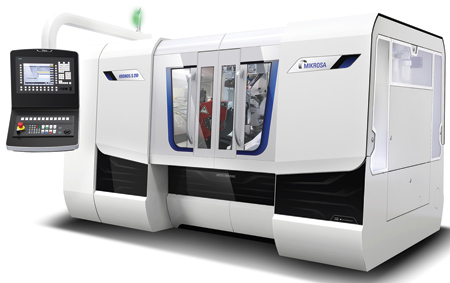
Centerless cylindrical grinding machine KRONOS S 250
As part of its recent Motion Meeting 2016 in Thun, Switzerland, United Grinding presented its latest technologies for automotive transmission applications. A transmission is essential for all cars with a combustion engine. The gear converter is connected directly downstream of the engine and converts speeds and torques along the power train. "The aim is to make the engine as efficient as possible, with the highest possible driving dynamics," said a company spokesperson. "Whether manual transmission, automatic transmission or dual clutch transmission - all contain countless precision parts that can be machined on machines from Schaudt Mikrosa GmbH."
SCHAUDT MIKROSA offers efficient machining solutions for many applications in the field of transmissions. The SCHAUDT ShaftGrind series, which is based on the camshaft grinding platform CamGrind, is designed for grinding input, output or intermediate shafts. For centerless grinding applications, all machine sizes in MIKROSA's KRONOS series are used. They can machine precision workpieces such as control spools for control units, planetary gear pins, shifter rods or needles for needle bearings with efficiency.
Grinding of Gear Shafts
"The conventional machining process for a gear shaft is difficult to standardize. Flexible solutions and new approaches are needed here," said the spokesperson. Different qualities of the bearing positions along a workpiece, divergent references for bearing positions and centers as well as the machining of bearing, keyway and spline diameters and shoulder surfaces place high demands on both machine and grinding process.
"SCHAUDT meets these challenges with the ShaftGrind series, which offers an individual combination of suitable machining and machine concepts for a variety of grinding tasks," said the spokesperson. From concepts with one grinding wheel to flexible solutions with up to four grinding wheels, various machine configurations are possible. "The result are efficient and relatively cost-effective solutions for transmission manufacturers," said the spokesperson.
The ShaftGrind S can be equipped with two grinding spindles, for example. The shaft diameters are ground with a ceramic-bound CBN grinding wheel on the main spindle, while the swivel-in spindle for machining the shoulders has a galvanic-bound CBN grinding wheel set. Due to integrated first contact detection the cycle time can be significantly reduced, as the machine detects fluctuations in the rough part stock allowance and only switches from rapid feed to grinding feed in the case of contact.
"Gear shafts can be machined even more effectively on the ShaftGrind L2," said the spokesperson. This machine is equipped with two cross slide systems with up to four grinding spindles (two main spindles and two swivel-in spindles), which can operate simultaneously. "This allows the grinding time for diameter machining to be almost halved," said the spokesperson. In-process measuring heads monitor the diameter dimensions to help ensure production reliability. Swivel-in spindles with galvanic-bound CBN grinding wheel sets are used for machining the keyways. "The machine can achieve a productive cycle time, together with high process reliability," said the spokesperson.
Multiwheel Transmission Shaft Technology
The Multiwheel Transmission Shaft Technology has been developed specifically for highly productive gear shaft applications. It allows synchronous machining of all bearing positions and spline diameters in a single plunge. A grinding tool with several wheels has been developed, which isolates spline machining from diameter machining in terms of vibrations. Machining times of just 15 seconds can be achieved. If plane surfaces and flat shoulders are also machined, the machines' wheelhead can be extended by a swivel-in spindle in accordance with the performance criteria. The concept is designed for maximizing productivity in gear shaft machining.
However, centerless machining can also be used for gear shafts. On machines of the KRONOS series all seats are ground in a single plunge, including machining of the spline gear. "In this case too, it is difficult to prevent the transmission of rounding errors from the gear to the diameters. A great deal of experience is needed for the configuration and setup of the grinding process," said the spokesperson. An advantage of centerless grinding is that the workpiece is supported along its lateral surface on the workpiece rest and on the regulating wheel, so that any deflection of the shaft can be prevented. This enables enhanced quality as well as a short grinding time.
Centerless Machining for Precision Parts
"In addition to the various gear shafts there are many other precision workpieces in the transmission that are ideal for centerless machining," said the spokesperson. Planetary gear pins, which are found in large quantities and different sizes in every automatic transmission, and needles for needle bearings are suited for through grinding, for example. Needles with an allowance of 0.1 mm, a workpiece diameter of 5 and a length of 16 mm, can be ground on a KRONOS M 400 at a speed of up to 16 m per minute. This gives roughly 1,000 finished parts per minute. Dressing occurs continuously and in parallel with the grinding process. So while machining is underway on the front side of the grinding wheel, the rear side is dressed simultaneously. "In addition to high productivity, these workpieces also have extreme demands on surface quality. Impressive values of Rz 0.4 and 0.5 microns are achieved when machining planetary gear pins - and that is with grinding," said the spokesperson.
Other workpieces are ground using the plunging method in single or multiple production. Control spools, found in great variety in the control units of automatic and dual clutch transmissions, can be machined efficiently on a KRONOS S 250 in fourfold production, for example. Shifter rods for manual transmissions are ground on a KRONOS L 660 in double production. "This allows for a reduction of cycle times and a decrease of unit costs, despite higher investment costs. The machines are part of a complete machining line," said the spokesperson. The parts are fed into the machine via a handling system, machined and finally measured and palletized.
For more information contact:
UNITED GRINDING North America, Inc.
510 Earl Blvd.
Miamisburg, OH 45342
937-859-1975
info@grinding.com
www.grinding.com
Southwest
E. TX
Charles Harter
CJ Harter & Son Machinery Inc.
550 Westcott, Suite 375
Houston, TX 77007
713-227-7221
harterhou@sbcglobal.nex
AR, LA
Steve Wherry
Cardinal Machinery
7535 Appling Center Dr.
Memphis, TN 38133
901-377-3107
s.wherry@cardinalmachinery.com
www.cardinalmachinery.com
NM
Mike Geoffroy
The Geoffroy Company, Inc.
5910 S. University Blvd, C-18 #211
Greenwood Village, CO 80121
303-756-3684
TGCIdenver@comcast.net
Southeast
AL, MS, TN, FL (Panhandle)
Steve Wherry
Cardinal Machinery
7535 Appling Center Dr.
Memphis, TN 38133
901-377-3107
s.wherry@cardinalmachinery.com
www.cardinalmachinery.com
VA, NC, SC, GA
David Chesnutt
Methods Machine Tools, Inc.
13607 South Point Boulevard
Charlotte, NC 28273
704-587-0507
dchesnutt@methodsmachine.com
www.methodsmachine.com
Northeast
NY (All Except NYC & Long Island)
Gordon Britton
Britton Machinery Sales, Inc.
330 Castlebar Rd.
Rochester, NY 14610
585-721-4160
gbritton@brittonmachinery.com
W. PA
Mark Henne
Marcus Machinery
106 Bellefield Court
Gibsonia, PA 15044
412-862-0803
mark.henne@marcusmachinery.com
www.marcusmachinery.com
WV
Chip Storie
Ellison Technologies
5333 Muhlhauser Rd.
Hamilton, OH 45011
513-874-2736
cstorie@ellisontechnologies.com
www.ellisontechnologies.com
DE, MD, NJ, E. PA, NY (NYC & Long Island)
Chris Cowan
Tuckahoe Trading
94 N. Hamilton St.
Doylestown, PA 18901
215-345-9275
chris@tuckahoetrading.com
www.tuckahoetrading.com
Midwest
MN, ND, SD, N. IA, W. WI
Dan Hales
Hales Machine Tool Inc.
2730 Niagara Lane North
Plymouth, MN 55447
763-553-1711
dhales@halesmachinetool.com
www.halesmachinetool.com
E. WI
Bob Stoltz
Merwin Stoltz Machine LLC
N30 W28979 Lakeside Road
Pewaukee, WI 53072
800-923-6255
merwinstoltzmachinellc@gmail.com
MO
David Smith
CJ Smith Machinery Company
2275 Cassens Dr., Suite 123
Fenton, MO 63026
636-349-7757
dsmith@cjsmith-machinery.com
www.cjsmith-machinery.com
IN, N. IL
Chris Tauber
Integrated Machinery Systems
101 North Prospect Ave.
Itasca, IL 60143
630-250-8305
chris.tauber@imscnc.com
www.imscnc.com
KY
John Stephenson
Tri-S
3 North Shaw Lane
Fort Thomas, KY 41075
859-380-5909
trisjohn@fuse.com
KY, OH
Chip Storie
Ellison Technologies
5333 Muhlhauser Rd.
Hamilton, OH 45011
513-874-2736
cstorie@ellisontechnologies.com
www.ellisontechnologies.com
MI
Brad Contrucci
Tooling Systems Sales
1782 Apple Ridge Court
Rochester Hills, MI 48306
248-656-2035
bradc@tssgrinding.com
www.toolingsystemssales.com
West
AZ
Richard Adams
Adams Machinery
215 S. Rockford Dr., Suite 101
Tempe, AZ 85281
480-968-3711
dick@adamsmachineryaz.com
www.adamsmachineryaz.com
S. CA
Jay Davis
DMARK Corporation
10552 Humbolt St.
Los Alamitos, CA 90720
562-799-9010
jdavis@dmarkcorp.com
www.dmarkcorp.com
NV, N. CA
John Franchuk
Die Mold Machinery
300F Danville Boulevard #323
Alamo, CA 94507
925-831-0920
john@diemoldmachinery.com
www.diemoldmachinery.com
CO, E. WY
Mike Geoffroy
The Geoffroy Company, Inc.
5910 S. University Blvd, C-18 #211
Greenwood Village, CO 80121
303-756-3684
TGCIdenver@comcast.net
MT, UT, S. ID, W. WY
James Grisley
JM Grisley Machine Tools, Inc.
1485 South 300 West St.
Salt Lake City, UT 84115
801-486-7519
sales@jmgrisley.com
www.jmgrisley.com
OR, WA, N. ID
Gary Anderegg
Machine Toolworks, Inc.
14600 Interurban Avenue South
Tukwila, WA 98168
206-575-3390
ganderegg@machinetoolworks.com
www.machinetoolworks.com