
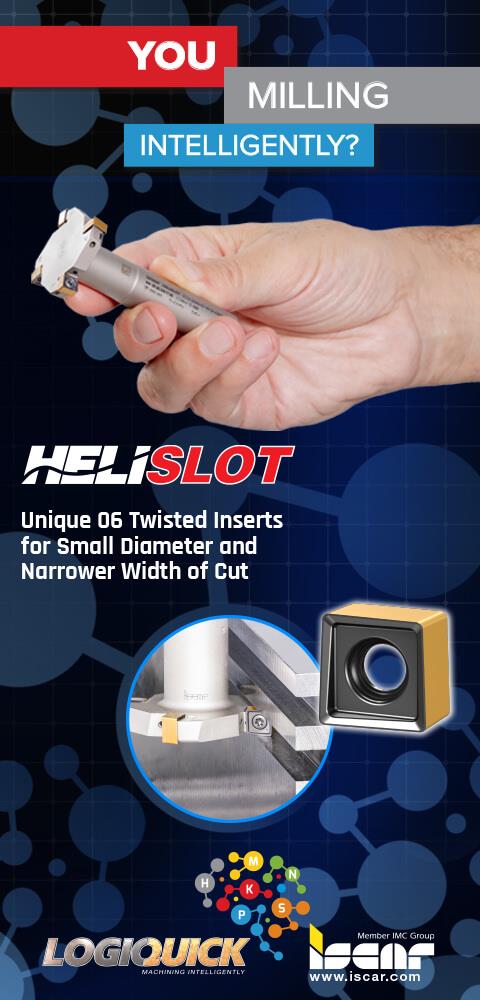
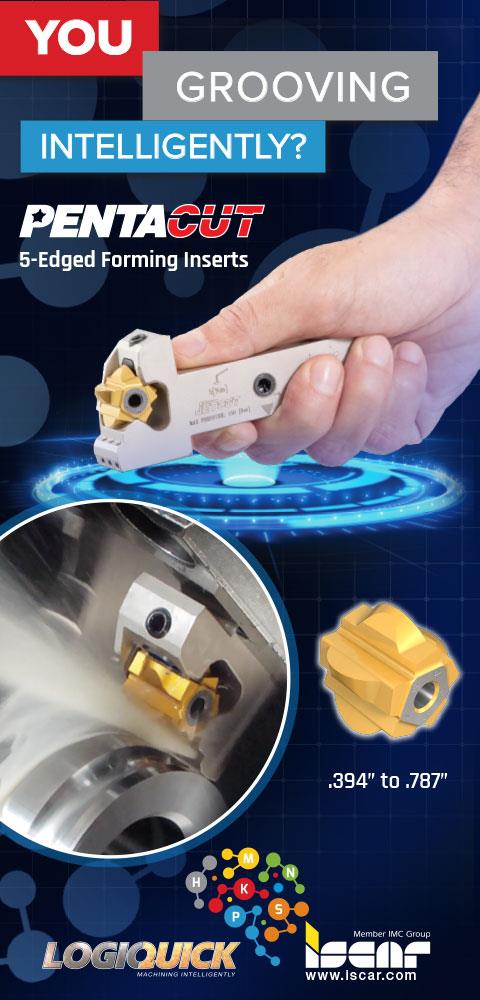
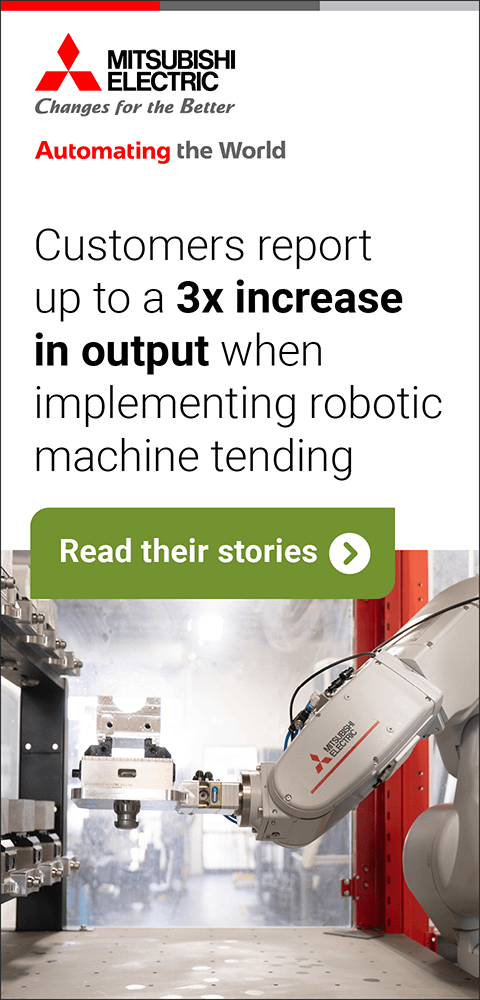
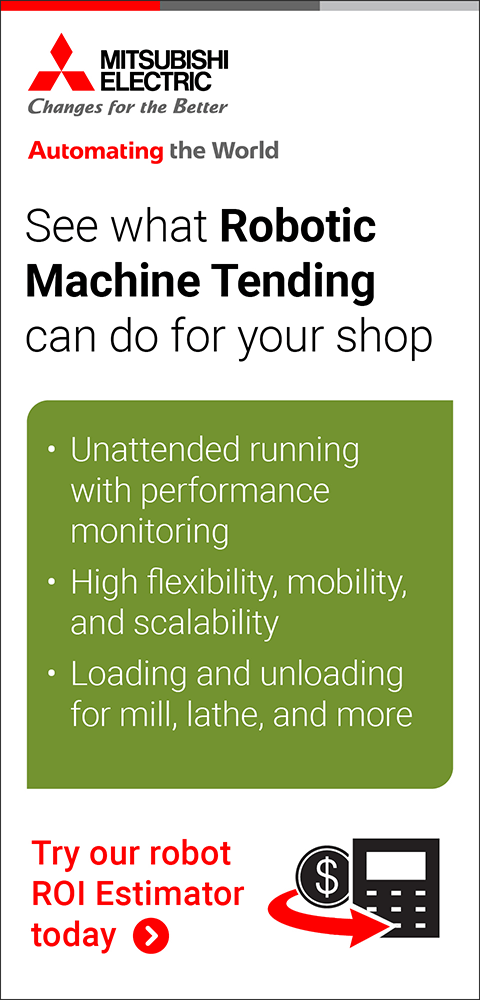
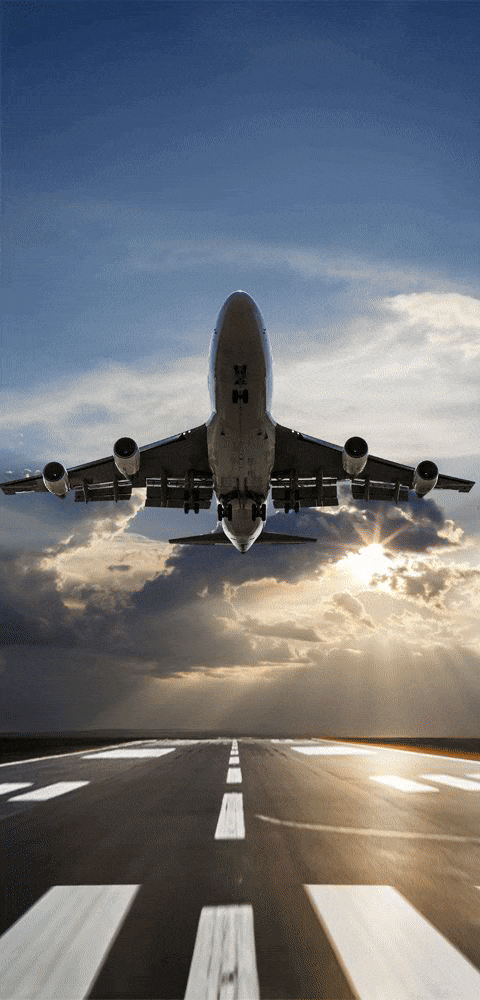
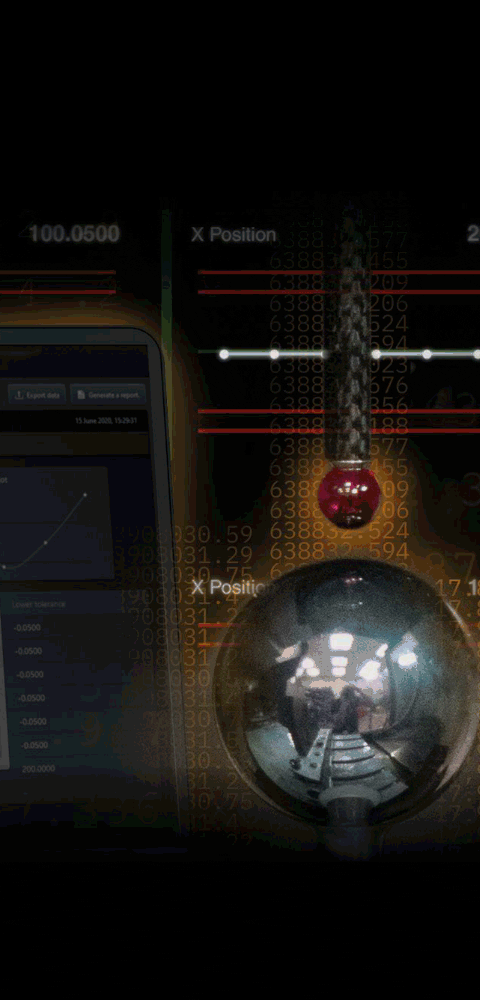
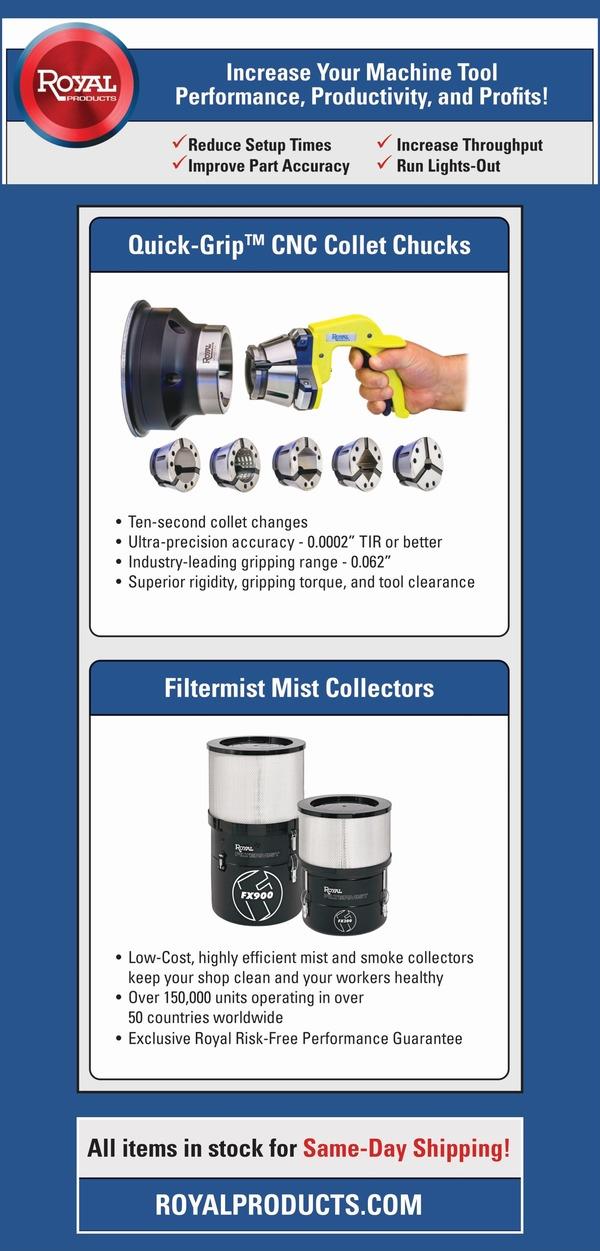
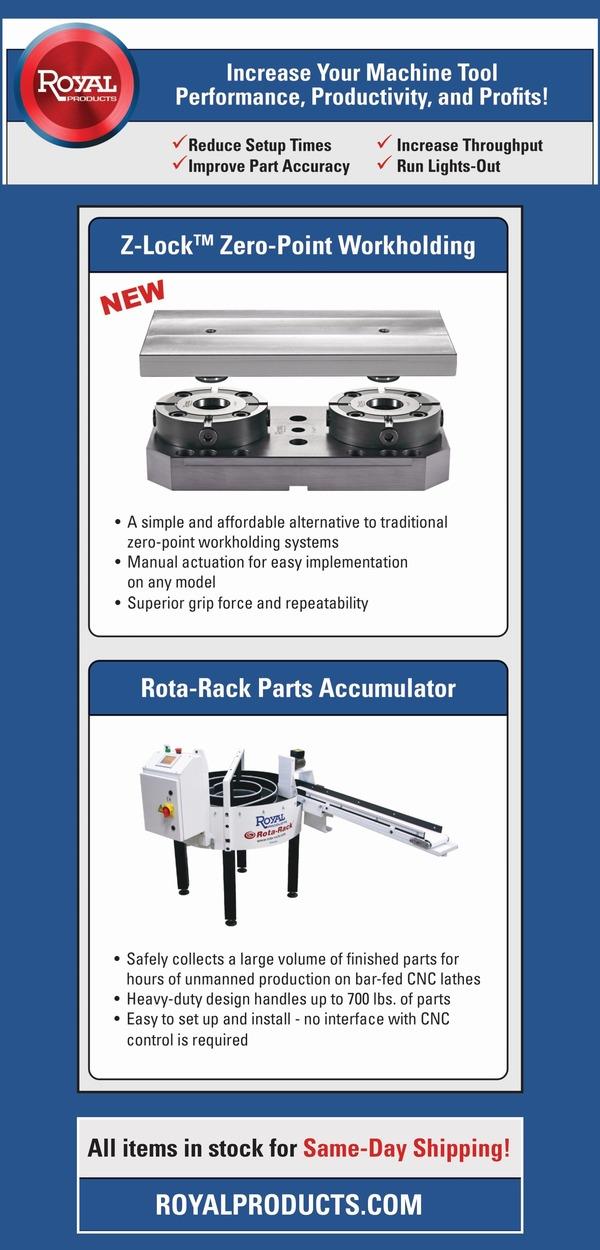

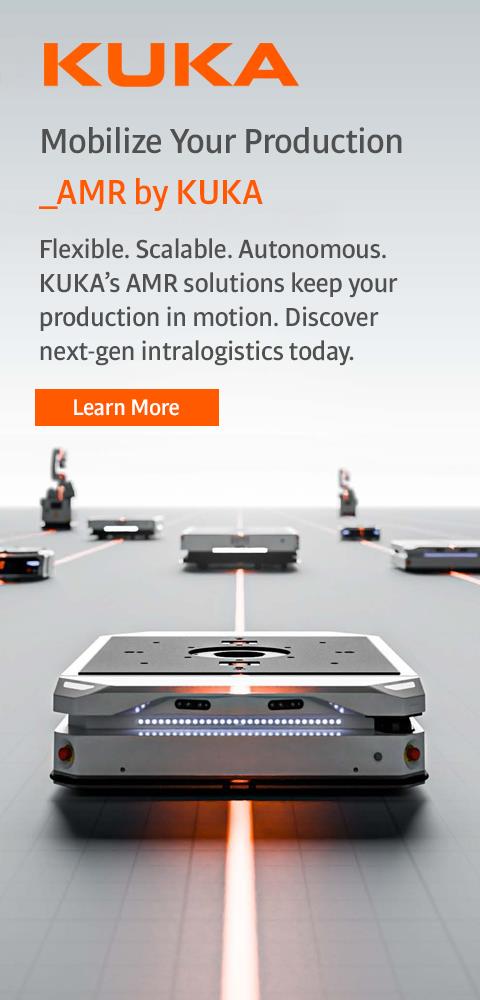
Ball Nose Milling Cutters
May 1, 2016
"For the production of homokinetic joints of hardened steel, numerous automotive manufacturers and suppliers rely on ball nose milling cutters from the MAPAL CPMill program," said a company spokesperson. "For years, these have been successfully used for pre-machining (soft milling) and finishing (hard milling with PCBN). They are subject to continuous improvement. A new, comprehensive development of the milling cutter for pre-machining now allows users to increase efficiency."
The spiraled geometry helps ensure optimal chip removal. Instead of four cutting edges, the solid carbide ball nose milling cutter has five. Furthermore, in addition to the base substrate, the coating has also been improved. For easy changing of the milling heads, they are equipped with the CFS interface. "Through the precise tuning of the taper and face, a concentricity of ≤ 5 µm, rigidity and consistently high quality are achieved," said the spokesperson.
With the CPMill ball nose milling cutter, machining time per component can be reduced. "While 75,000 parts were previously machined in one week, for example, there is around 12% more produced (namely, 85,000 components) with the five-edged cutter using the same machine capacity and without any additional investment in equipment. The reason is that it is possible to work with much higher cutting and feedrates. In addition, the milling cutter has a 25% higher service life than the previous model," said the spokesperson.
The solid carbide CPMill ball nose milling cutters are available in various diameters.
For more information contact:
MAPAL Inc.
4032 Dove Road
Port Huron, MI 48060
810-364-8020
info@us.mapal.com
www.mapal.com
< back