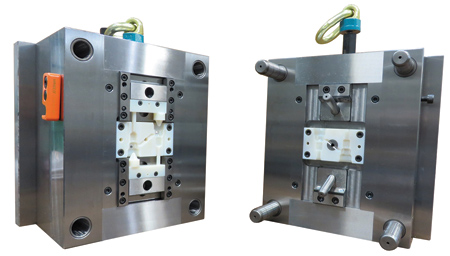
Hasco 3-D prints injection mold inserts with Stratasys PolyJet technology in a matter of hours and can make design iterations at a fraction of the time and cost of traditional tooling methods
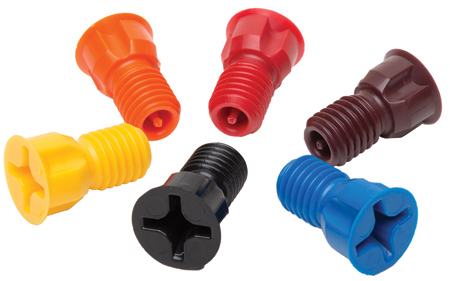
Hasco sealing plugs produced in POM (Polyoxymethylene) using Stratasys 3-D printed injection molds
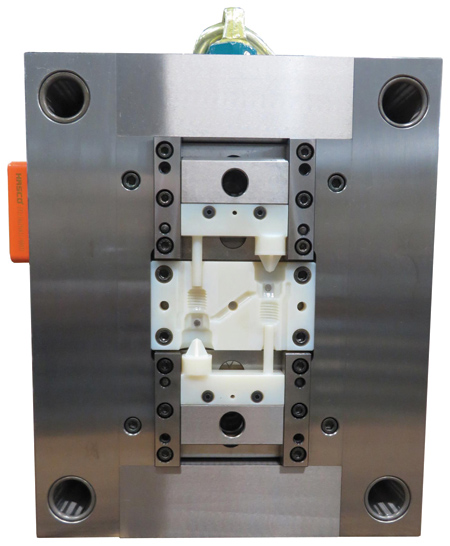
Close up of Hasco injection mold insert produced on a Stratasys Objet500 Connex 3-D Production System, mounted on the K3500 quick-change mold system
Stratasys Ltd. has announced that worldwide moldmaker, HASCO, has developed a rapid, cost-efficient method to produce low volumes of injection molded prototypes by integrating Stratasys 3-D printing with its K3500 quick-change mold system. "Utilizing this approach, molders can change between inserts for different products, enabling them to cost-effectively produce low volumes of injection molded parts for samples, prototypes and small production runs," said a company spokesperson.
HASCO 3-D printed the inserts in Stratasys' Digital ABS material using the Objet500 Connex Multi-material 3-D Production System. "With a 3-D printed mold insert taking only hours to produce, molders can make design modifications to the product for a fraction of the time and cost of conventional tooling methods," said the spokesperson.
"With time-to-market cycles shorter than ever and production quantities dropping, our customers are now looking for solutions that enable them to deliver prototypes quickly and cost-effectively," said Dirk Paulmann, Executive Vice President, Sales and Business Development at HASCO. "Compared with conventional metal or aluminum inserts, our new approach offers molders the flexibility to quickly produce and switch inserts, making them much more productive and profitable. Combining our expertise in moldmaking with Stratasys' pioneering expertise in 3-D printing injection molds, this technique is the future of prototype and low volume production."
When producing a sealing plug for its industry-standard A8001 clamping fixture, HASCO identified that the walls of the ABS plastic sealing screw would need to be 12 mm thick to seal the large number of threaded holes. Given this geometry, it was clear that that the screw could not be produced using the conventional injection molding process. With the level of intricacy enabled by Stratasys PolyJet 3-D printing, HASCO redesigned the screw with a reduced wall thickness and subsequently 3-D printed a mold insert to the new specifications in order to test the integrity of the design before mass production.
"The speed of the process was incredible," said Paulmann. "Using our Objet500 Connex 3-D Production System, we produced the parts of the cavity that shape the polymer - such as the inserts and slides - in just six hours compared to the 24 hours it previously took. We then worked with prototyping specialists Canto Ing. GmbH, Lüdenscheid to finish the 3-D printed inserts and test the sample mold. We were delighted with the result; the first sealing screws were produced ready for mounting on our clamping unit in a record time of only four days.
"Through the use of tried-and-tested standardized HASCO products and Stratasys state-of-the-art 3-D printing, the project has proved that it is possible to implement this rapid-technology application within the injection molding process. For the production of low-volume prototypes in the final product material, the ability to quickly change molds with a 3-D printed cavity offers a rapid, low-cost alternative to conventional methods."
For more information contact:
HASCO America Inc.
270 Rutledge Road, Unit B
Fletcher, NC 28732
828-650-2600
quotes.america@hasco.com
www.hasco.com
Stratasys Ltd.
7665 Commerce Way
Eden Prairie, MN 55344
877-489-9449 / 952-937-3000
info@stratasys.com
www.stratasys.com