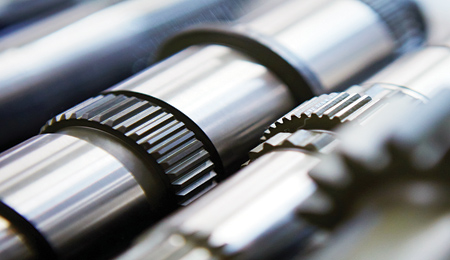
Machine utilization strategies and other factors have prompted Long's to precision grind many shafts that it formerly hard turned.
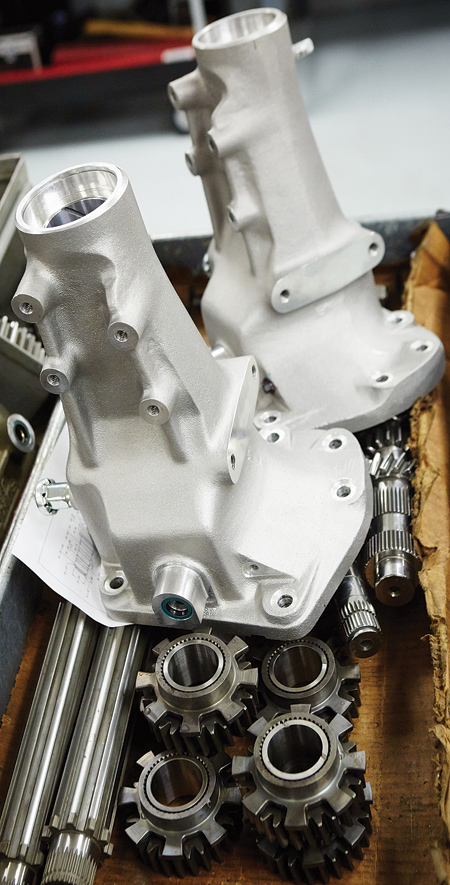
Long's Machine manufactures and services high performance transmission components ranging from gear kits for Friday night street racers to transmissions and rear end assemblies for NASCAR.
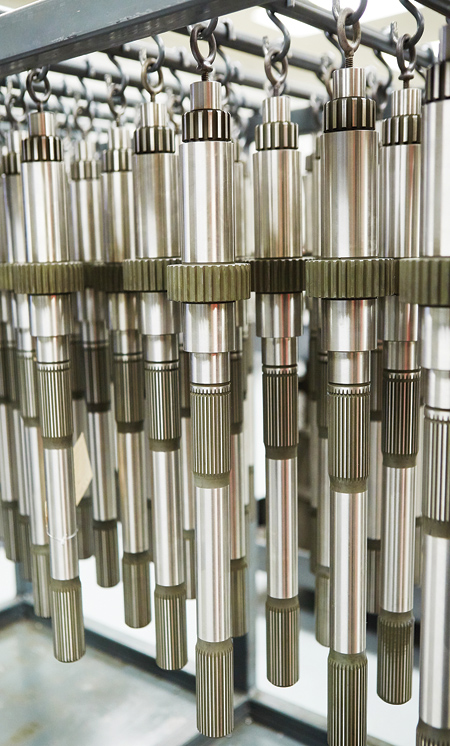
Long's hangs its ground transmission shafts, including these for NASCAR, to maintain their high precision and straightness.
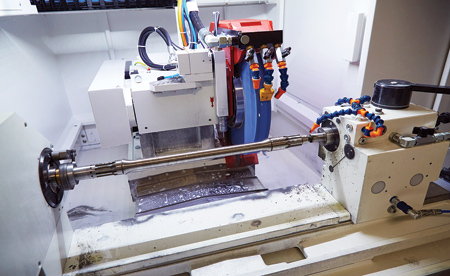
Long's performs O.D. shaft grinding on its STUDER S33s, and the combination of the machines' fast and precise grinding capabilities paired with the shop's manufacturing experience have resulted in much shorter cycle times.
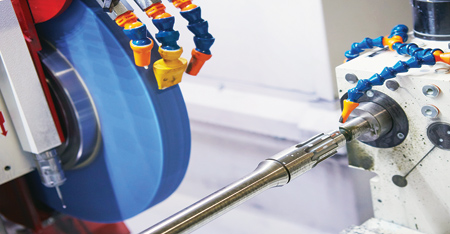
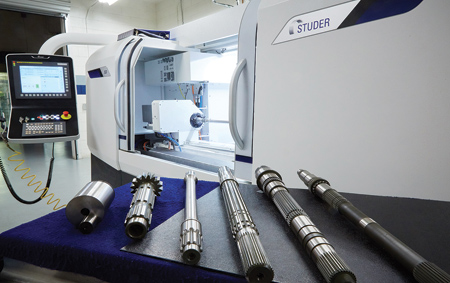
Long's Machine O.D. grinds transmission input shafts, main shafts and lower shafts with the STUDER machines, which can handle part lengths up to 25".
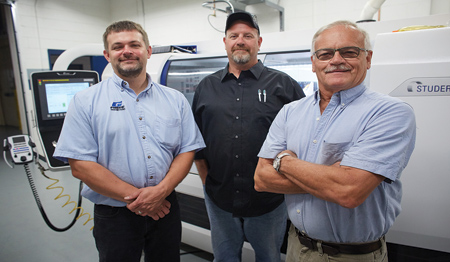
Long's Machine & Tool Inc. President Leonard Long (right), Vice President and Leonard's son Mike Long (left) and Production Manager Paul Dougherty (center) stand in front of the shop's latest advanced grinding machine - a STUDER S33 from United Grinding.
During 35 years of operation, Long's Machine & Tool, Inc. in Cleona, PA, has adapted to major shifts in its markets to become a leading supplier of auto racing transmissions and components for NASCAR and other race series. The adaptation involved changing production strategies and equipment to compensate for shrinking demand for some products while meeting growing orders for others. The strategies included increased use of precision grinding instead of hard turning operations and the application of just-in-time machining methods.
Leonard Long designed and patented a five-speed racing shifter in 1976 and in 1979 founded Long's Machine to produce it. To ensure a steady stream of revenue, the shop also provided contract machining of aerospace electronic connector housings and other products. Shifter manufacturing opened the door to making other transmission components, and the shop's capabilities expanded to include turning, milling, EDM and grinding of gears, shafts and cases. Today, the company outsources only casting and heat treating and has more than 30 CNC lathes and mills as well as grinding, broaching, EDM and gear cutting machines. In addition to its own product lines, the shop provides a variety of custom and contract machining services as well.
Dramatic market changes in the mid-2000s preceded the shop's present stability. The electronics industry then transitioned from large multi-pin connectors to USB and micro connectors along with wireless systems.
"Needless to say, orders for the connectors shrank," said Long. "And within five years, we went from being 80% industrial to 80% race car components. It was this expansion of automotive business that created a need to make parts for a wider variety of transmission types."
In the past, Long's Machine made only two kinds of transmissions, and that amount has since ballooned to 10. Back then, the shop could make and stock 100 to 150 of the same gears or shafts for one transmission type. Now, with servicing many more different transmission types, lot sizes of the same parts have shrunk to only 20 or 30 pieces.
Transmission component manufacturing at Long's Machine involves quite a bit of precision grinding. When job lot sizes were big, the shop used three manual grinders, and output was satisfactory. But as part variety grew and lot sizes decreased, the lengthy changeover times of the manual machines created huge production bottlenecks.
To boost flexibility as well as part changeover and processing speeds, Long's Machine, in 2006, acquired its first CNC grinder, a STUDER S33 Universal Cylindrical grinder through UNITED GRINDING North America. The shop experienced such remarkable success with the machine that it purchased another in 2015. The two STUDERS now enable the shop to carry out its new initiatives of doing less hard turning and more precision grinding for effective just-in-time production.
Mike Long, Vice President at Long's Machine and Leonard Long's son, said that the shop programs and runs all of its shafts on the STUDER machines regardless of shaft size or shape. But he strongly emphasized that the grinders' main benefits are their accuracy, speed and easy changeovers.
Long's Machine O.D. grinds transmission input shafts, main shafts and lower shafts with the STUDER machines, which can handle part lengths up to 25". The two machines have similar capabilities, although the newer one includes the StuderTechnologyIntegrated feature that automatically generates ISO grinding codes.
"In our manufacturing environment, we have to be able to change over quickly," said Long. "There is very little time to waste. We have to be able to load a part, touch it off and go. And once parts come off of the grinder, they go right into a transmission. The machines give us a competitive advantage in terms of product quality and short delivery times. Our customers might wait about two weeks for parts from us, but two or three months from another shop, and that is quite a dramatic time difference."
Long's Machine manufactures and services high performance transmission components ranging from gear kits for Friday night street racers to transmissions and rear end assemblies for NASCAR. Today, 10 to 12 top Sprint Cup teams as well as Xfinity Series and Camping World Truck teams use the company's products. A top team may stock 20 or 25 transmissions per car, using a few each race weekend then sending them out for service while rotating in the spares. "Our truck goes out Monday or Tuesday to deliver transmissions for the next week and picks up the ones to be serviced," said Mike Long.
Machine utilization strategies and other factors have prompted the shop to precision grind many shafts that it formerly hard turned. Mike Long recognized that hard turning shafts delivered to the shop after heat treating tied up lathes that could be utilized turning raw bar stock. "Anything that can be ground, we grind, because we have so much lathe work," he said.
Another reason for the switch from hard turning to grinding involves specific part requirements. A sealing segment of a shaft, for example, requires a surface that is ground, not turned. Hard turning a shaft and then moving it to a grinder to finish a sealing segment interrupts production flow.
The length to diameter ratio of some parts is also an issue. Hard turning a short shaft is easy, but hard turning a 20" to 25" long mainshaft is a whole other challenge. Also, slow feedrates can make some parts too time consuming to hard turn. And even though hard turning can generate required surface finish specifications, the appearances of those surfaces are oftentimes not as visually appealing as those of a precision ground surface.
The shop's single-wheel STUDER machines are set up for O.D. shaft grinding. So for the few cases where I.D. surface finishing is necessary, the shop uses hard turning operations on its CNC turning centers.
Control of overall processing time is a key element of productivity at Long's Machine. According to lead grinder Tom Kropp, typical grinding cycle times range from a minute or two up to 15 minutes, depending on part requirements.
"The combination of our manufacturing experience and STUDERS' fast and precise grinding capabilities have resulted in much shorter cycle times," commented Kropp. "Plus, we continue to work closely with UNITED GRINDING and have gained even more experience as well as the know how to, in some cases, push three times faster than what we did prior. A part that used to take half an hour, for instance, we now grind in 10 or 15 minutes. For us, that is huge."
In contract machining projects, workpiece materials range from steels and aluminums to nickel based alloy and titanium aerospace materials. Steel alloys are the primary workpiece materials for transmission components, with the majority of shafts made from 8620 or 4340 steel. The 4340 shafts normally are pre-heat treated, while the 8620 parts are case hardened. Typical mainshafts are 20" to 21" long and between 2" and 3" in diameter, with five to six different journals per shaft to be ground. The shafts are typically case hardened to 60 HRC, and volumes vary. But production of input shafts with three journals that require grinding, for example, averages about 40 or 50 a day with a maximum output of 80.
Today, about 85% of Long's Machine's output consists of automotive final drive components, comprising about 2,500 different part numbers. The rest is contract machining, and the shop's comprehensive capabilities enable it to handle nearly any job. "There are very few parts that we cannot make," said Mike Long. "If someone comes along with a crazy project, we can typically make it at a cost-effective price."
Long's Machine has several subsidiaries, including G-Force Transmissions and Long Shifters. G-Force South, in Asheboro, NC, functions as sales, service and assembly house for transmission components manufactured in Cleona and operates the largest leasing program for racing rear end gears and transmissions in North Carolina. Overall, Long's Machine employs about 50 people in Cleona and 25 in Asheboro.
In addition to the strong U.S. stock car transmission business, G-Force and Long Shifters sell drag racing and import (for Japanese and German cars) products around the world. Leonard Long himself is a top drag race competitor. In August 2015, he won the National Muscle Car Association championship in the carburetor or naturally aspirated (NA) 10.5 class driving his 408 cubic-inch small-block Ford Mustang and becoming the first stick shift transmission champion in more than a decade.
Leonard Long said the future for Long's Machine is bright, citing the expanding import racing market that includes building parts for popular Mazda racing motors. Mike Long pointed out the potential of programs such as production of powertrain components for hybrid buses.
He said, "Success is not just a matter of building a better mousetrap, it is being cost effective. And while we do not claim to be the least expensive, we do claim to be the best. And high-precision STUDER grinding technology helps us substantiate that claim."
For more information contact:
Long's Machine & Tool, Inc.
150 N. Grant Street
Cleona, PA 17402
717-202-8360
info@longsmachinetool.com
www.longsmachinetool.com
UNITED GRINDING North America, Inc.
510 Earl Blvd.
Miamisburg, OH 45342
937-859-1975
info@grinding.com
www.grinding.com