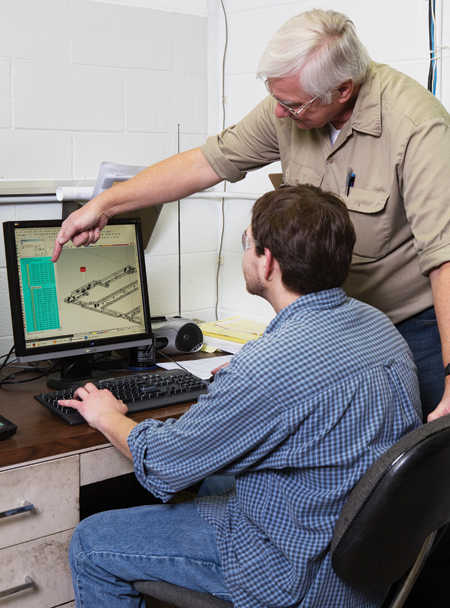
(standing) Fred Schubert and (seated) Wesley Shipman review a part program. At Acro Industries, Mastercam is used to write interchangeable programs for nine different CNC machines. This workflow gives the users maximum flexibility to create tools and fixtures that allow the fab shop to accommodate urgent production schedules that require frequent changeovers.
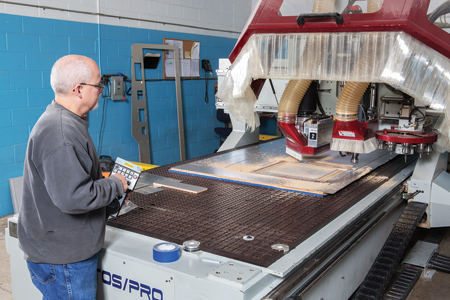
Increasing volumes of sheet metal are being cut in this 4-axis router cell, here operated by Mike Wing, at Acro Industries. Mastercam CAD/CAM software is invaluable not only for programming components for fast-turn, low-volume production runs, but also for creating workholding solutions that make it possible to machine lightweight formed laminates that consist of high-strength, low-alloy steel laminated to a cardboard backing.
Although only 8-10% of Acro Industries' manufacturing output is produced on CNC mills, lathes and wire EDMs, this equipment and the corporation's CAD/CAM system plays an important role in developing tools and fixtures that allow the company to meet tight product development schedules and cost-effectively manufacture a very diversified queue of high quality, short run fabrications every month.
Acro Industries has very close relationships with a small number of high-profile manufacturers in several industries: medical equipment, transportation (particularly rail cars), aerospace and alternative energy. As diverse as this customer base sounds, they have several things in common. They each require pristine, cosmetically clean enclosures and other fabrications. Manufacturing must be cost-effective even though monthly volumes are small. Deliveries must be made to the customers' manufacturing locations on a just-in-time basis.
The company operates two shifts five days a week, and employs numerous machinists who are all proficient users of the company's Mastercam CAD/CAM software (from CNC Software, Inc., Tolland, CT). Presently there are three seats of Mastercam Mill, and one each of Mastercam's Wire and Router programs. This CAM software can be used to write interchangeable programs for nine different CNC machines. This workflow gives the users maximum flexibility to create tools and fixtures that allow the fab shop to accommodate urgent production schedules that require frequent changeovers.
Diversity Rules
Not only are the industries served by Acro diverse, there is even substantial diversity within specific industries. General Manager Bob Coyne tells a humorous story about the rail car business that illustrates this point: The transit authority in New York City is one of the most efficient in the world at moving people. The seats on their railcars line the aisle so that more standing riders can be accommodated. The transit authority in Chicago took notice. They wanted to be more efficient also. So they had some cars made with the NYC style of seating. This caused an uproar in Chicago, because the seated riders, who were accustomed to looking at the backs of heads, did not appreciate the view when they sat on a crowded train facing the aisle. The next round of rail cars went back to the former configuration.
Each metropolitan area has its own idiosyncrasies. The Bay area on the West Coast wants all parts psychedelic in color. On the East Coast everything is more subdued. They are all customized. Further, every metropolitan area wants to use advanced materials technology, so that whatever they find to be aesthetically pleasing can also be made lighter to reduce energy costs.
Short runs of customized components is also a factor with Acro's major customer, which makes 300 systems a year, and each of these has 16 sub systems. That is an annual production volume of 4,800 subsystems that have to be delivered on time at a rate of 400 subsystems a month. To deal with its many product development cycles and delivery demands, the company relies heavily on a schedule so that all parts get manufactured according to their unique production specifications and delivery times.
Systems Approach to CAM
Coyne said that every piece of production equipment in the shop has proprietary software supplied by its manufacturer. As such, the production area operators are likely to be dedicated to one or two specific machines. However, in support operations such as the tool room or at the router cell where steadily increasing volumes of sheet are being cut, it is a different story.
Mastercam is the common CAM programming software used across nine different CNC systems including mills, a router and a wire EDM. Throughout the shop there are 10 individuals who are well versed in Mastercam - eight in the tool room alone.
Coyne said having one CAM system makes it very easy to cross-train people to use a variety of equipment. Additionally, many of the programs can be used interchangeably between various pieces of equipment with little, if any, modification required. The result is a tremendous amount of flexibility for shifting work between various machines and machinists to optimize production scheduling.
"What these guys do is machine details, fixtures, tooling - items that are critical to supporting the main streams of our production manufacturing," said Coyne. "CAM programs are generated quickly working from surface models created in the design department. The programmers/machinists use Mastercam simulation features routinely to make sure that there are no material removal or tool clearance issues. We have seen some interesting parts for such things as hydrogen fuel tow motors and helicopter components. Simulation and other features of Mastercam give us confidence that we can tool up for them accurately and efficiently."
Part of Acro's systems approach is taking measures to ensure that the company will have adequate access to young workers with an interest and aptitude for computer automated manufacturing. The average age at Acro is reaching 50, but the local community college is training its students in the latest version of Mastercam. Acro knows many of them because they offer an apprenticeship program in conjunction with Monroe Community College. It helps that Acro's main programmer, Fred Schubert, is also an instructor there.
The Next Big Thing
In order to make lighter weight fabrications that cost less and reduce energy costs in the field, Acro has been very active in developing manufacturing processes for forming and subsequently machining structural components made from formed high-strength, low-alloy steel. When these steels are laminated to a cardboard backing, they behave more like wood and become very formable and machinable, yet still maintain their essential strength characteristics.
Coyne said, "Our CAD software has allowed our designers to be a lot more creative. They see if they can replace a cast part that used to be really expensive at low volumes and design it out of 5/16 inch sheet, machining in some of the characteristics that used to call for a casting. Because sheet metal at that volume is significantly less expensive than buying a casting, we can offer more competitive pricing."
The challenge for the toolmakers is to develop workholding solutions that lock formed laminates in place for efficient accurate machining. This work has been a strong growth area and the company will be adding a 4-axis router to support manufacturing with these materials. The company's expertise in CAM will expedite development of these innovative new fabrications.
For more information contact:
Acro Industries, Inc.
554 Colfax St
Rochester, NY 14606
585-254-3661
acrosales@acroind.com
www.acroind.com
CNC Software, Inc.
671 Old Post Road
Tolland, CT 06084
info@mastercam.com
www.mastercam.com