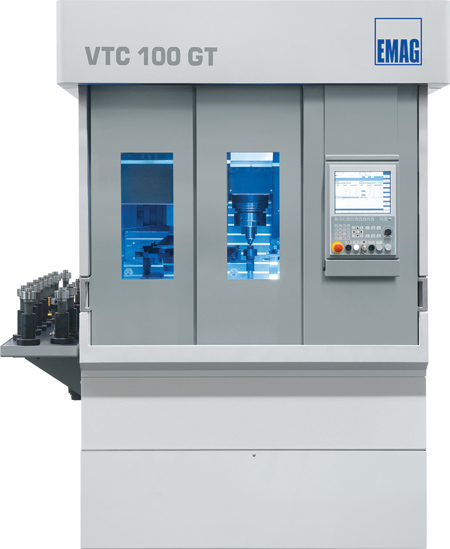
The VTC 100 GT is a vertical shaft production center for combination machining involving turning and grinding.
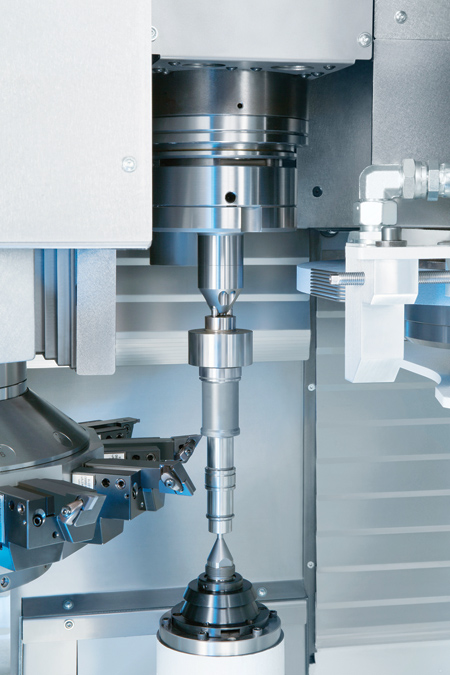
The machining area in the VLC 100 GT: all precision finishing processes (CBN grinding, hard turning and scroll-free turning) are completed in a single clamping cycle.
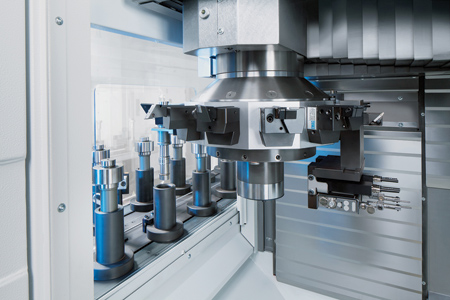
The gripper in the turret takes the raw part from the raw parts storage facility and transports it into and out of the clamping position.
The "FAST 2025" study by the German Association of the Automotive Industry (VDA) describes a trend towards suppliers within the automotive value-added chain. Shorter product cycles and an increasing range of models will change the car market, according to the authors.
What these changes mean for the production processes of suppliers and subcontractors can be seen through the example of shaft machining. "The production of various components versions must take place on a single system with ever greater flexibility and falling batch sizes," said an EMAG spokesperson. EMAG has introduced the VTC 100 GT, a customized production solution designed to meet these requirements on a single machine capable of grinding with aluminum oxide or CBN and the complete final machining of the shaft.
The machining of gearbox shafts, rotor shafts, pump shafts, engine shafts, propeller shafts and balancing shafts can differ greatly, since shaft machining covers a wide range of processes. The strength of the component plays an important role. For example, strong workpieces with a defined blade can be finish-machined by hard turning or using scroll-free turning technology, while a final grinding process is the method of choice for thinner and more fragile parts. The required component quality, machining time (and therefore machining costs), tool costs and energy consumption differ depending on the process used. All of these factors must be weighed against each other.
"It is at this point that the challenge starts for project engineers: grinding or hard turning?" said the spokesperson. "Depending on the component, it may be necessary to invest in a single-technology machine for a specific process, but at the cost of the general flexibility of the production process."
"In practice, this is often unsatisfactory," explained Dr. Guido Hegener, CEO of EMAG Maschinenfabrik. "In our experience, a lot of users manufacture very different workpieces on a single machine. It is, of course, important that the best technology is always used for the specific component and design detail."
With this in mind, the turning and grinding specialists at EMAG developed the VTC 100 GT shaft hard machining center to achieve maximum flexibility of final machining by integrating all hard processes in a single machine where the methods can be changed flexibly to suit the component. The important point for this is that the accessibility of the system ensures short tooling and retooling times.
The typical EMAG design, including integrated automation, is the main reason behind this concept. The VTC 100 GT has a grinding wheel and a disk-type turret that can hold up to 11 tools, with the twelfth tool place in the turret taken up by a loading gripper. Optionally, the machine can also be equipped with a live-tool turret with driven tools and a Y-axis. The gripper takes the component from the raw parts storage facility and transports it into the clamping position where the turret tools can then complete turning operations. Any grinding process takes place immediately afterwards in a second step, but in the same clamping operation. The downtimes between the operations are minimal. After machining, the workpiece is unloaded out of the machining area by the loading gripper.
"Efficient processes are also ensured by the VTC 100 G's motor with a workpiece spindle torque of 70 Nm and a 17 kW drive rating, providing the machine plenty of power in reserve to carry out even difficult machining processes at high speed," said a company spokesperson. "The substantial benefits of the components' vertical positioning is most clear when large volumes of chips are generated while turning the shaft. The vertical design ensures that the chips can fall freely out of the machining area, a major bonus for production reliability."
Quality is the main criterion for shaft machining, since these components determine the efficiency, or lack thereof, of the machine and gearbox. High-performance components in particular have cylindrical bearing seats, shoulders and grooves that require high-precision machining. "The strength of the EMAG approach is its component quality, largely due to the fact that workpieces are fully machined in a single clamping operation," said the spokesperson.
"If different machines or separate clamping operations are used for a shaft, geometry errors can have a cumulative affect," said Hegener. "Our approach drastically reduces this risk. All of the processes take place in a single clamping operation.
"Tool costs can be weighed against each other when selecting the right production process. The choice of process has a large affect on part costs. If necessary, we can advise our customers and help to develop a low cost, efficient strategy."
The compact vertical design features a small footprint of 1.8 meters wide and 3.6 meters deep.
For more information contact:
Peter Loetzner
EMAG LLC
38800 Grand River Ave.
Farmington Hills, MI 48335
248-477-7440
info@usa.emag.com
www.emag.com
Southwest
AR
David Fitzgerald
EMAG LLC
Charlotte, NC
248-595-1117
dfitzgerald@emag.com
www.emag.com
NM
Peter Loetzner
EMAG LLC
38800 Grand River Ave.
Farmington Hills, MI 48335
248-442-6590
info@usa.emag.com
www.emag.com
LA, OK, TX
Ric Lorilla
EMAG LLC
Houston, TX
248-595-1530
rlorilla@emag.com
www.emag.com
Southeast
AL, FL, GA, MS, NC, SC, TN, VA
David Fitzgerald
EMAG LLC
Charlotte, NC
248-595-1117
dfitzgerald@emag.com
www.emag.com
Northeast
NY, PA
James Petiprin
EMAG LLC
38800 Grand River Ave.
Farmington Hills, MI 48335
248-910-8413
jpetiprin@emag.com
www.emag.com
CT, DE, MA, MD, ME, NH, NJ, RI, VT
Jonathan Chomicz
EMAG LLC
Hartford, CT
248-497-8526
jchomicz@emag.com
www.emag.com
WV
David Fitzgerald
EMAG LLC
Charlotte, NC
248-595-1117
dfitzgerald@emag.com
www.emag.com
Midwest
MI, OH
James Petiprin
EMAG LLC
38800 Grand River Ave.
Farmington Hills, MI 48335
248-910-8413
jpetiprin@emag.com
www.emag.com
IL, IN, WI
Tod Petrik
EMAG LLC
Chicago, IL
248-470-2646
tpetrik@emag.com
www.emag.com
IA, KS, MN, MO, NE, ND, SD
Bill Konetski
EMAG LLC
Minneapolis, MN
612-804-0857
bkonetski@emag.com
www.emag.com
KY
David Fitzgerald
EMAG LLC
Charlotte, NC
248-595-1117
dfitzgerald@emag.com
www.emag.com
West
AZ, CA, CO, ID, MT, NV, OR, UT, WA, WY
Peter Loetzner
EMAG LLC
38800 Grand River Ave.
Farmington Hills, MI 48335
248-442-6590
info@usa.emag.com
www.emag.com