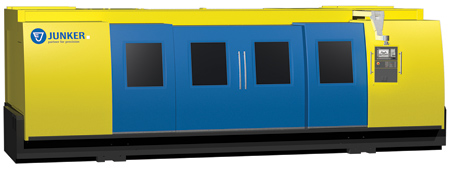
The newly developed JUCRANK 8 from JUNKER is up to ten meters (32.8 feet) long and grinds forged large crankshafts in just one set-up.
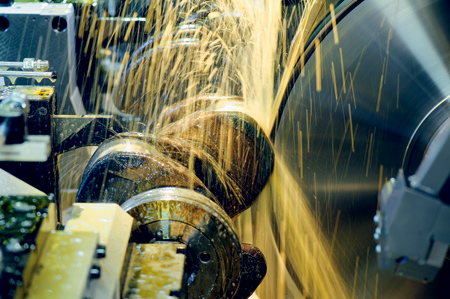
The largest JUNKER platform built to date will soon be put to use for the grinding of crankshafts. Other applications are to follow.
JUNKER has introduced a platform for cylindrical and non-cylindrical grinding of workpieces with a swing diameter of 470 mm and a part length capacity of up to 4,800 mm, initially applied for grinding of large crankshafts.
The platform will first be used in the JUCRANK series for grinding large crankshafts. As these weigh up to 1,000 kg, it is a challenge just to set the parts up for the process. To adjust the table assemblies, JUNKER has developed a slide with an integrated length measuring system. As a result, the setup technician first brings the work heads into position, then the steadies.
Newly Developed Steady with CNC Control
The patent-pending steadies developed by JUNKER are CNC-controlled and have only one axis each. "This considerably increases their stability and stiffness. Each of up to a maximum of eleven steadies can be controlled individually and applied to a section at any time - even during the process. This key feature allows for higher sequence flexibility of the grinding process," said a company spokesperson. "To make this possible, JUNKER applied its proven control concept to a larger, high-performance control system. After all, in its simplest execution the JUCRANK 8 already offers 24 CNC axes."
Integrated Measuring
Large crankshafts are mainly produced in small batches, and in some cases as single pieces. Furthermore, the forging and hardening costs are so high that scrapping a part is disastrous. JUNKER has added an integrated measuring system to overcome these challenges.
The two grinding wheels, each mounted on a wheelhead with its own X- and Z-axis, pre-grind the main and pin bearings. The diameters are measured during the process. Then it measures the entire workpiece after pre-grinding. The taper of each element, the bearing widths and lift heights are measured.
Based on the measuring data, the JUCRANK 8 finishes the grinding process while using the WK axis developed further by JUNKER. During grinding it swivels the grinding spindle, compensating for tapers in the process. With this technology the grinding machine is built to provide each main and pin bearing with its own profile shape, i.e. if necessary with specific crowning. With this functionality, the machine then also grinds the two shaft ends if required. These often feature a taper and not a flange or post end.
Another possibility of applying the new JUCRANK technology is for the re-grinding of used crankshafts. The crankshafts are ground based on the measurements taken by the machine in record time.
Prospective Applications Outside of Crankshafts
The first two machines were ordered for grinding of large crankshafts, however there is also potential for other applications - for example: printing rollers and electric motor shafts. JUNKER therefore built the first JUCRANK 8 for its technology center to develop the grinding of new applications.
For more information contact:
Erwin Junker Machinery, Inc.
2541 Technology Drive, #410
Elgin, IL 60124
847-488-0406
info@junker-usa.com
www.junker-usa.com