
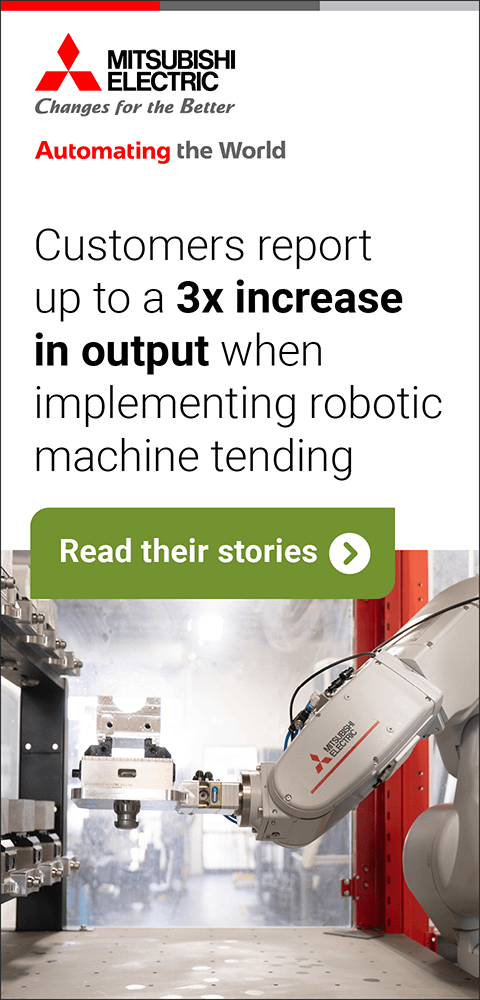
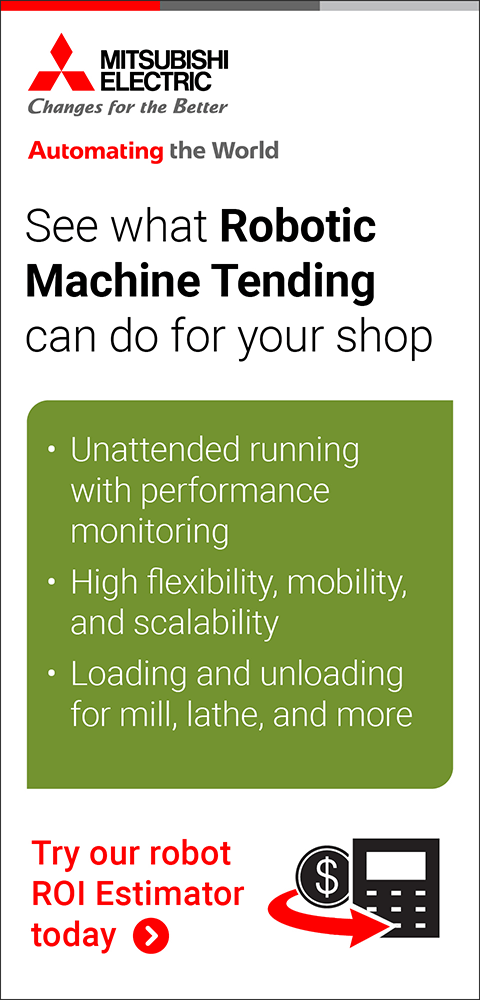
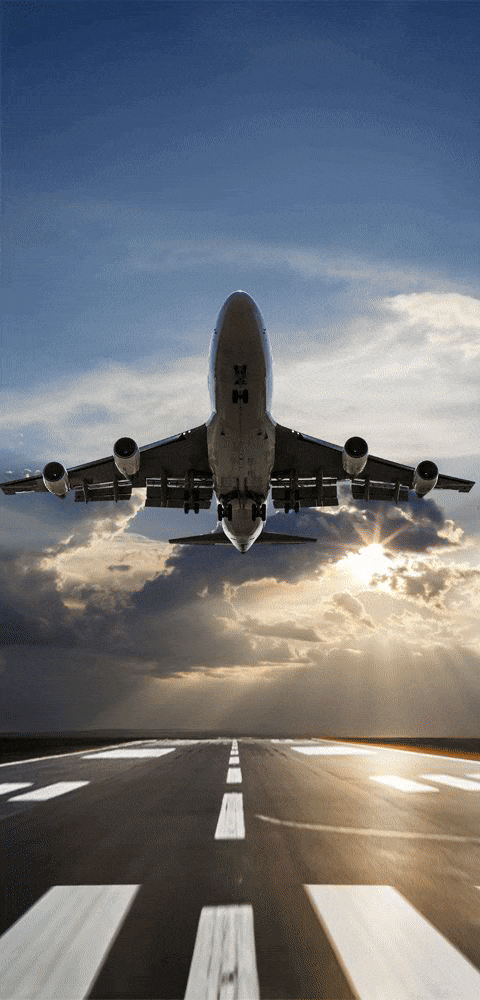
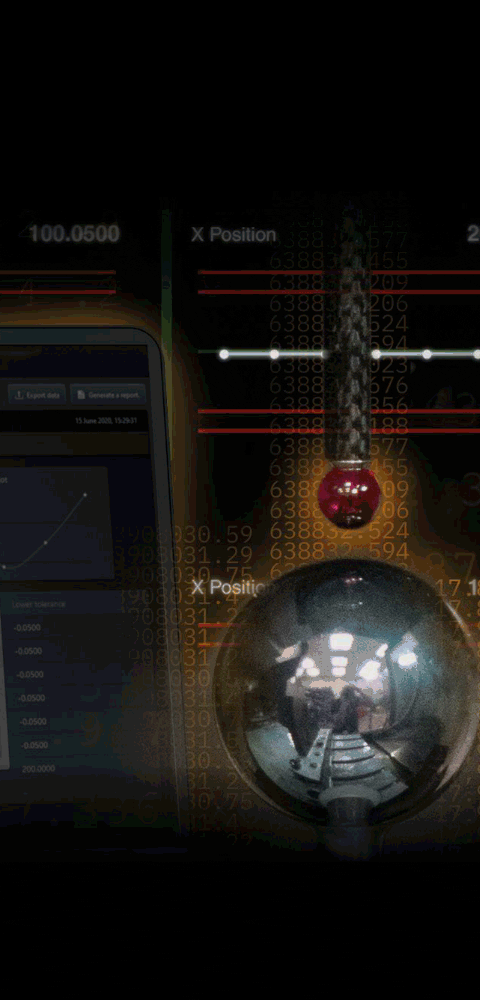
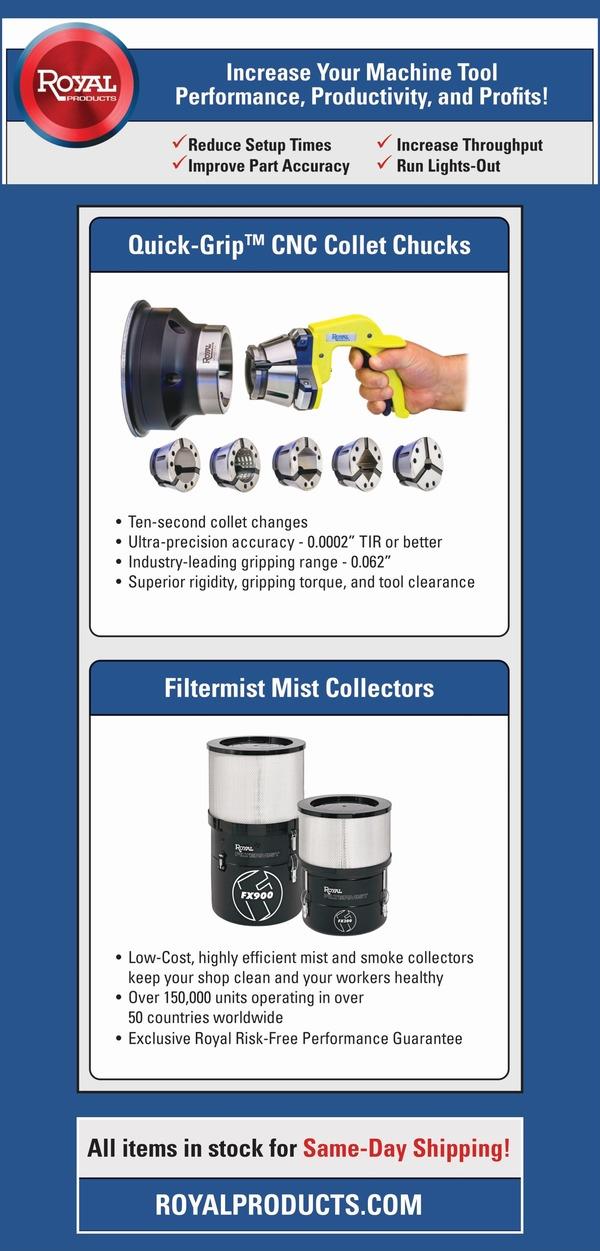
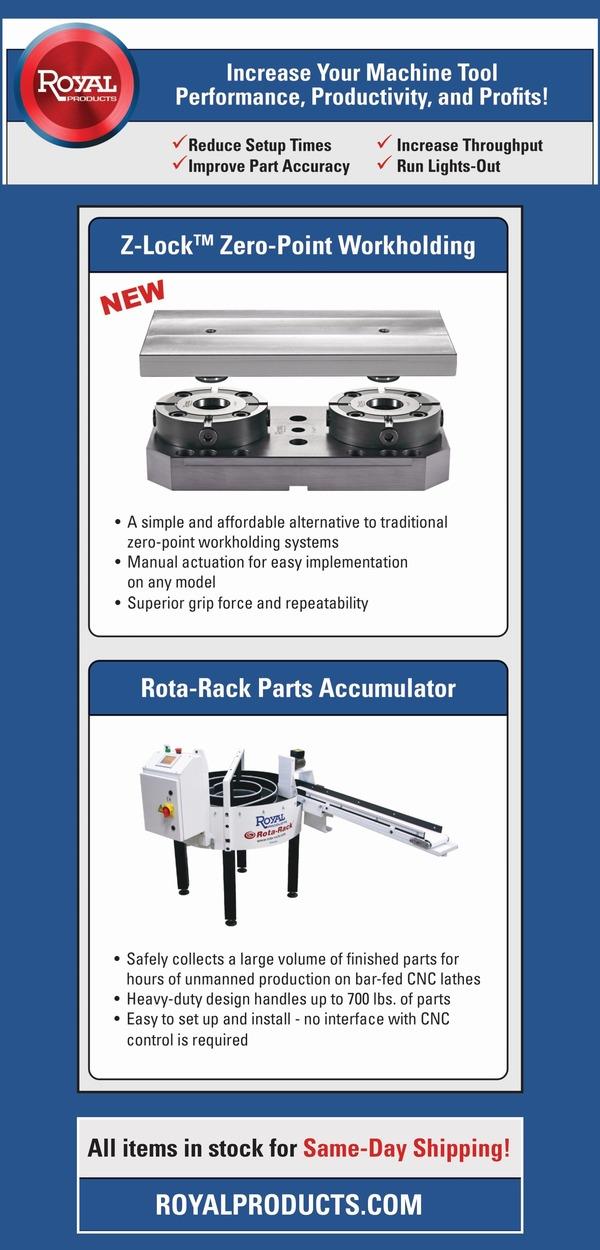

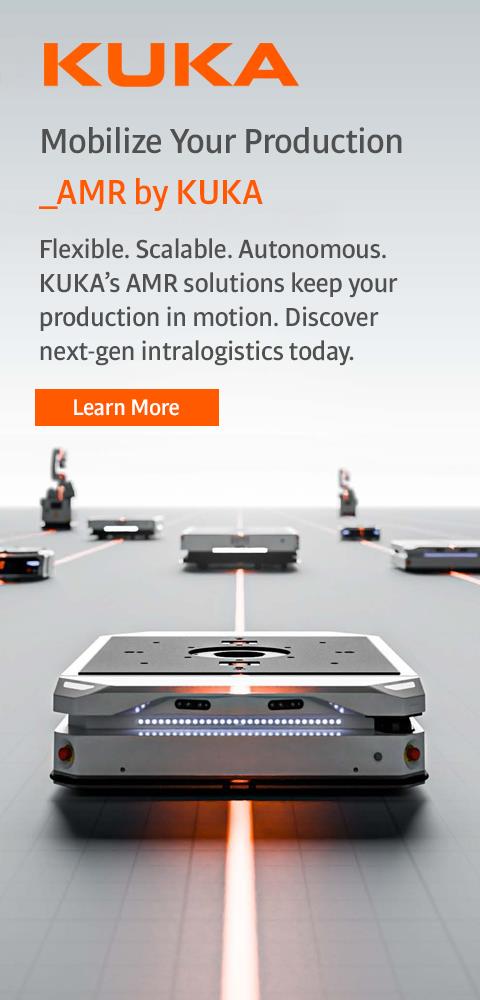
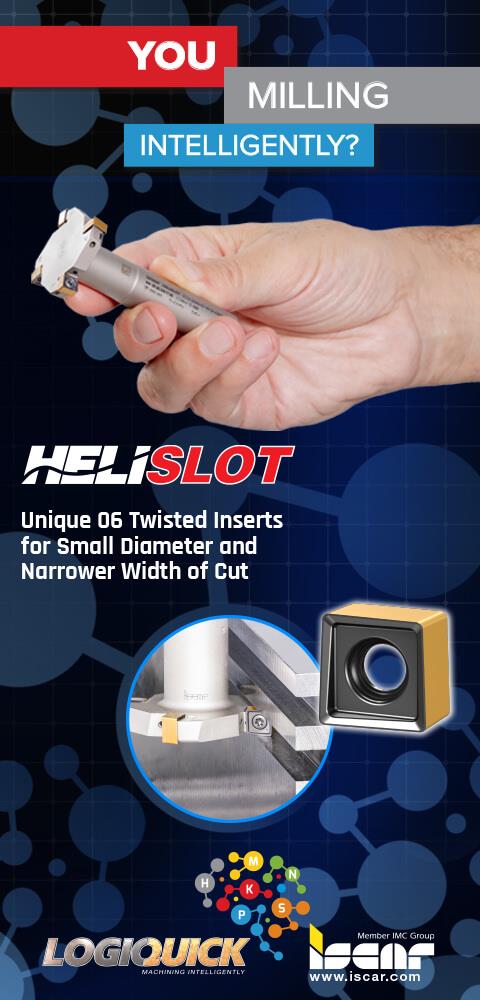
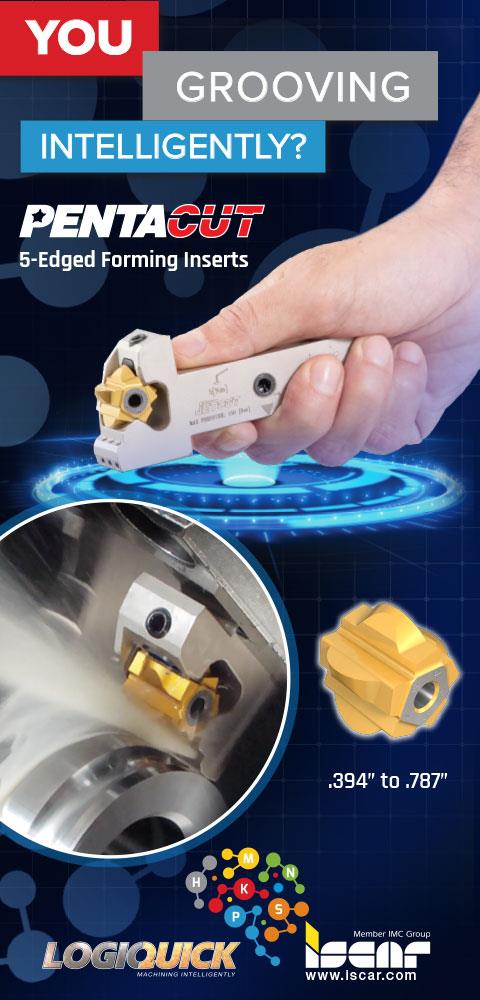
Bevel Gear Lapping Technology
November 1, 2015
Gleason Corporation has announced SmartLAP, a technology for lapping bevel gear sets that is engineered for productivity, control and data collection.
Available on the Gleason 600HTL Turbo Lapper Hypoid Lapping Machine (both new and as a field retrofit), the SmartLAP system combines a gear spindle design with real-time motion-error measurement. "It brings dynamic lapping forces under active servo control. The instantaneous tooth-to-tooth forces are no longer just a function of incoming part quality and passive physics but are instead actively modified by this smart mechatronic system to consistently improve DIN/AGMA part quality," said a company spokesperson.
Pinion speeds and gear torques can now be increased by 30% or more without introducing spacing errors. The system is also designed to compensate for workholding runout errors, making production less sensitive to tooling conditions. In addition, the tester-like data that is collected is displayed during the lapping process, giving users real-time insight into the process. This technology is aimed at high-volume automotive-size gear set production.
For more information contact:
Gleason Corporation
1000 University Avenue
P.O. Box 22970
Rochester, NY 14692-2970
585-473-1000
sales-americas@gleason.com
www.gleason.com
< back