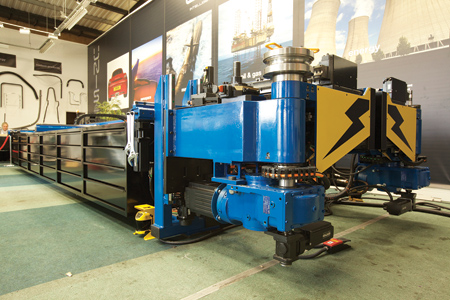
Unison is supplying Byers Precision Fabricators with a versatile 2-inch capacity dual-head bending machine to help accelerate production of complex tubular parts.
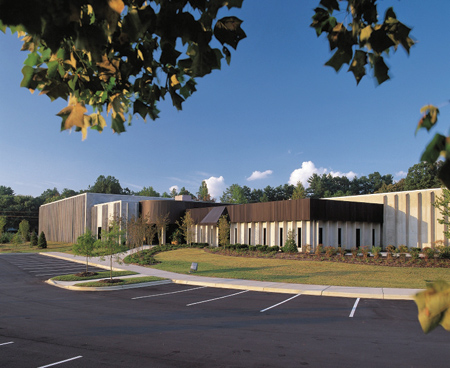
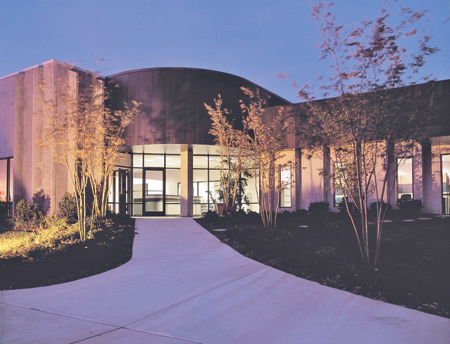
Byers Precision Fabricators' prestigious workshop facility in Hendersonville, NC, will act as a reference site for Unison's all-electric CNC tube bending technology.
Unison's North American support office in Asheville, NC, received its first order for an all-electric CNC tube-bending machine, just weeks after opening. Byers Precision Fabricators, Inc., of Hendersonville, NC, placed the order for a versatile dual-head machine that is capable of meeting a diverse range of tube and pipe bending needs.
Byers Precision Fabricators produces components and assemblies mainly from sheet and tubular aluminum and stainless steel. Most tubular parts are fabricated from 3/8 to 1-inch ANSI Schedule 40 or 80 stainless steel pipe stock. Until now, Byers has outsourced the bulk of its tube and pipe bending needs to third-party suppliers, except for a small amount of work which it produces using manual bending techniques. However, a Byers spokesperson reported that this approach was becoming increasingly expensive and created production bottlenecks.
"Bringing our tube bending operations in-house greatly enhances our flexibility to meet complex shape requirements, tight delivery schedules and last-minute design changes - which is important for several of our customers in processing sectors such as nuclear power," said Roger Byers, President of Byers Precision Fabricators. "It also allows us to broaden our range of fabrication services, which is critical for a subcontracting workshop like ours. We chose a Unison machine primarily on the strength of its performance and the company's reputation.
"Buyers Precision Fabrications is a modern machine shop. From the outset, the company was keen to avoid the type of hydraulic tube benders that are used by many fabricators, which are notoriously noisy and difficult to keep clean. It was also deterred by the difficulty of obtaining accurate and repeatable results from hydraulic machines. Avoiding material wastage was another factor - hydraulic tube bending often necessitates multiple trial runs before a good part that meets specification can be produced," said a company spokesperson.
Having chosen to adopt all-electric CNC tube bending technology, Byers looked at various manufacturers and chose a Unison machine. It also found that Unison was prepared to develop a bending solution to meet specific application needs. "The fact that the company has just opened a support office in Asheville, a short drive from Byers' facility in Hendersonville, was the final clincher," said the spokesperson.
The machine for Byers is a version of the 2-inch (50 mm) capacity CNC all-electric tube bender from Unison's Breeze range, customized to maximize versatility of use. The machine features two independent bend heads that provide both left-hand (CCW) and right-hand (CW) bending to accommodate the most complex shape requirements, and is capable of handling many popular tube and pipe sizes - including 1.5 inch Schedule 40 stainless steel stock with an outside diameter of 1.9 inches. The machine bed is designed to accommodate tube lengths up to 20 feet.
Some of the more specialist parts that Byers currently produces feature a variety of complex, closely spaced bends, with radii as small as 60 mm. The Unison tube bender will enable the company to produce these parts efficiently in a single uninterrupted machine cycle. Single-piece part fabrication will also help Byers to further increase the speed and efficiency of production by eliminating multiple cut-to-length and welding operations. An advantage of the Unison machine is its fully automated, software-controlled setup. Byers produces parts in a wide range of batch sizes, even in single or very small quantities, so machine set-up time has a major bearing on productivity. The machine that is being supplied to Byers can typically be reconfigured by a single operator in less than 15 minutes.
To help maximize throughput and accelerate right-first-time production of parts, both bend heads on the machine will be equipped with Unison's laser-based spring-back measurement and correction system. This helps to ensure bending precision by automatically compensating for the natural tendency of metal tubes to spring back slightly after being bent.
Unison will also be supplying a comprehensive control and support software package. In addition to Unison's Windows-based Unibend machine control software, this will include Internet-based remote diagnostics and video monitoring facilities, as well as an Op2Sim 3-D tube-bending simulator.
The simulation software uses a CAD (computer aided design) model of the bending machine to generate detailed video imagery. It offers collision detection facilities, with user-adjustable parameters for real-world environmental factors such as the distances between the tube centerline and the ceiling, floor and walls of the workshop, and has built-in artificial intelligence to reiterate bend cycles until a successful solution is found. The simulator will enable Byers to develop production-ready tube bending programs offline, without needing to test and optimize them on the bending machine, saving valuable production time.
The data for bending programs and simulation can be input manually from customers' drawings, derived from CAD models of parts, or obtained by reverse-engineering existing components using Byers' tactile or laser-based CMMs (coordinate measuring machines).
"The bending machine will be networked to our CAD/CAM facilities - Unison is handling the system integration aspect. About 90 percent of our customers submit drawings, and most of these are backed by CAD models," said Jeff Cox, a member of Byers' CAD/CAM Department. "We use SolidWorks CAD software extensively for design and development work, so we have also ordered the TubeWorks add-in software from Unison. This will enable us to extract manufacturing information such as tube specifications and CNC bending data direct from the CAD models in a matter of minutes, accelerating our RFQ (request for quotation) procedures."
"This is the first order that Unison has received following its decision to open a direct sales channel in the U.S. and comes from a renowned manufacturer. We are also delighted to announce that Byers has agreed to act as a reference site for Unison. Its Hendersonville facility is only 15 miles from our office and we look forward to showing our bending machinery operating in such a modern fabrication environment," said Dale Coates, responsible for Market Development at Unison's Asheville office.
For more information contact:
Dale Coates
Unison, Ltd.
28 Schenck Parkway, Suite 200
Asheville, NC 28803
828-771-0850
dalec@unisonltd.com
www.unisonltd.com