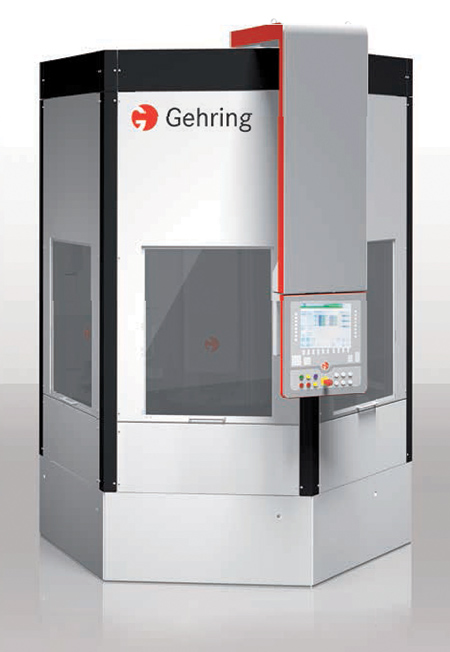
Lifehone honing center with inner column and rotary table
In recent years honing has become a worldwide leading high performance process. There is hardly anyone in the entire metalworking industry who wants to manufacture without a performance advantage. Honing is a precision stock removal process for practically all materials.
The Goals of Honing Are
- To reach diameter tolerances in the range of um
- To improve the accuracy of form and position tolerances
- Optimize the tribological characteristics.
Due to the increasing demand for friction-optimized sliding surfaces, the demands on the honing process increases. Gehring confronts these challenges every day.
Lifehone - High Precision Technology in a Gehring Design
Small bore diameters often place different demands on the production technology than large ones. Problems such as a less favorable length/diameter ratio of the bore and less available space have to be solved.
Due to the customer requirements Gehring has continuously improved its lifehone machine. Functional modules have been included in a modular design. Whether constructed as a multi-spindle transfer solution for mass production, or as single-spindle design for small batches - highly accurate parts with honing diameters up to 90 mm can be processed optimally with the appropriate machine.
Easy Operation and Optimal Conguration Options
Gehring selects the appropriate spindle unit based on workpiece design and the required speed dynamics. The Gehring honing control allows for precision controlled stroke speeds and reversal precisions.
For the stroke drive, manufacturers can choose between a ball screw and a linear motor.
The graphic interface of the Gehring operator panel (GOP), as well as the program assistant, eases machine operation. After entering a few relevant parameters about the component, material and tool, the process and stock removal can be defined, and honing can be started once the tool has been positioned. The stroke position and all other relevant parameters for machining the component are automatically calculated.
The bore diameter and the conicity will be determined by a pneumatic gauging system and graphically shown on the display of the honing control. Depending on customers request, in-process as well as pre- and post-gauging systems can be installed.
It is possible to integrate a brushing process to deburr slight burrs at the edges of holes or cross holes produced by honing. An option is also available for the integrated cleaning of the workpiece by centrifugal application or air blowoff station.
A Complete Package
The super finishing of high-precision components depends on the coordination of all influencing factors to the honing process such as the honing tool, abrasives, fixtures, feeding and gauging systems. All of these elements must be matched to one another to achieve an optimal result.
"Gehring supplies manufacturers with the complete package from the abrasives to the machine, so that manufacturers always receive the perfect solution for the application," said a company spokesperson.
The newly developed single-stone L series tooling system is especially designed for honing high-precision bores with a diameter range of 3-15 mm. The tool joint and base are assembled by means of "thermal shrinkage". This joint features high concentric accuracy as well as the capability to transfer high torque and axial forces. From a diameter range of 5 mm and larger, Gehring can offer manufacturers tools with an active honing stone retraction. By eliminating the retraction bushing for abrasives, the tooling design gets shorter and so the stability increases. In addition, the contact of the bore wall during expansion of the tool is avoided, thus increasing the quality.
Besides tools and abrasives, Gehring offers manufacturers various automation concepts - automatic loading or unloading with robot or gantry are possible.
Lifehone Machines with Rotary Transport
- Flexible one-spindle honing center
The single-spindle version of lifehone series has a compact design and small footprint. Depending on the machining task and the batch size this type of machine can be equipped with a fixed or rotary table and up to four stations. This is a solution for customers with limited space or must frequently change the type of workpieces.
- Flexible two-spindle honing center
This version can be equipped with one or two honing spindles. In general, rotary tables with three to eight stations are installed. These stations can also be used for measuring or brushing operations. Compared with the pure single-spindle honing center, this variant is wider by 60 cm. The two spindles allow for a two-stage honing process, shorter honing times and the honing of more material.
Due to the great demand for machining of gears, Gehring's two-spindle lifehone machine is especially designed for the needs of machining of gear types. The integrated gripper transport offers the possibility to cycle gears with different diameters. Furthermore, the user only needs one fixture below the two spindles.
Gehring has adapted a honing tool with an internal measuring system specifically for the given requirements. The honing process is stabilized by a counter-guidance, thus leading to an improved honing quality. Abrasives can be replaced in a short time when equipped with compact honing stones.
- Honing center with inner column and rotary table
"The rotary table is placed around the inner column so we can guarantee quick access to the process stations, a good over-view and a quick and easy changeover. Additionally there are maintenance panels to set up the process in a short time," said the spokesperson.
Alternatively equipped with a six or eight-sided inner column you can fix up to seven honing spindles. Pre- and post-gauging stations are fixed on the opposite side to optimize the interior space the best way possible. Another design feature is the compact design and the resulting low space requirement in a facility.
The Gehring Operator Panel can be led around the machine so that it is easily visible from any location.
Honing Center with Inner Column and Rotary Table
- Horizontal honing machine for pinion gears
"Gehring's three-spindle lifehone series for pinion gear processing has already proven itself in the market. The main difference compared to the other lifehone machines is the horizontal honing of the work-pieces," said a company spokesperson. The machine is loaded via a handling system from the pallet. In general, the number of workpieces per pallet is between five to 10 pinion gears.
The advantage of pallet method is the shortened processing time per workpiece.
- Multispindle transfer honing machine
The lifehone transfer design is usually recommended for solutions with four or more spindles. Depending upon the desired cycle time and the honing process, the machine is designed with the proper number of spindles. This design is also suitable when different bore diameters must be processed on one workpiece.
MicroStar - Three Processes on One Machine
In order to offer an innovative solution for the machining of pinion gears to its customers, Gehring has jointly developed the new MicroStar 285. The machine is one single rotary transfer machine that ideally interconnects finishing, grinding and honing. The MicroStar F-G-H is a high precision machine tool for carrying out several high precision operations in one chuck.
The machine features an indexing table with eight tool spindles as its base. All tool units are arranged around a central column. After generating a highly precise reference face on one face of the workpiece all subsequent operations like finishing, gaging, bore grinding and honing are carried out with the workpiece clamped in one chuck.
For more information contact:
Gehring L.P.
24800 Drake Road
Farmington Hills, MI 48335
248-427-3901 / 888-923-9760
info@gehringlp.com
www.gehringlp.com