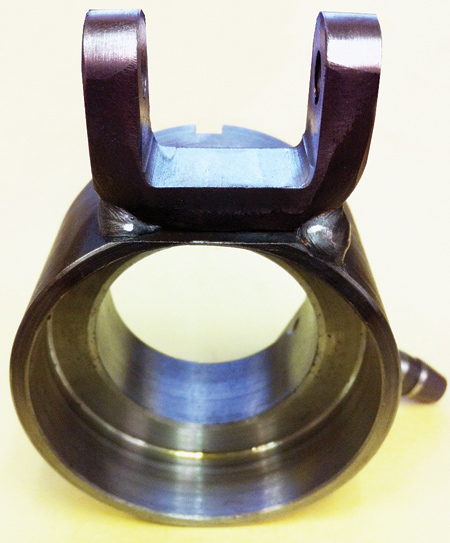
Anti-rotation adaptor assembly to be affixed to an electronic steering mechanism.
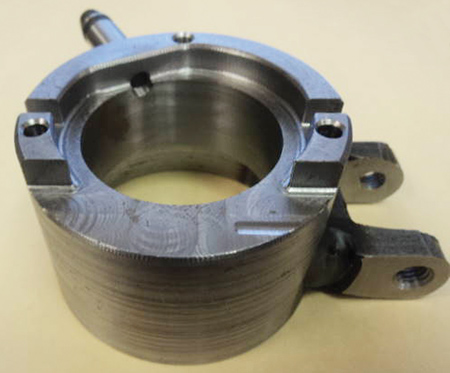
Multiple tight tolerance machining operations must be performed on the base of the part.
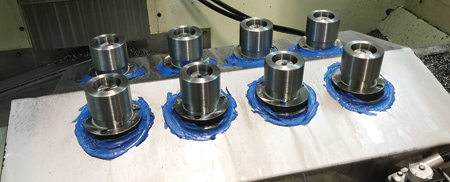
A sub-plate assembly incorporating eight Hainbuch hs docks clamp the I.D. of the parts to assure high precision while generating increased production.
CSM Manufacturing Corporation of Farmington Hills, MI, has been an exclusive supplier to the automotive industry since its founding in 1978. The company, which now employs 150 skilled workers, offers a variety of services including CNC machining, Acme Gridley and Davenport screw machining, cold heading and stamping. Components produced include transmission valves, engine housing parts, steering column parts, steering pistons and others.
The company was recently awarded a contract for the anti-rotation adaptor assembly that is affixed to the electronic telescopic steering mechanism. Management was faced with the need to develop a production solution capable of maintaining high-precision tolerances. Al Knightley, Engineering Manager, explained, "The part is particularly challenging because of the number of operations, as well as the tolerances.
"The first operation involves machining the base on a screw machine," continued Knightley. "On the next operation, CNC Mill Op #1, 50% of the machining is completed. A U-shaped bracket is then welded to the part. The next operation is CNC Mill Op #2, in which the remaining machining is completed, including the machining of the bracket. The assembly is then finished and hand deburred." The base is SAE 1215 steel and the bracket A36 stamping material. The finished part is 2-11/16" diameter x 1.800" in length. Knightley commented, "Tolerances run .008 inch on length and .002 inch on drilled holes."
The parts are made on five Fadal 5-axis machining centers equipped with three rotary indexers. "The solution to maintaining tolerances throughout the process involves the use of high-precision workholding systems from Hainbuch America," said Knightley. "The original set-up consisted of a series of sub-plates, on each of which were mounted two Hainbuch devices operated by hydraulic or pneumatic lines." These were affixed to the rotary indexers for the rapid processing of the parts.
"The success of the system and the need for greater production led us to design a series of sub-plate assemblies that are each equipped with eight Hainbuch hs docks equipped with expanding mandrels that clamp the I.D. of the parts," continued Knightley. "At present, we have two machines performing the first operation and three completing the second. The results have been dramatic. Formerly, the yield in the first operation was 18 to 20 parts per hour. That has now increased to 35 parts per hour. In the second operation we are completing 30 parts per hour, and at present, we are delivering 840 parts per day. Our quality control demands include a variety of measurements on equipment including gauges, comparators and coordinate measuring machines (CMMs). All specified measurements are maintained and exceeded."
Larry McMillan, Hainbuch representative, stated, "The CSM team's solutions are an excellent example of out-of-the-box thinking. Many of our customers associate Hainbuch products with quick-change capability for holding multiple different sized parts. In fact, the first arrangement used a Hydrok O.D. chuck equipped with a mandrel and was used for both O.D. and I.D. applications. As demand for the part increased, the CSM team saw the advantages inherent in defining a precision/production equation to meet their customer's needs."
As Al Knightley said, "Historically, given the need for large quantities of high-precision parts, automotive applications have always required innovative manufacturing solutions. At CSM Manufacturing Corporation, we are proud to be advancing that tradition."
For more information contact:
CSM Manufacturing
24650 N. Industrial Dr.,
Farmington Hills, MI 48335
248-471-0700
info@csmmfg.net
www.csmmfg.net
HAINBUCH America
W129 N10980 Washington Dr.
Germantown, WI 53022
800-281-5734 / 414-358-9550
sales@hainbuchamerica.com
www.hainbuchamerica.com