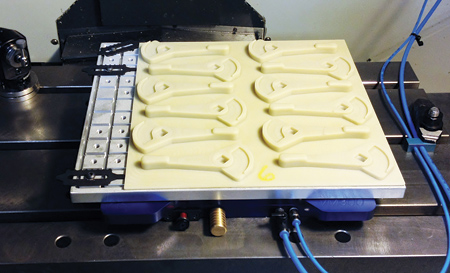
In-process shot of cam actuator handles for a medical application. When finished, the cross section between the square through hole and the hooked end of the tool is only 0.020". The part is made on the Vac Magic system in a vertical mill.
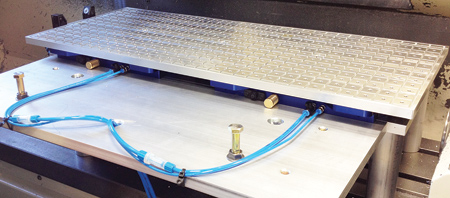
Straightline had to produce a part that was larger than the machines travels. "We took two Vac Magic systems and mounted them side by side with a large sub-plate supplied by Mitee-Bite," said Paulson. "We produced the part by machining one section at a time and indexed it on the Vac Magic along the machine's X-axis to access the next section of the part." The whole vacuum system has been raised up on aluminum pillars to clear the fourth axis rotary table and the Renishaw laser tool pre-setter. Flatness and parallelism were critical over a large span.
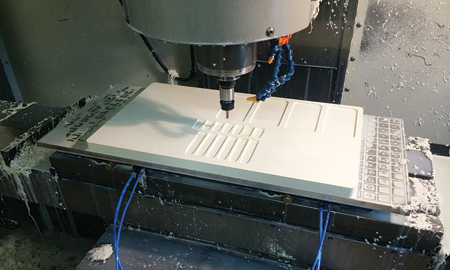
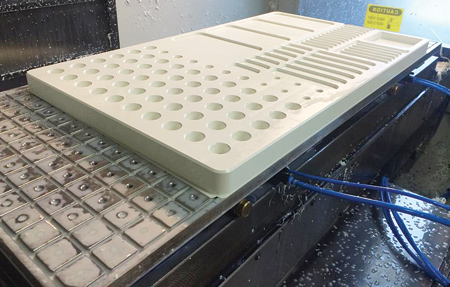
The dual Vac Magic bases are combined with a large sub-plate for machining a large plastic tooling tray used to hold all of Straightline's in-house produced CMM fixturing.
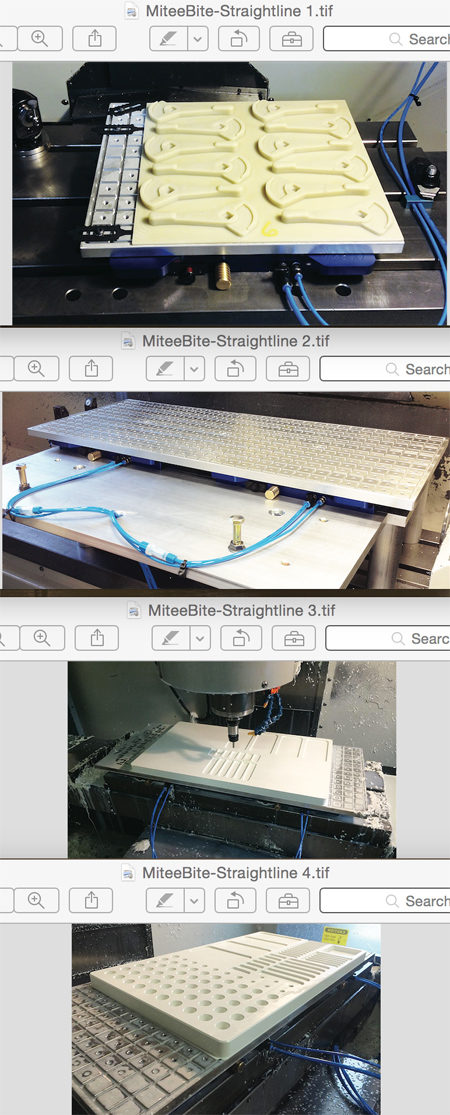
Straightline Precision Industries was recently challenged with producing a specialized cam actuator handle for the medical industry. The lever had very thin cross sections in many areas of the cam section spanning fairly large gaps. These would be very difficult to machine without deflection and there would also be issues in holding tight tolerances and finishes. The part was also manufactured from a very expensive engineered material; therefore the ability to nest the parts tightly in the stock was a consideration.
The part was produced in a vertical machining center and conventional means of holding the sheet stock were considered, such as screwing the material to a sub-plate, cutting the material into individual pieces and using vises, etc. None of these options fit every criteria, especially the main issue of supporting the large thin cross sections.
"After years of positive experiences with our most trusted workholding supplier, I decided to get on the phone to Andy Arsenault at Mitee-Bite Products," said Straightline Precision Industries Owner DJ Paulson. "He reviewed the part with his engineers and informed me of their vacuum plate system, called Vac Magic, which he thought would be the best option to hold the part securely while maintaining excellent support for maintaining the tolerances of the thin sections on the part."
Previous considerations had been to use Mitee-Bite's fixturing wax, called Mitee-Grip, which could accomplish similar results. However, Straightline needed something that was very quick to change over in high production and, due to the porous nature of the material, Paulson was unsure how it would be effected by the wax, so he chose to use the vacuum clamping method.
"We chose to go with the Vac-Magic system, and immediately upon delivery we were blown away by the attention to detail that Mite-Bite put into its product," said Paulson. "Everything is thought out very well. The main plate incorporates precision locators to facilitate the use of the vacuum plate as a quick change fixture. We had used vacuum fixturing many years ago, with a very expensive vacuum pump, but the Mitee-Bite system uses standard shop air to actuate the vacuum, and is therefore much more simple, quiet and reliable."
Straightline has been using the Vac Magic very successfully and reported that it has had no issues. "The part we are producing is held down extremely rigidly and the finishes are exceptional," said Paulson. "The thin sections of the part are pulled down directly against the precision face of the vacuum pallet and are supported 100%. We get no chatter, and can maintain the thicknesses every time. Because we do not have to screw the material to a sub-plate and can avoid the screw heads during machining, we can nest the parts much closer together and get a better yield out of the expensive materials."
"The Vac Magic made us more competitive on this job because it required no prepping of the stock, and it also allowed for more efficient stock utilization," continued Paulson. "It is also very quick and simple to set up, and has eliminated several potentially problematic issues with the machining of the part."
Straightline has found many other uses for the Vac Magic and is benefitting also from its ability to act as a quick change pallet loader. "We can now set up many different jobs on fixture plates and in seconds be fully changed over from one job to the next," said Paulson. "This has proven very useful in running high volume production, where the parts can be loaded offline and then the pallets can be quickly swapped out once the machine cycle is finished."
Straightline, owned by Dennis and DJ Paulson, who are both journeyman machinists by trade, provides aerospace and medical machining. The company specializes in multi-axis machining, including 9-axis mill/turn, 5-axis machining, Swiss turning and 4-axis horizontal machining. Other capabilities include robotic machine tending, laser engraving, temperature controlled QA lab with 5-axis Zeiss CMM and injection molding.
"We make it our goal to exceed customer expectations in CNC manufacturing while giving excellent value and reliable service, as well as working closely to achieve the customers' ultimate goals," said Paulson.
For more information contact:
DJ Paulson, Owner
Straightline Precision Industries
#2-10019 Galaran Rd., Sidney
British Columbia, Canada
250-655-6603
spi@shaw.ca
www.straightlineprecisionindustries.com
Andy Arsenault
Marketing & Sales
Mitee-Bite Products LLC
P.O. Box 430
Center Ossipee, NH 03814-1430
800-543-3580
miteebite@miteebite.com
www.miteebite.com