
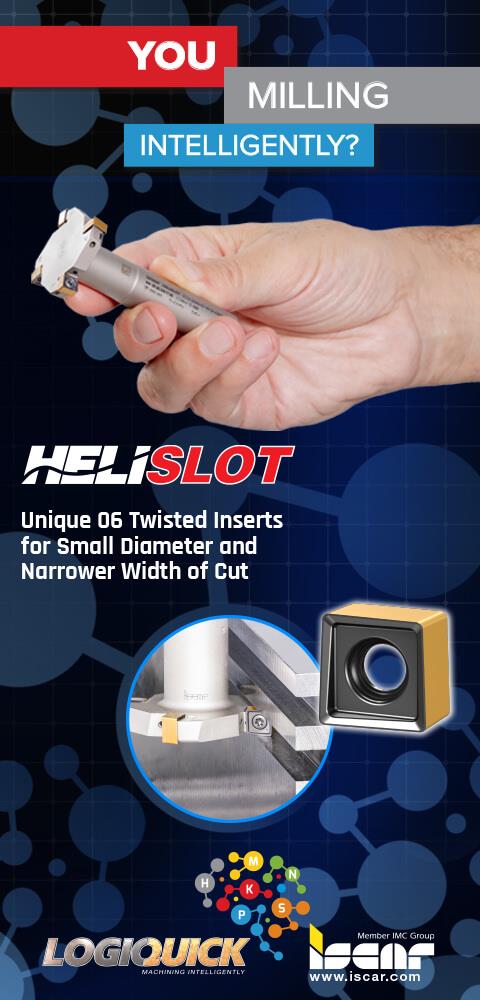
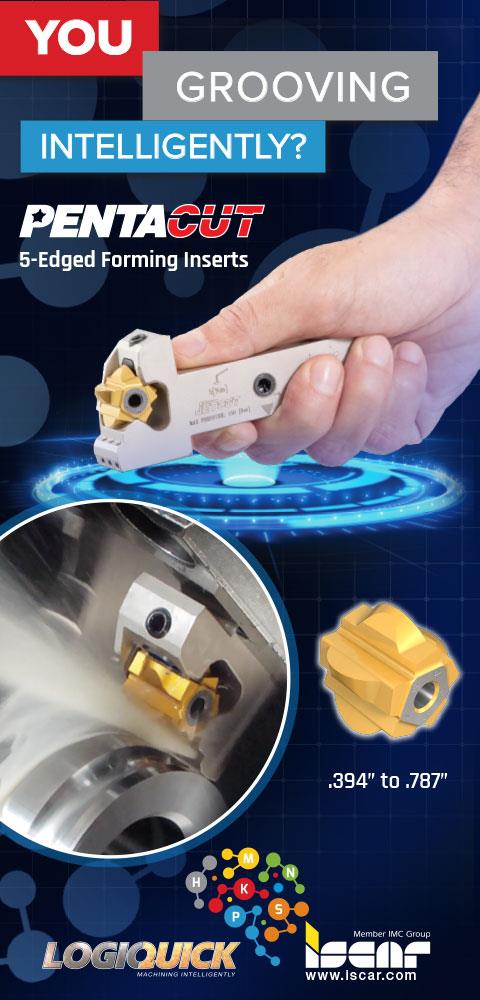
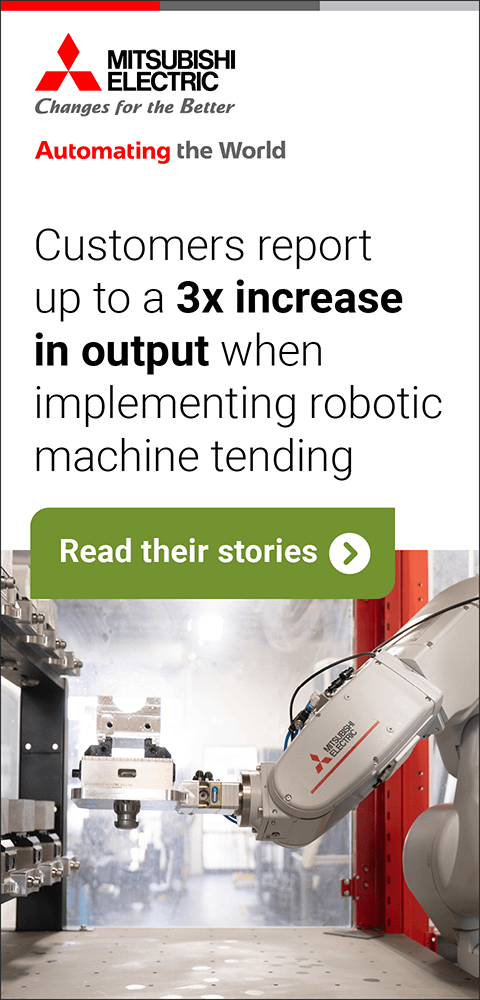
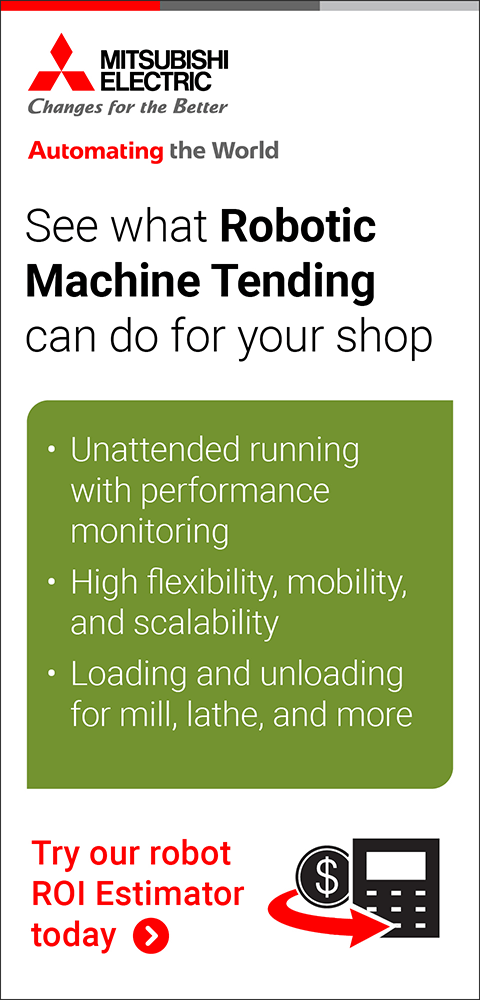
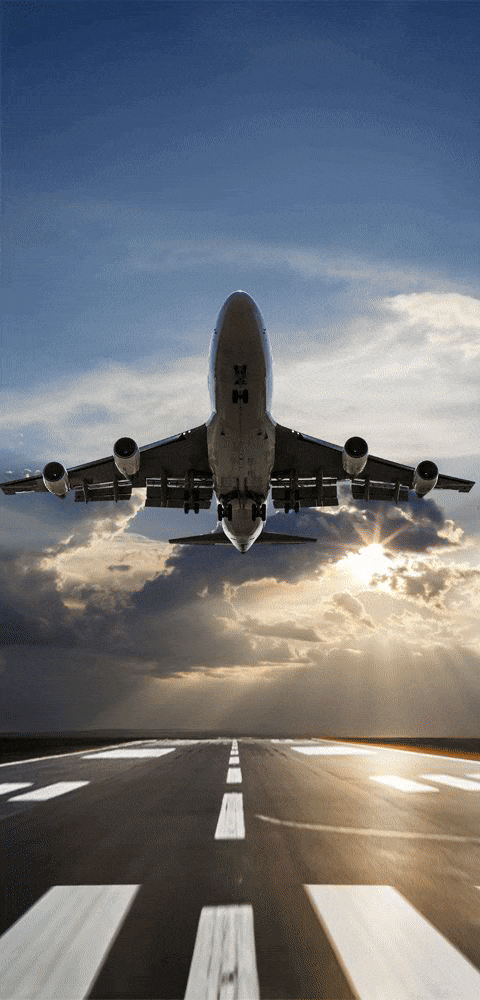
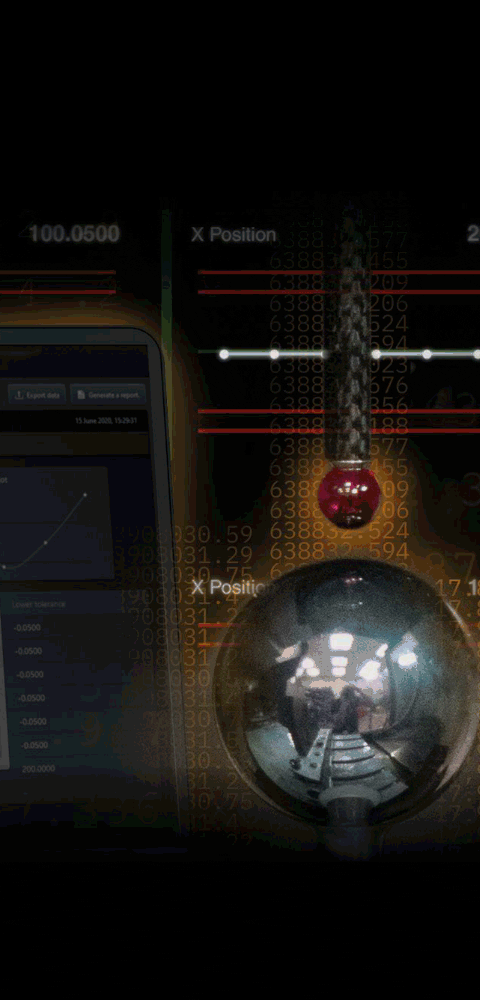
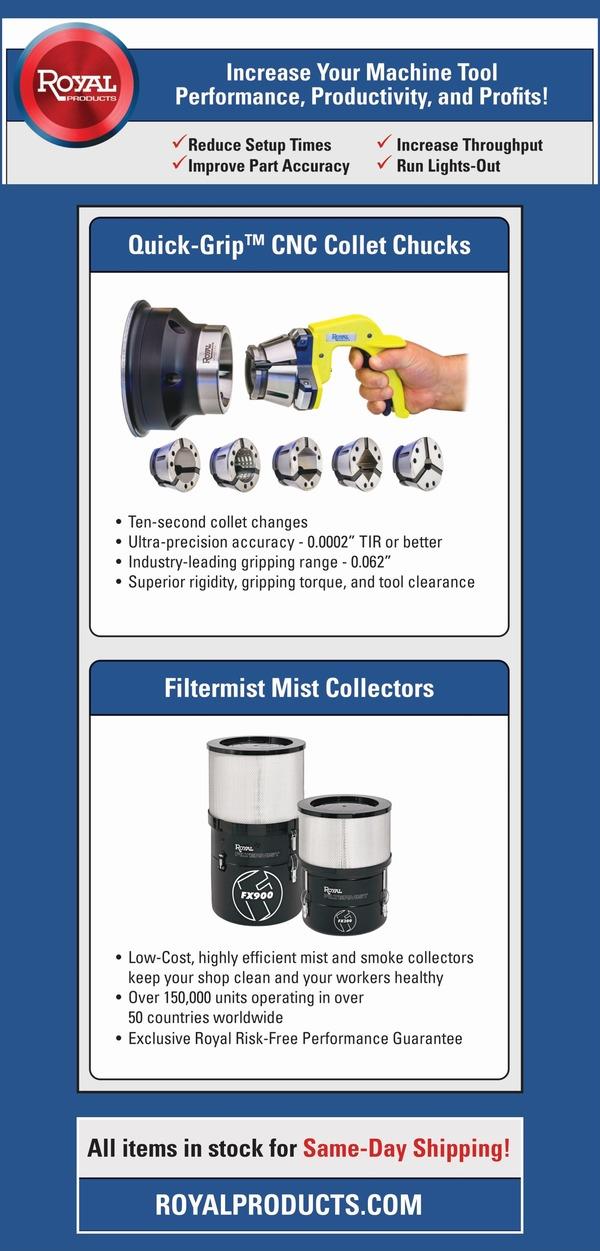
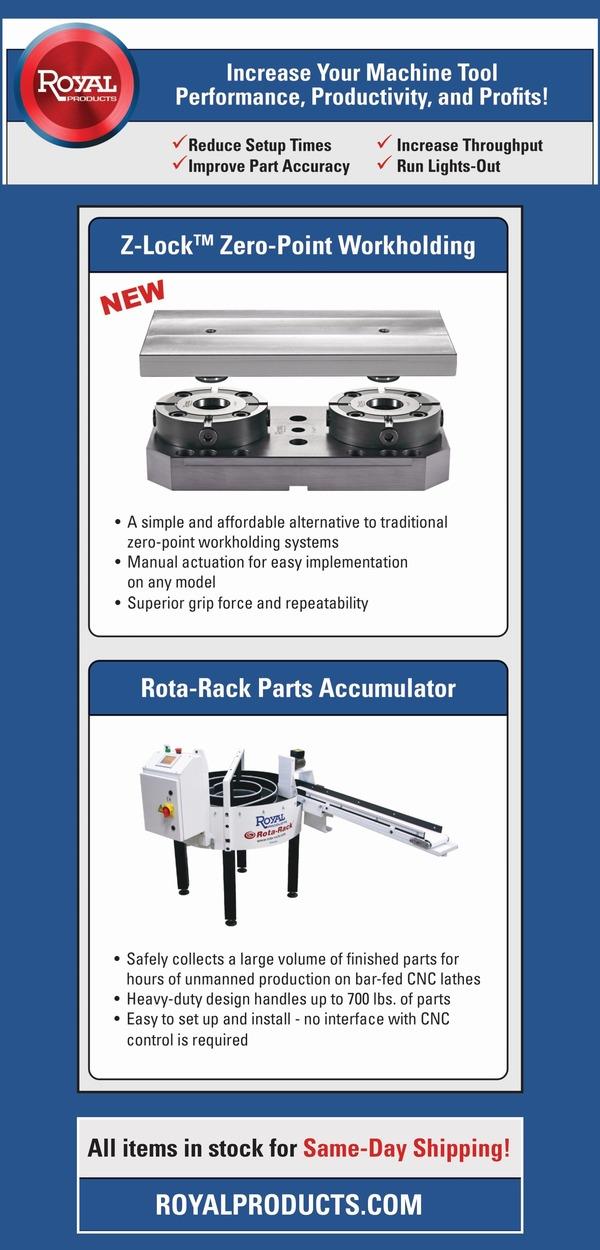

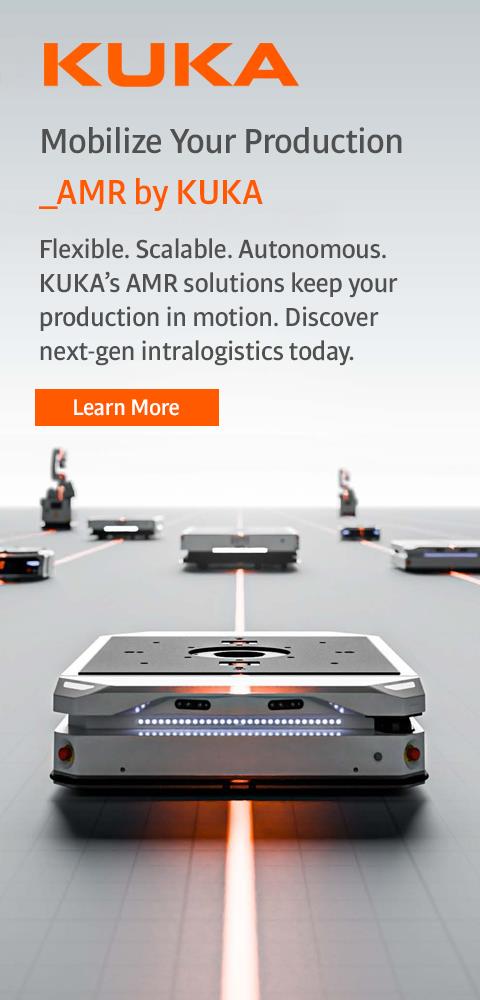
Chip-in-Spindle Detection System
July 1, 2015
After several years of collaboration with two industrial associates from the Allgäu region of Germany, GROB engineers have finally found a solution for dealing with chips during a tool change: the GROB motor spindle with an intelligent spindle nose. With this GROB innovation, after an automatic tool change, the tool interface checks with ultra-precision for the presence of chips. Because this chip-in-spindle check is also cycle-time neutral and no alterations are required in the machine's working area, for many machining centers this development is an excellent way for improving reliability during an automatic tool change.
The sensors in the spindle nose detect any asymmetric deformation caused by chips at the tool fixing point and assess it. The information is transmitted via high frequency radio signals to the machine control, which then flags up the faulty tool change. The energy for the sensors in the spindle nose is supplied through one stationary and one rotating induction coil. The combined electronics and gauging technology affects only the design of the spindle face. The reading is taken when the spindle is at a standstill immediately after tool clamping. When the reading is taking place, the feed axes move to the new machining position. The accuracy of the system is impressive. Chips are reliably detected, which at a distance of 150 mm from the face contact on the HSK A63 toolholder can cause a change in concentricity at the tool of only 0.01 mm. It is immaterial whether the chips are in the tool taper or in the face contact area.
For more information contact:
GROB Systems, Inc.
Machine Tool Division
1070 Navajo Drive
Bluffton, OH 45817
sales@grobgroup.com
www.grobgroup.com/en
< back