
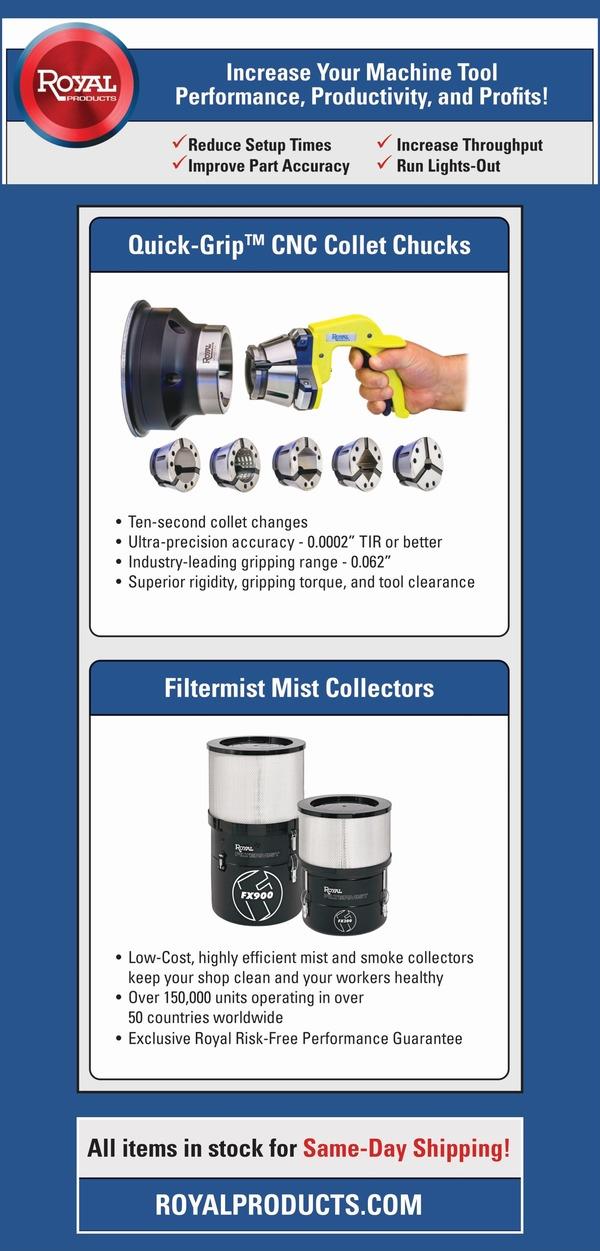
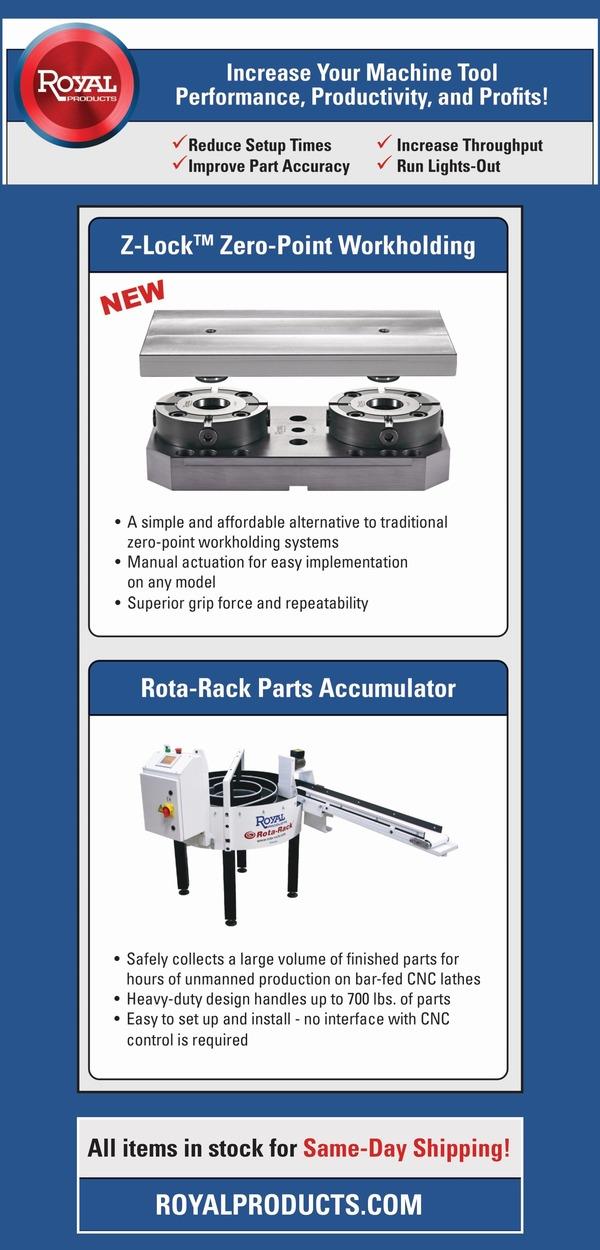

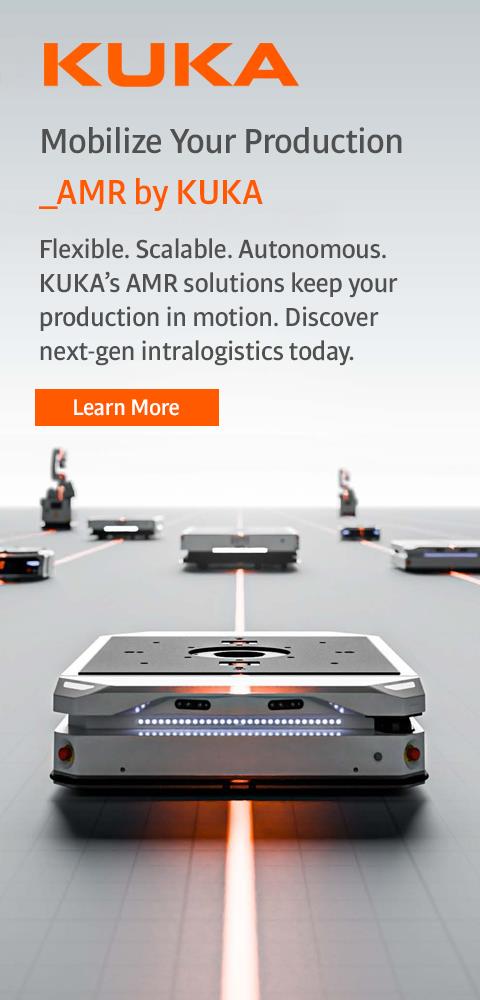
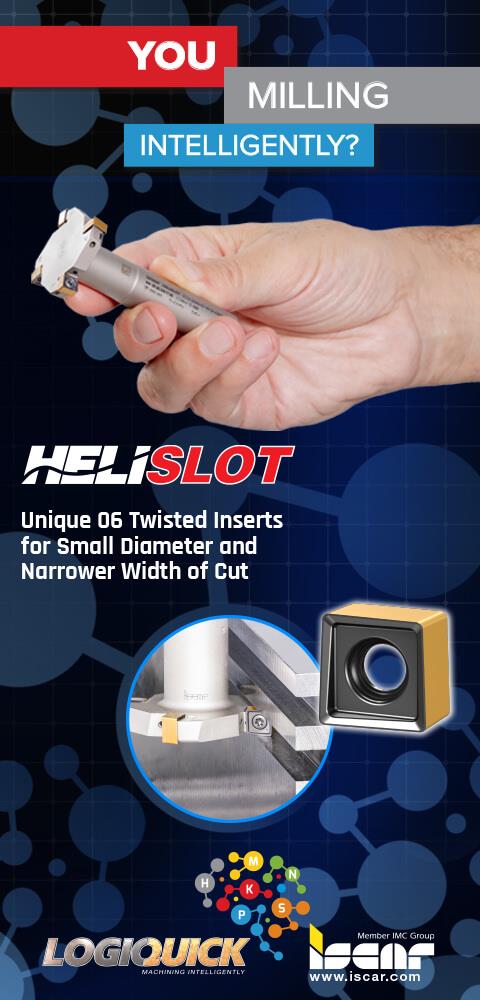
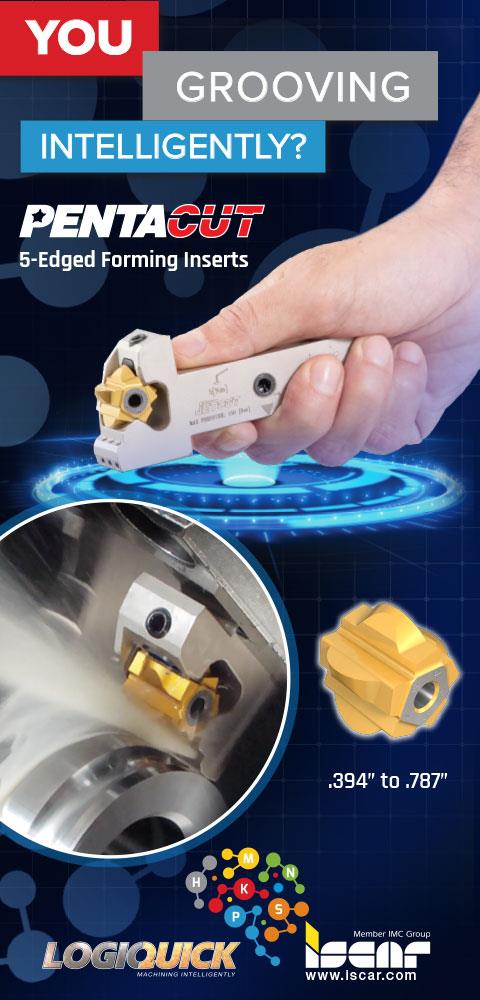
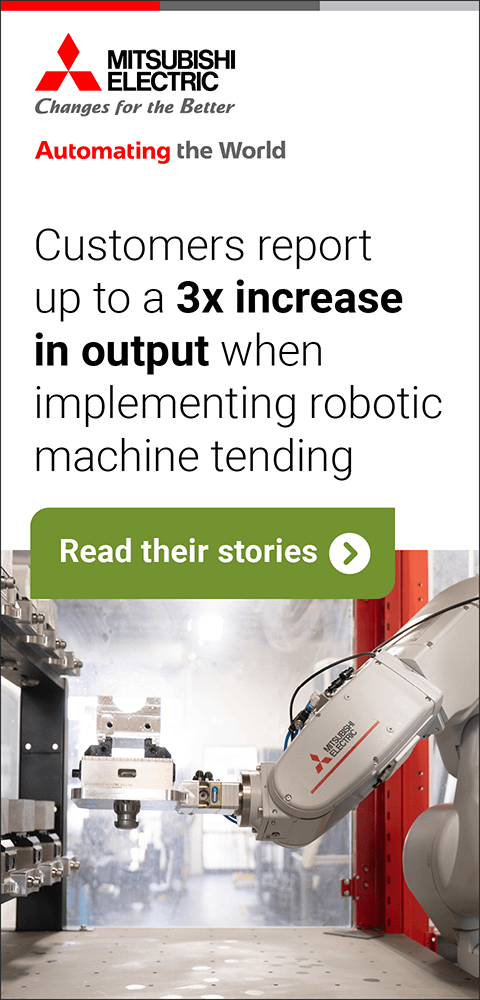
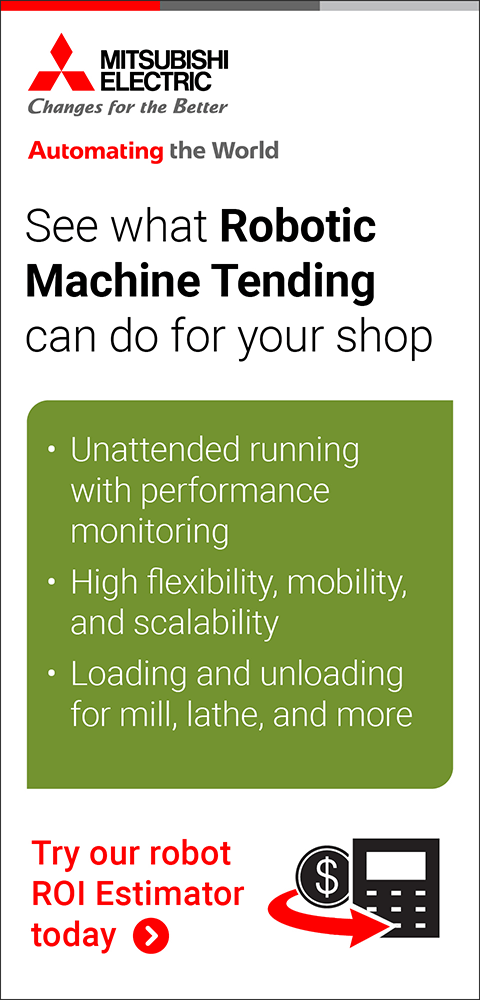
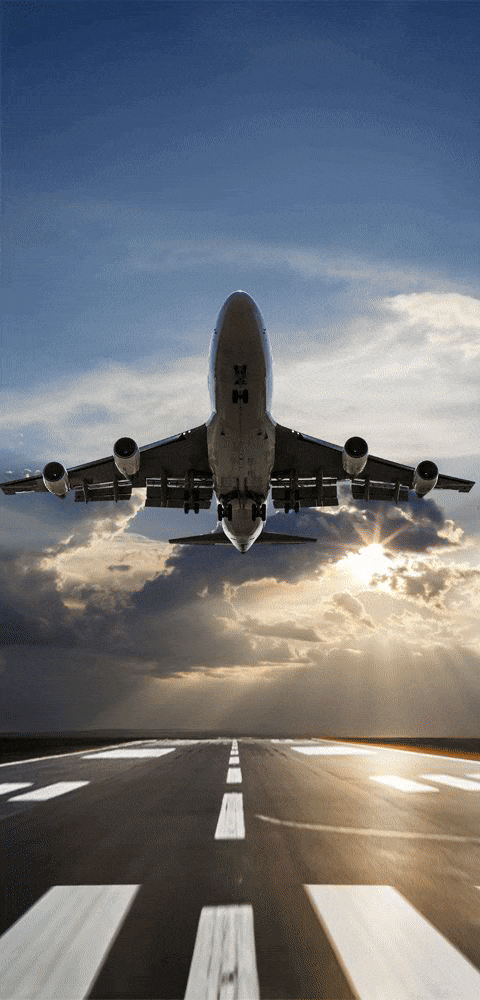
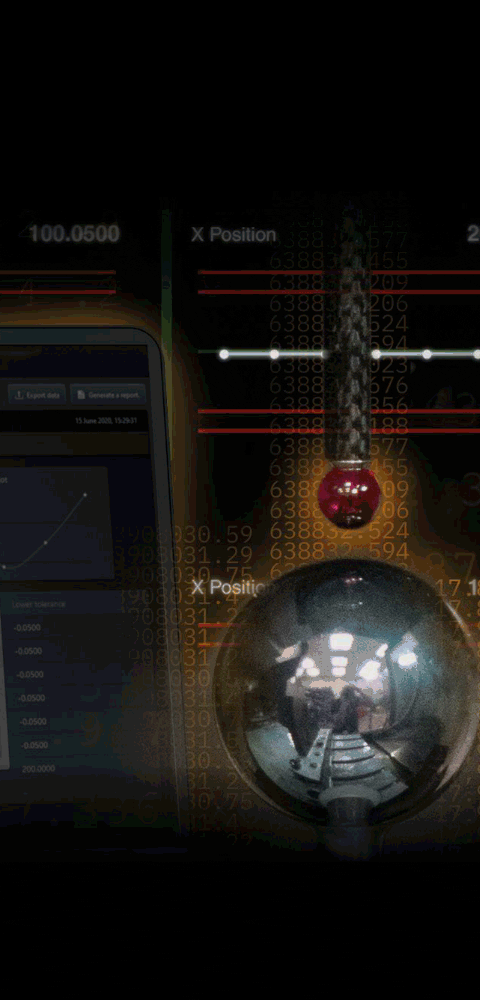
Versatile Robot for Range of Applications
July 1, 2015
Yaskawa Motoman's new MH24 6-axis robot is designed for assembly, dispensing, material handling, machine tending and packaging applications. It features a new curved upper arm that enhances its reach and allows a wider range of applications. This patented double yoke design also offers additional strength if the robot crashes due to a programming error. The MH24 features Sigma-5 motors and Advanced Robot Motion (ARM).
This model has a 1,730 mm horizontal reach and a large work envelope that extends behind the robot, permitting space for robot tool storage or maintenance. The MH24 robot features an increased 24 kg payload, and higher moment and inertia ratings over previous payload class models, enabling it to carry larger and heavier payloads. It has brakes on all axes and can be floor- or wall-mounted for layout flexibility. Additionally, a smaller 12 kg payload model is available (MH12).
Through-arm cable routing provides longer cable life and reduces the risks of snagging or interference. A large 50 mm through-hole in the upper arm provides space to minimize wear and maximize cable life.
The MH24 has a small interference radius that allows the robot to be placed close to other equipment. A mounting surface is provided on the back of the upper arm for junction boxes or pneumatics. Mounting in this area provides a lower profile to the robot and avoids interferences within the cell.
The standard MH24 has an IP67-rated wrist and an IP54 body. A variety of optional features are available. MH24 robots are compatible with the DX200 controller.
The DX200 controller features patented multiple robot control technology to handle multiple tasks and control up to eight robots (72 axes). The DX200 has been designed to improve process capability, reduce energy usage and improve maintainability and safety. An enhanced Functional Safety Unit (FSU) provides control-reliable zone and tool position monitoring, standstill monitoring and speed limiting. This can reduce costs for safeguarding hardware, and it provides new capabilities such as collaborative tasks. It is compliant to ANSI/RIA R15.06-2012 and other relevant ISO and CSA safety standards.
For more information contact:
Yaskawa America, Inc.
Motoman Robotics Division
100 Automation Way
Miamisburg, OH 45342
937-847-6200
www.motoman.com
< back