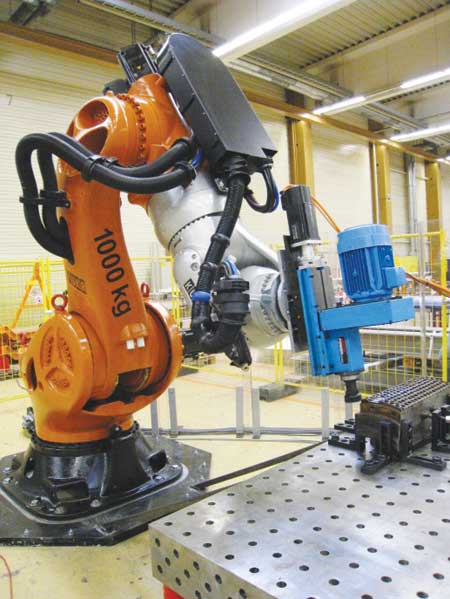
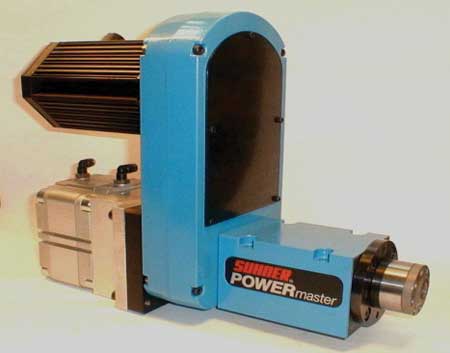
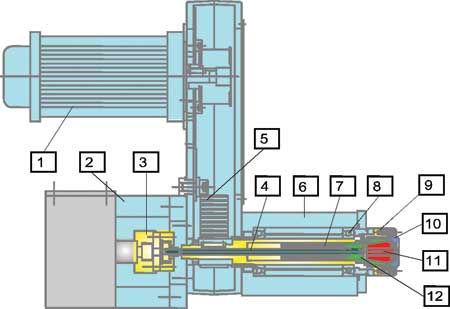
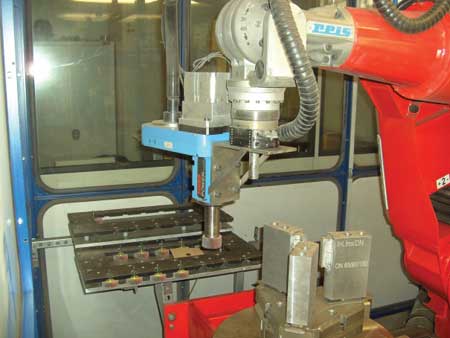
This clamping system is designed for tools with a cylindrical shaft and best applied in grinding and wire brush operations. Here, the BEX 15 WW is tooled with abrasive flap-wheels to clean a welding seam.
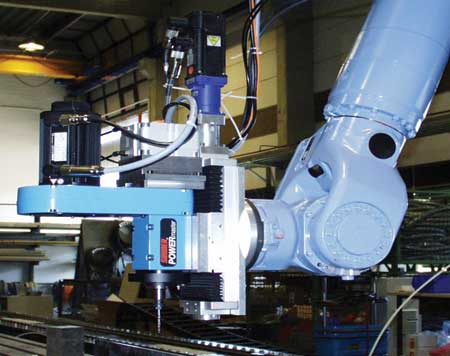
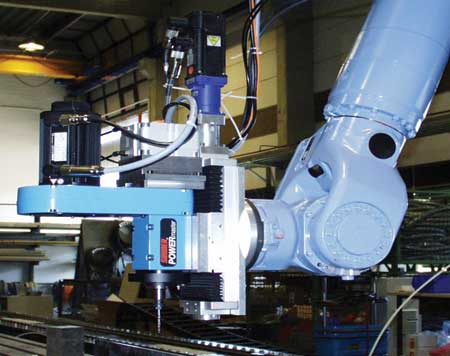
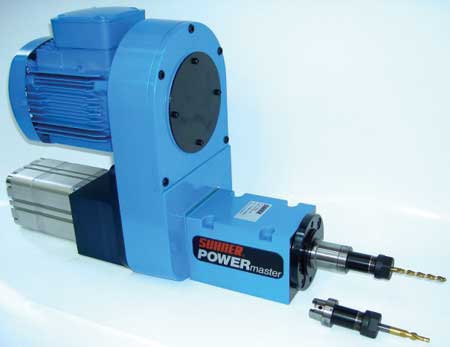
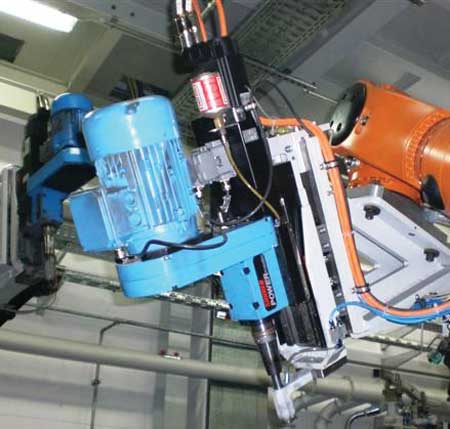
A BEX 15 WW-HSK 32 used in an automotive application for precision drilling.
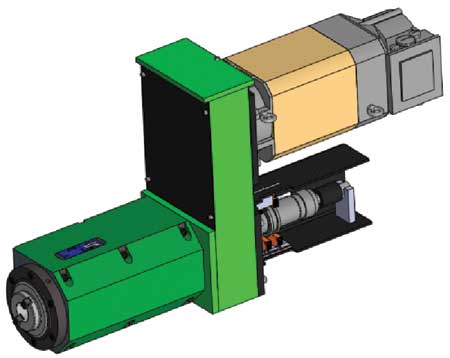
Machining units used with strong arm robots are becoming more popular in drilling, milling, deburring, grinding or brushing operations. SUHNER now has a spindle program specifically made to use with robots and designed to meet demanding application requirements.
Manufacturing cells with robots typically work in a fully automatic mode and require automatic tool changes.
SUHNER offers three types of machining units. Selection ties to drilling performance for mild steel. Models BEX15 WW-ER25 and BEX 15 WW-HSK32 cover up to Ø15 mm. Maximum permissible torque values, depending on unit configuration, range between 12 Nm and 50 Nm. Model MAX 40-CO offers 400 Nm maximum torque, reaching a drilling capacity of Ø 40 mm in mild steel.
BEX 15 WW - ER 25
This model includes a specially designed clamping system. Tool clamping is achieved with ER collets size ER16 or ER25. Collet (Pos. 11) is inside a pressure ring (Pos. 12.). Clamping occurs as the disc-spring-loaded drawbar (Pos. 4) pushes the pressure ring into the spanner ring (Pos. 10). An inline, short-stroke cylinder (Pos. 2) opens the clamp. This type of clamping system transmits up to 12 Nm of torque.
This clamping system is designed for tools with a cylindrical shaft and best applied in grinding and wire brush operations. Here, the BEX 15 WW is tooled with abrasive flap wheels to clean a welding seam. The machining unit can pick up a new tool from a linear tool magazine located towards the rear. In order to control wear and usage, the abrasive tool is measured after each grinding cycle. This information is fed back to the robot control system to make adjustments or to initiate a tool change.
Another application is placement of rivet holes on aircraft parts. Feed motion is done with a CNC-controlled slide to achieve required accuracy. The robot is used primarily for positioning.
According to the company, the key advantage of a collet-type toolholder and clamping system is that exact spindle orientation is never a requirement. This allows the use of standard AC motors; a servo motor is not necessary.
BEX 15 WW - HSK 32
This unit uses a standard BEX 15 machining unit combined with an HSK 32 Superloc clamping system from Roehm. The clamping system is a self-locking design, eliminating the need for a disc spring package. The HSK clamping system opens and closes using an activation rod. An inline short-stroke, pneumatic cylinder with end position control opens and closes the tool clamping mechanism.
With this design, a complete tool change includes both the HSK 32 toolholder and the tool. This allows pre-setting the tools outside of the machine - a critical requirement for high-precision manufacturing operations.
The application of tool clamping systems according to HSK form A and form C requires spindle orientation features with servo motor drives. Maximum torque is limited to 55 Nm.
AC motor drive options without spindle orientation use an HSK form E. Maximum torque is limited to 16 Nm.
BEX 15 WW-HSK32 with a Superloc clamping system can be used for coolant-through-spindle applications.
MAX 40 CO
The largest machining unit for use in robot applications is the MAX 40 CO. This unit comes equipped with an ISO 40 or an optional HSK 63 spindle. Coolant-through-spindle is possible for both toolholder options. Clamping and tool retention are accomplished by a spring-loaded drawbar assembly. Tool release is done with a pneumatic cylinder. Disc spring package including a tool gripper system with an included mechanical ratio can develop a tool retention force up to 12 kN. Process capability can be monitored using four proximity switches controlling the following functions:
- Tool clamped
- Tool released
- Home position w/o tool
- Home position w/o tool and no rotation (tool change position).
According to the company, the best choice for a spindle drive on a MAX 40 CO is a servo motor because automatic tool change requires a defined spindle orientation point.
"Up to 400 Nm torque at the spindle allows substantial drilling and milling operations," said a company spokesperson. "This also demands a strong robot. Clamped workpieces of alloy steel can be milled completely and followed by a drilling operation of Ø21 mm diameter."
For more information contact:
SUHNER Industrial Products Corp.
Hwy. 411 S. at Suhner Drive
P.O. Box 1234
Rome, GA 30162-1234
706-235-8046
automation.usa@suhner.com
www.suhner.com