
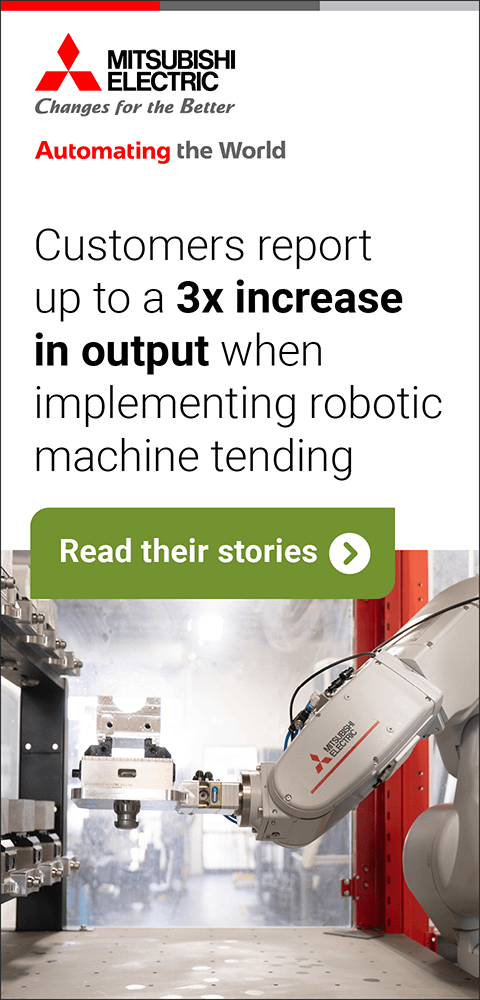
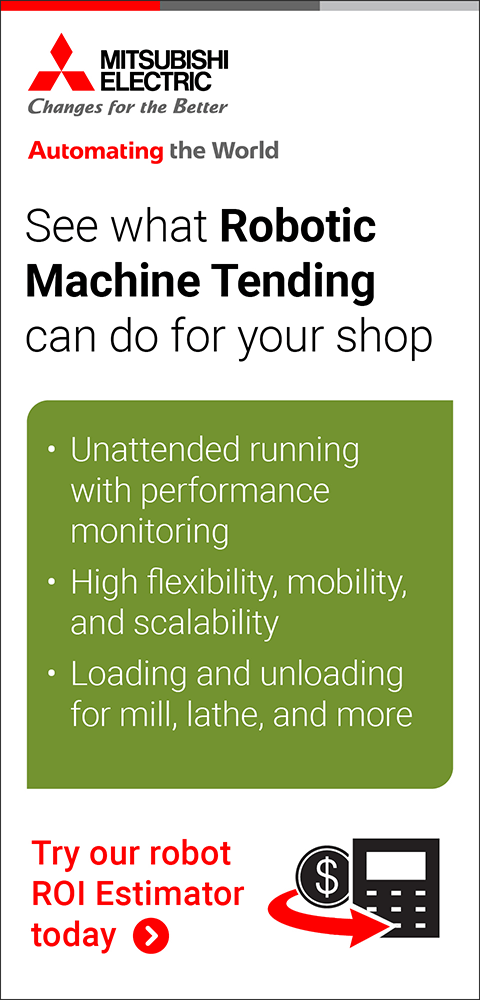
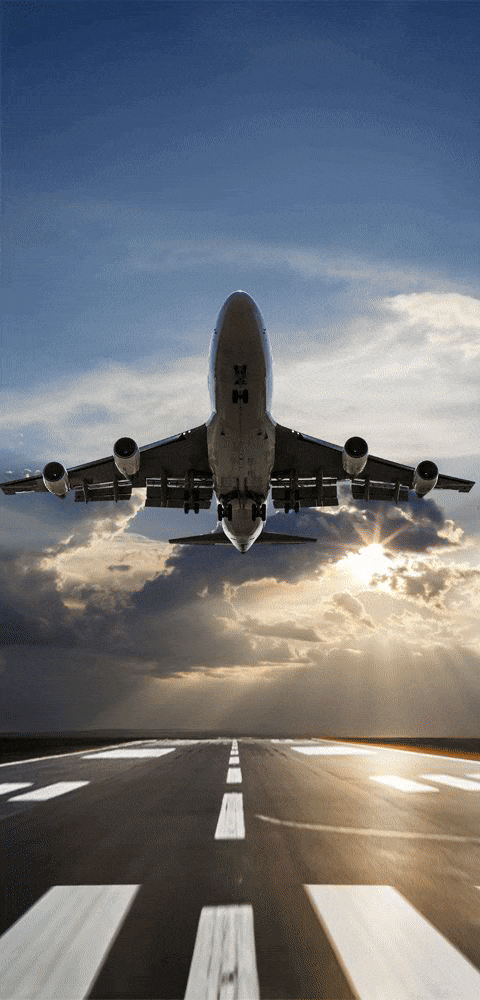
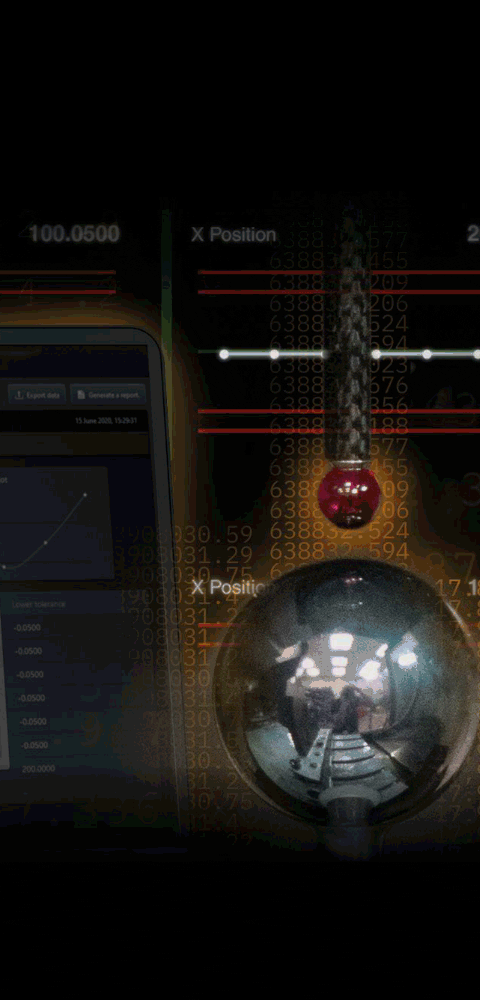
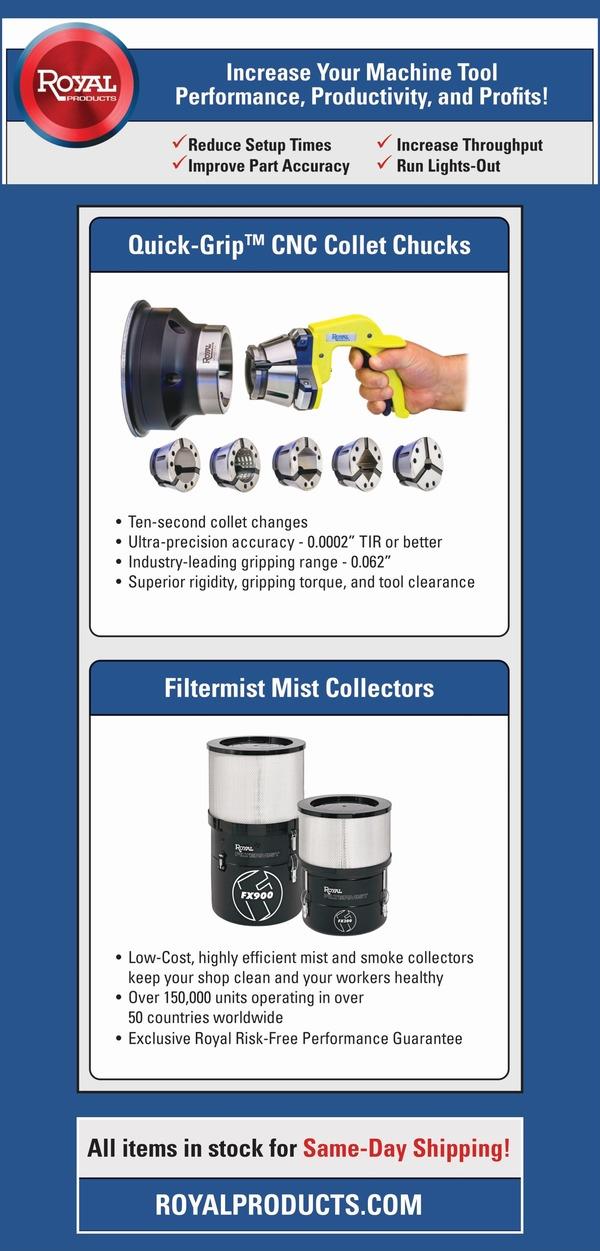
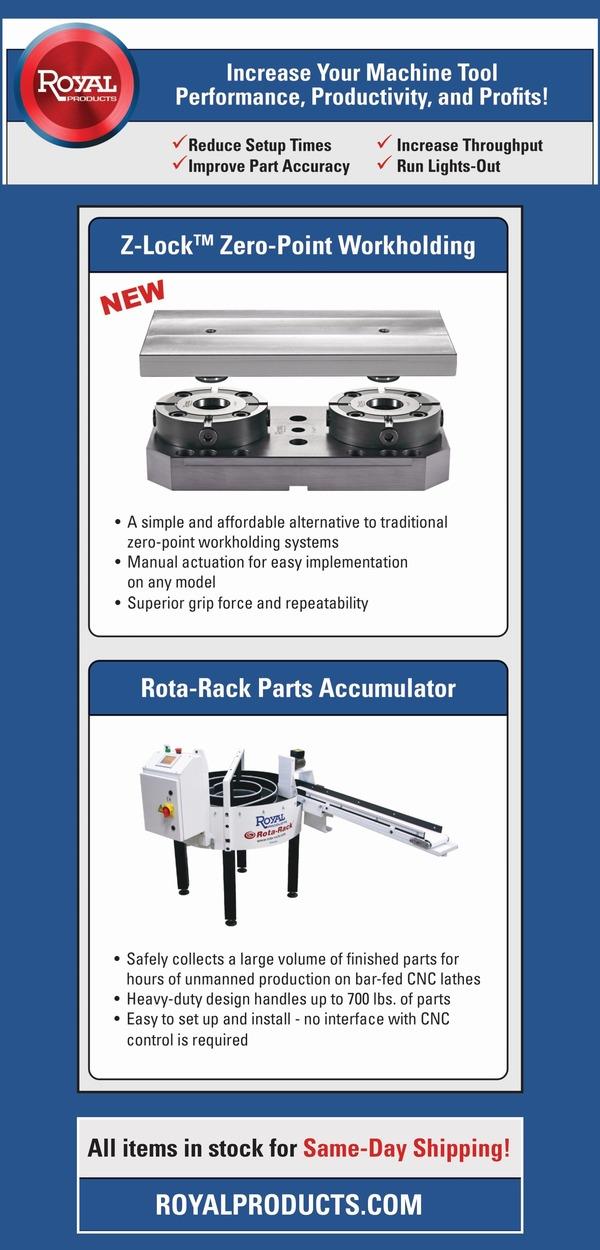

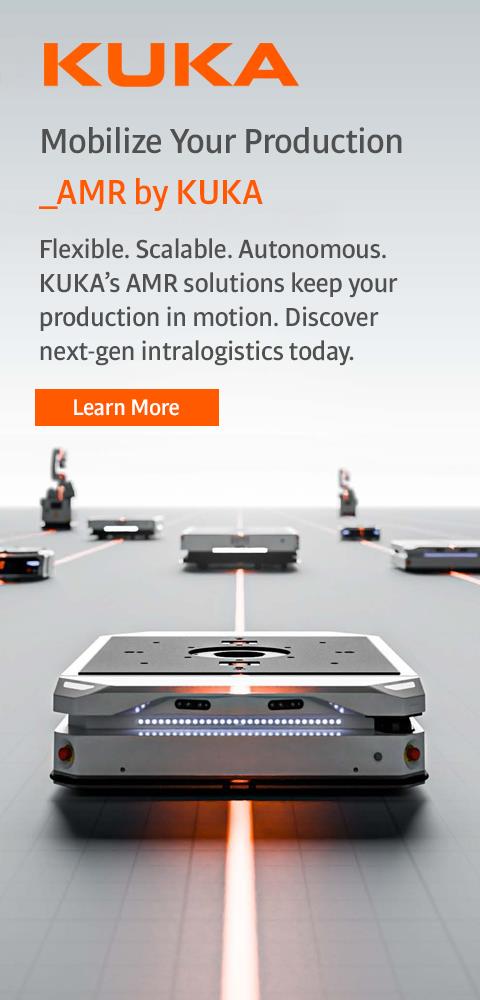
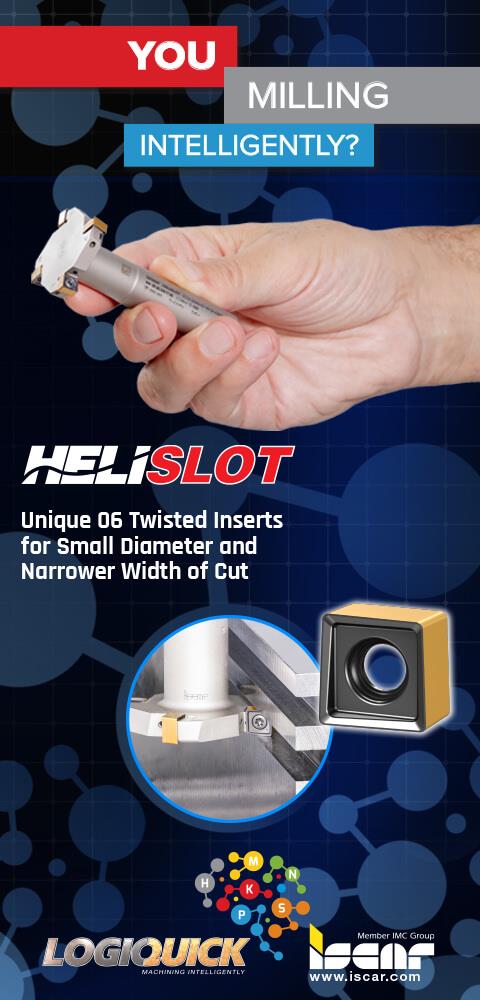
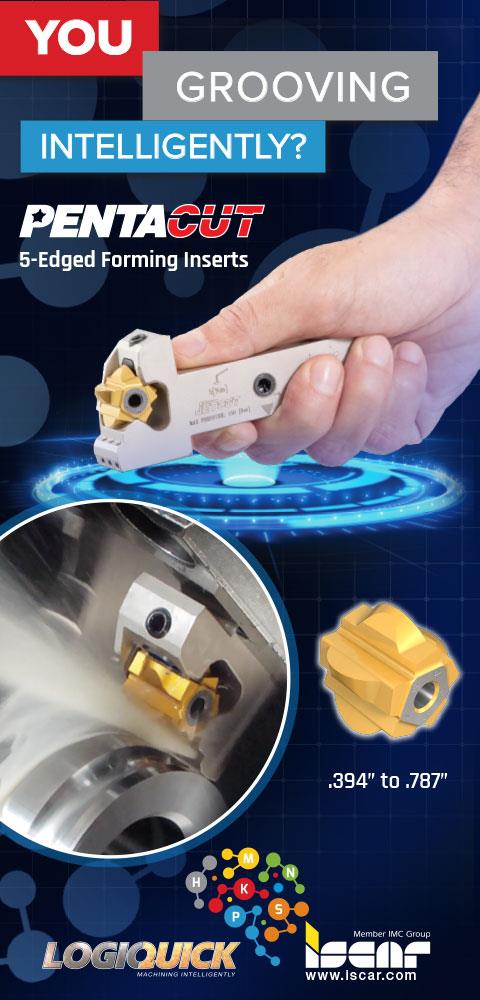
Oil Contamination Eliminated by Oil/Water Separator
June 1, 2014
A frequent problem encountered in parts wash lines is the buildup of an oil layer on the surface of the rinse tank. When the rinsed parts are raised out of the tank, the oil layer recontaminates the parts. The problem can be solved by continuously removing the oil layer from the surface of the rinse tank.
In principle, removing oil from the surface of the rinse tank is similar to separating tramp oil from the surface of coolant in machine tool sumps, an application for which Keller Products Inc. has reportedly supplied several thousand units. In practice, however, the parts wash application has two additional requirements:
- The temperature of the rinse water is typically about 160 °F
- The rinse water usually contains a low concentration of alkaline cleaner.
The TKO-1OHT, introduced by Keller, functions the same as the other Keller TKO products but is resistant to the special rinse water operating conditions.
A self-priming air operated diaphragm pump on the TKO-1OHT pulls oily rinse water from the surface of the rinse tank through an inlet device and then through a filter to remove any floating solids. The filtered oil/water mixture is then pumped through the patented Keller all-plastic separator element immersed in a separator tank. The oil-free water returns continuously to the rinse water tank at a high flow rate, 120 gallons per hour. The oil layer collects on the top of the separator tank and is occasionally drained into a waste oil container by opening the oil drain valve. No other operator attention is required. The TKO-10HT is shipped from stock by UPS.
For more information contact:
Jonathan Strauss, Sales Manager
Keller Products, Inc.
6 Ledgerock Way, Unit #6
Acton, MA 01720
800-352-8422 / 978-264-1911
info@kellerfilters.com
www.kellerfilters.com
< back