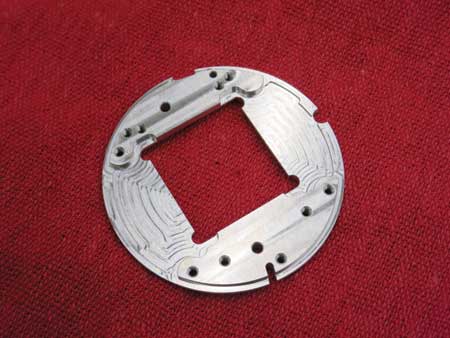
Precision machined component for defense industry.
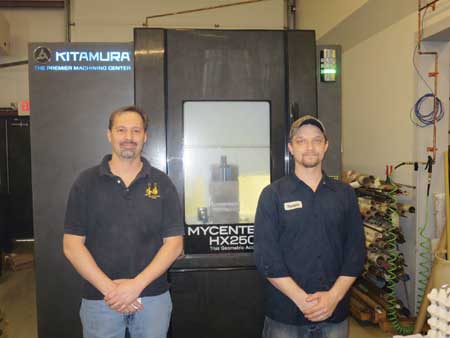
(l-r) Dan Labonville, President and Dwayne Dunton, Crucial Component Machining LLC, Concord, NH, with the Kitamura Mycenter-HX250G horizontal machining center that has a super compact, small footprint.
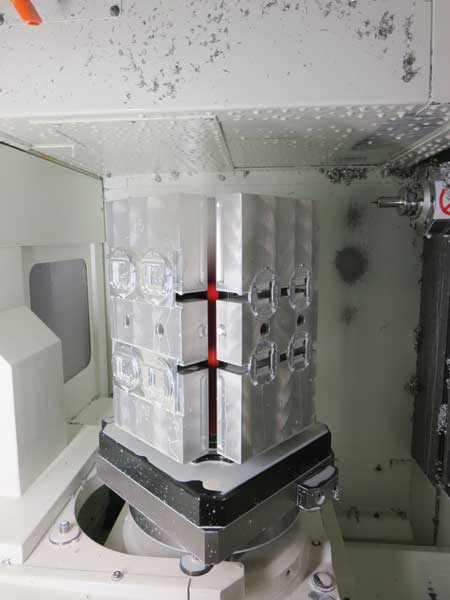
Internal work envelope of the Mycenter-HX250G, smart fixturing and multi-part set-up.
Crucial Component Machining LLC was awarded a contract to produce 10,000 tight tolerance parts for a defense contractor. The component is made of 6061 aluminum, has flatness and parallelism requirements of .001" and .0005" respectively and a surface finish max of 32 Ra. The parts require high levels of accuracy, which resulted in the need for new CNC equipment to meet demand and production requirements.
"We decided to go with one of the bigger manufacturers known for accurate, reliable and quality machines that would run continually to keep production flowing," said Dan Labonville, Owner, Crucial Component Machining LLC. "Our first vertical machine that we selected had unsatisfactory results. Right away we noticed an issue with the surface finish on the floors of the part. There were a series of rings left along the tool path. The smaller the tool the worse the rings were. It was not just visual; you could feel the roughness with a fingernail."
After several weeks of the dealer and manufacturer trying to fix the problem the machine was removed and replaced with a machine from a different manufacturer. The second machine that was purchased had the exact same finish problem. Neither of the machines could hold the accuracies or give the finishes required.
"After the second machine was removed I had a visit from Paul Karpinski with Packard Machinery Company, Inc. He asked if I would consider a horizontal machining center since my parts were relatively small, about 2.5 inches in diameter," said Labonville. "Karpinski gave me a quote for a Kitamura Mycenter-HX250G, which surprisingly, was not much more than the cost of either of the two vertical machining centers I had already purchased. We ran a test using 6061 aluminum as the component material and the part came out great."
The Kitamura Mycenter-HX250G has a table size of 10" x 10" (254 x 254 mm) and a 15 HP, 15,000 RPM, dual contact through coolant spindle with 51.6 ft. lbs. of max torque. The HX250G comes standard with a two-station, 180° rotating pallet change system and a full 4th axis rotary table for multi-part tombstone fixturing. The Mycenter-HX250G can handle four-sided tombstones up to 15.8" high and 13.8" in diameter, weighing up to 220 lbs. The HX250G can also machine multiple workpieces while another tombstone is being unloaded and reloaded with new parts to be machined. A Blum tool probe was also added to speed up set-ups and tool replacements.
"Our basic philosophy is to produce parts that are as close to perfect as possible," said Labonville. "With the Kitamura Mycenter-HX250G the surface finish is far superior to the prior machines. We were able to cut cycle time from 15 minutes each to under 10 minutes while maintaining both finish and tolerance requirements. Also, the small footprint of the HX250G makes it very beneficial due to the size of our shop."
Crucial Component Machining LLC offers CNC machining, Swiss screw machining and CNC turn mill machining with sub-spindle and Y-axis milling. The company uses SolidWorks and ESPRIT CAM for programming and Chick Workholding vises for part fixturing. Typical materials machined at Crucial Component Machining LLC include 6061 aluminum, stainless steel, titanium, molybdenum and plastics. Dan Labonville started Crucial Component Machining LLC in 2007.
For more information contact:
Dan Labonville, Owner
Crucial Component Machining LLC
27 Industrial Park Drive, Unit 5
Concord, NH 03301
603-223-0012
dan-ccm@comcast.net
Kitamura Machinery of USA Inc.
78 E. Century Drive
Wheeling, IL 60090
847-520-7755
info@kitamura-machinery.com
www.kitamura-machinery.com
(For NE edition only)
Wendell Packard III
Packard Machinery Co., Inc.
504 Groton Road
P.O. Box 1618
Westford, MA 01886
978-692-3100
www.packardmachinery.com