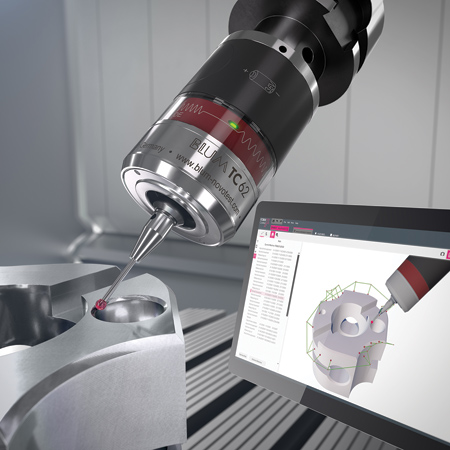
With the FormControl X measurement software from BLUM, machining processes can be automated quickly and reliably, which is reflected 1:1 in productivity and the quality of the manufactured workpieces.
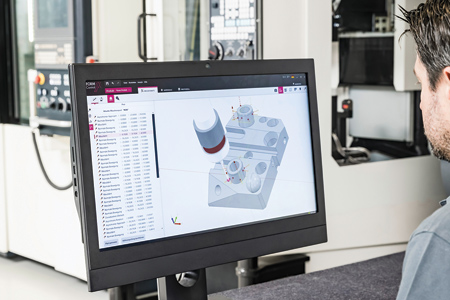
With FormControl X, measuring programs are created on a PC at the click of a mouse.
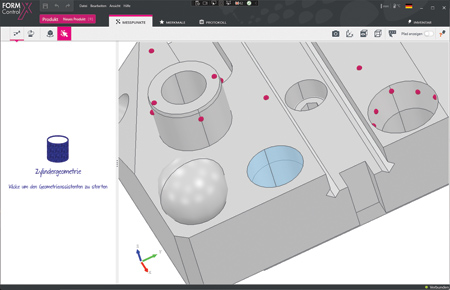
The creation of measuring programs in FormControl X is intuitive with the help of the context wizard.
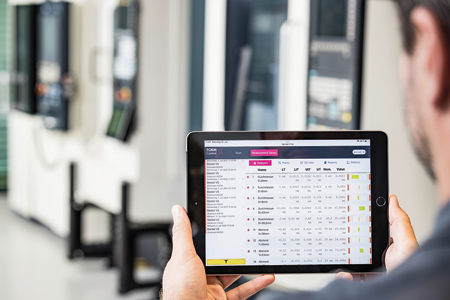
The measurement results can be conveniently displayed in the web browser of any end device.
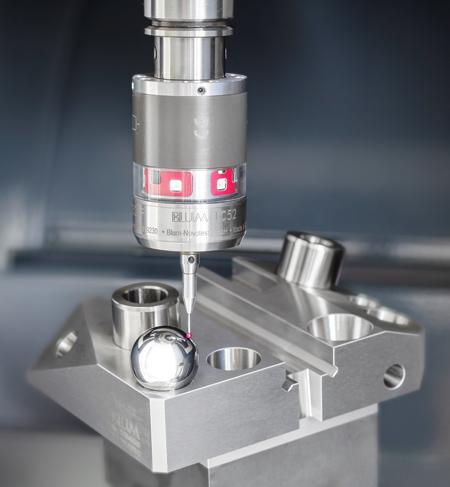
Processes in both individual and series production can be automated with FormControl X from BLUM.
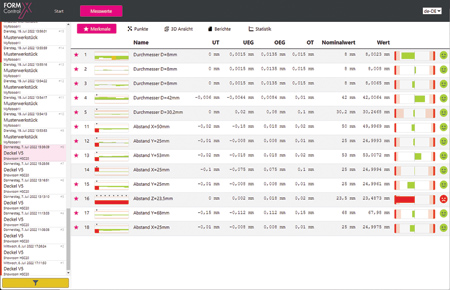
With FormControl X, a closed control loop (SPC) where threshold values for process adjustments can be defined can be made a reality with little effort.
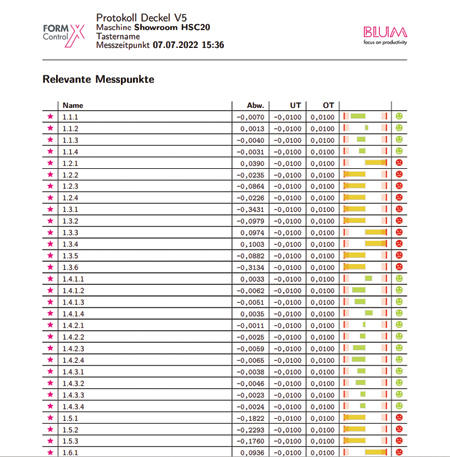
The protocols resulting from the measurements can be adapted very easily and extensively, tolerance limits can be displayed as a number or image, red/green coloring can be defined and much more.
Blum-Novotest recently showcased the FormControl X for reliable process automation.
"The foundation of intelligent automation solutions is process data that is evaluated live or very quickly and serves as a control variable for process optimization. The automation reacts to the measurement result and readjusts to ensure that the process always remains within the predefined limits," explained Wolfgang Reiser, Technology Division Manager at Blum-Novotest. "With the new FormControl X software, Blum-Novotest is presenting a solution for machining centers that can be used to gain much more knowledge by continuously measuring workpieces in the machining process."
"While the previous FormControl version (without the 'X') was based on a scenario in which a machine operator works at a machine with the laptop and processes the measurements at the same time, the trend today is moving toward automating such processes, meaning this 1:1 relationship is now fairly rare," said a company spokesperson. "Genuine automation of workpiece measurement also opens up completely new areas of application. That is why the goal with FormControl X was to enable real measurement automation on the basis of a modern client-server architecture-this means moving away from pure logging and towards process integration and automation with the help of the measurement data collected by the software."
In this way, workpieces can be measured directly after each machining operation, and the results serve as a correction value and basis for optimization for the next component. To do so, the user defines intervention limits when creating the project, which the software uses to make corresponding corrections. This makes it possible to compensate for tool wear, among other things. FormControl X works in line with the trend that bore holes, for example, get smaller and smaller as the corresponding tool wears out, and can counteract this process. This widens the focus of the software: while FormControl was focused on higher-priced parts in individual production, FormControl X also targets small, medium and large series production.
Evaluated data and results are accessible in a web interface using various end devices. The server communicates with the machines on which measurements are taken, so an operator can run measurement projects on many different machines and have them evaluated automatically. Complex measuring routines such as the alignment function can be used to adapt the reference points of the machining program to the position as well as the shape of the workpiece to ensure that machining runs optimally. Another innovation in FormControl X is the management of measuring devices and machines. Since it is now centrally located on the server, the data is available for all machines. Definition of the measurement is also simple and intuitive due to a context wizard.
FormControl X now also makes it possible to create and evaluate data series over time. What with FormControl ended in a protocol of a single machining operation can now be used to evaluate entire machining series. This offers the operator completely new ways to gain knowledge. The protocols resulting from the measurements can also be adapted easily and extensively, tolerance limits can be displayed as a number or image, red/green coloring can be defined and much more.
FormControl X is another step on the path to integrating measurement results from machine tools into company processes and making them usable for Industry 4.0 applications. "With a networked client-server architecture, the reusability of measurements and the interaction with the machine, the new version of the software solution offers many new options for keeping processes transparent and optimizing them on an ongoing basis," said Reiser. "However, perhaps the most important aspect for many users will be that with FormControl X, the machining process can be automated quickly and reliably, which is reflected 1:1 in productivity and in the quality of the manufactured workpiece."
For more information contact:
Blum-Novotest, Inc.
4144 Olympic Blvd.
Erlanger, KY 41018
859-344-6789
info@blum-novotest.us
www.blum-novotest.com/us