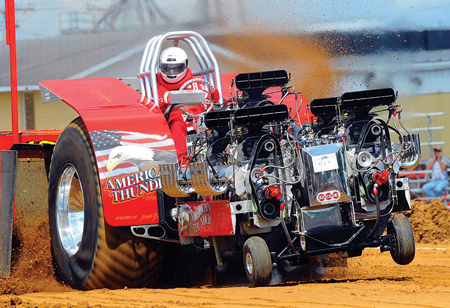
Fowler Performance designs, services and upgrades all major race and street supercharger brands in addition to designing and manufacturing superchargers.
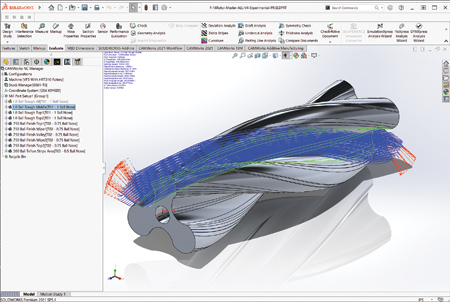
With HCL CAMWorks, Fowler Performance has machined more complex parts with tighter tolerances and smooth finishes.
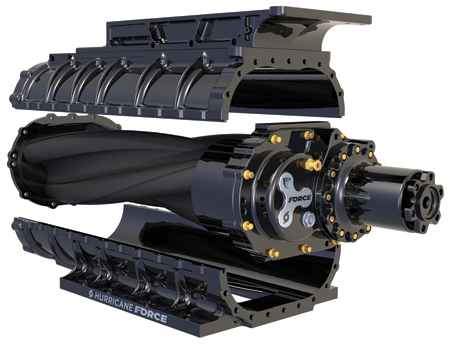
With seamless integration between CAD and CAM software, changes to product design is faster and more efficient-allowing time for product line expansion.
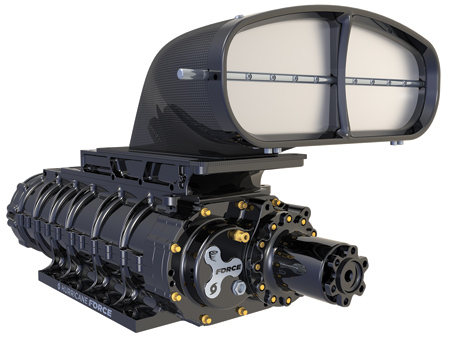
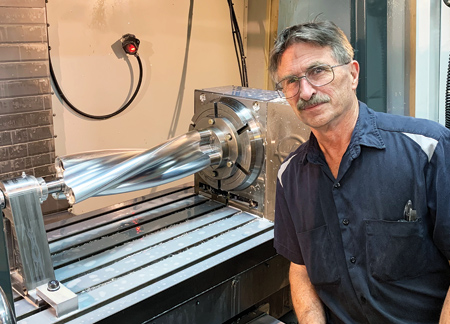
Jeff Fowler, owner and CEO of Fowler Performance
Fowler Performance builds, services and manufacturers components for automotive performance superchargers used on high-performance fuel engines. The company needed a solution to handle more complex parts requiring 4-axis machining but had challenges finding the right CAM software solution. Fowler saw that HCL CAMWorks could support 4-axis machining while integrating with its SOLIDWORKS software.
Fowler Performance began rebuilding and enhancing modern automotive performance superchargers in 1979 and is now one of the few supercharger manufacturing and service companies east of the Mississippi River. Superchargers are used on high-performance fuel engines to provide additional power and speed, and are used for blown alcohol engines, dragsters, funny cars, tractor pulling, land-speed racing and hot rods. Fowler Performance designs, services and upgrades all of the major race and street supercharger brands, including Kobelco, SSI, PSI, BDS, Mooneyham, Littlefield, Weiand and GM. In addition to developing and producing superchargers, Fowler manufacturers and supplies all of the major components required to set up and service superchargers.
In 2011, Fowler acquired the entire Kobelco K-11 "Superman" supercharger line-including full design, manufacturing and distribution rights-and reintroduced it as the Fowler F-11 line. All Fowler Performance F-11 superchargers are designed, machined, assembled and tested in the firm's state-of-the-art production facility in Columbus, OH. Kobelco had a reputation as a premium supercharger brand designed for serious competition, and Fowler Performance raised the stakes on what a high-performance supercharger can do with the introduction of the F-11 Plus, F-11 Xtreme and the latest F-12 Hurricane Force lines of superchargers.
Until 2020, Fowler Performance used the combination of SOLIDWORKS CAD design and an industry CAM milling software to machine supercharger components. "However, as our R&D efforts progressed, we reached a point where that solution could no longer handle more complex parts that required live 4-axis machining," said owner and CEO Jeff Fowler. "While the capabilities of our CAM system could handle roughly 95% of our more simplistic parts, we needed to acquire 4-axis capabilities to machine parts for our newer, more complex products."
"When our CAM system was acquired by another company, we were told that we would have to leave SOLIDWORKS and invest in the provider's alternate CAD program in order to get the live 4-axis capabilities that we needed," Fowler added. "We have been using SOLIDWORKS for 10 years and did not want to move to a new platform, and the move was very expensive with no value added. We hit the end of the road with them, so we decided to investigate other options."
Fowler worked with Dale Hays of SINNOVATE, a long-term friend and design consultant, to help with the search, which led them to a meeting with Jeff Trevorrow of Columbus Advanced Manufacturing Systems, or CAMS (recently acquired by Hawk Ridge Systems), a SOLIDWORKS and CAMWorks reseller. "CAMS has a heavy manufacturing background and more manufacturing expertise than the distributor that we had been dealing with," Fowler recalled. "Hays brought an example of the rotor that we needed to make and provided the tolerances and finish requirements and asked them if they could make the part in CAMWorks and produce it on our HAAS mill. They believed it could be done and agreed to support us on creating a prototype in CAMWorks as a proof of concept. After just a few initial prototype parts, we proved we could produce our rotors, and we were off and running with CAMWorks."
Fowler Performance implemented CAMWorks Professional multiaxis milling software to support 4-axis machining. One of the reasons Fowler chose CAMWorks was to take advantage of the solution's seamless integration with SOLIDWORKS 3D modeling software in support of Fowler's ongoing R&D effort so it can continue to accelerate the production of complex parts and boost the company's productivity overall.
More Complex Parts with Tighter Tolerances, Smoother Finishes
Since implementing CAMWorks Professional multiaxis milling software, Fowler Performance has consistently been able to machine more complex parts with tighter tolerances and smoother finishes. "Some supercharger components move at a speed of 14,000 to 16,000 RPM and require tolerances within a couple thousandths of an inch with ultra-smooth finishes," Hays explained. "CAMWorks gives us the flexibility to make any changes that we need to get the tolerances and finishes right."
"It is important that we have a well-integrated product because associativity between our CAD and CAM solutions is critical for machining complex parts," Fowler stressed. "Unlike a job shop where the primary focus is on keeping the spindles turning, we are more focused on pushing supercharger designs and machining parts that are difficult to make. We are not looking for efficiency-the rotor that served as a proof of concept for CAMWorks takes 5-1/2 hours to machine. What we need is the ability to make parts that are hard to machine by providing the flexibility to modify and play with the design, which the associativity between CAMWorks and SOLIDWORKS makes very efficient."
Machining Intelligent Parts with Configurations
In addition to providing 4-axis machining capabilities, the move to CAMWorks software has enabled Fowler Performance to further automate machining operations by imbuing intelligence within part designs using SOLIDWORKS design configuration capabilities. "When I create a part, I am including intelligence within the part through the use of design tables and configurations," Hays said. "For example, on the rotor part design, I can go into configurations and change one variable in the design, such as a left-hand or right-hand twist or small, medium or large rotors for different types of superchargers. Because the combination of SOLIDWORKS and CAMWorks enables us to invest in `intelligent' design, we include intelligence in the original part design. Instead of having to make changes to six different parts on 20 different rotors prior to machining, we can use design configurations to generate the G-code for all the different configurations at the click of a button, providing a very efficient method for maintaining very complex parts."
Investing in 4-Axis Machining to Spur High-End Supercharger Development
Another reason why Fowler Performance made the decision to invest in CAMWorks is because the 4-axis solution complements the company's new product development goals. "As a supercharger manufacturer, we are judged on our knowledge and the performance of our products, which is why we are looking to expand our product line and infuse it with imagination and creativity," Fowler said. "Although our products have historically been high-end, there are still ideas that I have had over the past 20 years that I just could not figure out how to make. With our investment in CAMWorks, we are making an investment in our future by providing us with the design and production tools to take product performance to the next level. With CAMWorks, we are confident that we will develop, machine and bring to market the next generation of fuel engine superchargers, providing levels of performance the likes of which the market has never seen."
For more information contact:
Fowler Performance
3021 Switzer Ave.
Columbus, OH 43219
www.fowlerperformance.com
HCL Americas
15974 N 77th Street #103
Scottsdale, AZ 85260
480-367-0132
camworks.inquiries@hcl.com
www.camworks.com