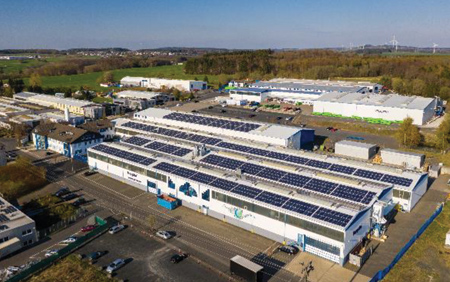
Vecoplan supplies machine and plant technology for the economical processing of residual materials and waste for the purposes of material and thermal recycling.
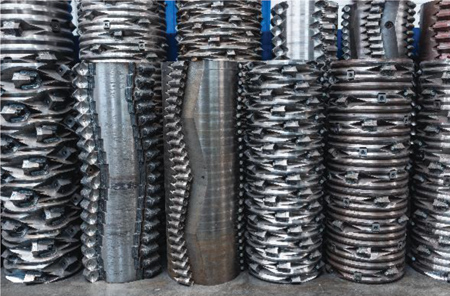
Wide variety of rotors for shredders: machining times range from 3 to 19 hours.
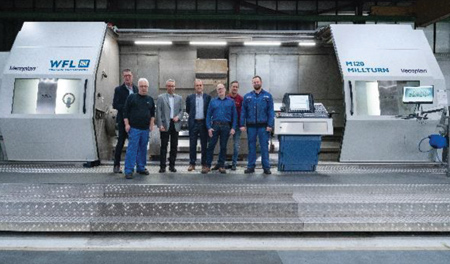
(l-r) Andreas Rose, Regional Sales Manager, WFL; Klaus Weitershagen, Vecoplan; Thomas Kauls, Kauls GmbH; Reinhold Wieland, Regional Sales Manager, WFL; Martin Selbach, Head of Production, Vecoplan; Daniel Dittmann, Head of Machining, Vecoplan; Nico Hammer, Machine Operator, Vecoplan
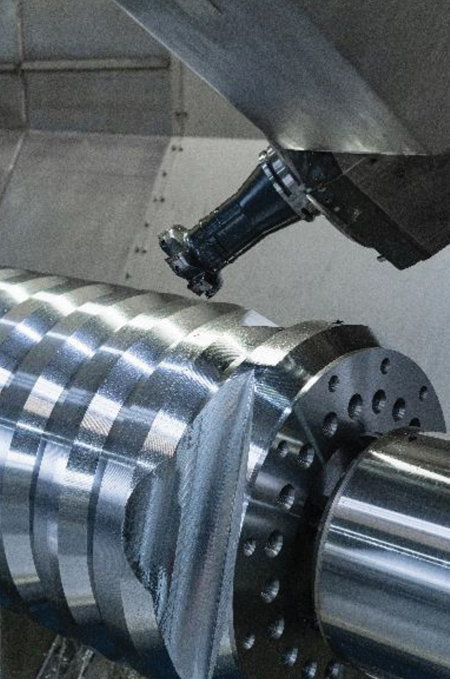
Reduced wait times and clamping: the large time advantage brought a 50% saving on machining time for a typical workpiece.
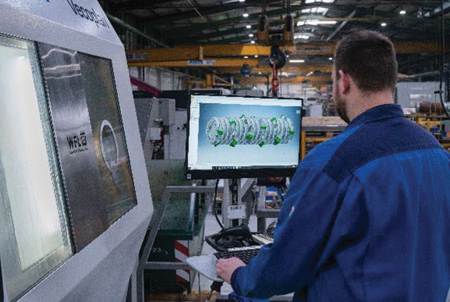
Pilot project: a monitor on the M120 Millturn provides access to drawings, 3D models, machining times and much more.
Famous for its spas and health tourism, the town of Bad Marienberg is located in the German state of Rhineland-Palatinate. The region has a long history of promoting entrepreneurial activity.
Vecoplan was founded in 1969. The company's activities are focused on the processing of residual materials and waste for material and thermal recycling. Various systems for shredding, conveying, storage and separation have been developed in support of these activities.
The Vecoplan product portfolio comprises a range of machines and systems for different preparation processes. This makes it possible to cater to a broad range of industries, applications and companies-from craftsmen and SMEs through to the major players on the market. Customers include recycling companies, biomass and thermal power stations, companies from the primary and secondary wood industries, cement manufacturers, plastics processors and many more.
Vecoplan provides its customers with end-to-end support: from planning to production, delivery, installation and commissioning, right through to maintenance of the entire plant. As a result, the company delivers the highest possible quality standards to meet customer demands across the globe, be it an individual machine, a complete plant or anything in between. Excellent service, including the provision of original spare and wearing parts as well as a broad range of additional after-sales services, are also part of its comprehensive customer care.
Vecoplan now offers the networking of machines and plants as an extra source of added value. This new range of digital services is up and running under the name VSC-Vecoplan Smart Center-and comprises a wide range of features, from remote access and data analysis, right through to live camera monitoring via smartphone.
One thing that sets Vecoplan apart is its technology center. More than 3,200 tests and counting have been documented in the database. A broad range of machine configurations that are matched to the needs of the customer makes it possible to process a vast array of materials. Customers and interested parties value the shredding tests because it gives them the opportunity to see for themselves just what the machine can do.
Machining Time Cut in Half
Rotors of various sizes are manufactured at Vecoplan for use in shredding technology. This is where the new WFL machine comes in. Daniel Dittmann, Head of Machining, explained the manufacturing process: "Before we got the M120 Millturn from WFL, all operations were completed and all workpieces manufactured on two machines: first on a simple turning machine and then the turned shaft was moved to a milling machine. The benefit is that we now have reduced wait times between the individual resources and do not need to clamp as often. This has saved us a huge amount of time. We can now achieve a 50% saving on pure machining time for a typical acceptance workpiece."
Head of Production Martin Selbach added: "We were experiencing a major bottleneck in this respect, and our delivery times would definitely have suffered if we had not invested in the new machine. The WFL machine allowed us to eliminate this bottleneck. The M120 Millturn is now enabling much faster availability of rotors, which we manufacture on an order-specific basis."
The average machining time for large rotors is approximately 18 hours. "We have a really wide range of rotors here-from small to large-which is why machining times range from three to 18 or 19 hours," explained Dittmann. Generally speaking, the same component is manufactured in different sizes and versions, depending on the intended application for the rotor.
As many as 95% of rotors are manufactured on an order-specific basis. "There are only very few rotor types-mostly smaller ones-that we can manufacture as stock goods. The challenge for us is that the majority of rotors have customer-specific features," said Dittmann.
Easy Programming on the Machine
The M120 Millturn is equipped with the programming editor Millturn PRO. This allows programming to be performed directly on the machine. "The development team is currently in the process of standardizing certain components in order to enable us to increase batch sizes and make production more efficient," said Selbach. "For instance, we manufactured around 150 different rotors on the machine in 2021, and we, of course, had to program them too. Our aim is to simplify this process in coordination with the design department."
Selbach continued: "When two of our employees received training from WFL, we all learned a lot and identified a number of new possibilities. For operators, this obviously demands a certain amount of effort to begin with until they know what they are doing with the different software functions. Integrated thinking is required to realize the machine's full potential. It is easier said than done at first."
Robust and Accessible
Hundreds of shredders are built at Vecoplan every year. "Of these, 25% are machines with larger rotors of up to 3,200 mm, and the rest are smaller machines. The small rotors in question here have lengths between 600 mm and 1,400 mm. With the exception of conveyor and plant technology, the components that we manufacture on the M120 are used in all shredders, be it for applications in the fields of wood/biomass or waste and recycling," said Selbach.
Selbach explained Vecoplan's decision to ultimately opt for a Millturn from WFL: "We were familiar with WFL and knew that they were technology leaders, especially in complete machining. We of course looked at a range of machine manufacturers, but ultimately all the manufacturers within the scope or of the scale that we were considering at that time backed out. Others were unable to provide a machine that could meet our requirements in terms of the loads that may arise."
Dittmann agreed with his colleague: "For us, stability, the maximum clamping weight and of course the drive power with the weights were the most important factors in favor of a Millturn from WFL. The performance live on the machine during milling was impressive too. This tipped the scales and won our trust completely."
Selbach added: "We had a shaft with a diameter of 700 mm. No other raw material was available, so we had to turn down the shaft across the entire diameter. We went all out in terms of the depth that the indexable insert could manage and the drive power of the axis was around 55%, which was very impressive."
The accessibility to the machine also impressed: "If you compare the Millturn with other machines that we use, the main difference is that the maintenance access points, maintenance doors and general accessibility to the machine-and that goes for the structure too-are very well thought-out. It is all more organized and easily accessible," said Selbach.
"The machine is really very reliable," said Dittmann. "The last service deployments went very well. None of the others offered this level of flexibility or speed of response. For instance, we once had WFL Service on the phone in the afternoon at 5 PM, and at 9 AM the next morning, the service engineer was on site with the spare parts. We are very satisfied."
High Demand for Innovation
In addition to the Flanx gear teeth package, the machine is equipped with a measuring package. "We use in-process measuring for every component. It is worth its weight in gold," said Dittmann. "Accuracy is especially important on the face of the shafts because this is where the connecting surface centering device is attached. An imbalance would definitely be detrimental for this kind of bearing."
Vecoplan is constantly investing and optimizing and has a 20,000 sq. m production area, four production halls and 80% in-house manufacturing. Selbach explained: "We have installed a camera in the working area of the machine. As mentioned earlier, we have our own VSC, and this connects the machine to the production network. This allows us to see the machine from anywhere using our own app."
In terms of low-paper manufacturing, the next few years are set to bring fresh changes in production, such as monitors next to machines. At the moment, all processes-from setting up to the individual machining operations-are subject to analysis to boost efficiency. As part of a pilot project, a monitor is attached to the M120 Millturn, which provides access to drawings, 3D models, etc. The plan is to install these monitors on all machines to provide access to all order-specific data, part numbers, times, etc.
In order to deal with the strong growth prevalent at Vecoplan, checks are being carried out to determine whether additional staff can bring about the necessary efficiencies. That is why work is being done to monitor and track all data from the plants and machines.
"Modernization of the plant's machinery is also up for debate; take staff training, for example. It is no good having a great machine if nobody knows how to use it. It is absolutely vital to emphasize the importance of a competent employee," said Dittmann.
Selbach added: "The appeal of this kind of machine is clear. At first, there were some concerns. Now, we have a skilled team of operators and suddenly other colleagues want to work with the machine too. The new, state-of-the-art technology is certainly appealing-there is a big backlog of demand. But we are obviously delighted that our employees are very motivated."
Vecoplan sites are located across Europe and the USA.
For more information contact:
Vecoplan LLC
5708 Uwharrie Road
High Point, NC 27263
336-861-6070
info@vecoplanllc.com
www.vecoplanllc.com
WFL Millturn Technologies
Autania Tec Center
48152 West Road
Wixom, MI 48393
248-347-9390
office@wfl-usa.com
www.wfl-usa.com