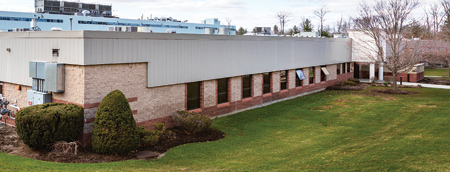
Alpha Grainger Manufacturing in Franklin, MA
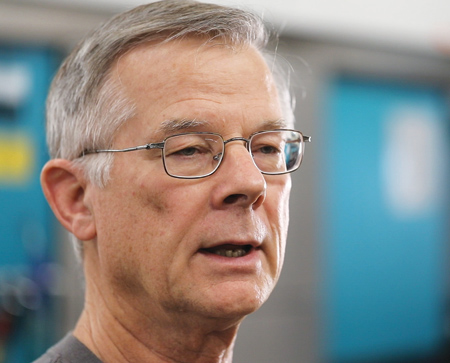
Jake Grainger, President of Alpha Grainger
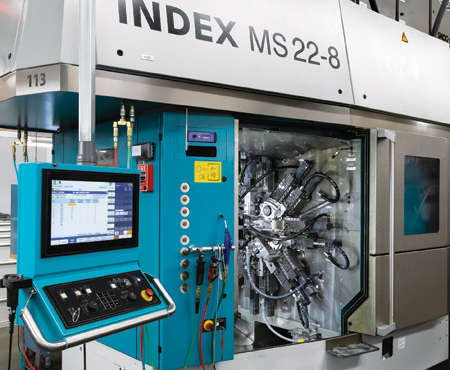
On of Alpha Grainger's INDEX MS22-8 machines. These machines feature eight spindles and work with 22 mm bar stock.
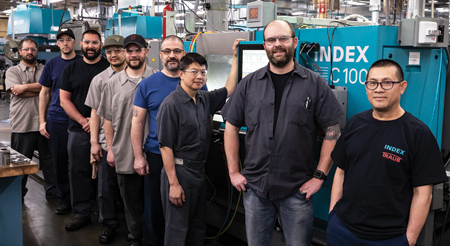
Alpha Grainger team
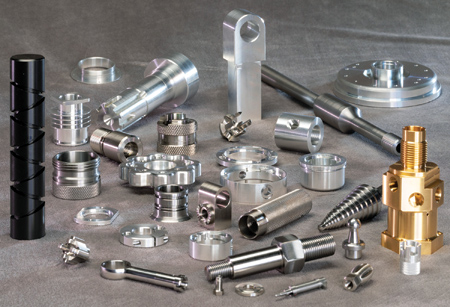
A variety of parts machined at Alpha Grainger. "Our customers bring us the parts that are causing them problems. We solve their problems," said Jake Grainger.
If one asks a variety of longstanding shops how they have maintained growth over the years, some common themes typically emerge: being fully committed to quality; striving for constant improvement; investing in a strong mix of people and technology; going above and beyond to meet customers' needs.
Talking to the team at Alpha Grainger Manufacturing, a Franklin, MA, shop approaching 50 years in business, one hears many of the traits that are shared across many shops with a long history of success. They also give a lot of credit to a factor that is referenced a bit less frequently: optimism.
"I think it is on the boss of a company to set the personality of the place and let that trickle down throughout the organization," said Jake Grainger, President of Alpha Grainger. "I am an optimistic person by nature, and I have worked to make sure that is reflected here. We are a group that always believes we can solve a problem and we enjoy tackling challenges together."
That can-do attitude has permeated Alpha Grainger since the company's founding in 1973 by Jake and his brother, Gary Grainger. They started in a small garage, but quickly built up enough business to expand. In the late 1970s, Gary approached Jake with an idea.
"My brother came to me to say he wanted to buy an Apple computer and teach himself how to program," said Jake. "We spent $5,500 on the computer, which was a sizable investment for us then. It paid for itself pretty quickly."
Shortly after acquiring the computer, Gary had taught himself enough Basic to write a custom billing program that automated enough tasks to completely free up a full-time employee for other tasks. Over the years, Gary consistently expanded the system.
"That internal programming capability has been huge for us," said Jake. "Machine info, order entry, raw material inventory, quality control, lead time management, tool life monitoring, customer notifications-all of that and more are built into our own customer software. We would not be where we are now without it. It essentially does the work of 30 to 40 people and, for a long time, it has basically given us access to capabilities that most shops our size could not possible have."
For some shops, such an advantage would be the defining pillar of their success. For Alpha Grainger, it is but one of many. The two brothers have built a culture that revels in pushing technology to its optimal point, and then continue to improve it. Walking through the shop, visitors see a variety of technologies that have been pulled apart and put back together to perform beyond what was originally possible. Internally developed systems for automation and part measurement can be found at many stations. All of this is done in service of the customer.
"Our customers bring us the parts that are causing them problems," said Jake. "We solve their problems."
Since 2006, INDEX machines have been a key part of that approach. Around that time, Alpha Grainger saw the potential of turn-mill centers that could turn parts and then conduct secondary milling operations in the same set-up. The shop's first INDEX machine was a C100, a production turning center that can apply rotating tools in any position on any of its three turrets.
Four years later, Alpha Grainger purchased its first INDEX multi-spindle machine, an MS40-6. With six turning spindles in a barrel drum and two slides serving each spindle station, the machine allowed for dramatic cycle time reductions across a variety of complex parts, according to Jake. The company quickly invested in another MS40-6, followed by the decision to purchase four MS22-8 machines at once. Those machines feature eight spindles instead of six and work with smaller 22 mm bar stock.
"We bought four of those machines at once," said Jake. "Our thinking was, we saw the benefit they would provide and were confident that they would be the least expensive way to cut a pretty large variety of parts. We knew we could fill the capacity for one or two of them instantly, and then we would be left deciding which parts we wanted to produce at a higher cost by not having them on the multi-spindles. So, we went big and bought four."
Today, Alpha Grainger has 13 MS Series multi-spindle machines and eleven C Series production turning centers with milling capabilities. The company also purchases INDEX's Virtual Machine software for its machines. Each copy of Virtual Machine is customized to provide a true, fully accurate digital representation of the specific, individual machine to which it is tied. This gives the team at Alpha Grainger the ability to tinker with and optimize processes in a virtual environment, without costing the machines a single second of downtime.
"Working with INDEX technology frees us up to focus on process design and other areas of our operations," said Jake. "The machines just run. For example, we have machines that are 10 years old that we have never touched the chip handling or oil processing systems. They are also the only machines I've ever seen that truly keep thermal expansion under control, where over the course of a day, you might see 0.0001 inch variance. Couple that reliability with the ability to cut cycle times to a fraction of what they would be on other equipment, and we have a real, sustainable advantage."
Throughout all of the growth and evolution, the pervasive of sense of optimism has remained a constant at Alpha Grainger. When they see a dynamic new piece of advanced technology, they believe in their ability to take advantage of it. When a customer brings them a demanding part with complex geometries, they are confident that they can design a process to make it. They expect continued growth in their future as well.
"The number one critical factor the industry is facing today is getting and training young people to carry on as those of us who have been doing this for four or five decades retire," said Jake. "We have a great company for that. Creative people thrive in our environment. We find people who like solving problems and get them trained on our INDEX equipment, and they just about never leave. I would say I am pretty optimistic about the future of Alpha Grainger."
For more information contact:
Alpha Grainger Manufacturing
20 Discovery Way
Franklin, MA 02038
508-520-4005
www.agmi.com
INDEX Corporation
14700 North Pointe Blvd.
Noblesville, IN 46060
317-770-6300
sales@index-usa.com
us.index-traub.com