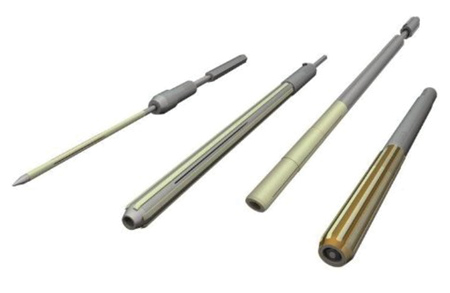
The precidor tools from Nagel are available in a wide variety of designs with full-surface or strip-shaped diamond coatings.
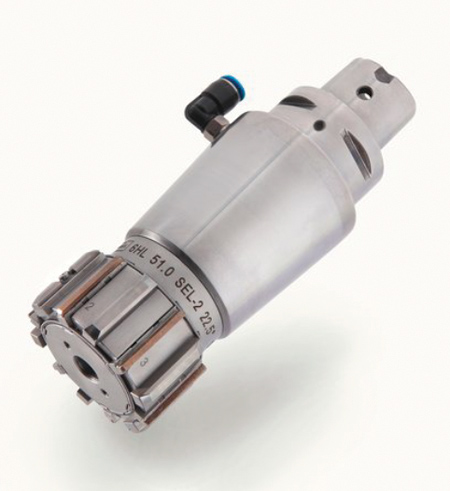
Honing tool with mounting for the spindle in the machining center or another processing machine. The equipment includes honing stones that can be expanded by coolant pressure and an optimal connection for air measurement.


"Fine machining honing is usually carried out on specially developed honing machines," said a Nagel spokesperson. "For large quantities, there is no way around this type of machine. But what about small series or even individual pieces and prototypes? Nagel Maschinen- und Werkzeugfabrik GmbH in Nürtingen (Germany) has suitable honing tools for machining centers (BAZ) in its range."
Component manufacturers who only have a manageable number of workpieces to hone each year understandably shy away from purchasing a classic honing machine. Two alternatives remain open: one is to outsource the work. This approach usually costs valuable time and requires the corresponding logistical effort. The second alternative, in-house machining on a BAZ turning or milling center, is faster and less expensive. Specially designed honing tools make this possible.
"With optimized tools for machining centers, honing can easily be integrated into the portfolio as a further production technology," said Markus Auch, Technical Sales Manager at Nagel. In addition to manufacturing conventional honing tools, Nagel also produces these customized tools.
Honing on the BAZ is anything but an emergency solution. There is even a central advantage: the workpiece is already in a clamping device on the BAZ and does not need to be reclamped. This means that small honing allowances are possible, which benefits process reliability and bore quality. If necessary, the number of necessary honing operations and consequently the machining time is reduced. The bottom line is that the costs per bore are minimized.
Single Stroke Honing
Honing tools for the BAZ and related machine tools can be divided into two main groups: versions with and without expansion or infeed. Honing without expansion is also called single stroke honing or friction honing. The process can be performed with hondornen or grinding pins. Although the classic cross-ground surface cannot be achieved with this process, high dimensional and form qualities with tolerances <1 µm can be achieved. The common diameter range is about 3 mm to 50 mm. Larger diameters rarely occur.
Nagel developed the Precidor tools (from "precise" and "mandrel") for single-stroke honing. The tools are either used after reaming or replace reaming completely (reaming honing). While reamers produce the chips with geometrically defined cutting edges, the material removal with hondorns takes place with full-surface or strip-shaped diamond coatings.
Typical applications are bores with longitudinal grooves where the cutting edges of a reamer would get caught. Further examples are valve seats and guides, e.g., in hydraulics. If required, Nagel can also supply designs for stub bores or multistage processes. Most mandrels include wear compensation by means of an expanding mandrel. The mechanism is actuated at the adapter of the spindle pick-up. A knurl and a scale allow µ-accurate adjustment.
Especially for ream honing, i.e., to replace reaming, Nagel has developed low-cost DAL-E Hondorns. "In principle, these are simplified precidor tools," said Auch. "The background: many users have to struggle with tool life problems when reaming. The reaming tools, on the other hand, offer a tool life that is about a factor of 10 longer than that of reamers. Another bonus is that they can be used on hardened materials. Equipped with a cylindrical shank as standard, these tools are also suitable for standard machine tools and even for hand-held drilling machines, e.g., to rework bores on large components. The DAL-E Hondorns are cost-effective machining solutions for high-quality results. Like the precidor tools, they can be readjusted, but not via an adapter on the holder; via an opening on the face."
Classic Honing
Classic honing with the typical cross pattern is also possible on a BAZ and comparable machining centers, both with vertical and horizontal spindles. Special last tools are available for this. Depending on the setting of the stroke and rotation movement, the angle of the cross pattern can be controlled. In addition, these tools can be expanded with the help of coolant pressure, so that an infeed movement can also be realized. As with the tools for the specialized honing machines, the honing stones can be individually equipped with the desired cutting medium and exchanged at any time. Nagel manufactures this type of tool for the large diameter range 6 mm to 180 mm. For very deep bores or difficult machining situations, such as horizontal bore positions, variants with optional internal cooling are available.
"Compared to a classic honing machine, the general conditions on a BAZ are completely different and usually also vary," said the spokesperson. "However, the quality requirements are constantly high. At the end of the day, µ-accurate results are required. The prerequisite for this is an optimally coordinated overall package. Being able to provide this to every user is a strength of Nagel."
Auch said: "Since we develop not only the tools but also the cutting materials and the application technology ourselves, we are flexible and can offer a functioning solution for every conceivable machine constellation and task. For example, we match the cutting tools exactly to the material, allowance and cooling lubricant."
While the honing machine is cooled and lubricated with honing oil, the BAZ also uses emulsion. This has to be taken into account in the tool design. Furthermore, with the appropriate choice of cutting medium, all materials can be machined: soft materials such as aluminum, as well as cast iron, steel or hardened steel. There is also flexibility with regard to the spindle interfaces. Nagel supplies BAZ-capable tools for all connections (HSK, SK, Capto, Hydrodehn, MK, etc.).
Authored by Nagel Precision
For more information contact:
Nagel Precision, Inc.
288 Dino Drive
Ann Arbor, MI 48103
734-426-5650
info@nagelusa.com
www.nagelusa.com