
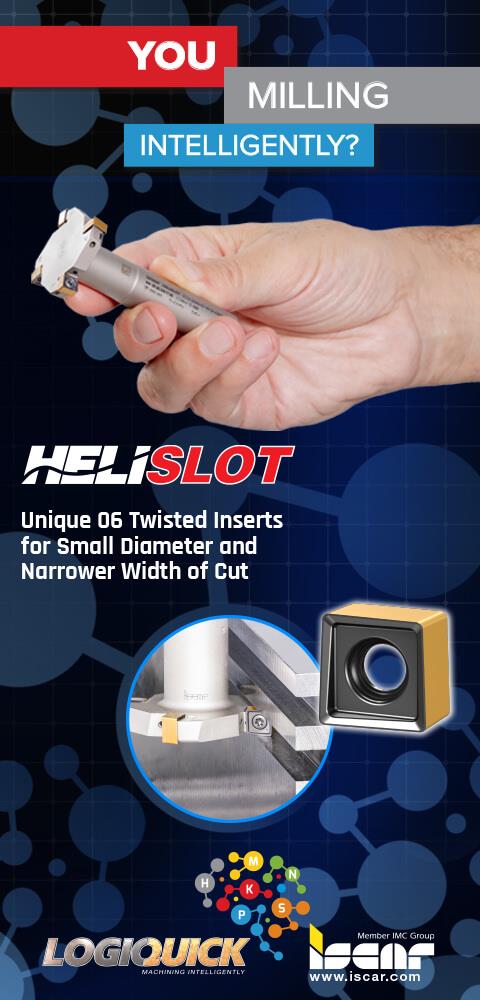
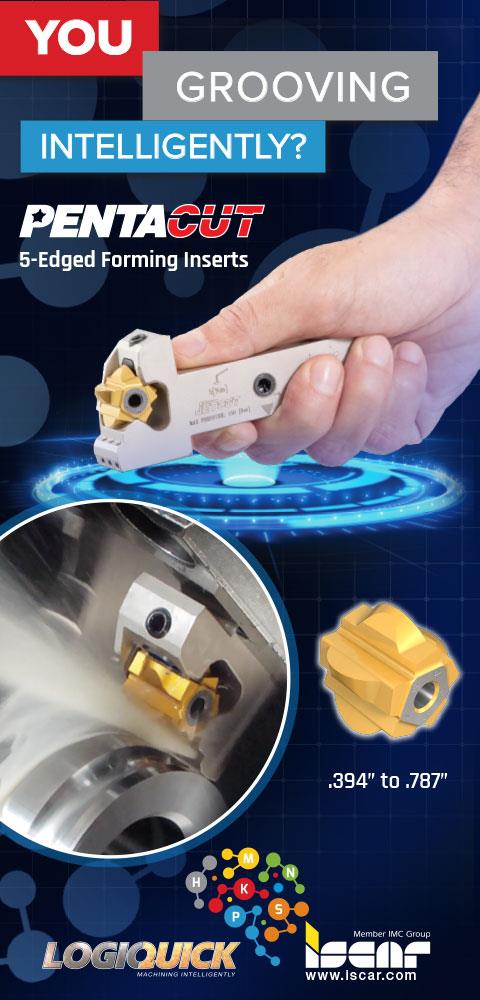
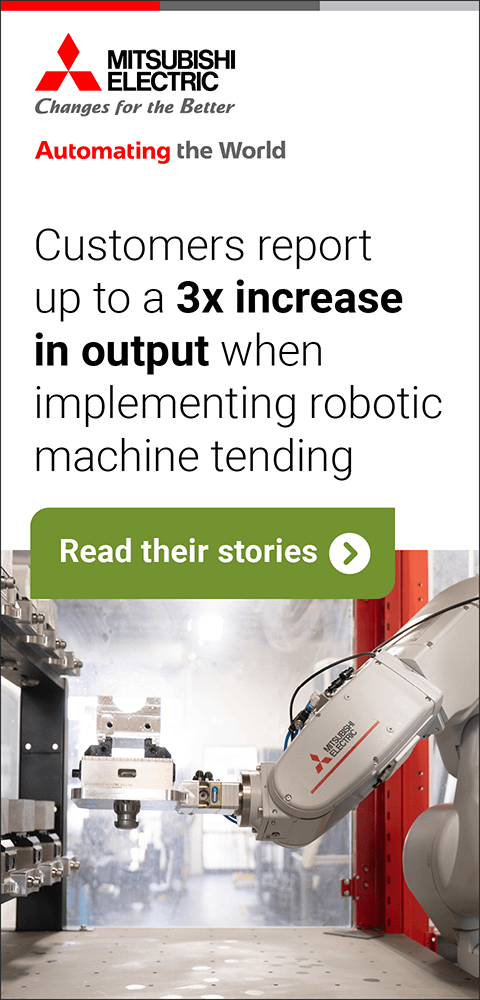
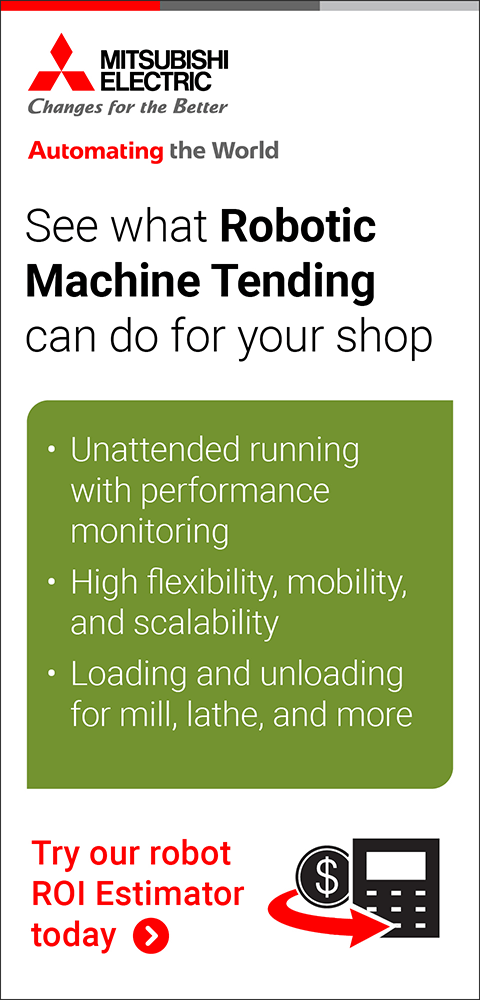
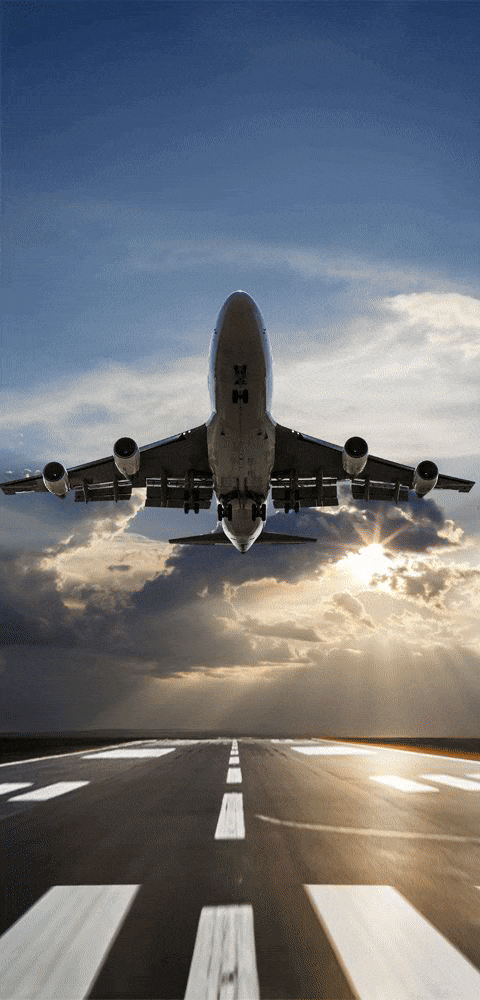
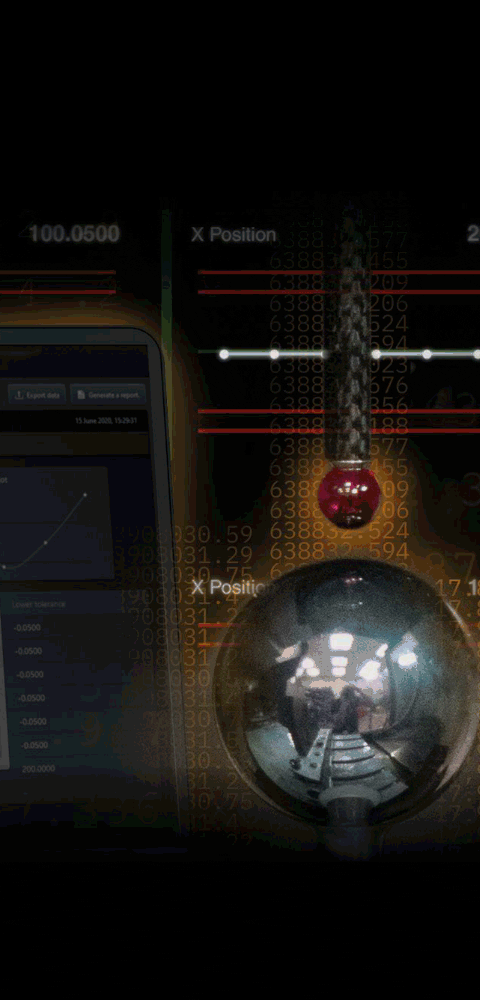
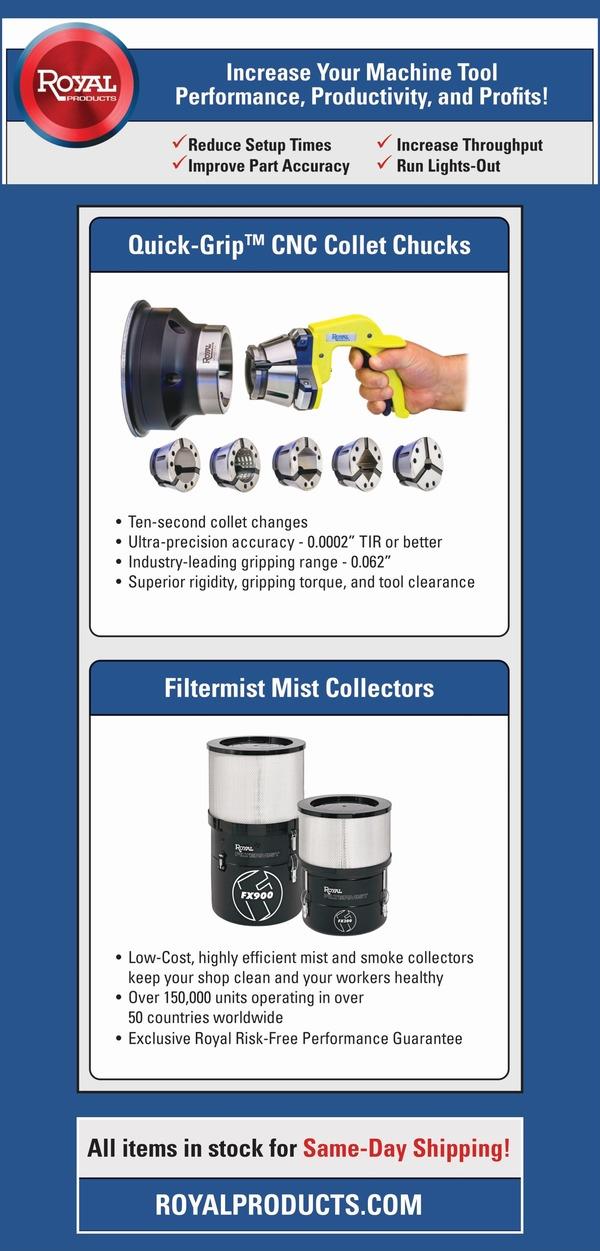
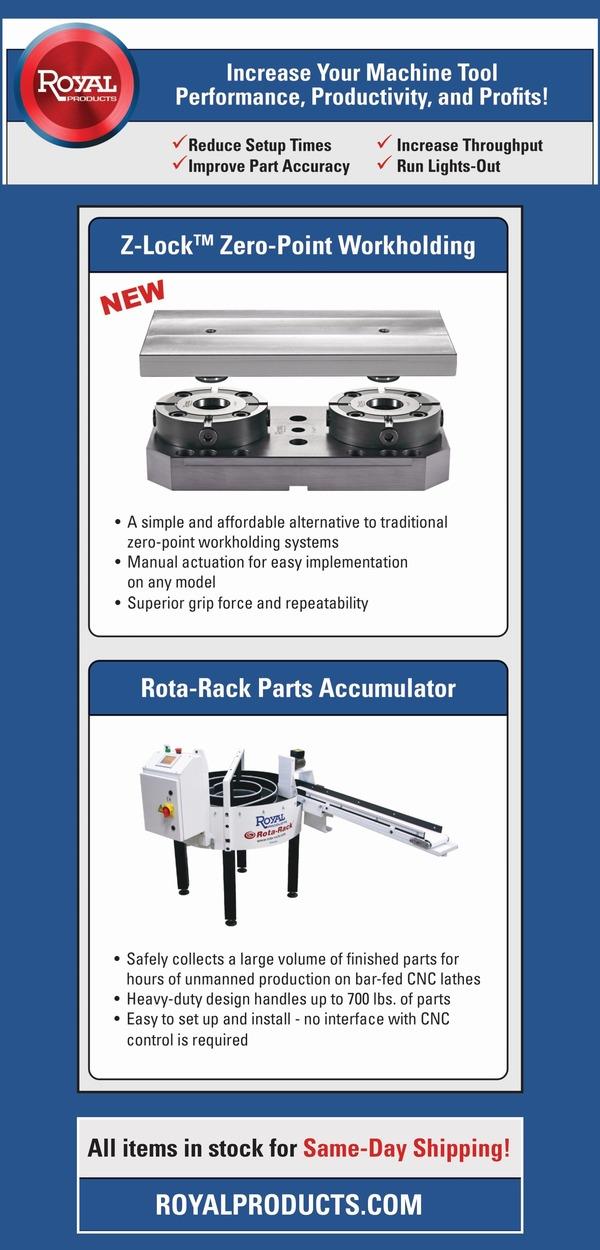

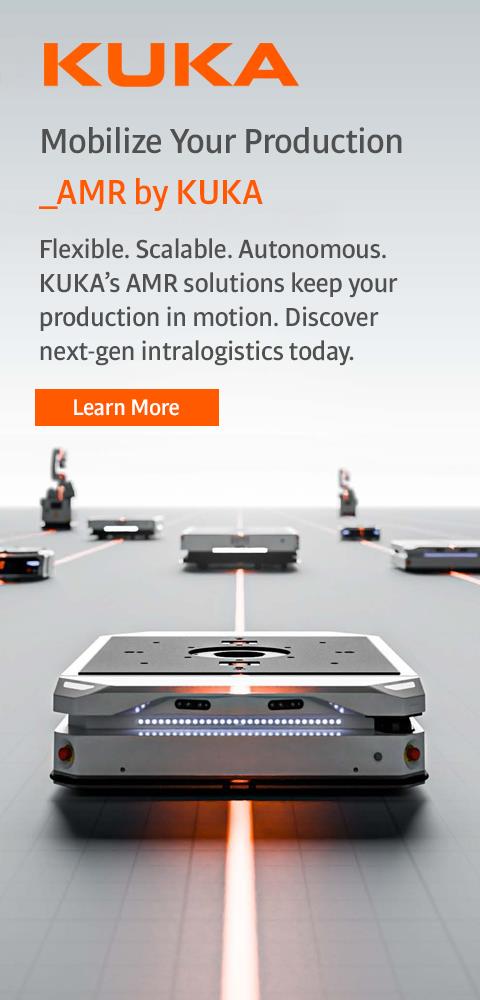
Bending Machine for Large, High Tonnage Parts
April 1, 2024
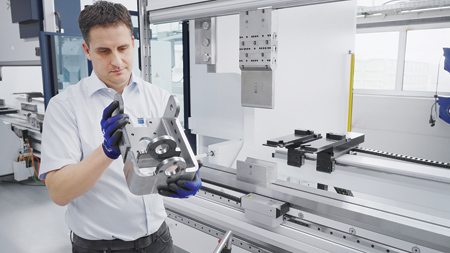
With a press force of 440 tons, the TruBend 8000 from TRUMPF bends high-strength steels.
TRUMPF offers the latest generation of its TruBend 8000. With a 34" open height and a stroke of 27", the TruBend 8000 bending machine offers an efficient way to bend very large parts, allowing workers to easily bend and remove workpieces that require a large box height. The press brake is available with numerous optional extras designed to facilitate the bending of heavy parts. These features include a bending aid that makes operators' lives easier by automatically positioning the workpiece for bending. TruBend 8000 Series machines can also be equipped with a special tool clamp for high tonnage applications.
Starting with a press force of 440 tons and going all the way to 1,100 tons, this new generation of machines is an efficient powerhouse that has no trouble processing long, thick pieces of sheet metal. The machine is also suitable for bending high-tensile materials such as Hardox or Weldox engineering steels. Station bending is another option available with the TruBend 8000. By moving workpieces from one station to the next, each equipped with different upper and lower tools, workers can tackle a range of parts and bending operations without having to change the machine setup for each operation. This makes the TruBend 8000 particularly suitable for companies that bend large parts in small batches, including fabricators in the vehicle manufacturing, mechanical engineering and building-services sectors. This model is also suited for general-purpose work in job shops.
The TruBend 8000 Series comes with TRUMPF's Boost and TecZone Bend bending software for offline programming. The machine operator simply uploads a 2D or 3D model of their part into the program. Then, the software independently creates a 3D simulation, including collision monitoring, which the operator can then adopt for the bending process, either in its entirety or with minor manual changes. TruBend 8000 machines are also designed to facilitate the trend toward greater sustainability in manufacturing. Users can choose to equip their machine with an on-demand drive, which automatically adjusts the motor's revolution speed to the movement of the press beam. As well as limiting noise generation, this feature can also reduce energy consumption by up to 26%.
For more information contact:
TRUMPF Inc.
Farmington Industrial Park
Farmington, CT 06032
860-255-6000
info@us.trumpf.com
www.us.trumpf.com
< back