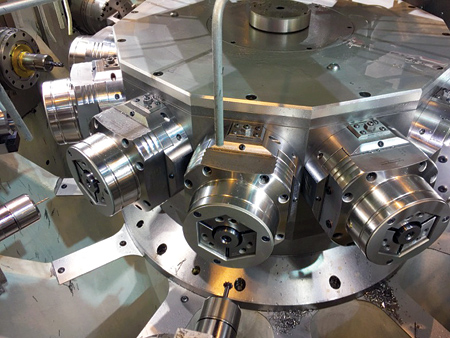
The Hydromat Eclipse machine at RW Screw is equipped with HAINBUCH's Hydrok SE 65 hexagonal chucks. The hexagonal geometry offers optimal protection from contamination, increases tool life and delivers 25% greater clamping force. It accommodates round and hexagonal bar stock with clamping heads that can be quickly changed.
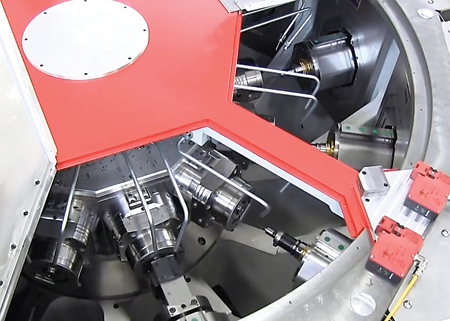
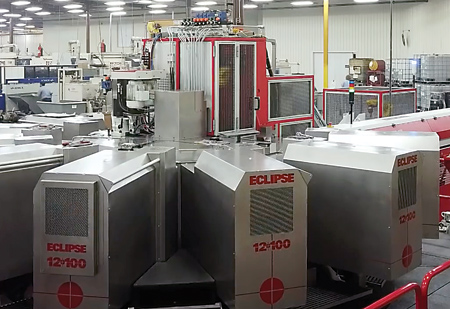
For one particular parts family, RW Screw incorporates a 12-station Hydromat Eclipse rotary transfer machining system equipped with HAINBUCH precision workholding systems. The objective was to consolidate the entire manufacturing process from bar stock to finished product without having to transfer parts to multiple machines.
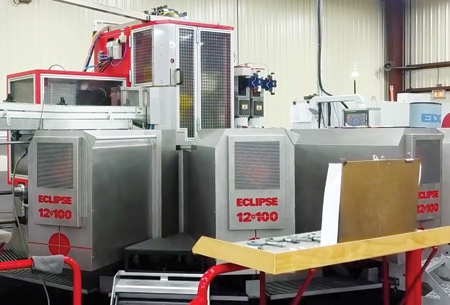
In response to increased demand for large quantities of select high-precision components, RW Screw LLC of Massillon, OH, implemented a manufacturing strategy that combines advanced multispindle capabilities with precision workholding. The result is a production cell that eliminated the need for performing multiple operations on different machines and reduced cycle time to an impressive 22 seconds per part. An additional benefit is the virtual elimination of scrap and damage to parts due to handling and repeated machine set-ups.
Bill Reeder, RW Screw President, explained: "We manufacture literally millions of precision machined components annually for a wide variety of industries, including automotive, small appliance, energy and agricultural. We employ 230 people, and our services include high-precision Swiss-style machining of complex parts, multispindle CNC machining of full or partial tight tolerance components, screw machines that handle up to 2-3/8 inch diameter stock, secondary machining for post-forming operations and high-volume grinding."
"We are constantly seeking ways to extend our production capability while maintaining the quality and precision that our customers require," continued Reeder. "For one particular parts family, we chose a highly innovative approach incorporating a 12-station Hydromat Eclipse rotary transfer machining system equipped with HAINBUCH precision workholding systems. Our objective was to consolidate the entire manufacturing process from bar stock to finished product without having to transfer parts to multiple machines."
Parts the company manufactures on this equipment are machined from 14' bar stock in both round and hexagonal configurations. Materials used include 12L14 and 1215 steel. Tolerances extend from .002 to .0006, and applications include drilling, milling, threading, boring, cross-drilling, reaming and deburring. Runs can range from a maximum of 600,000 parts to a minimum of 4,000 or 5,000.
"Typically, at least four different operations are performed per part per station," said Reeder. "The Eclipse system is capable of 3- and 4-axis turning and milling using three to four tools per spindle and is programmed to produce 12 parts simultaneously. All parts programs are in the system so set-up is fast, and the machining sequence begins by cutting the bar stock to the correct part length. Because the part is stationary and the tooling is live, the system can perform multiple tasks without removing the part. If necessary, parts can be inverted while in process to allow machining on both ends. The fact that the bar stock is not rotated eliminates the vibration associated with tailwhip-further enhancing accuracy."
Key to production efficiency is the quick-change capability of the HAINBUCH workholding system. According to Jason Schoemann, Sales Engineer at HAINBUCH America Corporation, "The Hydromat Eclipse machine at RW Screw is equipped with Hydrok SE 65 hexagonal chucks with a clamping range of 3 mm to 65 mm. The Hydrok SE 65 is ideally suited to the size range of the RW Screw parts family, and the hexagonal geometry offers optimal protection from contamination, increases tool life and delivers 25% greater clamping force. It accommodates round and hexagonal bar stock with clamping heads that can be quickly and easily changed."
Reeder said, "The HAINBUCH quick-change feature is essential to achieving our production goals. What used to take one or two days to change between parts now takes 30 minutes, and we can go from a hex stock to round stock in three hours. Equally important to successfully holding tolerances is the high repeatability of the HAINBUCH system due to precision grinding. The extra 25% rigidity reduces chatter, which is a critical factor when overturning on a hex. We use HAINBUCH products in many applications throughout our facility, so we knew how well they would perform in the Eclipse installation."
Schoemann noted, "Although the majority of the collets used on the chucks at RW Screw are standard, we work with them in supplying specially sized units when required. Also, chucks can be adapted for ID clamping with a HAINBUCH MANDO Adapt, and the clamping diameter can be expanded with a jaw module."
Reeder emphasized the importance of eliminating transfer of parts between machines: "We have really reduced the scrap rate by eliminating the nicks and dings that come from moving parts around the shop. Our quality is maintained, and by saving time we are able to meet customer delivery requirements-even for rush orders."
"By combining Hydromat's speed and flexibility in machining and HAINBUCH's quick-change high-precision workholding, we have been able to deliver the quantities and quality of parts that will meet customer needs while achieving previously unheard-of cycle times," Reeder concluded.
For more information contact:
RW Screw LLC
999 Oberlin Road SW
Massillon, OH 44647
866-797-2739
sales@rwscrew.com
www.rwscrew.com
HAINBUCH America
W129 N10980 Washington Dr.
Germantown, WI 53022
800-281-5734 / 414-358-9550
sales@hainbuchamerica.com
www.hainbuchamerica.com
Hydromat, Inc.
11600 Adie Road
St. Louis, MO 63043
314-432-4644
www.hydromat.com