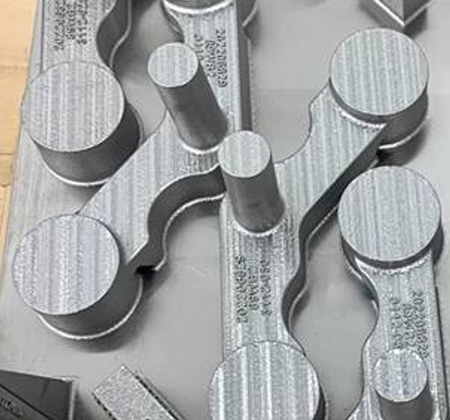
Metal 3D printed production parts for the Pacer Edge program (printed in cobalt-chrome and nickel alloy 718 on a GE Additive Concept Laser M2) nine months after requirement flow down.
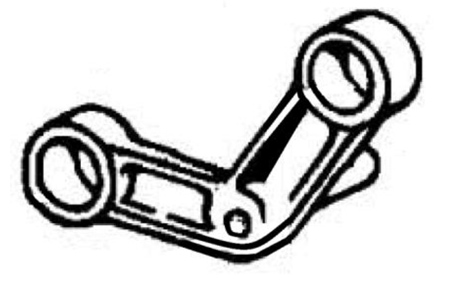
A hand-drawn technical illustration of the cross shaft arm dating from the 1960s.
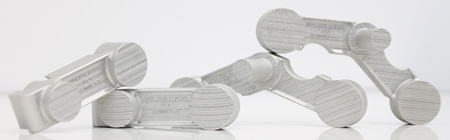
The first successful development build of the cross shaft arm was printed nine months after requirement flow down.
The US Air Force (USAF) and GE recently entered the third phase of its Pacer Edge pathfinder. Phase III has focused on 3D printing for four parts that are currently obsolete: a bellcrank, gearbox seat, anti-icing valve body and a cross shaft arm. The first two parts, the cross shaft arm and the bellcrank, have been successfully printed in cobalt-chrome on a fleet of M2 Series 5 system at GE Additive's facility in Cincinnati.
The final phase of the program over the coming years is to establish the USAF's own metal additive production infrastructure initially at Tinker Air Force Base in Oklahoma. This capability will alleviate long lead timetables that currently plague the casting and forging industries.
"Pacer Edge represents a monumental step forward in innovative partnership with industry. Through this program, our enterprise team will deliver safe and timely propulsion readiness in support of the United States warfighter," said John Sneden, Director of Propulsion, USAF.
USAF is not the only entity struggling to receive castings and forgings in a timely manner. It remains a choke point for many industries and has only been exacerbated by the COVID-19 pandemic.
"Public-private initiatives like the recently announced AM Forward initiative will also help to address DoD's sustainment and readiness challenges head on. Strengthening U.S. supply chains, by encouraging small and medium sized manufacturers across the United States to adopt metal additive technology, will create a nationwide network of a qualified additive manufacturing suppliers," said Lauren Tubesing, Director of Operations, Military Programs at GE Additive.
For more information contact:
GE Additive
www.ge.com