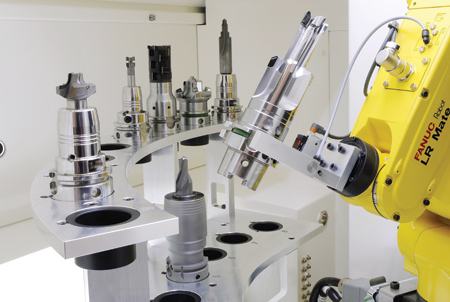
FANUC high-speed robot for automatic loading and unloading
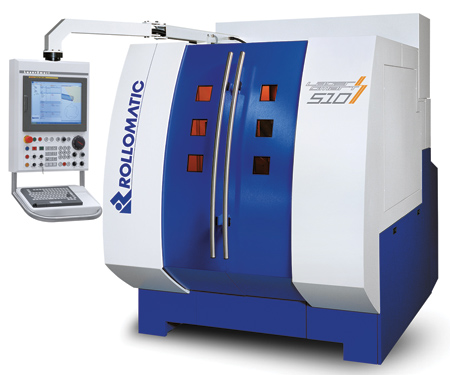
Rollomatic ShapeSmart LS510
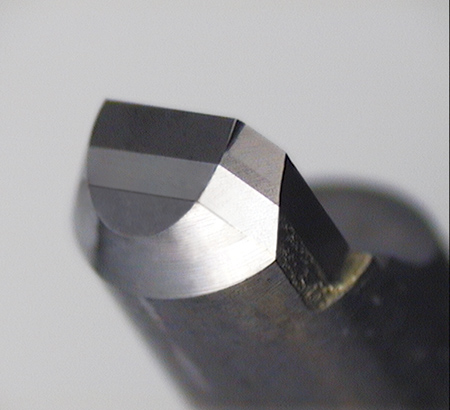
Rollomatic has succeeded in producing a surface finish of Ra 48 nanometers (0.048 micrometer) on a primary relief of a profile insert in PCBN material.
The tests were performed on the LaserSmart LS510 cutting and ablation machine with 5 interpolating CNC axes.
"A 'super-mirror' finish is generally known to be around 100 nanometers, which Rollomatic was able to cut in half," said a company spokesperson. "These tests were performed at the Rollomatic showroom facility in Mundelein, IL, without sacrificing on feedrates or cycle times. In particular, the process ensured that the integrity of the edge quality was fully maintained without compromise."
The verification and measuring process was carried out by a Bruker-Alicona EdgeMaster Optical 3-Dimensional Metrology Unit.
"This machine produces the sharpest corner radius in the PCD/CBN industry with a maximum radius on the cutting edge below 0.5 micron," said a company spokesperson. "In addition, a defined radius of 3, 6 and 9 microns can also be produced consistently." In addition to round-shaft tools, HSK63 shanks can also be accommodated on this machine.
The strategy for this machine is to offer a more cost-effective way and higher quality in the production of high-performance PCD polycrystalline diamond, CBN cubic boron nitride and CVD chemical vapor deposited cutting tools, which traditionally need to be produced by a double process of spark erosion and polish grinding.
According to Rollomatic, features and benefits of the LaserSmart LS510 include:
- Up to 4x faster feedrates with identical edge and surface quality
- 3D machining of drill points and endmill cutting geometries
- Process to sharpen the cutting edge of CVD or thick-film diamond coated cutting tools
- Fine-laser cutting achieves a superfine cutting edge with a surface finish that is unachievable by grinding/EDM
- Conventional grinding with diamond wheels will invariably "pull out" an entire PCD crystals, while laser cutting will "slice" through the crystal and leave a portion of the crystal in the matrix, thus providing a razor-sharp cutting edge unattainable by EDM, EDG (electro-discharge) or grinding
- Linear motion technology on all linear and rotary axes provides highly accurate trajectories for complex cutting paths
- Continuous field testing has shown that sharper cutting edges and enhanced surface quality on PCD tools deliver longer tool life and higher feedrates during machining
- Laser ablation allows the freedom to optimize tool geometries
- Manufacturing chip form geometries in PCD is easily performed by this machine using the ablation process as a cost-effective and powerful alternative to existing complicated and expensive conventional methods.
For more information contact:
Rollomatic Inc. USA
1295 Armour Blvd.
Mundelein, IL 60060
847-281-8550
solutions@rollomaticusa.com
www.rollomaticusa.com