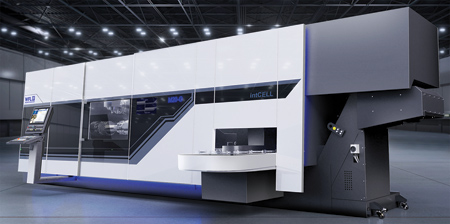
The M20 MILLTURN is the latest addition to WFL's product portfolio. The integrated intCELL production cell is mounted on the right-hand side of the machine.
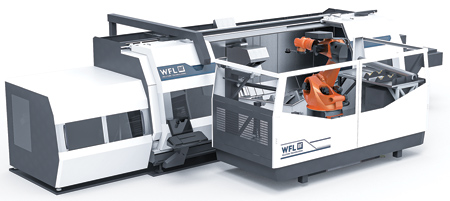
Static production lines are giving way to the next generation of robots. Intelligent mobile robot units move around the space independently, providing absolute flexibility for industry.
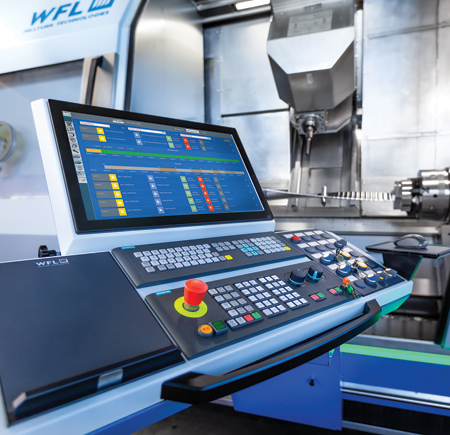
With the new myWFL operational data acquisition, operators get a 24/7 overview of their operations.
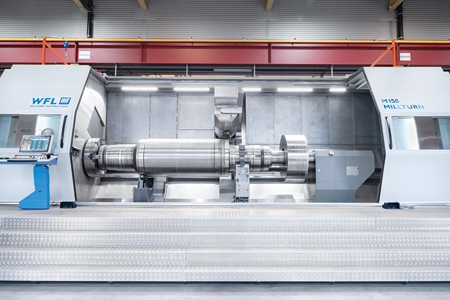
The WFL range of machines can accommodate weights of up to 66 tons. This kind of heavy component can be processed in just a few clamping operations and on one machine.
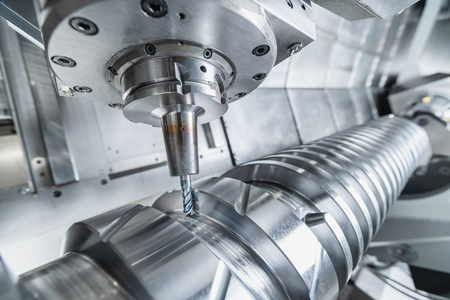
The latest solutions from WFL range from smart software for screw programming to intelligent tools and clamping devices.
WFL Millturn Technologies recently held a technology meeting, where one of the innovations showcased was mobile robot automation on the M65 MILLTURN.
On a M20-G MILLTURN one of the counter spindles was equipped with an innovative automation solution-the intCELL. This is a new turning-boring-milling unit with integrated spindle motor and a B-axis with torque motor. Another highlight was the individual toolholder with B-axis on the lower slide. The upper and lower system can be used simultaneously. Both systems are supplied from a joint magazine by a dynamic tool changer. Highly complex components can be produced efficiently on both spindles at the same time without the usual setting up of the tool turret. Because the center of the milling spindle can travel up to 100 mm below the turning center, drill patterns on the face up to O 200 mm can be produced with high precision without rotation of the C-axis.
A key advantage of this machine is that a wide range of automation options can be integrated with ease. The new, integrated intCELL production cell is mounted on the right-hand side of the machine and the workpieces are provided on a strip accumulator. Due to the integrated loading concept, WFL has reduced the space required compared to a conventional production cell by 50%. The integrated M20-G loading is designed for chuck parts up to 300 mm in diameter and workpieces up to 15 kg in weight. In the case of shaft parts, a workpiece diameter of 100 mm and a workpiece length of 300 mm is possible.
Machine Design
The machine features a continuous front made from hardened glass and features an integrated display of performance data as well as a touch panel for easy operation of the tool magazine from the front of the machine. Bright, energy-efficient LED lights help ensure the working area is properly lit. The machine status is indicated via a highly visible LED strip light in the lower part of the sliding door.
The M20 is offered with tailstock or counter spindle and features dynamic drives. The machine offers power of up to 44 kW during turning for difficult to machine materials. With up to 25 kW and 20,000 RPM, the milling spindle is designed for all machining tasks. Either the HSK 63 or Capto C6 can be selected as the tool system.
Visitors were able to see a challenging chuck part being machined live on the M20-G. Also shown was gear skiving of internal and external gears as well as complex turning, drilling and milling operations on the main and counter spindle.
M65 MILLTURN with Mobile Robot Automation
To meet automation needs, mobile robots can move around completely autonomously with no need for cables or human input for them to work. Another key advantage of these robots is that they avoid obstacles, meaning that they can also be used in halls where the set-up is constantly changing and where machines and people are moving around. Sensors help to ensure that mobile robots move safely and efficiently between locations and interact safely with people, forklifts and other material handling equipment.
Using intelligent software in combination with the relevant automation solutions not only enables workpieces to be loaded and unloaded, but also means that machining centers can be supplied fully automatically with tools and clamping devices. As an innovative automation partner to WFL, FRAI presented its mobile robot system, which responds to this trend, at the event. This concept has scope for various expansion stages, making it as future-proof as possible.
Smart Tools: ICOtronic and Ultrasound Measurement
The ICOtronic tool is equipped with sensors and supplies information about the machining process as close as possible to the cutting edge. This optimizes milling processes and increases machine productivity.
Ultrasound measurement was also demonstrated live. The automatically exchangeable ultrasound measuring probe enables a fully automatic measuring process. The large measurement range and automatic, error-proof measuring process are the main advantages. Ultrasound measurement is suited for determining and compensating for the tool drift of very deep center holes.
Operational Data Acquisition with myWFL
Another highlight at the WFL Technology Meeting was the new myWFL Cockpit operational data acquisition system. Machine and program status over time, productivity and technical availability can be displayed, either on the control system, PC or mobile device via a web browser.
Another new feature is the myWFL Energy, an energy usage measurement device integrated into the myWFL Cockpit, which displays the current power data as well as the energy and compressed air consumption of each workpiece.
The Condition Monitoring cycle integrated into myWFL continuously records the status of the axes and spindles during a measuring run and saves them to the control system. Possible changes can be detected and displayed via the Condition Monitoring Viewer.
Machining Large Parts
WFL can now machine large, heavy parts weighing up to 66 tons-such as gas and steam turbines, components for wind turbines, rollers, crankshafts and transmission parts in machine construction-in just a few clamping operations and on a single machine. A MILLTURN can handle high-strength steel or heat resistant super alloy (HRSA) material, replacing special-purpose machines, such as those needed in multi-step production.
Distortion-free, secure clamping is required when it comes to high quality standards. Large masses have a tendency to deform or change as a result of their net weight. The sag of a turbine shaft weighing 66 tons is so great that this needs to be taken into account when clamping the workpiece. This variable can be compensated with the right design for the clamping device, clamping method and use of WFL measuring cycles to adjust the workpiece. The accessibility to the machine with folding grate elements and tread plates enhance ergonomics.
Programming and Processing of Plasticizing Screws
The medium-size machine models offer efficient machining of long shaft parts, rotors and screws. The M50 features higher drive power combined with the HSK-A100 or Capto C8 tool accommodation and offers a turning diameter of 670 mm. A separate pick-up magazine is available for very long and/or heavy tools. Tools up to 1,600 mm long can be used and exchanged automatically in the machine. The standard disc magazine can be expanded to up to 200 positions.
ScrewCAM, software for programming plasticizing screws with complex geometries, was introduced at the WFL Technology Meeting. Geometries that can be produced include single or multi-thread channels, changeable depths, any change in pitch, wall shaping and wall inclination. Furthermore, the entire NC program is checked for collisions and the correctness of the workpiece geometry produced using a material removal simulation and geometrical verification against the 3D target geometry of the screw. The result is a verified NC program with estimated machining time.
For more information contact:
WFL Millturn Technologies
Autania Tec Center
48152 West Road
Wixom, MI 48393
248-347-9390
office@wfl-usa.com
www.wfl-usa.com